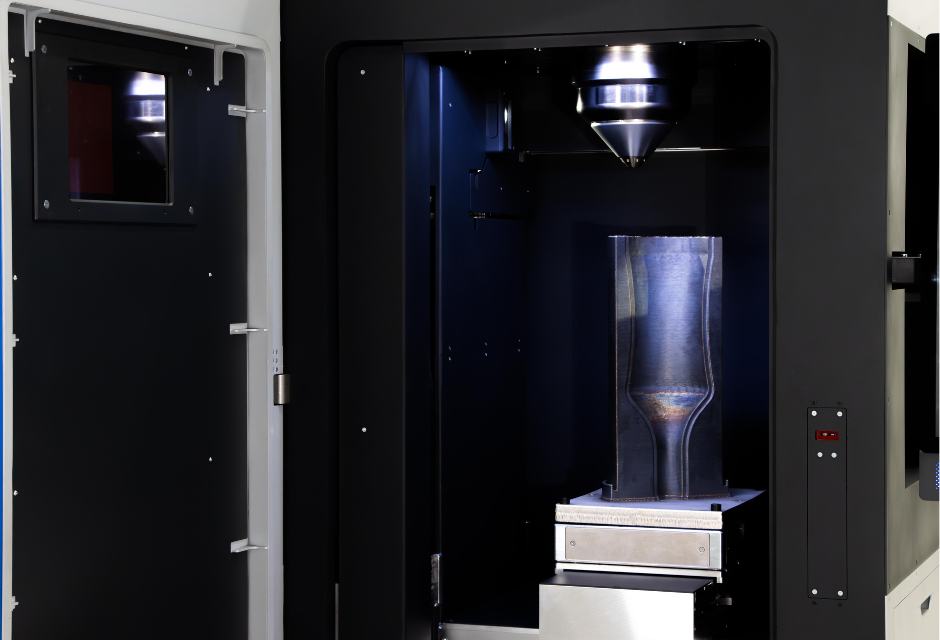
金属3Dプリンティングは革新的な製造技術として、製品開発の最前線で注目を集めています。
従来の加工方法では実現できなかった複雑な形状や高い設計自由度を実現できるため、多くの製造メーカーにとって大きな選択肢となりつつあります。
そこで本記事では、金属3Dプリンティングの仕組みからメリット・デメリットまで、製品開発担当者の皆様に役立つ知識を徹底解説します。
Taigaで技術提案を受ける目次
金属3Dプリンティングとは?金属プリントの仕組み
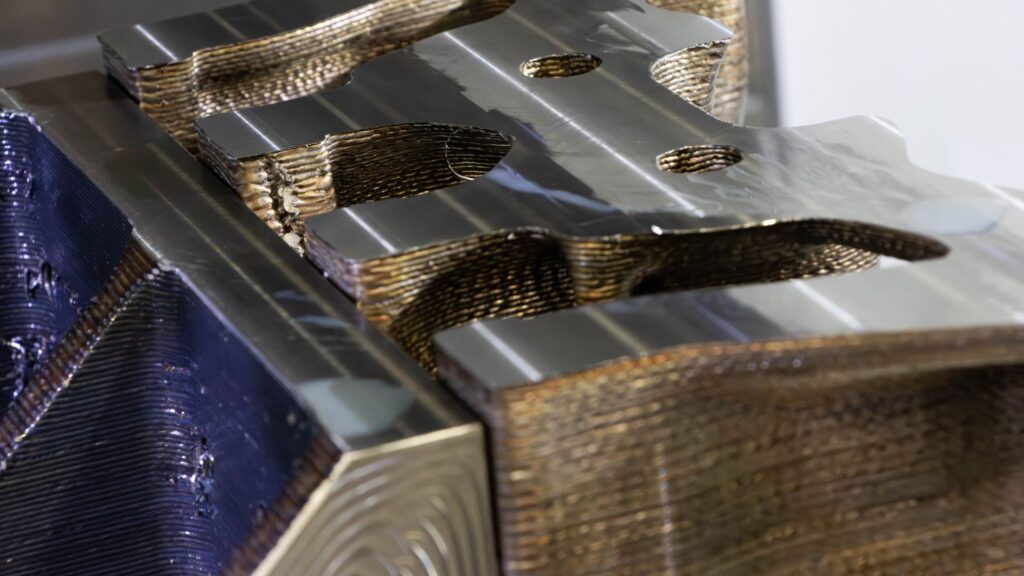
金属3Dプリンティングとは、3次元CADデータを基に金属粉末を積層して立体物を造形する技術です。
造形にはパウダーベッド(PBF)方式が採用されることが多く、レーザーや電子ビームで金属粉末を溶融・固化させながら層状に積み重ねる仕組みです。
ステンレス鋼やチタン合金などの金属粉末を使用可能で、複雑な形状や中空構造の造形も実現することができます。
また、専用の型を必要とせず、高強度・耐熱性を持つ部品を製造できる点も魅力です。
金属3Dプリンティングのメリット
金属3Dプリンティングのメリットについて解説します。
複雑な形状の造形に向いている
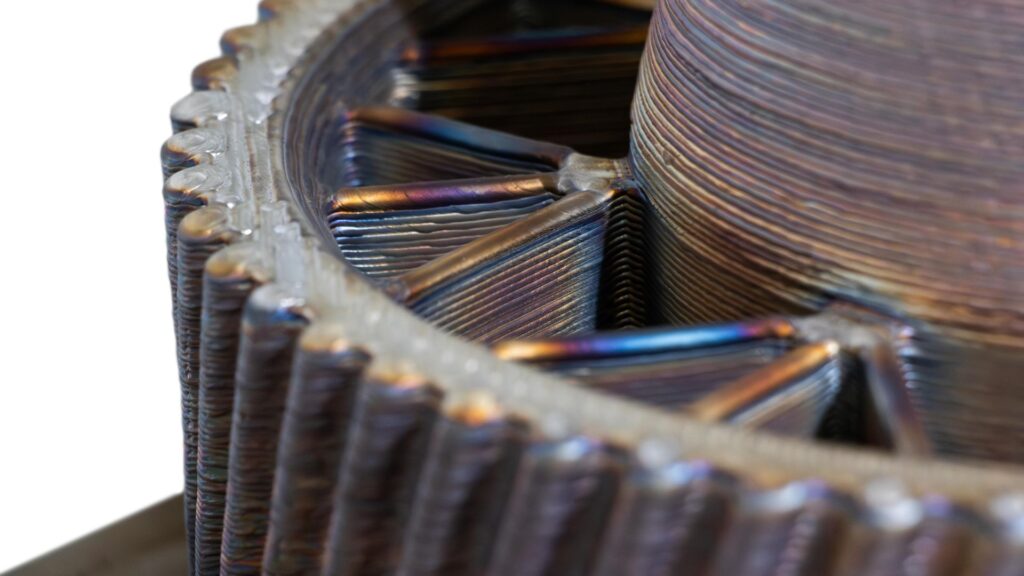
金属3Dプリンターは、従来の金属加工では困難だった複雑な形状の造形が可能です。
金属粉末をレーザーで少しずつ溶かす工程を繰り返すことで、工具では到達できない箇所や、鋳造では成形できない形状も成形できます。
設計の自由度も高く、中空構造による軽量化やメッシュ構造など、革新的な造形ができる点も魅力です。
金属の特性を活かして造形できる
金属3Dプリンターは、さまざまな金属材料を使用できるので、製品の性能を最大限に引き出すことができます。
ステンレス鋼・アルミニウム合金・チタン合金・銅などの金属材料を用い、樹脂材料では実現できない高強度や耐熱性を備えた部品の製造が可能です。
製品に求められる強度や耐熱性などの特性を維持しながら、あらゆる形状を造形できます。
生産コストの削減が可能
3Dプリンティング技術は金型製作が不要なため、試作品の作成や少量生産にかかるコストを大幅に削減できます。
試作品を簡単に作成できるため、後々の修正にかかるコストを抑えられるのもポイント。そのほか、部品の統合や軽量化によって材料費そのものを抑えることにもつながります。
造形物を軽量化できる
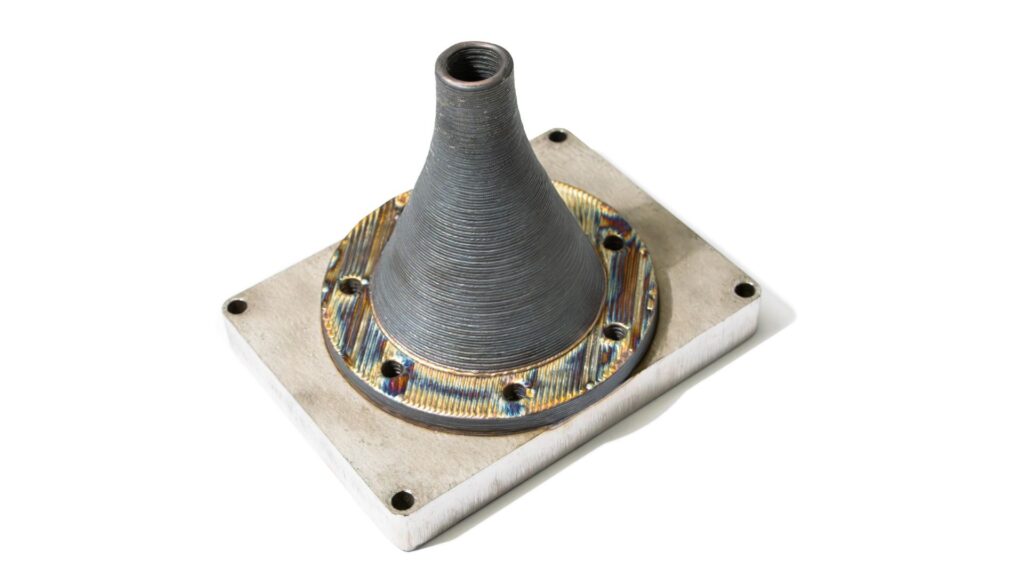
金属3Dプリンターでは、中空構造やラティス構造などの内部構造を持つ部品の製作も可能です。
そのため、強度を維持しながらでも軽量化を実現できます。
また、航空機や自動車の製造においては、従来の方法では難しかった複雑な形状の部品を効率的に作れるようになったことで、部品数を削減しながら製品の性能を高めることが可能です。
金属3Dプリンティングのデメリット
一方で、金属3Dプリンティングにはデメリットもあります。
造形の精度が粗い
金属3Dプリンティングの精度は、従来の機械加工と比べると劣り、実測値で約±0.1mmの精度が限界です。
そのため、より高い精度が要求される部分には後加工が必要になることを覚えておきましょう。
追加工程により、手間や時間、製造コストが増加する可能性があるため、製品に求める精度と技術の特性を十分に考慮する必要があります。
サイズや生産量に制限がある
現状の金属3Dプリンターは、造形可能なサイズに制限があり、大型製品の製作には複数の部品を組み合わせる必要があります。
また、製品を一つずつ時間をかけて造形していくため、大量生産には適していません。大量生産を目指す場合、他の製造方法と比べて時間がかかることを覚えておきましょう。
設計やプリント設定にノウハウが必要
金属3Dプリンティングを効果的に活用するには、3D CADの操作スキルや造形に関する専門知識が必要です。
具体的には、適切な配置や支持構造の設計、造形方式の特徴理解や専用ソフトウェアの使用など、幅広いノウハウが求められるでしょう。
これらの知識がない場合、目的に合った製作方法や設計が困難になるため、専門業者やデザイナーと連携しながら進めるのが大切です。
導入コストやランニングコストが高い
金属3Dプリンターの導入には高額な初期投資が必要で、本体価格だけでも3,000万円以上のコストがかかります。
さらに、不活性ガスの供給・排出設備・防塵防爆対策・専用スペースの確保など、設置環境の整備にも多額の費用がかかるでしょう。
加えて、材料となる金属粉末やメンテナンスなどのランニングコストも高額です。
金属3Dプリンティングの導入を検討する際は、これらのコストを総合的に評価する必要があります。
金属3Dプリンティングの種類
ここでは、金属3Dプリンティングの種類を5つ紹介します。
PBF方式
PBF方式は、10〜60μmの金属粉末にレーザーや電子ビームを照射し、層ごとに溶融・固化させる最も一般的な金属3Dプリンティング技術です。
高精度な造形が可能ですが、造形速度が遅く、大型造形には向いていません。
レーザーと電子ビームの2種類があり、それぞれ異なる特徴を持っているため、多種多様な金属材料に対応できるのが特徴です。
DED方式
DED方式は、ノズルから金属粉末やワイヤーを噴射し、同時にレーザーで溶融・積層する方式です。
大型部品や既存部品の補修に適しており、X・Y・Z軸の長さを調整することで大型造形も可能です。
後工程が少なく、異種金属の造形もできますが、PBF方式と比べて精度は劣ります。
FDM方式
FDM方式は、金属粉末を含んだフィラメントを溶融・積層する金属3Dプリンティング技術です。
樹脂と金属を混練した材料を使用するため、積層後に脱脂・焼結の工程が必要になります。
比較的安価で扱いやすい一方、造形物の強度や密度は他の方式より劣ります。
また、造形中の収縮を考慮した設計や後工程の焼結作業が必要です。
バインダージェット方式
バインダージェット方式は、金属粉末に接着剤を噴射して固め、後から焼結する方式です。
造形後に接着剤を取り除き、脱脂・焼結工程を経て完成します。
造形速度が速く、大型の造形物にも適していますが、精度や強度には課題があります。
金属3Dプリンティングの代表的な用途
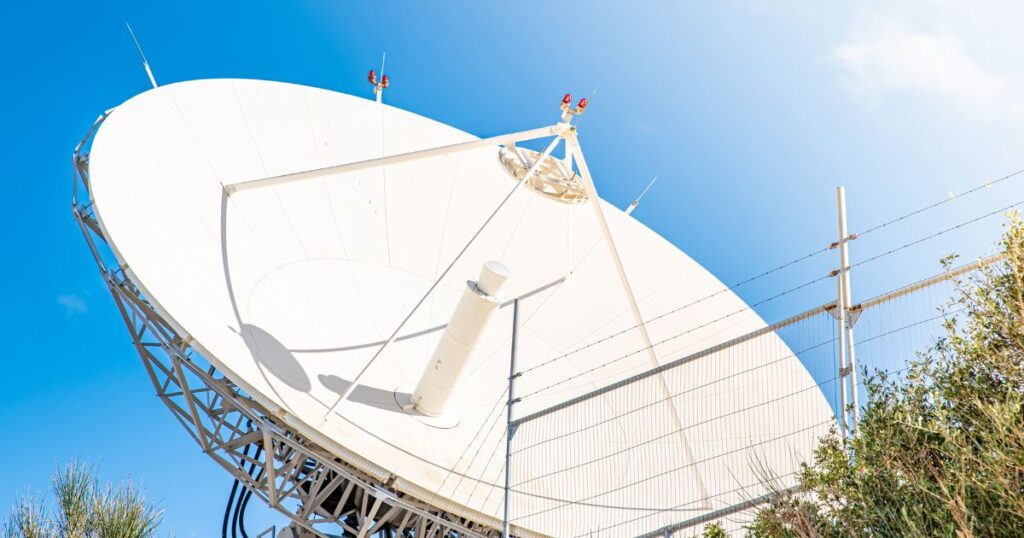
金属3Dプリンターは、主に以下の分野で活用されています。
- 航空宇宙産業
- 医療機器
- 金型産業
- 自動車産業
- 産業機械
航空宇宙産業では、ディーゼル燃料噴射器や小型衛星用アンテナなど、軽量化や複雑な形状の部品製造に活用されています。
他にも、患者に最適化されたインプラントや3次元冷却水管を持つ金型など、活用用途はさまざまです。
高い精度と効率性により、各産業に新たな可能性をもたらす次世代の製造技術として注目されています。
まとめ
金属3Dプリンティングは、製造業に革新をもたらす可能性を秘めた技術です。
しかし、金属3Dプリンティングのメリットを最大限に引き出すには、適切な造形方式の選択と専門知識が必要になります。
導入を検討する際は、自社の製品開発ニーズと金属3Dプリンティングの特性を十分に理解し、適切な方式を選ぶことが重要です。
専門知識を持つ信頼できる業者と連携することで、金属3Dプリンティングの利点を最大限に活かした製品を開発できるでしょう。
3Dプリントを活用した部品製造を検討している方は、ぜひ「Taiga(タイガ)」をご活用ください。Taigaは、無料で経験豊富な業者に相談できるサービスです。
難易度の高い部品や新規部品の開発、少量生産、試作から量産まで、コストを抑えつつ効率的に進めることが可能です。
Taigaで技術提案を受ける