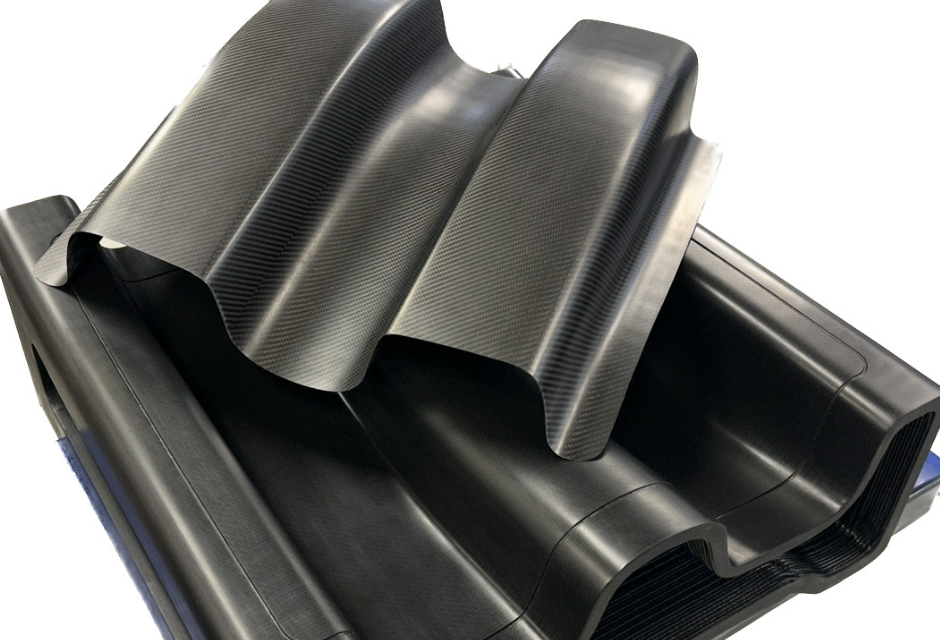
カーボンの加工成形技術に、オートクレーブ成形があります。
オートクレーブ成形は、メリットがある一方でデメリットもあり、加工時には注意が必要です。
今回の記事では、オートクレーブ成形とはなにかに加えて、メリットやデメリットを解説します。
オートクレーブ成形の手順についても紹介していますので、ぜひ参考にしてください。
目次
オートクレーブ成形とは?
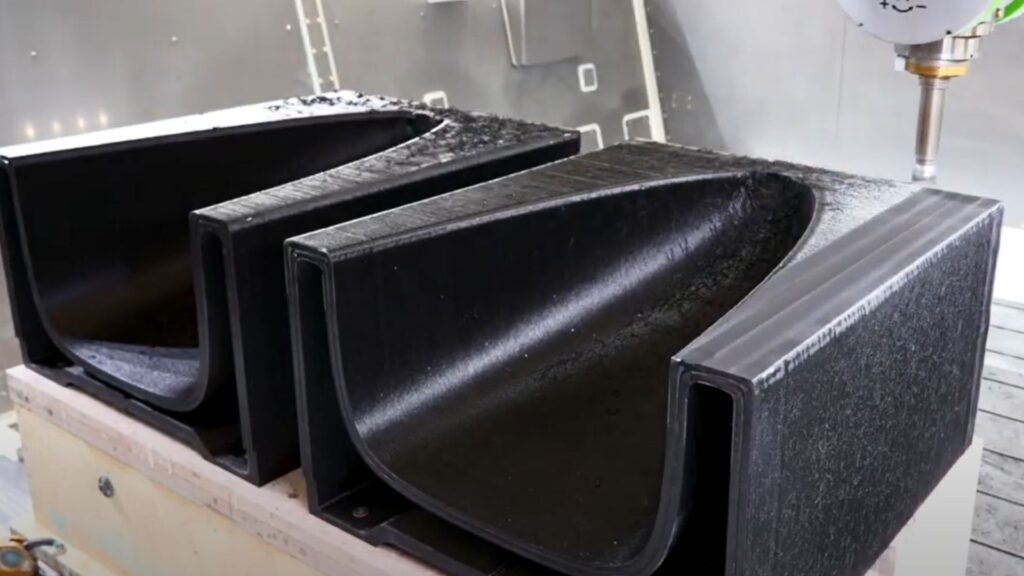
オートクレーブ成形とは、オートクレーブと呼ばれる圧力容器を使用して成形する方法です。
容器に材料を入れた状態で圧力をかけると、内部に残存する空気が抜けて成形される仕組みです。
圧力や温度などを製品に合わせてプログラミングすることで、加工が難しい素材も適切に生成することができます。
なお、オートクレーブ成形では以下のようなさまざまな材料を成形可能です。
- プリプレグ
- CFRP
- CFRTP
- リキッドモールディング
オートクレーブ成形のメリット
オートクレーブ成形のメリットを解説します。
設計の自由度が高い
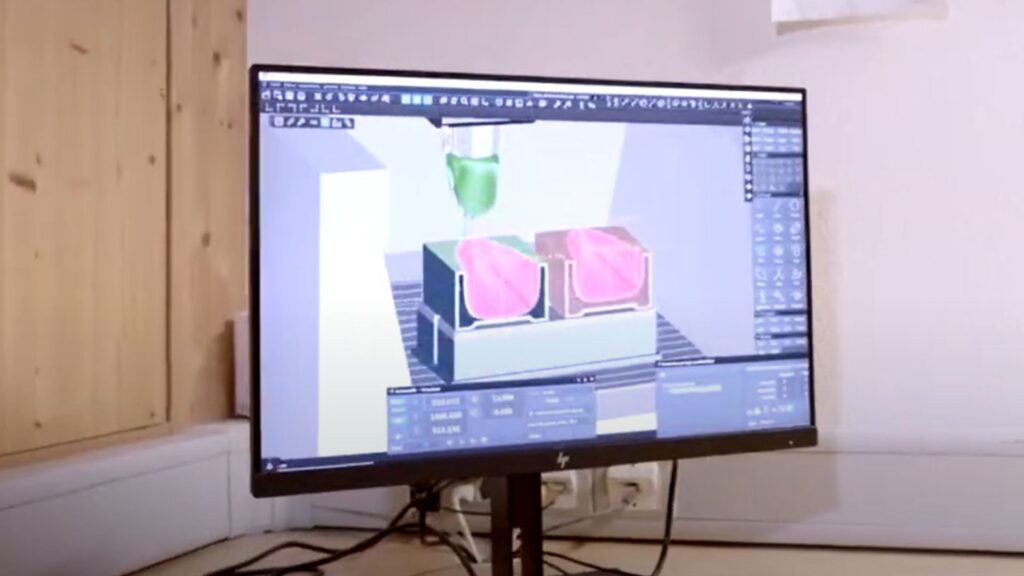
オートクレーブ成形は設計の自由度が高いのが特徴です。
大型部品や小型部品はもちろん、複雑な形状の部品など、幅広い製品づくりが実現できます。
高品質な成形が可能
オートクレーブ成形は、成形時に圧力を加える成形方法です。
加える圧力は通常で0.3MPa程度、最大でも2MPa程度と高いため、気泡(ボイド)発生を抑えることができます。
また、圧縮した空気を利用して材料に加圧するため、材料に対して圧力が均等にかかり、高品質・高精度な成形が可能です。
なお、カーボンなどの炭素繊維を材料とした場合、特性を最大限引き出せるため、より成形の精度が上がります。
成形用の金型が安く、少量生産にも向いている
オートクレーブ成形用の金型は、プレスや射出成形といったほかの成形方法で使用する金型よりも製作費用が安いのが特徴です。
金型製作にかかるコストが抑えられるため、大量生産はもちろん、少数生産や試作品製作用途にも向いています。
オートクレーブ成形のデメリット
オートクレーブ成形には、メリットがある一方でデメリットもあります。
覚えておくべきオートクレーブ成形のデメリットを順に解説します。
成形に時間がかかるため、大量生産には向かない
オートクレーブ成形は、圧力容器内に空気を送り込み、空気を加熱することで圧縮・成形する方法です。そのため、成形圧力や成形温度に到達するまでに約1~8時間程度の時間が必要となります。
成形に時間がかかるため、大量生産には向いていないといえるでしょう。
ただし、オートクレーブ成形の加熱時間を短縮する方法として、材料や成形型を直接加熱する方法もあります。
設備導入にコストがかかる
オートクレーブ成形は、金型の制作費用は安めであるものの、成形加工機自体の費用は非常に高額です。
設備導入のための初期費用が発生するため、高額設備が不要な成形方法よりもコストがかかるでしょう。
ただし、成形品が小型の場合は、比較的導入費用が安い小型モデルのオートクレーブを導入する方法もあります。
オートクレーブ成形の手順
オートクレーブ成形の具体的な手順を解説します。
成形用金型の作成
まず、材料となるプリプレグを貼りこむ金型を設計・製作します。
オートクレーブの成形用金型は、鋳造や射出成型で使用する金型と同じ役割を持っています。
金型には、使用する製品に応じて以下のように幅広い材料が採用されます。
金型の材料 | 特徴 |
⾦属型(アルミ合⾦、スチール等) | ・試作〜量産まで対応・耐久度が⾼い・⼿⼊れが比較的容易・耐熱性が高くCFRTP成形にも耐えられる・外注先の選択肢が豊富 |
パールボード(石膏ボード)型 | ・試作や少量生産向け・低粘度エポキシ樹脂で目⽌めを⾏って使⽤する・低価格で加工性が高い・熱膨張率が低いため、成形精度が⾼い・脆く金型の寿命は短い |
FRP型 | ・試作や少量生産向け・製品、マスター型から反転型を安価に製作可能・熱膨張率が⾼く、型製作の段階からから熱収縮を起こす点に注意が必要・熱劣化により金型の寿命は短い・ハンドレイアップによるFRP成形技能が要求される |
CFRP型 | ・FRP型の弱点、デメリットを克服した金型 |
なお、成形後なめらかに脱型するために、製作した型の表面には離型剤を塗ります。
離型剤は、成形品に求める仕様に応じて以下のタイプを使い分けましょう。
- 型表面に焼き付けて繰り返し使用するタイプ
- 離型剤自身が壊れる毎回塗布タイプ
- 型表面にシートを貼るタイプ
プリプレグの裁断
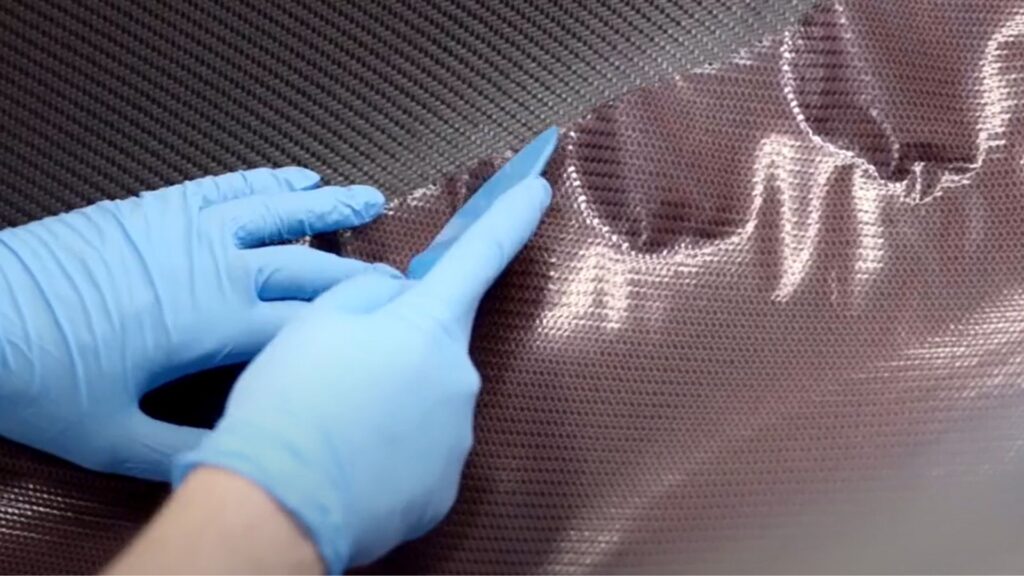
次に、プリプレグの裁断を行います。
プリプレグはシート状になっており、一般的な厚さは100μm〜250μm程度です。
プリプレグの裁断は、寸法精度や裁断面の品質維持のためにカッティングマシンを用います。
ただし、カッティングマシンは高価なため、試作や少量製作の場合は手作業で裁断することもあるでしょう。
プリプレグを積層する
裁断したプリプレグを型に貼り付け、積層します。
金属板のプレス成形と異なり、オートクレーブ成形はプリプレグシートを部分的に積み増すことで、成形品の板圧を部分的に変化させて補強したり、構造物の剛性を上げたりすることが可能です。
強度や剛性など、素材の特性を発現させたい方向へ炭素繊維が並ぶように配置し、組み合わせや積層順序を考慮しながら積層設計を行います。
積層は、単純にプリプレグシートを平面状に積み上げるのではなく、金型に沿って積み上げていくのがポイントです。曲面などがある場合は、裁断時点での工夫が求められるでしょう。
積層が完了したら、プリプレグの上から加圧するために空気を通さないプラスチックフィルムでシールを施します。
バギング
バギングとは、シール材と型の間に含まれる空気を引き抜く工程です。
プリプレグを硬化させる際に空気が残っていると、成形品内部に空孔(ボイド)ができる原因となります。
プリプレグの層間や型、シール材との間に空気が残らないよう真空引きを行います。
加圧・加熱によって硬化させる
プリプレグを圧力容器(オートクレーブ)に入れて加圧・加熱し、硬化させます。
使用するプリプレグの種類や形状により異なるものの、一般的にオートクレーブ成形が完了するには数時間が必要です。
オートクレーブ内部で成形品の温度に偏りが出ると、変形が起きる恐れがあります。
成形品全体が均一な昇温となるように制御しながら加熱するため、長い時間がかかるのです。
型から外す
成形が終わったら、成形品を型から外します。
型の表面には離型剤による離型処理が施されているものの、接着力によって張り付いています。
破損を防ぐために、力尽くで外そうしないようにしましょう。
仕上げ加工
型から外した製品に対して、必要に応じて以下の仕上げや後処理を行います。
- 外周のトリミング
- 端面を滑らかにする
- 表面処理
- 穴あけ など
まとめ
オートクレーブ成形の概要やメリット・デメリット、成形工程の手順を解説しました。
オートクレーブ成形は金型を使用するものの、試作や少量製作にも向いている加工方法です。
ただし、成形に時間がかかる、初期費用が高くなるといったデメリットも踏まえておきましょう。
オートクレーブ成形で納得のいく成形を行うためには、製作したいシーンや製品形状に応じた技術や実績を持つ加工業者を選ぶことが重要です。
オートクレーブ成形を活用した部品製造を検討している方は、ぜひ「Taiga(タイガ)」をご活用ください。Taigaは、無料で経験豊富な業者に相談できるサービスです。
難易度の高い部品や新規部品の開発、少量生産、試作から量産まで、コストを抑えつつ効率的に進めることが可能です。
Taigaに登録してみる