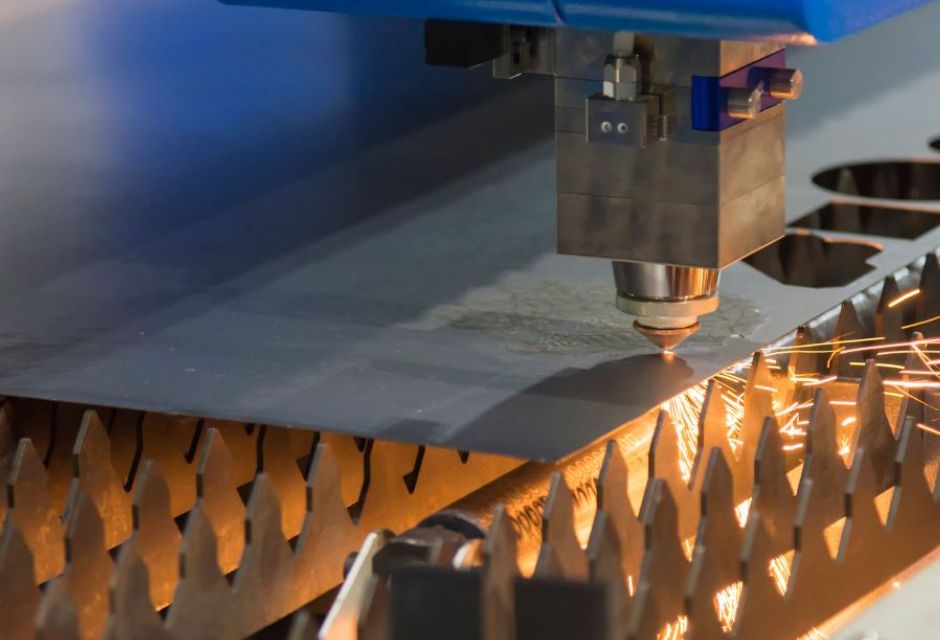
精密板金加工は、通常の板金加工と比較して高い加工精度と寸法公差が要求される製品を加工する技術として知られています。
主に採用されているのは、医療機器や自動車部品、電子機器など、高い精密性を求められる機器製造の分野です。本記事では、精密板金加工の特徴から、メリット・デメリットまでを解説します。精密板金加工の導入を検討している方は、本記事を参考にご自身の選択に役立ててみてください。
Taigaで技術提案を受ける目次
精密板金加工とは?
精密板金加工は、金属板を高精度で加工する技術であり、主に0.1㎜から3㎜程度の薄い金属材料を使用します。
一般的な板金加工と異なり、より厳密な寸法管理や高度な加工技術が求められるのが精密板金加工です。精密板金加工はより精密な部品の製造に適しており、電子機器、自動車、航空宇宙、医療機器などの分野で広く利用されています。
精密板金加工と通常の板金加工の違い
精密板金加工と通常の板金加工では、加工精度や用途、材料の種類などに違いがあります。それぞれの特徴について以下にまとめましたのでご確認ください。
精密板金加工 | 通常の板金加工 | |
加工精度 | 高精度(ミリ単位~マイクロ単位の精度が必要) | 一般的な精度(±0.1mm~±0.5mm程度) |
用途 | 電子機器、自動車、航空機、医療機器など高精度が求められる分野 | 建築資材、家具、産業用機械部品など比較的大きな構造物 |
材料 | 薄板金属(1〜3mm)を主に使用 | さまざまな厚さの金属板を使用 |
生産規模 | 試作から少量~中量生産が多い | 中量~大量生産が中心 |
コスト | 高め | 比較的安価 |
この表を見ると、それぞれの加工方法が適する用途や製品の分野が、明確に分かれていることがわかります。
精密板金加工の特徴は?
精密板金加工の特徴は以下の5つです。
- 精度が非常に高い
- 多様な加工が可能
- 製造効率の向上
- 長期的な耐久性の期待
- コスト効率が良い
精度が非常に高い
まずは、加工精度が非常に高いことが特徴として挙げられます。
具体的な精密板金加工の基準は、寸法公差±0.1mmから±0.05mm以下です。そのため、高い精密性を求められる機器製造の分野で重宝されています。
特に、わずかな寸法の誤差が製品性能や安全性に直結する医療機器や航空宇宙、自動車、電子機器などで活用されています。
多様な加工が可能
精密板金加工の大きな特徴は、切断、曲げ、穴あけ、溶接、組立など、多彩な加工技術を組み合わせて製品を製造できる点にあります。
これらの技術を活用することで、複雑な形状の製品が製造でき、さらにデザイン性の高い仕上がりも実現します。幅広いニーズに対応した製品を効率的かつ柔軟に製造できることが精密板金加工の魅力です。
製造効率の向上
精密板金加工は、複数の工程を一つの施設内で行うことで、外注や移動による手間や時間を省き、効率的な生産ができます。
また、設計データを機械に反映できるCAD/CAMシステムや自動化技術の導入によって、よりスピーディーな生産を可能にします。
特に、最新のレーザー切断機やNCベンダーなどの加工機械は、自動化や数値制御ができるため、高速かつ安定した加工が可能です。
長期的な耐久性の期待
精密板金加工は、高精度な加工機技術や仕上げ処理によって長期的な耐久性を期待できます。
高い基準を満たすことで、部品同士の適合性が向上し、組み立て後の製品の強度もさらに増します。また、耐久性の高い金属材料が使用されることも、長期間の使用に耐えられる特性の一つです。
コスト効率が良い
精密板金加工は、デジタル技術の活用や汎用性の高い加工機械によって、急な設計変更にも柔軟に対応できます。
そのため、製品の市場投入までの時間を短縮し、結果的にコストを削減することが可能です。
また、CADソフトを使用して設計段階で材料の配置を最適化することで、材料の無駄をさらに削減できます。
精密板金加工の流れ
精密板金加工は、製品の設計から完成まで一貫したプロセスで行われます。ここでは精密板金加工の流れを7つのステップに分けて紹介していきます。
- 設計・図面作成
- 材料の選定・調達
- ブランク加工(抜き加工)
- 曲げ加工
- 穴あけ加工
- 溶接加工
- 組立/検査
1.設計・図面作成
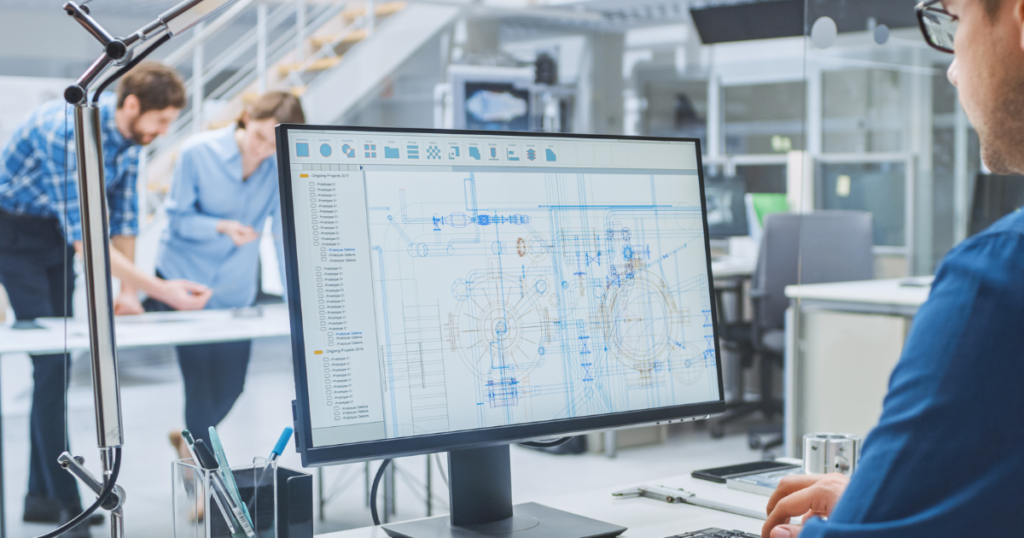
まずは、顧客の要望に応じた、製品設計図の作成です。
具体的には、加工工程をシミュレーションし、切削経路や工具選定をします。また、CADソフトでデジタルモデルを作成し、精密板金加工の最適化を図ります。
設計ミスは加工や製品品質に直接影響するため、設計段階で材料の特性や加工方法などを十分に確認することが重要です。
2.材料の選定・調達
設計図が完成したら、金属板の形状を平面で示す図面展開を行い、使用する部品の形や寸法などを確認していきます。
図面に基づいて、材料や加工機を選定し、調達まで行います。
材料の品質は、加工精度や製品の耐久性に直結するため、JIS規格やISO規格などを満たしている材料を選定することが重要です。
3.ブランク加工(抜き加工)
材料の調達が済んだら、プレス機やレーザーを使用してブランク加工(抜き加工)を行います。
ブランク加工とは、材料(主に金属)から特定の形状を切り抜く方法です。この工程によって次に使うための素材を作りだします。
4.曲げ加工
続いて、ブランク加工で作られた材料を、プレスブレーキやロールベンディングで指定の角度や形状に曲げます。
曲げ加工は製品の立体的な形状を作り出すための重要な工程です。このとき、材料の反発や厚みに応じて、曲げの過剰や不足を防ぐための調整が必要になります。
5.穴あけ加工
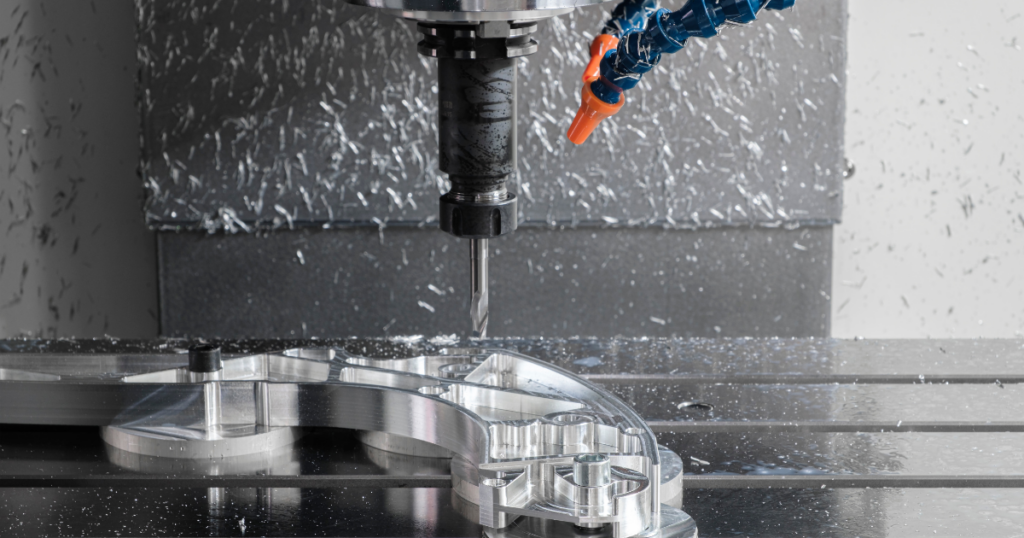
曲げ加工の次は、穴あけ加工です。
その名のとおり、材料の適当な部分にネジやボルト、配線用の穴をあけます。あけたい穴の種類や深さによって、使われる機会が異なります。
例えば、複数の金型を使い分けて連続的に穴をあける場合にはタレットパンチプレス、小さい穴をあける場合はレーザー加工、深い穴をあける場合はドリル加工などです。
このとき、穴周辺のバリを除去し、仕上がり品質を確保することが重要になります。
6.溶接加工

曲げ加工と穴あけ加工が終わったら、必要に応じて溶接をします。溶接は、部品同士を結合するための重要な工程で、TIG溶接やMIG溶接、スポット溶接などの技術が使用されます。
ここでは、材料が熱変形しないために、溶接熱の管理が重要です。溶接部位の強度が均一であることも忘れず確認します。
7.組立/検査
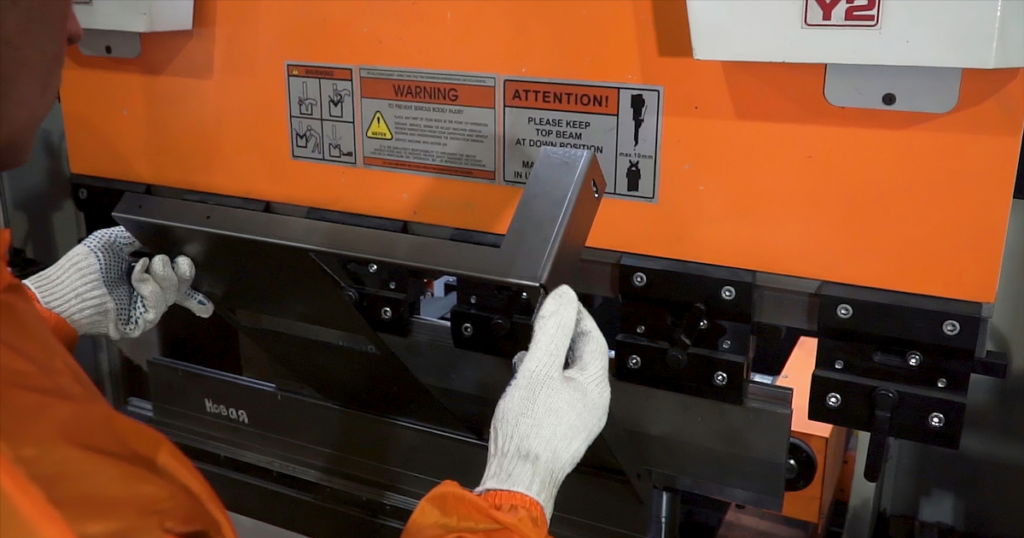
溶接加工が完了したら、表面の仕上げ加工が行われ、組み立てます。必要な部品を組み立て終わったら、最後に設計通りの精度や品質を満たしているかの検査をして終了です。
強度や寸法、外観など、検査基準に基づき適切に行われます。万が一設計の公差範囲を超えた場合は、原因を特定し再加工を行います。
まとめ
この記事では、精密板金加工の特徴と設計から組み立てまでの流れを詳しく解説してきました。
精密板金加工は、寸法公差±0.1mm以下の高精度を実現する加工技術で、医療機器、自動車、航空宇宙、電子機器などの分野で広く活用されています。
設計から組み立てまで一貫して行われ、CAD/CAMシステムや最新の加工機械を駆使することで、複雑な形状や高品質な仕上がりを実現します。
少量生産品の調達なら「Taiga」
「Taiga」は部品の再生産や多品種少量生産に対応し、納期短縮やコスト削減を実現する製造プラットフォームです。納期短縮やコスト削減を実現し、製造現場の効率化をサポートします。
精密板金加工を活用した部品製造を検討している方は、ぜひ「Taiga(タイガ)」をご活用ください!Taigaは、無料で経験豊富な業者に相談できるサービスです。
難易度の高い部品や新規部品の開発、少量生産、試作から量産まで、コストを抑えつつ効率的に進めることが可能です。
Taigaで技術提案を受ける