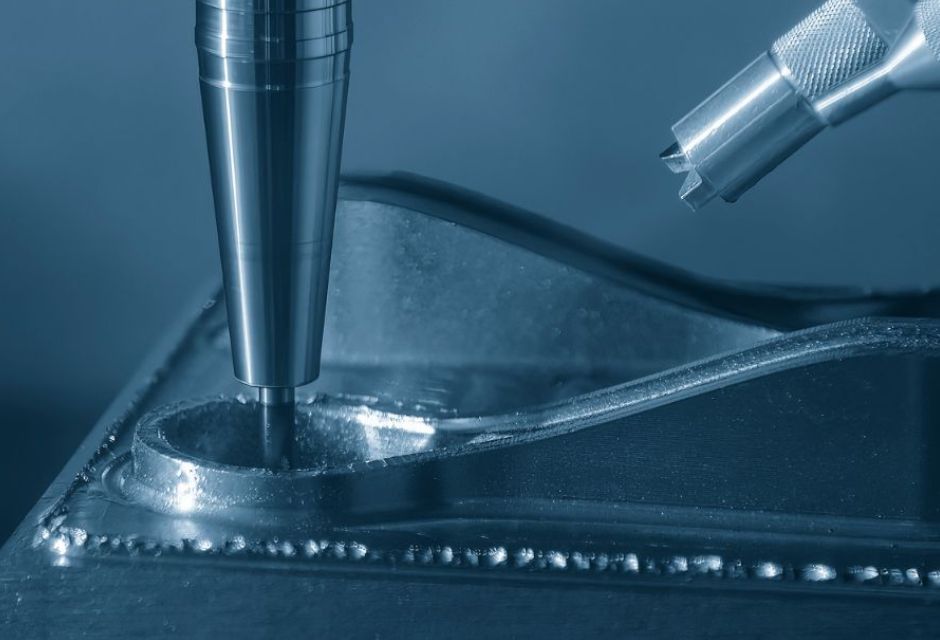
射出成形は、主に樹脂製品の成形加工の際に用いられる加工方法です。
しかし、最近では金属の製品や部品の成形手法としても注目されています。
今回の記事では、金属の射出成形の概要と似ている成形方法との違い、メリットやデメリットを解説します。
金属射出成形の手順も紹介していますので、ぜひ参考にしてください。
Taigaで技術提案を受ける目次
金属射出成形(Metal Injection Molding)とは?
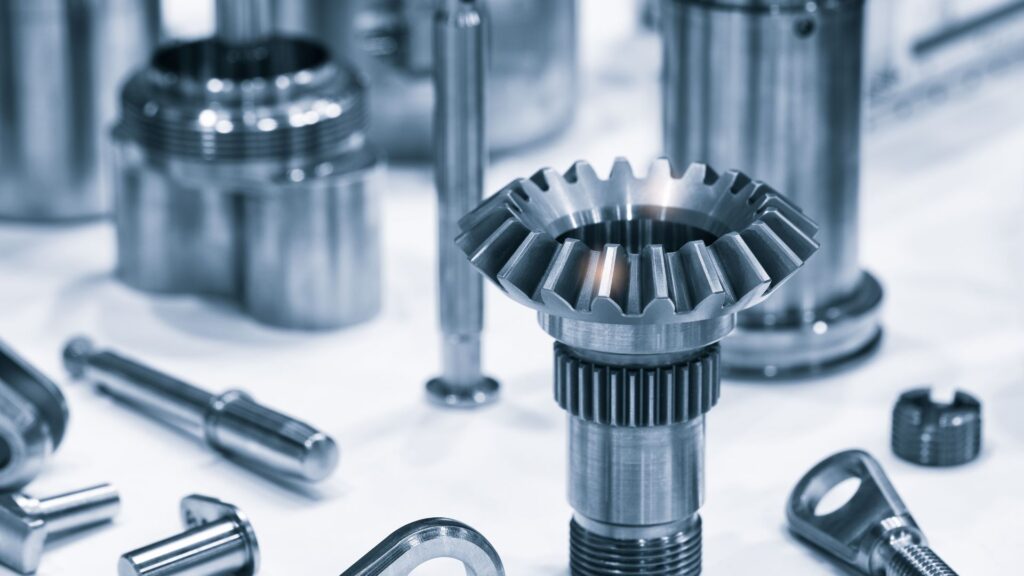
金属射出成形とは、樹脂の射出成形と金属粉末冶金の技術を組み合わせ、応用した成形方法です。
英語表記である「Metal Injection Molding」を訳して「MIM」と呼ばれることもあります。
一般的な樹脂の射出成形とは異なり、10ミクロンレベルの微細な金属粉末を原料とし、溶解はせずにつなぎを加えて射出成形をするのが特徴です。
そのため、チタンやステンレスなど加工難易度が高い材料でも、複雑形状への加工ができます。
金属射出成形は、自動車をはじめ、精密機械・電気機器・通信機器・医療機器の部品の製造にも採用できる可能性があり、近年注目されている成形方法のひとつです。
鋳造・鍛造と金属射出成形(MIM)の違い
金型を使用して金属を成形する方法には、鋳造・鍛造もあります。
鋳造は、金型に溶かした金属を流し込んだ後、冷やして固める手法です。
鍛造はインゴットを金型で挟み込み、プレスして引き延ばすことで成形する手法を指します。
金属射出成形は、金属の粉末と樹脂を混ぜて金型の中で射出成形を行うため、成形方法としてはまったく異なるものといえるでしょう。
焼結合金と金属射出成形(MIM)の違い
焼結合金は、金属の粉末をプレスして成形する方法です。
金属射出成形は金型を使用して射出成形をすることで、焼結合金よりも精度が高く、より複雑な形状の加工ができます。
金属射出成形(MIM)のメリット
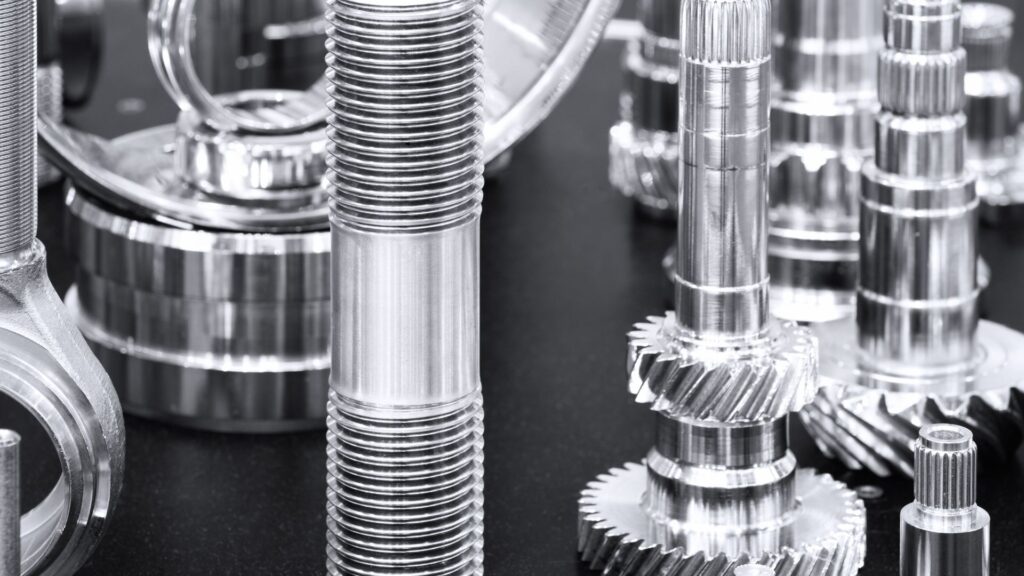
金属射出成形ならではのメリットも多くあります。
加工が難しい金属でも複雑な形状に加工できる
金属射出成形は、切削加工が難しい以下のような難削材も加工できます。
- 超硬金属
- チタン
- ステンレス
- タングステン など
また、金属射出成形では切りくずなどが出ない分、材料ロスが発生も発生しません。
高額な材料でも、材料効率を考えた加工が実現できます。
大量生産に向いている
金属射出成形では金型を使うため、大量生産にも向いています。一度金型を作ってしまえば、加工が難しい材料でも短時間で製作可能です。
また、金型を使用することで複雑な形状も簡単に加工できるため、コストを削減しつつ大量生産ができる点もメリットです。
高精度な加工が可能
金属射出成形は、材料を溶解させず成形体を脱脂・焼結して成形するため、高精度の加工が可能です。均一規格の部品など、高品質・高精度を求められる部品の製造にも向いています。
金属射出成形(MIM)のデメリット
金属射出成形には多くのメリットがある一方、デメリットもあります。
成形条件の設定にノウハウが必要
金属射出成形で使用する材料は流動性が高い一方、熱伝導性が高いため固まりやすいのが特徴です。
そのため、以下のような成形不良が発生しやすく、安定して成形を行うには正確な成形条件の設定が求められます。
よくある成形不良 | 状態 |
ショートショット | 金型内に材料が十分に充填されない |
バリ | 金型の合わせ目から材料がはみ出す |
ヒケ | 冷却時に材料が収縮する |
ウェルドライン | 材料の合流地点に線が生じる |
ボイド | 製品内部に空洞が生じる |
反り | 製品が曲がる |
フローマーク | 製品表面に流れの跡が出る |
ジェッティング | 金型内に材料が噴射して飛び散る |
一般的な射出成形よりも成形条件の設定が難しいため、加工には高い技術やノウハウが必須です。
二次加工が必要なケースもある
金属射出成形では、加工時にバリやショートが発生するため、二次加工が必要なケースもあります。
二次加工には当然手間や時間もかかるため、樹脂材料を使用した一般的な射出成形よりもコストは高くつくでしょう。
また、スプルーやランナーなど、製品以外の部分が成形されてしまうことも金属射出成形のデメリットです。
二次加工の必要性や材料の無駄によって、追加コストが発生する可能性があることを知っておきましょう。
少量生産には向いていない
金属射出成形は金型を使用するため、少量生産には向いていません。
金型の製作には費用はもちろん、作成期間が発生するため、少量生産でもある程度の制作期間や初期費用が発生します。
極端な例ですが、1つだけ部品を作りたい場合でも金型の制作が必要なため、少量生産には向かないのです。
設計に制約がある
金属射出成形は、金型から製品を取り出すための抜き勾配を考慮した設計が必要です。
また、サイズが大きい製品の成形には、大型の射出成形機と金型が必要になります。
設計上の制約をクリアできたとしても、製作コストは高くなってしまう可能性が高いでしょう。
金属射出成形(MIM)の手順
ここからは、金属射出成形の加工手順を紹介します。
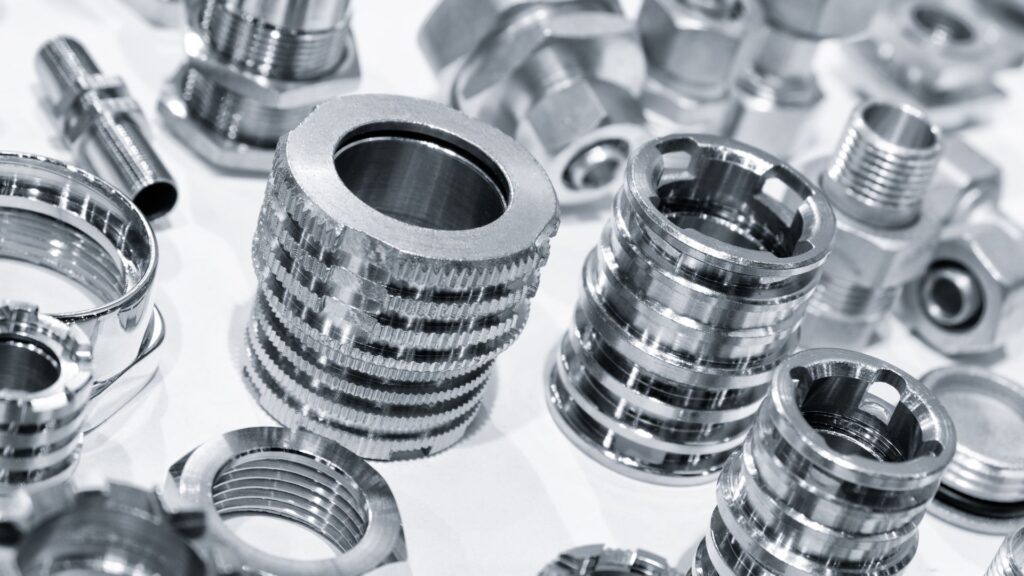
混練
まず、原料となる金属粉末と有機バインダ(結合剤)を、熱と圧力をかけながら均一に混ぜ合わせます。有機バインダとは、結合材とワックス成分の可塑材、潤滑材から構成される原料です。
この作業を「混練」と呼びます。
造粒
ペレタイザーという機械で混ぜ合わせた材料を加圧しながら絞り出し、ペレット状に成形する「造粒」を行います。
造粒によって作られた材料は、フィードストックと呼ばれます。
射出成形
材料の準備ができたら、成形機によって射出成形を行います。
金属射出成形で成形されたもの(グリーンパーツ)にはバインダーが含まれているため、本来必要なパーツよりも大きく作られます。
脱脂
脱脂は、バインダーの中に含まれている可塑材や潤滑材などのワックス成分を除去する工程です。
以下3つの方法のうちいずれかで行います。
脱脂の方法 | 特徴 |
溶媒脱脂 | 溶媒によってワックスを溶かす |
加熱脱脂 | 加熱してワックスを蒸発させる |
触媒脱脂 | 加熱しつつ触媒ガスで脱脂を行う |
適切な脱脂が行われないと、次工程の焼結時にワックス成分が炭素として残ってしまい、金属の組成に悪影響を及ぼします。
また、脱脂後のパーツ(ブラウンパーツ)は、ワックス成分が抜けているため変形や割れが発生しやすく、取り扱いに注意が必要です。
焼結
脱脂が終わったブラウンパーツを焼結炉で加熱し、焼結します。
焼結したパーツはシルバーパーツと呼ばれ、バインダーが消失した分体積が小さくなるのが特徴です。
二次加工
高い寸法精度を求められるネジ加工の場合などは、必要に応じてサイジング(コイニング)などの二次加工を行います。
金属射出成形の材料は通常の金属材(溶製材)と同様に熱処理やメッキ、塗装などの表面加工を施すことも可能です。
検査
金属射出成形では、製造する部品によって以下のような検査を実施します。
- 寸法検査
- 焼結密度の検査
- 化学検査
- 非破壊検査(X線など)
例えば、化学検査は炭素含有量の管理、非破壊検査はヒビなどの内部破壊の有無の確認を目的に行います。
まとめ
金属射出成形の概要やほかの成形技術との違い、メリットやデメリット、手順を解説しました。
金属射出成形は高精度な金属製品を大量生産したいときに適した成形方法です。
一方で、材料の生成や管理などには高い技術が求められ、金型の作成には期間やコストも発生します。
金属射出成形で納得のいく製品づくりを実現するには、実績のある加工業者を選び、依頼することが重要です。
射出成形を活用した部品製造を検討している方は、ぜひ「Taiga(タイガ)」をご活用ください。Taigaは、無料で経験豊富な業者に相談できるサービスです。
難易度の高い部品や新規部品の開発、少量生産、試作から量産まで、コストを抑えつつ効率的に進めることが可能です。
Taigaで技術提案を受ける