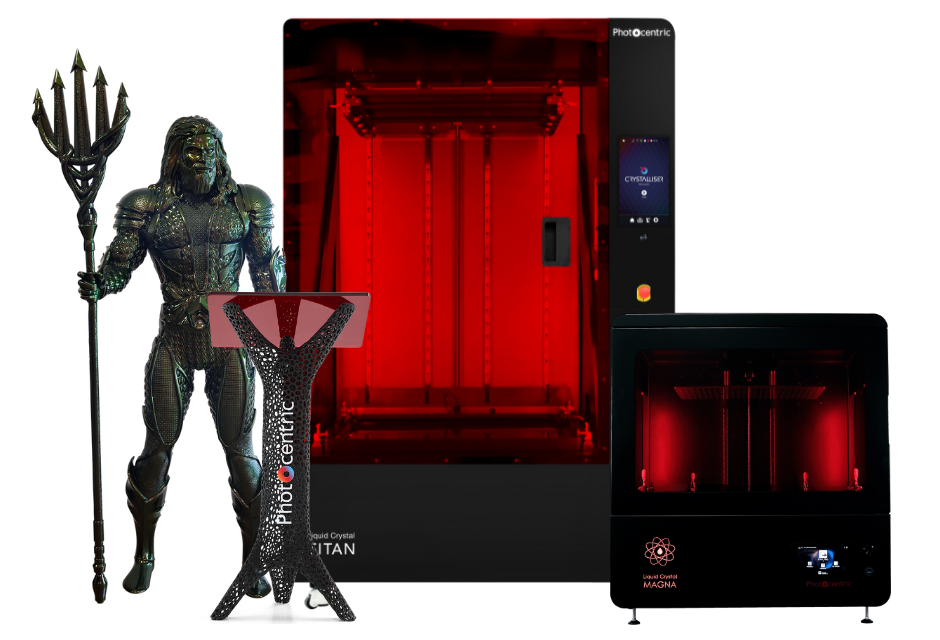
3Dプリンターの造形方式の中でも、歴史が長い「光造形」。
今でも試作品の造形や製品の小ロット生産まで幅広く活用されているプリント方法です。
とはいえ、現在ではさまざまな3Dプリント方法があり、選択肢もさまざま。
「光造形(LCD)の仕組みも知っておきたい」「ほかの造形方法と比べて何が違うの?」という疑問をお持ちの方も多いでしょう。
そこで本記事では、光造形の仕組みやメリット・デメリット、使用時の注意点まで詳しく解説します。
Taigaで技術提案を受ける目次
光造形とは?仕組みや歴史
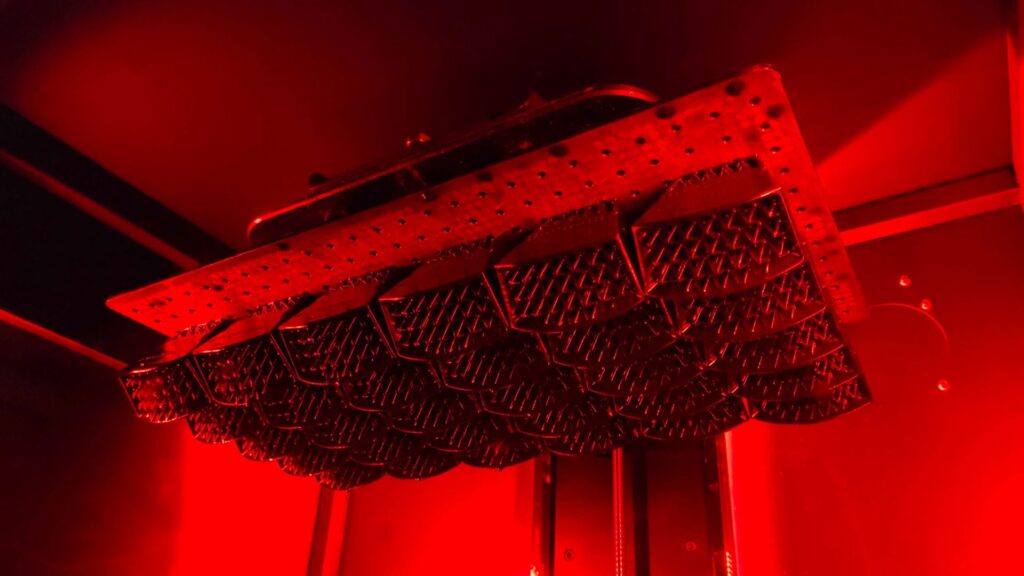
光造形は、3Dプリンターの中で最も歴史ある造形方式です。
液体の光硬化性樹脂にUVライトやレーザーを照射し、層ごとに硬化させながら積層を行います。
そのため、高精度で滑らかな表面に仕上がるのが特徴です。
光造形技術については、もともと1980年に日本の小玉秀男氏が「立体図形作成装置」として特許出願しましたが、当時は特許取得には至りませんでした。
その後、1986年にアメリカのチャック・ハル氏が光造形方式の米国特許を取得し、3D Systems社を設立して世界初の光造形3Dプリンターを製品化しています。
そして、2006年に特許が失効してからは多くのメーカーが開発・生産を行い、3Dプリントの技術は現在も進化を続けているのです。
光造形とFDM(熱溶解積層法)の違い
3Dプリンターの代表的な造形方式には、光造形のほかにもFDM(熱溶解積層法)があります。
FDMは、加熱ノズルで熱可塑性樹脂を溶融して層状に積み上げる方法で、溶解した素材は積層後に急速に冷却され固化します。
一方、光造形は液体樹脂を光で硬化させる方式です。
光造形はFDMと比べて高精度で滑らかな表面仕上げになる一方、FDMは材料コストが低く大型造形に適しています。
光造形には3つの方式がある
光造形には、DLP方式・LCD方式・SLA方式の3つの種類があります。それぞれ、以下で詳しく見ていきましょう。
DLP方式
DLP(Digital Light Processing)方式は、プロジェクターのような仕組みで造形面全体に一度に紫外線を照射する3D造形技術です。
特定の箇所に一点ずつ照射する方法とは異なり、短い時間でプリントすることができます。
また、DLP方式では少ない材料で造形でき、レジンの劣化を最小限に抑えられるのもメリットです。
一方、造形範囲が広くなると精度が粗くなる傾向があるため、大きなパーツの造形には向いていません。
LCD方式
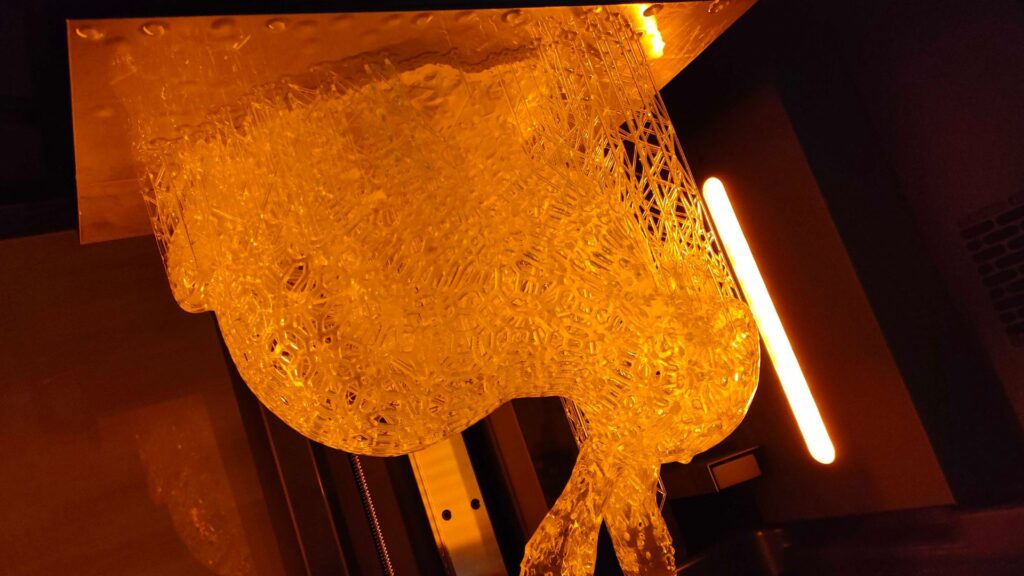
LCD(Liquid Crystal Display)方式は、DLP方式と同様に面状に紫外線を照射しますが、液晶ディスプレイを使用する点で異なります。
LCDパネルの各ピクセルが光のマスクとして機能し、レジンを個別に硬化させることが可能です。
ただし、LCDパネルは造形時の熱や紫外線により劣化するため、定期的な交換が必要でランニングコストがかかる点に注意が必要です。
とはいえ、比較的低コストで高解像度の造形ができるため、個人用や小規模な製造に適しています。
SLA方式
SLA(Stereolithography)方式は、レーザーを使用して樹脂を硬化させる最も古典的な光造形方式です。
大型の造形物も一体で作れる利点がありますが、造形速度はDLPやLCD方式に比べてやや遅くなります。
また、多くの樹脂を用意する必要があり、長期保管によって樹脂が劣化する点も課題です。
ただし、最近では最新技術によって造形時間や樹脂の劣化の課題を解決するプリンターも開発されています。
光造形(LCD)のメリット
ここからは、光造形(LCD)のメリットについて解説します。
高精度な造形が可能
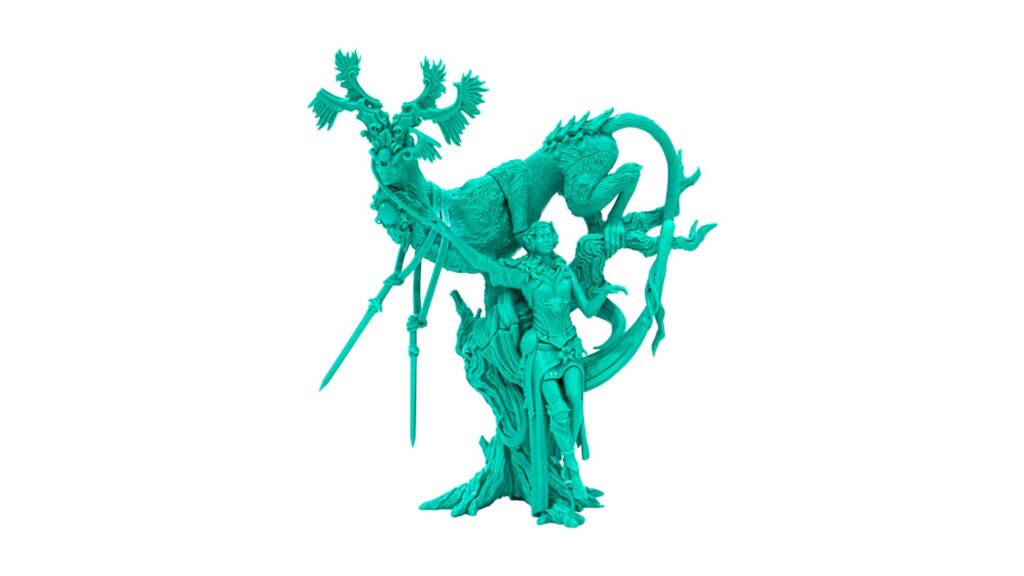
LCD方式の光造形3Dプリンターは、非常に高い精度で造形物を作成できます
微細な構造や複雑な形状を正確に再現し、0.5mm以下の微細表現も可能です。
また、積層痕が目立たず、滑らかな表面を実現できるため、試作品から最終製品まで幅広いシーンで利用できます。
造形にかかる時間が短い
LCD方式では、一度に面全体を硬化させるため、造形速度が非常に速いのが特徴です。
従来のSLA方式のように点状に硬化させる必要がないため、大きな造形物や小さな製品の複数造形も効率的に行うことができます。
さまざまな材料で造形できる
LCD方式では、さまざまな光硬化性樹脂を使用できるのもメリットです。
標準的な樹脂から、柔軟性のある樹脂・高強度樹脂・耐熱性樹脂まで、幅広い特性を持つ材料が利用可能です。
製品の用途や要求される性能に応じて、最適な材料を選択できるでしょう。
透明な造形物にも対応可能
LCD方式の光造形3Dプリンターは、特殊な透明樹脂を使用することで、透明な造形物の作成も可能です。
光学部品やディスプレイカバー、流体解析用モデルなど、透明性が重要な製品開発において大きな利点といえるでしょう。
光造形(LCD)のデメリット
ここからは、光造形のデメリットについてそれぞれ解説します。
二次硬化が必要なケースもある
LCD方式の光造形では、造形中に受ける光の量が部位によって異なるため、造形直後の部品が完全に硬化していない場合があります。
強度を上げるために二次硬化処理を行うと、製造時間の延長や追加設備が必要になることもあるでしょう。
また、二次硬化の条件によっては寸法精度に影響を与える可能性もあり、使用する樹脂の種類や造形物の厚みに応じて適切な設定が必要です。
造形後に洗浄やサポート材の処理が必要
LCD方式の光造形では、造形後に未硬化樹脂の洗浄とサポート材の除去が必要です。
この際、複雑な形状では処理に手間がかかり、跡が残ることもあります。
太陽光や紫外線に弱い
光造形で使用される光硬化性樹脂は、一般的に太陽光や紫外線に弱い特性があります。
長期間にわたって紫外線にさらされると、変色や劣化が進行する可能性があるため、屋外での使用や長期保存を想定した製品開発では配慮が必要です。
対策として、UV保護コーティングや、耐UV性の高い特殊樹脂を使用することも検討しましょう。
光造形(LCD)で使用する材料
光造形で使用される主な材料は光硬化性樹脂(レジン)で、紫外線や可視光線に反応して硬化する特性を持ちます。
樹脂においては、標準樹脂や高強度樹脂、柔軟性樹脂や耐熱性樹脂、生体適合性樹脂など、さまざまな特性を持つ種類が開発されており、最近ではセラミックスや金属粒子を含む特殊樹脂も登場しています。
光造形(LCD)が用いられるシーン
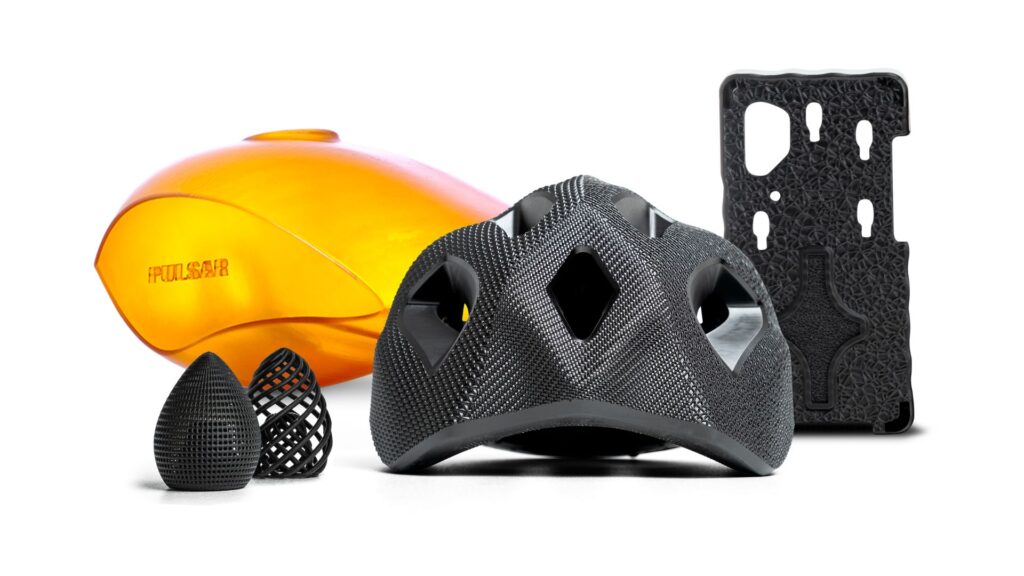
光造形は、その高精度と表面品質の良さからさまざまな場面に対応可能です。
例えば医療分野では、患者固有の解剖モデルや手術ガイドの作成にも利用されています。
そのほか、試作品作成や治具・工具の製造、金型作成、ロストワックス鋳造用のモデル作成にも適しており、特にデザイン性が求められるアイテムやオーダーメイド製品に最適です。
光造形(LCD)で3Dプリントをする際の流れ
光造形で3Dプリントを行う際の一般的な流れは以下の通りです。
- 3Dモデルの作成とデータの最適化
- プリンターの準備(レジン充填)
- 造形
- 後処理(洗浄・サポート材除去)
- 二次硬化
- 仕上げ
まず、CADソフトで3Dデータを作成し、サポート部分を追加してスライス処理を行います。
次に、レジンタンクを充填し、光を照射して層ごとに硬化と剥離を繰り返して造形します。
完成後は未硬化樹脂の洗浄、サポート材の除去、必要に応じてUV光による二次硬化と表面処理を行います。
光造形(LCD)で3Dプリントをする際の注意点
光造形3Dプリントを行う際は、用途に適した樹脂の選択が重要です。
造形物の方向や配置は品質や後処理に影響するため、慎重に検討する必要があります。
また、薄肉や平板形状では反りや変形に、厚肉の場合は気泡(ボイド)の発生を防ぐための工夫が必要です。
さらに、洗浄や二次効果などの後処理は最終的な品質を左右するため、慎重に行わなければなりません。
まとめ
光造形方式、特にLCD方式の3Dプリンターは、高精度・高速造形・豊富な材料など、多くの利点を持っています。
光造形は、製品開発プロセスの効率化や品質向上に大きく貢献する一方で、後処理の必要性や材料の特性に関する制約もあります。
高品質な造形結果を得るためには、適切な機器の選択と運用が不可欠です。
また、自社導入には専門知識を持つスタッフの育成と設備整備が必要になるため、外部の3Dプリントサービス業者の利用も選択肢となるでしょう。
3Dプリントを活用した部品製造を検討している方は、ぜひ「Taiga(タイガ)」をご活用ください。Taigaは、無料で経験豊富な業者に相談できるサービスです。
難易度の高い部品や新規部品の開発、少量生産、試作から量産まで、コストを抑えつつ効率的に進めることが可能です。
Taigaで技術提案を受ける