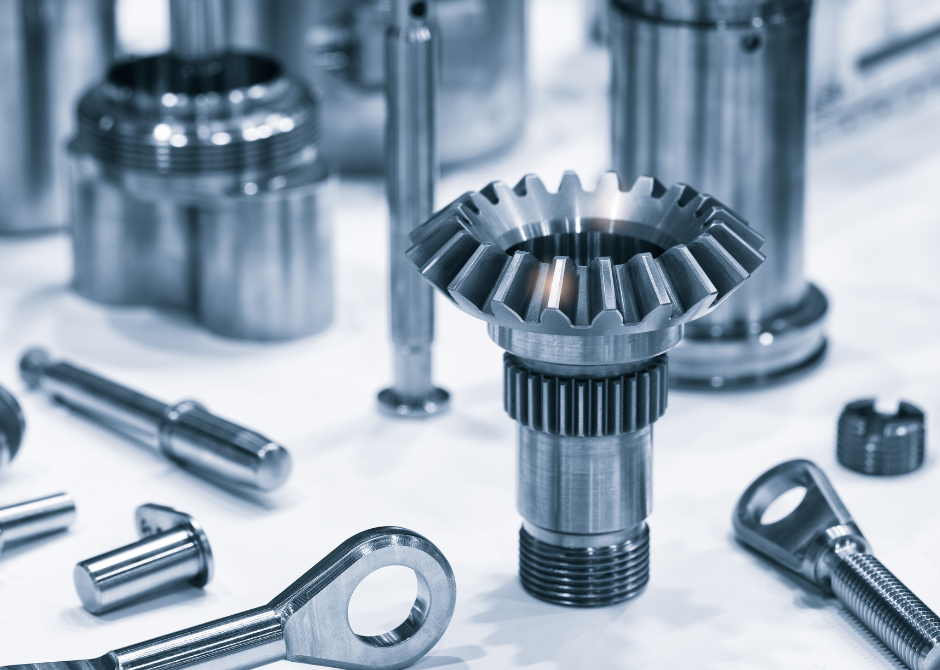
自動車をはじめとした機器製品は、さまざまな理由から軽量化が求められることがあります。
そのため、機器の軽量化のために部品そのものを軽量化したいと検討しているものの「軽量化に適した素材がわからない」「素材は変えずに部品の軽量化はできるかが知りたい」といった疑問を持つ方も多いでしょう。
今回の記事では、製品の軽量化が求められている背景や軽量化実現できる具体的な素材、素材を変えずに部品を軽量化する方法を解説します。
部品の軽量化のメリットや注意点についても解説していますので、ぜひ参考にしてください。
Taigaに登録してみる目次
なぜ今、製品の軽量化が求められているのか
機械や装置の軽量化が求められる背景には、持続可能性への取り組みがあります。
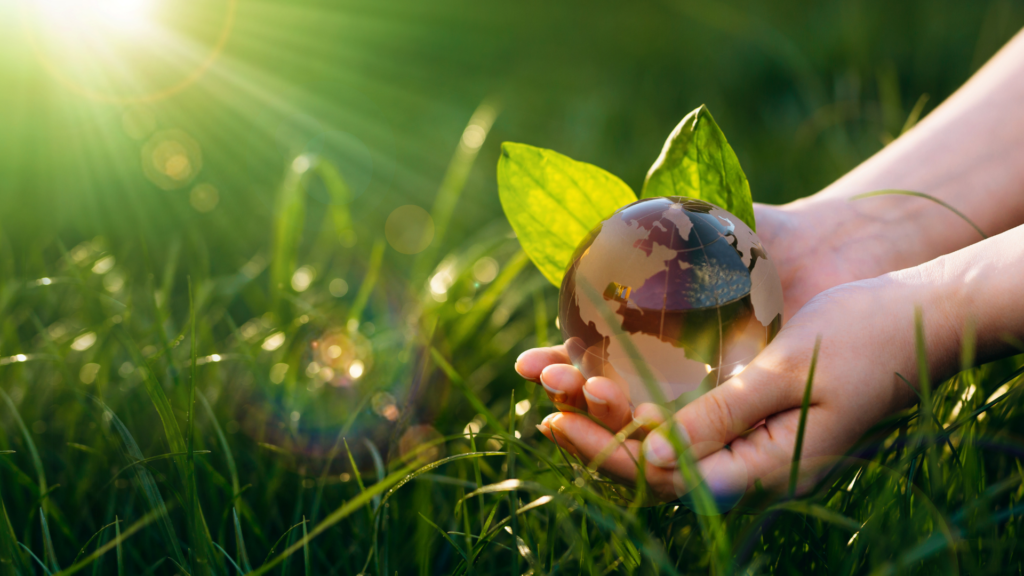
現在、世界各国では2050年までに温室効果ガス排出量実質ゼロ(カーボンニュートラル)実現に向けての取り組みが推進されおり、中でもガソリン車から走行中に排気ガスを排出しない電気自動車(EV)への変更が注目されています。
ただし、電気自動車は内燃機関ではなく電動モーターで駆動するため、モーターの重量がガソリン車よりも重く、走行距離が短くなってしまいます。
そこで、モーターが重くなった分、他の部品を軽量化することが求められているのです。
また、自動車はもちろん、航空機や産業機械などの燃料で駆動する機器については、部品となる金属製品の軽量化が求められています。
これらを踏まえると、今後もカーボンニュートラルや持続可能性の推進のために、金属製品の軽量化ニーズは高まっていくことが予想されるでしょう。
部品の軽量化を実現できる5つの素材
部品の軽量化を実現する方法のひとつに、既存の素材を他のものに変更する方法があります。
ここでは、部品の軽量化に有効な5つの素材を順に紹介します。
アルミニウム合金
アルミニウム合金とは、アルミニウムとほかの金属を掛け合わせた合金を使って作られた金属です。
アルミニウム合金には幅広い種類があり、1000~8000番台まで番号付けがされています。
中でも、アルミニウムと銅の合金である2000番台のジュラルミンや超ジュラルミン、アルミニウムと亜鉛、マグネシウム、銅の合金である7000系の超々ジュラルミンは、アルミニウムの持つ軽量性に、鉄鋼材にも匹敵する強度を持つ合金です。
特に、ジュラルミンは軽量性と強度を持つ合金として航空機の部品としても多く採用されています。
チタン合金
チタンは軽量かつ強度の高い金属のため、従来より自動車部品の素材として多く活用されてきました。
近年では、低コスト化されたチタン金属を使用したチタン合金も誕生しています。
チタン合金で作られた部品は自動車の軽量化を目的に、サスペンションロッドやエンジンバルブなどの自動車部品の素材として活用されています。
CFRP(炭素繊維強化プラスチック)
CFRP(炭素繊維強化プラスチック)とは、炭素繊維とプラスチック樹脂を合成して作られた素材です。
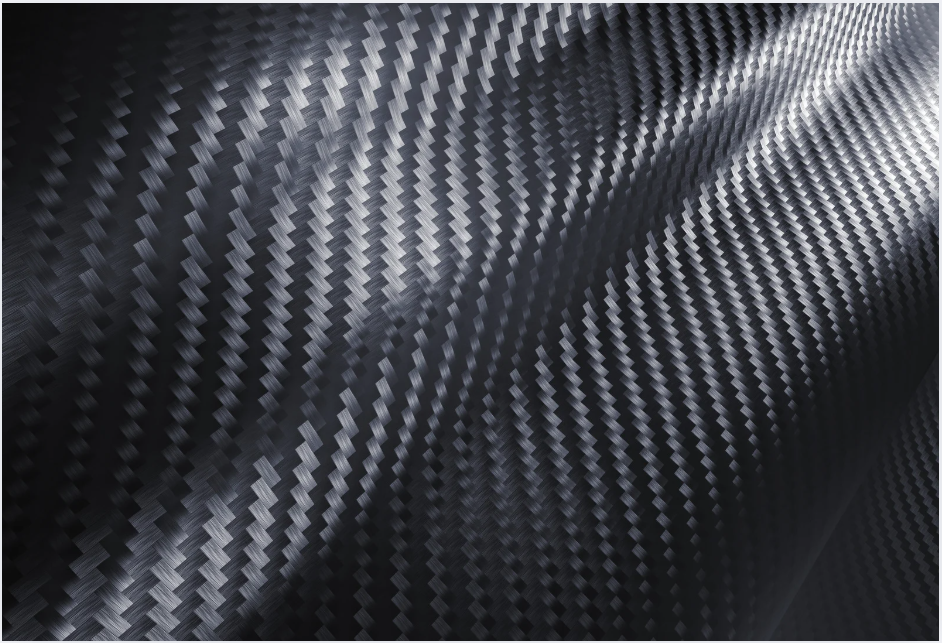
強靭かつ軽量である炭素繊維の特性と、プラスチックの持つ汎用性や強度を持ち合わせています。
腐食耐性や熱変形への強さも持つため、軽量化を目的とした自動車や航空機、スポーツ機器のほか宇宙事業にも採用されています。
マグネシウム合金
マグネシウム合金は、素材であるマグネシウムの入手のしやすさに加えて、実用金属の中でもっとも軽量かつ、比強度が大きい特徴を持つ合金です。
耐くぼみ性が高く、物質が衝突した際に発生する凹みがアルミニウム合金などに比べて小さいため、小型の部品加工の素材にも向いています。
実用金属の中でも最大の振動吸収性も持っていることから、自動車のホイールやステアリングなどの、振動を和らげるための部品の素材としても有効です。
高性能樹脂・エンプラ
高性能樹脂・エンジニアプラスチックとは、高熱での変形や割れが起きやすいプラスチックの弱点を克服した樹脂素材です。
高性能樹脂やエンジニアプラスチックの中には、耐熱温度が100度以上あり、強度や耐摩耗性が高いものも多くあります。
軽量性と強度、さらに熱による変形が起きないことから、自動車をはじめとした機器の部品の素材として多く活用されています。
素材を変えずに部品を軽量化する方法
材料の調達方法やコストなどの面から、素材は変えずに軽量化を実現したいというケースもあるでしょう。
その際は、加工方法を変えることで既存の素材のまま軽量化することも可能です。
既存の素材を変えず、部品を軽量化する方法を順に解説します。
肉抜き・中空構造に形状を変更する
軽量化の手段としては、製品の肉抜きや中空構造への設計変更が挙げられます。
設計段階で肉抜き穴を多く加える、構造上に空洞を入れることで、製品の素材はそのままに軽量化が可能です。
ただし、肉抜きや中空構造化を行うことで、製品の強度や剛性が落ちてしまうことがあります。
部品の用途や使用環境を考慮し、必要な強度や剛性を確保した上での設計が求められるでしょう。
薄肉化や板厚の変更
薄肉化や板厚の変更は、部品の構造をほとんど変えずに軽量化が実現できる方法の一つです。
設計変更などの手間が発生せず、設計時に部品の持つ課題や弱点も把握しやすいメリットもあります。ただし、薄肉化は鋳造・ダイキャストや樹脂成型、板厚の変更は製缶加工・板金加工といったように、軽量化に対応できる加工方法が限定されるのがデメリットです。
部品を軽量化するメリット
部品を軽量化することで、以下のようなメリットが得られます。
- 製品の燃費向上
- 性能面の向上
- 部品の寿命が長くなる
まず、部品を軽量化することで製品の燃費が向上します。
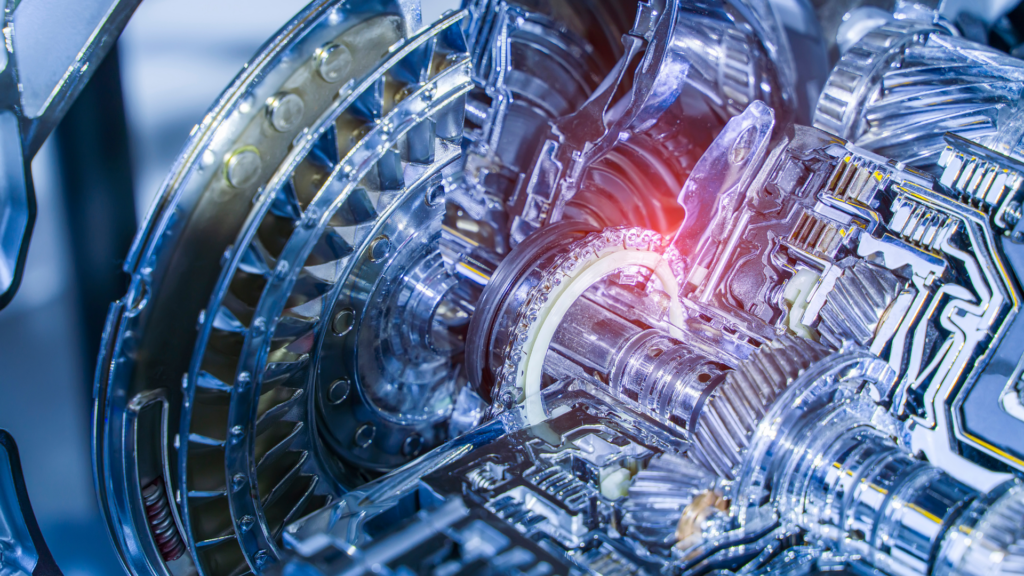
たとえば、自動車は重量が少ないほど走行に必要なエネルギーが少なくなるため、同じ燃料の量でより多くの距離を走れるようになるでしょう。
また、軽量化をすることで製品の性能面の向上も期待できます。
たとえば、自動車がカーブを曲がるときに働く遠心力は、自動車の重量が重いほど大きくなります。
反対に、自動車の重量が軽いほど遠心力は小さくなり、旋回性や操作性などが大きく高まるでしょう。
そのほか、部品が軽量化すれば、部品そのものの劣化や消耗を遅らせることにもつながります。
重い自動車を止めるにはブレーキパッドやタイヤの消耗も大きくなりますが、自動車が軽くなれば、各部品の消耗も小さくなるためです。
部品を軽量化する際の注意点
部品の軽量化には、メリットも多い一方でデメリットもあります。
素材や加工方法の変更によるコスト増加
軽量化を目的に素材や加工方法を変更すると、コストが高くなる場合が多いです。
軽量化することで耐久性が低くなり、交換頻度が高くなってコストが増えることを考慮しておきましょう。
耐久性や快適性などの低下
軽量化を行うことで部品の耐久性が低くなる可能性があります。
特に、自動車のホイールなどの接地面の多い部品は、軽量化によって自動車そのものの性能や安全性を確保できなくなることもあるでしょう。
軽量化によって、静寂性を高めるための機能が損なわれ、自動車運転時のノイズの発生原因となることもあります。
部品の軽量化に3Dプリント加工を採用する利点
軽量化を目的とした部品の製造や加工を検討しているときには、3Dプリンターの活用が有効です。
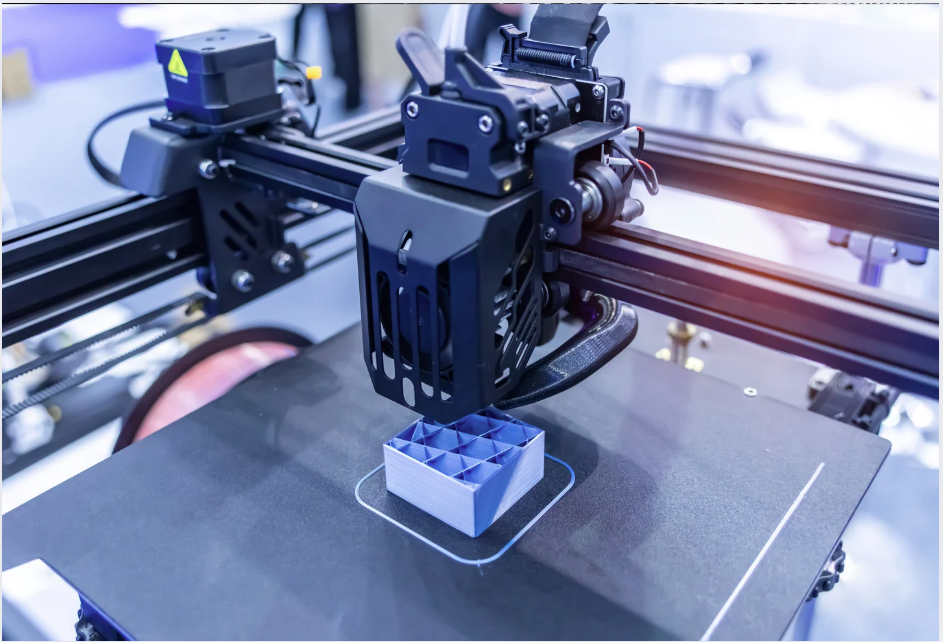
3Dプリンターを活用すれば、3DCADで作成した3Dデータから、短期間・低コストでの部品の試作や小ロット生産を実現できます。
また、樹脂素材から金属素材まで対応できるため、樹脂素材から部品を創るのはもちろん、金属製の簡単な型を作ることで量産にも対応できます。
特に、短納期や仕様変更の多い顧客ニーズに対応するための部品作成には、3Dプリンターが向いているといえるでしょう。
まとめ
部品の軽量化に有効な素材や軽量化を実現する方法、軽量化のメリットや注意点を解説しました。
カーボンニュートラルの実現などの観点から、今後も部品の軽量化のニーズは高くなることが予想されます。
設計変更やコスト増などの課題を踏まえつつ、3Dプリンターでの作成なども検討し、部品の軽量化を実現させましょう。
軽量な部品の製造・加工を検討している方は、ぜひ「Taiga(タイガ)」をご活用ください。Taigaは、無料で経験豊富な業者に相談できるサービスです。
難易度の高い部品や新規部品の開発、少量生産、試作から量産まで、コストを抑えつつ効率的に進めることが可能です。
Taigaに登録してみる