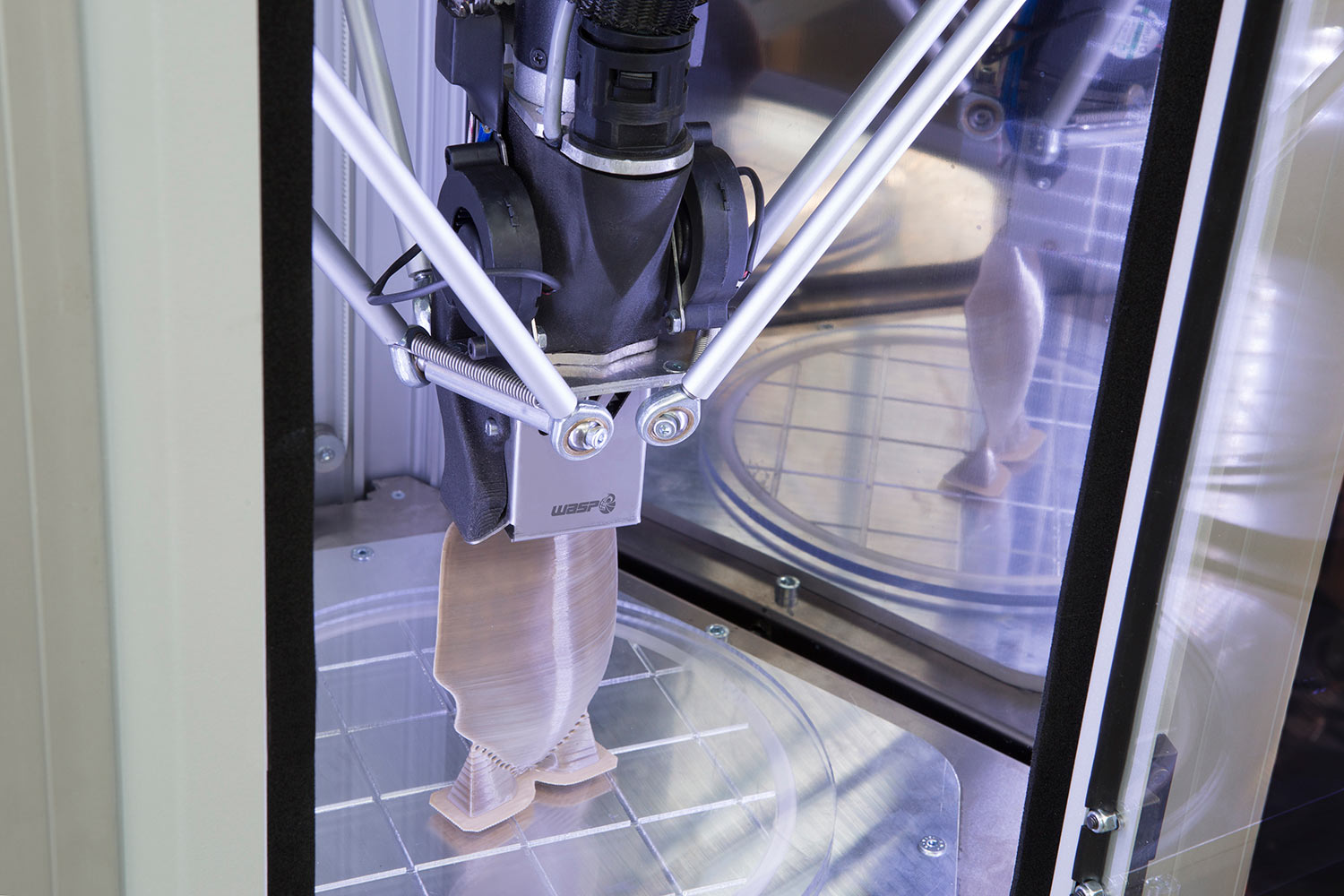
医療機器の開発において、PEEK(ポリエーテルエーテルケトン)は高い機械的強度と生体適合性を持つ素材として注目されています。
本記事では、PEEKを用いた医療機器の試作における加工方法や制作の流れ、さらには業者選定のポイントまでを詳しく解説します。
医療機器メーカーの開発・設計担当者や、インプラント・手術用器具の試作を進める技術者にとって、有益な情報をお届けするので、ぜひ参考にしてください。
Taigaで技術提案を受ける目次
医療機器開発でPEEKが選ばれる理由
医療機器分野でPEEK(ポリエーテルエーテルケトン)が多くの場面で採用されている理由は、PEEKが持つ優れた特性にあります。
PEEKが持つ主な特性は、以下の通りです。
- 耐熱性:連続使用温度は260℃程度、融点は334℃と非常に高い
- 機械的強度:高温環境下でも引張強度や耐衝撃性に優れる
- 難燃性:燃焼時の発煙や有毒ガスの発生が極めて少ない
- 耐薬品性:多くの酸、アルカリ、有機溶剤に対して優れた耐性
- 耐加水分解性:高温水蒸気下でも腐食などの影響を受けにくい
- 電気絶縁性:安定した電気特性
- 生体適合性:体内で無毒かつ不活性
- X線透過性:インプラントの位置確認が容易
- 食品安全性:日本の食品衛生法や米国FDAなどの規格を満たす
- 軽量性:金属より軽量で扱いやすい
こうした特性が医療機器製造に適しており、骨固定器具やインプラントなど、幅広い用途で採用されているのです。
また、PEEKには以下の種類があります。
種類 | 特徴 |
標準グレード | 「PEEK」と呼ばれる基本的なグレードです。耐熱性、機械的強度、耐薬品性のバランスが優れており、250°C程度の連続使用温度に耐えます。加工性が良く、高精度な切削加工が可能です。 |
摺動グレード | 基本グレードに炭素繊維、黒鉛、四フッ化エチレン(PTFE)を約10%添加し、摺動性と耐摩耗性を向上させています。高温環境での無潤滑摺動にも対応し、摩擦係数が低く、耐摩耗性に優れています。 |
強化グレード | ガラス繊維や炭素繊維を添加して機械的強度を向上させたグレードです。基本グレードと比べて強度や剛性・弾性が大幅に向上しており、熱変形温度が非常に高い。繊維の添加により切削加工性は低下します。 |
導電グレード | 炭素繊維を添加して導電性を付与したグレードで、静電気やほこりを嫌う環境で使用されます。機械的強度や耐摩耗性も向上しますが、切削加工性は低下します。 |
帯電防止グレード | 表面抵抗率が10^6〜10^9Ωの帯電防止性を持つグレードです。静電気の発生を抑制する必要がある用途に適しています。 |
医療グレード | 生体適合性を特に強化したグレードです。耐薬品性や耐放射線性に優れ、高温加圧蒸気滅菌が可能で、インプラントや医療機器に使用されます。 |
用途に応じて適切なグレードを使用することで、それぞれの特性を活かした最適なパフォーマンスが期待できます。
医療機器の試作で用いられるPEEKの加工方法
医療機器向けPEEK製品の試作には、さまざまな加工方法が存在します。
それぞれに特徴があるため、用途や目的に応じて最適な方法を選択することが重要です。
切削加工
切削加工は、医療機器向けPEEK製品において最も一般的かつ効果的な加工方法です。
旋盤やマシニングセンタなどの工作機械を用いて、プレート状の素材に切断・削り・穴開けなどの加工を施し、製品や部品を形成します。
切削加工の強みは、±0.01〜0.05mmの高精度な加工ができる点です。
例えば、複雑な形状のインプラント部品や、微細な溝を持つ医療用コネクタなど、射出成形では困難な細部まで再現できます。
少量生産やプロトタイプ制作に向いていますが、大量生産時には専用工具の消耗や加工時間が長くなるなど、コスト面で課題が生じる点に注意が必要です。
射出成形
射出成形は、ペレット状のPEEK樹脂を高温で溶融し、金型に注入して冷却固化させることで、製品を形成する加工方法です。
高い再現性と効率的な生産が可能で、均一な品質と短時間での大量生産が求められる場合に向いています。
一方で、初期投資として金型製作費用が必要となるため、小ロット生産には不向きです。
また、表面精度が切削加工に劣り、複雑形状の成形が難しいという課題もあります。
押出成形
押出成形は、長尺物や中空構造物の製造に適した加工方法です。
溶融したPEEKをダイ(口金)から連続的に押し出すことで、一定の断面形状を持つ製品を形成します。
機械的強度、耐薬品性、耐摩耗性に優れたPEEK樹脂の特性を活かし、小口径から大口径、薄肉から厚肉までのさまざまなパイプやロッドの製造が可能です。
特に、チューブ状部品やワイヤー被覆材の生産に適しています。
デメリットとしては、押出成形では複雑な形状には対応しづらい面が挙げられます。
3Dプリント
3Dプリントは近年注目されている造形技術であり、カスタマイズ性と柔軟性が高い点が特徴です。
特に、医療分野では患者ごとに異なる形状やサイズのインプラントを制作する際に活用されています。
また、多孔質構造や中空構造など、従来の加工技術では実現困難だったデザインも可能です。
ただし、大量生産時の生産速度やコスト効率面では、他の加工方法と比較してまだ改善の余地があります。
PEEKを用いて医療機器の試作品を作る流れ
医療機器向けPEEK製品の試作は、一般的に以下のような流れで進行します。
- 問い合わせ
- 打ち合わせ・見積もり
- 設計
- 加工方法の選定
- 試作
- 検査
- 納品
まず、業者を選定し、製品の要件や予算などを打ち合わせ、見積もり確認後に正式に依頼します。
その後、製品仕様や加工方法が決まると、試作品の製作を開始します。
試作品完成後は、性能評価や改良点の洗い出しを繰り返し、設計の最適化を行います。
その後は、本格的な量産体制への移行準備のため、評価と改良のサイクルを繰り返し、製品の完成度を高めることが必要です。
医療機器は、安全性や機能性が厳しく求められるため、試作段階でも滅菌処理や生体適合性試験など、医療機器特有の工程が含まれる場合があります。
PEEKを用いた医療関連の試作品例
PEEKは多くの医療分野で活躍しており、その用途は多岐にわたっています。

PEEKを用いた代表的な医療機器は、以下の通りです。
- 骨の固定器具
- 仮の支台歯
- インプラント治療器具
- カテーテルシャフト
- 試薬ラインチューブ
- 脊椎ロッド
- 外傷治療用プレート
PEEKは、脊椎ロッドやインプラント治療器具など、高強度かつX線透過性が求められる部品に使用されています。
軽量でありながら安全性が確保されているため、さまざまな医療機器への応用が可能です。
PEEKを用いた医療機器の試作を依頼する業者の選び方
医療機器向けPEEK製品を依頼する際には、以下のポイントを確認することが重要です。
医療機器分野の実績確認
PEEKの加工や試作を依頼する業者を選ぶ際は、業者が過去にどれだけ医療分野で実績を積んできたかを確認する必要があります。
特に、インプラントや手術用器具などの高精度かつ安全性が求められる分野で成功事例を持つ業者は信頼性が高いといえるでしょう。
品質管理体制が整っているか
医療分野では厳格な品質管理体制が求められます。
ISO13485規格への準拠や滅菌対応力など、業者が提供する品質管理体制について十分確認しましょう。
まとめ
PEEKは医療機器産業において重要な素材として注目されています。
その優れた耐熱性、生体適合性、X線透過性により、インプラントから手術器具まで幅広い利用が可能です。
PEEKを用いた医療機器の試作・加工を検討中の場合は、高い技術力と適切な品質管理を行える業者を選びましょう。
PEEK部品の製造を検討している方は、ぜひ「Taiga(タイガ)」をご活用ください。Taigaは、無料で経験豊富な業者に相談できるサービスです。
難易度の高い部品や新規部品の開発、少量生産、試作から量産まで、コストを抑えつつ効率的に進めることが可能です。
Taigaで技術提案を受ける