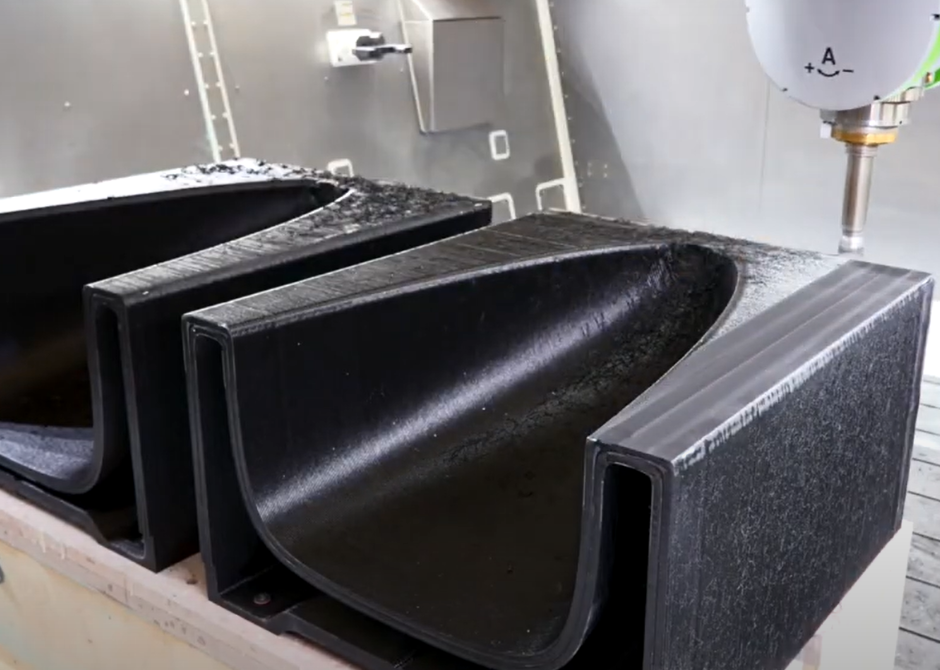
CFRP(炭素繊維強化プラスチック)は、その性質を活かしてさまざまな部品や製品の素材として活用されています。
しかし、CFRPを使った製品の製造にあたり「CFRPは難燃材料?」「CFRPを使って製品を作りたいけれども、向いている?」といった疑問を持つ方もいるのではないでしょうか。
今回の記事では、CFRPのメリットやデメリットとともに、難燃材料であるかどうかやCFRPの活用シーンについて解説します。
代表的なCFRPの加工方法についても紹介していますので、ぜひ参考にしてください。
Taigaに登録してみる目次
CFRP(炭素繊維強化プラスチック)とは?
CFRPとは、樹脂に強化材として炭素繊維を加えた複合材料のひとつです。
樹脂の軽さと金属に匹敵する剛性を持つ素材で、航空機をはじめとしたさまざまな部材として採用されています。
使う樹脂と炭素繊維の種類や炭素繊維の長さ、含有率や配置方向によって、性質が異なるのが特徴です。
ここからは、CFRPの持つ性質から、長所や短所を順に解説します。
CFRPの長所
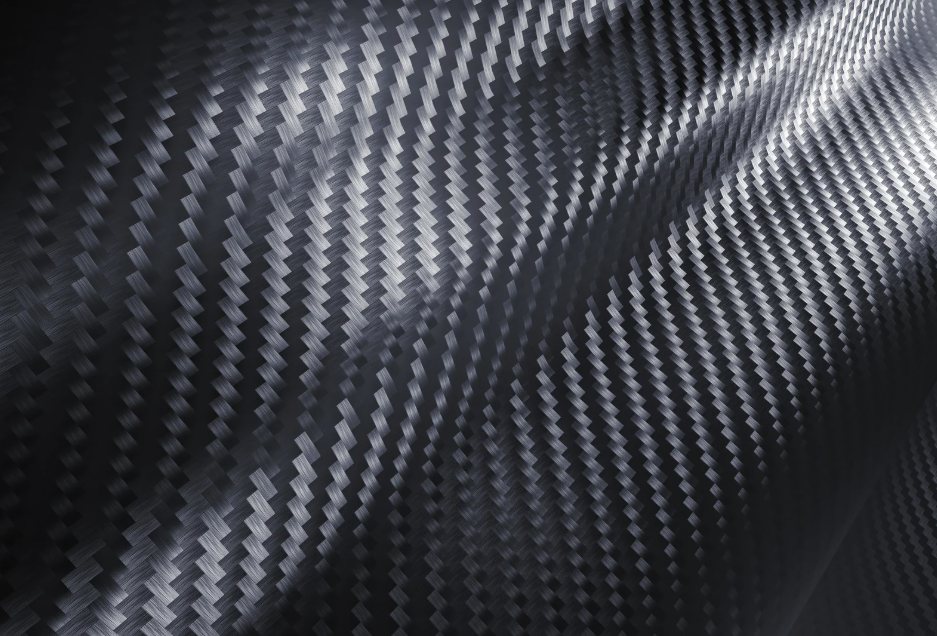
CFRPの長所は、主に以下の通りです。
- 軽い
- 強い
- 腐食しない
- 熱膨張しづらい
- 一体成形が可能
CFRPは、樹脂素材の持つ軽さと炭素を付帯することで得られる剛性を両立させた素材です。
また、熱によって伸びる樹脂、熱で縮む炭素をかけ合わせたことで、熱膨張にしづらい特性も持っています。
これにより、一体成形ができるため、金属と比べると効率的な成形が可能な点もメリットです。
CFRPの短所
CFRPは多くの長所がある一方で、以下のような短所もあります。
- 製造が煩雑
- 量産性が低い
- コストが高い
CFRPは、樹脂と炭素の異方向材料同士をかけ合わせた素材のため、加工時には複雑な材料設計が求められます。そのため、量産には向きません。
また、CFRP自体が高価な材料のため、加工コストが高くなる点もデメリットです。
CFRPは難燃材料?
CFRPはある程度の耐熱性を持っている素材ですが、金属と比較すると難燃性は低いです。
一方で、CFRPは軽量かつ剛性・疲労特性・耐環境特性が高い素材であることから、軽量化や燃料効率性の向上を目的に、自動車や航空機、宇宙分野での部材として活用される機会が増加しています。
そのため、近年では難燃性を兼ね備えたCFRPが求められており、実際に材料特性の解析や材料開発の技術が進歩したことで、難燃性をカバーしたCFRP素材の研究や開発が進んでいます。
CFRPが採用されるシーンや製品例
CFRPが採用されているシーンや主な製品の例を解説します。
航空宇宙分野
航空宇宙分野では、機材の軽量化や耐疲労性の向上、耐熱性や難燃性の向上を目的に、以下のような用途でCFRPが活用されています。
- 航空機1次構造材(主翼、尾翼、胴体、フロアビーム)
- 航空機2次構造材(補助翼、方向舵、昇降舵、フェアリング)
- 航空機内装材(座席、フロアパネル、ラバトリー)
- ロケット部材(衛星フェアリング、段間部、モーターケース、ノズルスロート)
- 人工衛星(アンテナ、太陽電池パネル、チューブトラス構造材)
- 電波望遠鏡(アンテナ、支柱)
自動車分野
自動車やバイクの分野では、軽量化や耐疲労性、振動減衰性、衝撃エネルギー吸収性といった安全性の向上、そして匠性の向上のためにCFRPが採用されています。
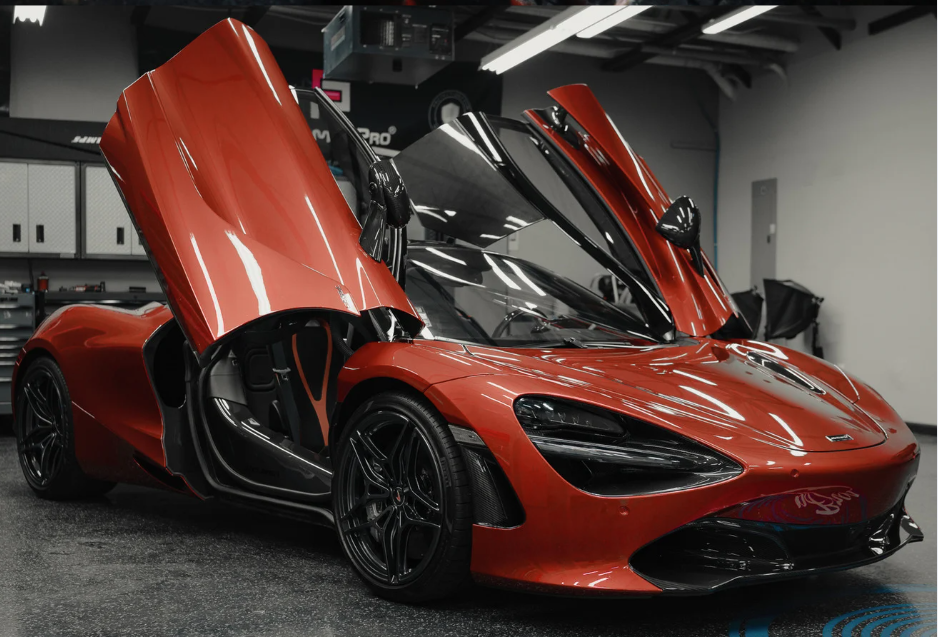
- 自動車構造材(モノコックボディ、クラッシュボックスストラクチャー)
- 自動車外板(ルーフ、フード、フェンダー、スポイラー)
- 自動車内装(シートフレーム、インストルメントパネル)
- 動力系(ホイール、スプリング、板バネ、ダンパー、プロペラシャフト、トランスアクスル、バッテリーケース)
- バイク構造材(ボディフレーム、スイングアーム)
- バイク外板(カウル、ギアカバー、マフラーカバー)
医療分野
医療や福祉介護分野では、CFRPの持つX線透過性を活かしつつ、機器の軽量化を目的に以下のような面で使用されています。
- 医療機器(天板、カセッテ、X線グリッド、リトラクター)
- 福祉・介護機器(車椅子、車椅子用携帯スロープ、義足、膝継手、杖、アシストスーツ)
その他産業分野
ほかにも機器の軽量化や耐腐食性、剛性の面から、以下のような幅広い産業分野の部材にCFRPが活用されています。
- 鉄道(車体、車両台車、座席、止水版)
- 機械部品(搬送用ロボット、板バネ、ロボットアーム、アシストスーツ)
- 高速回転体(遠心分離機ローター、ウラン濃縮筒、フライホイール、工業用ローター、シャフト、人絹ポット)
- 電気部品(パラボラアンテナ)
- 土木建築(コンクリート補強材、ケーブル、ロッド)
CFRPの成形方法
CFRPはさまざまな加工方法に対応できる素材のため、用途に応じた成形方法を選ぶことが重要です。
主なCFRPの成形方法の特徴を解説します。
オートクレーブ成形
オートクレーブ成形とは、オートクレーブと呼ばれる圧力釜内で基材であるプリプレグを積層し、さらにバギングフィルムを被せて真空状態にしてから減圧、最後に圧力をかけて加熱硬化する成形方法です。
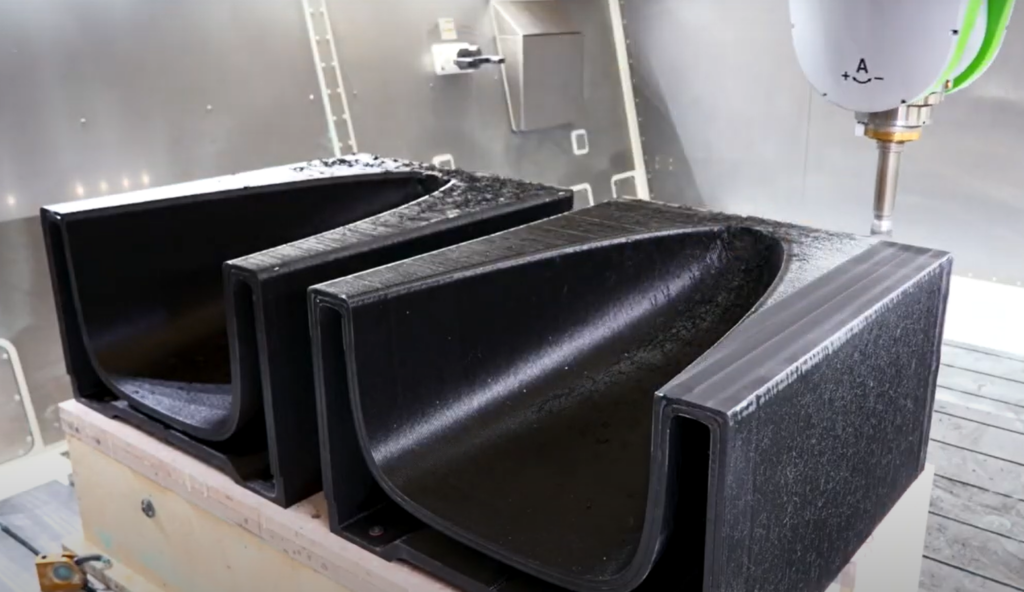
圧力をかけることでCFRPの物理強度の向上が期待できます。
品質や性能を重視したいときや、複雑な形状のCFRP製品を製造したいときに適しています。
ただし、成形工程のサイクルが長いだけでなく、プリプレグが高価なため加工納期やコストに難点があります。
オーブン成形
オーブン成形は、減圧まではオートクレーブ成形と同じ工程で行いますが、減圧ではなく真空圧をかけて加熱硬化を行う成形方法です。
オートクレーブ成形と比較すると、加工や材料のコストを抑えられ、大型の成形品にも向いています。
ただし、加工品の性能や品質面ではややオートクレーブ成形に劣り、複雑な形状の成形には向いていません。
引抜成形
引抜成形とは、液状の樹脂へ炭素繊維を金型に引き込んで浸してから通し、加熱硬化させて成形する方法です。
プルトリュージョン成形とも呼ばれています。
ロッド状やパイプ状といった一定の断面形状を持つ成型品の加工に向いています。
連続成形も可能なため、制作工程の効率化にも有効です。
フィラメントワインディング成形
フィラメントワインディング成形とは、フィラメントを基材として加熱硬化させ、成形する方法です。
チューブやタンク形状の成型品に適しています。
液状の樹脂を含浸した炭素繊維のトウをマンドレルに巻き付けたあとに加熱します。
樹脂槽(バス)に炭素繊維を浸しながら巻き付ける方法と、あらかじめトウを樹脂に含浸させたトウプリプレグを巻き付ける方法があります。
基材であるフィラメントは安価で手に入り、加工の自動化も可能です。
工期やコストを抑えつつ制作を進めたいときに向いています。
RTM成形
RTM成形とは、オス・メス一対の密閉型の金型を使用する成形方法です。
炭素繊維を製品の形状に予備整形したもの(プリフォーム)を金型へ配置し、液状の樹脂を圧入、含浸してから加熱硬化させます。
なお、RTM成形の中でもメス型のみを使用して真空圧で硬化させる場合は、VaRTM成形(バキュームアシステッドRTM)と呼ばれます。
RTMは小・中形、VaRTMは中・大形の成型品の加工向けです。
いずれのRTM成形も、物性強度の向上や形状精度を担保しての加工に向いています。
プレス成形
プレス成形とは、金型やシートへ圧力をかけ、加熱硬化によって成形する方法です。
金型に積層したプリプレグやSMCなどの樹脂を含浸させたシートを使用します。
コストと加工効率のバランスの取れた成形方法で、大型製品の加工に適したプレス成形を行っている業者もあります。
シートラップ成形
シートラップ成形とは、マンドレルと呼ばれる鉄芯を使った成形方法です。
マンドレルにプリプレグを巻き付けテーピングしたものを加熱硬化します。
その後、脱芯して成形するため、パイプやロール形状の成形に向いています。
まとめ
本記事では、CFRPの特徴やメリット・デメリット、難燃材料であるかと加工方法について解説しました。
CFRPは機材や機器の軽量化、燃料効率性向上などの観点から、今後も高いニーズが見込まれる素材です。
防火性の面から、難燃性を高めたCFRPの研究開発も進められています。
CFRPの加工を検討しているときには、製造したい製品に適した加工方法を取り扱っている業者へ依頼することが重要です。
CFRP加工を活用した部品製造を検討している方は、ぜひ「Taiga(タイガ)」をご活用ください。
Taigaは、無料で経験豊富な業者に相談できるサービスです。
難易度の高い部品や新規部品の開発、少量生産、試作から量産まで、コストを抑えつつ効率的に進めることが可能です。
Taigaに登録してみる