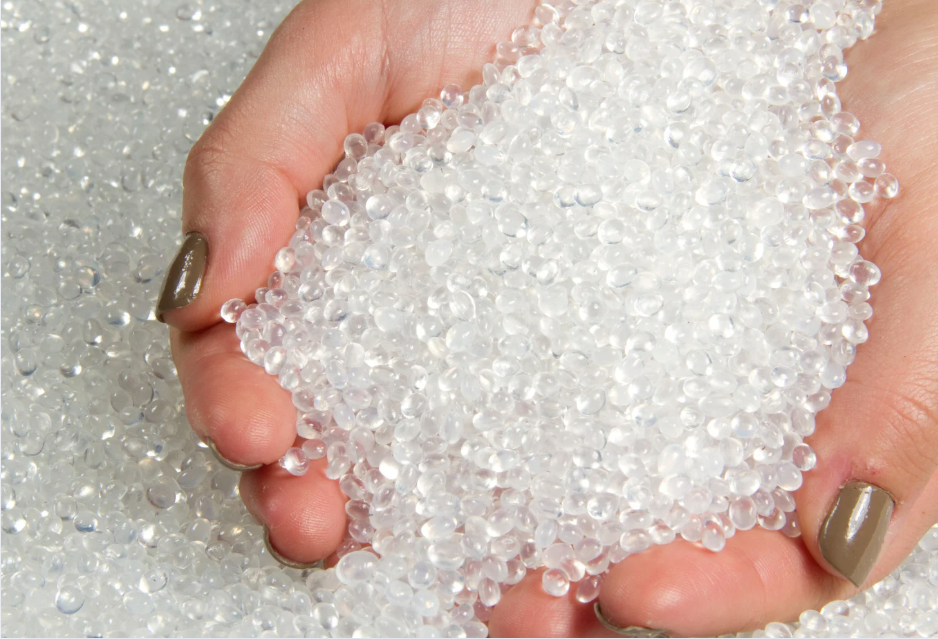
PEEKとは、高性能なスーパーエンジニアプラスチックのひとつです。
PEEKを素材としての製品製造を検討しているとき「PEEKは切削加工に向いている?」「切削加工と射出成形どちらの方が向いている?」といった疑問を持つ方もいるかもしれません。
今回の記事では、PEEKの切削加工の概要やメリット、デメリットについて解説します。
PEEKの切削加工時のポイントや、注意点についても解説していますので、ぜひ参考にしてください。
Taigaで技術提案を受ける目次
PEEKとは?切削加工に適した高機能樹脂
PEEK(Poly Ether Ether Ketone)とは、ポリエーテルエーテルケトン樹脂という高性能なスーパーエンジニアリングプラスチックです。
最高260℃の耐熱性をはじめ、摩擦や熱、放射線に対して優れた耐性を誇ります。
硬度や機械特性、難燃性や寸法安定性、絶縁性にも優れているほか、耐薬品性はエンジニアリングプラスチックでもっとも高いです。
特性を活かして、溶剤や腐食性のガスが使用される環境下や、自動車や航空機の部品など高温に達する環境下の部品の部材として多く用いられています。
PEEKのグレードによる違い
PEEKはグレードにより性質が異なります。
グレードによる違いは、以下の通りです。
グレード | 特徴 | 主なPEEKの種類 |
標準グレード(ナチュラルグレード) | 基本性能が高い加工精度に優れる | PEEK 90GPEEK 151GPEEK 381GPEEK 450GPEEK-HT G22 |
ガラス繊維強化グレード | ガラス繊維を強化他のグレードより強度と剛性に優れている | PEEK 90GL30PEEK 150GL30PEEK 450GL30 |
炭素繊維強化グレード | 炭素繊維を強化他のグレードより強度と剛性に優れている | PEEK 90CA30PEEK 150CA30PEEK 450CA30 |
高摺動性グレード | 炭素・PTEF配合すべらせながら動かしやすいように強化 | PEEK 150FC30PEEK 450FC30 |
PEEK切削加工のメリット
PEEKはエンジニアプラスチックの中では難削材に当たるものの、金属と比較すると切削加工がしやすい素材です。
PEEKの切削加工で得られるさまざまなメリットを解説します。
高精度・高品質な仕上げが可能
切削加工は、機械で対応できる範囲なら素材に厚みの制限がないため、寸法、面粗度ともに高い精度での加工が可能です。
そのため、PEEKを使った半導体装置や医療機器、電子部品といったミクロンレベルでの精密さが要求される分野の加工にも向いています。
納期が早く、低コスト生産が可能
切削加工は、鋳造や鍛造加工などで必要となる金型の製作が不要です。
金型製作で発生する時間やコストは必要なく、3D-CADデータがあればすぐに製作ができます。
特に、PEEKを用いた製品の少量生産や試作品の製造においては、早い納期と低コストでの生産が可能です。
加工の自由度が高い
切削加工は、材料の厚みの制限がないことに加えて、「5軸加工機」や「多軸(複合機)」といったさまざまな加工機があるため、加工の自由度が高いのも特徴です。
上面に加えて前後、左右からの加工が可能となるため、より複雑な形状にPEEKを加工することができます。
PEEK切削加工のデメリット
PEEKの切削加工にはメリットがある一方で、デメリットもあります。
覚えておきたいPEEKの切削加工のデメリットを解説します。
大量生産をする際はコストが高くなる
切削加工は、大量生産をする際にコストが高くなるのがデメリットです。
切削加工は材料を削り取りながら加工をするため、材料の無駄となる切りくずが発生します。
切りくずは再利用が難しいこともあり、材料自体が高価な場合はコストが高くなりやすいです。
また、切削量が多ければ多いほど加工に時間がかかるため、複雑な形状や高い精度が必要な場合はさらに生産効率が落ちてしまいます。
金型製作で発生する時間やコストは不要なものの、大量生産の場合には金型を使った加工方法の方がコスト面で有利となることも多いことを覚えておきましょう。
出来栄えが加工技術者の技量に左右されやすい
PEEKの切削加工では、工具の選定知識や高精度な製品を作る加工技術など、さまざまなスキルが必要です。
製品の形状が複雑になるほど加工の手順も複雑になります。
同じ切削加工でも、作業者の技術力が出来栄えに影響しやすいことを覚えておきましょう。
同じものを作り続けるのが難しい
切削加工を続けて行っていると、使用している刃物に摩耗が発生し、寸法や面粗度などに影響が出てきます。
PEEKを用いた切削加工で同じものを作るには、加工部品ごとに管理が必要となる点に注意しましょう。
PEEKにおける切削加工と射出成形の違い
PEEKは熱可塑性樹脂のため、切削加工のほか射出成形も選択肢となります。
PEEKにおける切削加工と射出成形の違いやメリット、デメリットを以下で比較しました。
加工方法 | 特徴 | メリット | デメリット |
切削加工 | 旋盤やフライス盤、マシニングセンタなどの工作機械を使う工作物を切断、削る、穴を開けるといった加工を行う | PEEKは精密加工も可能 | 大量生産には不向き |
射出成形 | 柔らかい素材を金型に押し出し、冷却固化させて製品を形作る加工方法溶けやすいペレット(粒)状の樹脂を材料として使用する | 量産に向いている | 表面精度は切削加工に劣る複雑な形状を作るのは難しい |
PEEK切削加工時のポイント
PEEKの切削加工時に注意すべきポイントを解説します。
切削条件の調整にノウハウが必要
PEEKは硬度が高いため、切削加工時に適切な切削条件を設定しなければ、切削工具が摩耗したり、欠けてしまったりすることがあります。
刃物の選定を間違えた場合は、刃物自体が折れてしまうこともあるでしょう。
切削条件や切り込み方法の調整にはノウハウが必要なため、十分な知識や技術のある業者へ加工を依頼することが重要です。
歪み対策で事前の熱処理が必要なケースもある
切削加工を行うものの形状によっては、切削加工時に発生する熱で歪みが起きてしまう可能性があります。
薄肉部分などの歪みやすい形状を切削加工する場合には、あらかじめ熱処理を行った上での加工が必要です。
適切な切削工具を選ぶ必要がある
PEEKは非常に硬い素材のため、切削工具で使用する工具の摩耗は激しく、工具の寿命が短くなりやすい特徴があります。
超硬刃物や高硬度を持つコーティングを施した工具など、安定してPEEKを切削加工できる工具を選ぶことが重要です。
PEEKの切削加工が用いられるシーン
PEEKの切削加工が用いられるシーンや具体的な製品について、以下の一覧にまとめました。
分野 | 具体的な加工例 |
医療産業 | 骨の固定器具ヒーリングキャップ仮の支台歯歯科インプラントの治癒期に使用する歯肉フォーマー歯科領域のカテーテルインプラント治療器具 など |
航空宇宙産業 | 航空機のブレーキシステム |
食品産業 | ピッキング工程や包装工程に使用されるロボットアーム |
まとめ
PEEKの切削加工の概要や切削加工のメリットやデメリット、射出成形との違い、切削加工時の注意点などを解説しました。
PEEKはエンジニアリングプラスチックのなかでは切削加工がしやすいため、複雑な形状や一点ものの製品を早く製作したいときには、切削加工が向いています。
ただし、切削加工は技術者の技術によって出来栄えが左右され、切削条件の調整や適切な工具の選定などのノウハウが必要です。
PEEKの切削加工を検討するときには、技術力や実績の高い業者への依頼を検討しましょう。
高精度な樹脂部品の製造を検討している方は、ぜひ「Taiga(タイガ)」をご活用ください。Taigaは、無料で経験豊富な業者に相談できるサービスです。
難易度の高い部品や新規部品の開発、少量生産、試作から量産まで、コストを抑えつつ効率的に進めることが可能です。
Taigaで技術提案を受ける