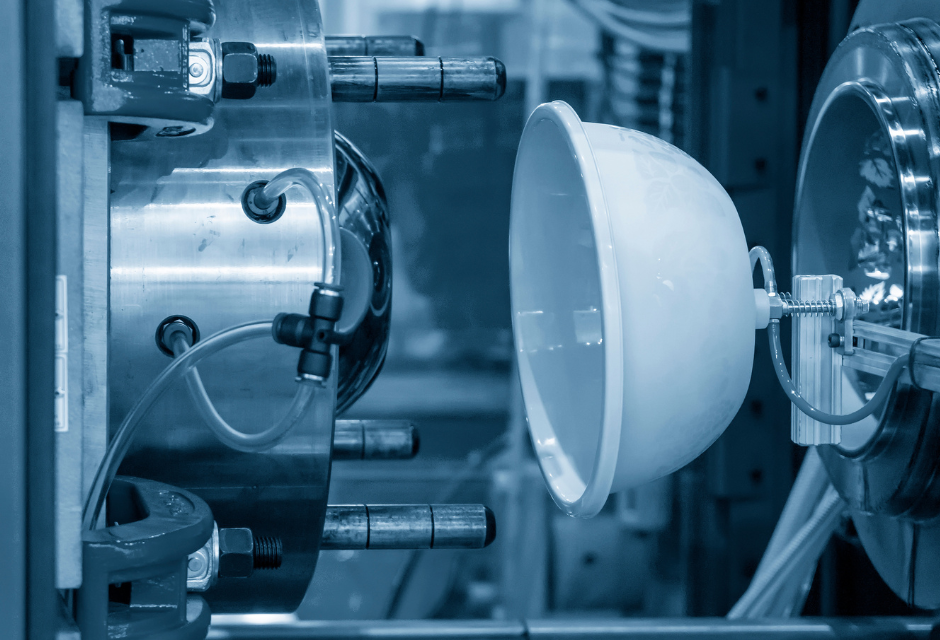
射出成形は、樹脂の加工で多く用いられる成形方法です。
とはいえ、一口に樹脂の射出成形といっても多くの成形方法があり、使用される樹脂さまざまです。
成形する製品やシーンに合わせた成形方法や樹脂を選ぶために、メリットやデメリットを踏まえておくようにしましょう。
今回の記事では、樹脂の射出成形の概要やメリット・デメリット、射出成形で使われる樹脂の種類を解説します。
Taigaで技術提案を受ける目次
樹脂の射出成形とは
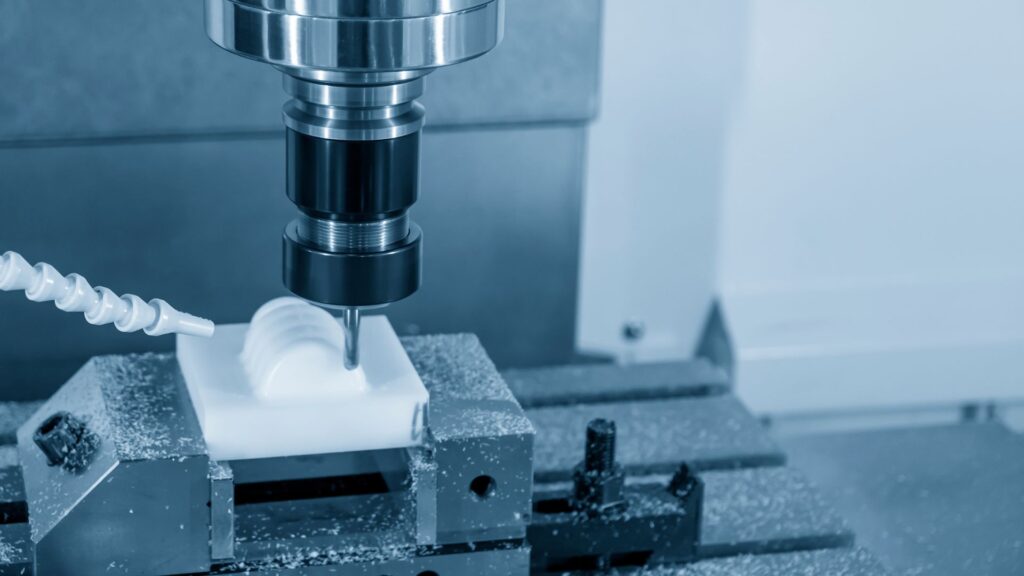
樹脂の射出成形とは、加熱して溶融したプラスチック樹脂を金型に射出し、冷やして固めることで成形品を作る方法です。インサート成形またはインジェクション成形とも呼ばれています。
樹脂の射出成形には、以下の種類があります。
射出成形の種類 | 特徴 |
多材質射出成形 | 多色成形、複数材質など2回射出する成形方法 |
インモールド成形 | 印刷してあるフィルムをキャビティに挿入し、射出工程に移る方法 |
ホットアンドクール成形 | キャビティ面の完全転写を目的とした高温度金型にて、射出・保圧後に、すぐに冷却して離型する方法 |
射出圧縮成形 | CDや導光板などのキャビティ面への転写を目的とした成形方法 |
発泡成形 | やけ防止対策などで窒素ガスや化学発泡剤を使用する成形方法 |
サンドイッチ射出成形 | コア層とスキン層を別の成形機で射出する成形方法 |
ガスアシスト射出成形 | ヒケ、変形対策として圧力の不均一を解消した成形方法 |
金型内組立法 | 大スライドで組み立て位置に接合部を合わせてから二次成形する方法 |
中空品の射出成形 | 接合部を射出成形する型内組立成形方法 |
樹脂の射出成形は、以下のような部品・製品の製造シーンで用いられています。
- 自動車関連(外装品、エンジンルーム、運転席)
- 大型・小型家電
- 事務機器
- 情報・通信機器
- 光学機器・レンズ
- 住宅・建築
- 容器・包装
- スポーツ・レジャー
- 文房具・玩具
- 医療
- 航空機
- 舟艇・船舶
射出成形のメリット
樹脂の射出成形には、以下のメリットがあります。
- 金型を製作すればある程度の複雑な形状や微細な製品を製造可能
- 用途や形状に応じた幅広い種類のプラスチック樹脂材料が使用可能
- 一般的に不良発生率がほかの工法と比較して少ない
- ロット生産から大量生産まで対応できる
- 大量生産のコスト効率が良い
- 射出成形機が対応していれば小型から大型製品まで対応できる
- 穴あけやバリ取りといった成形品の後加工が少ないまたは不要
- 自動化がしやすく、人件費削減や生産性向上につながる
さまざまな樹脂を用いて複雑な形状を作れるほか、大量生産にも向いているため、多くのシーンで用いられる成形方法です。
射出成形のデメリット
樹脂の射出成形のデメリットは、以下の通りです。
- 金型の製作費用が高額
- 設計に制約がある
- 製品以外の部分も成形されるため材料の無駄が生じる
- バリ、ヒケ、ウェルドラインなどの成形不良が発生することがある
- 大型製品は大型の射出成形機と金型製作コストが高くなる
射出成形には金型を用いるため、金型製作費用がかかる分少量生産には向きません。
また、成形品を型から外す必要がある分、設計に制約がある点にも注意が必要です。
射出成形で使われる樹脂の種類
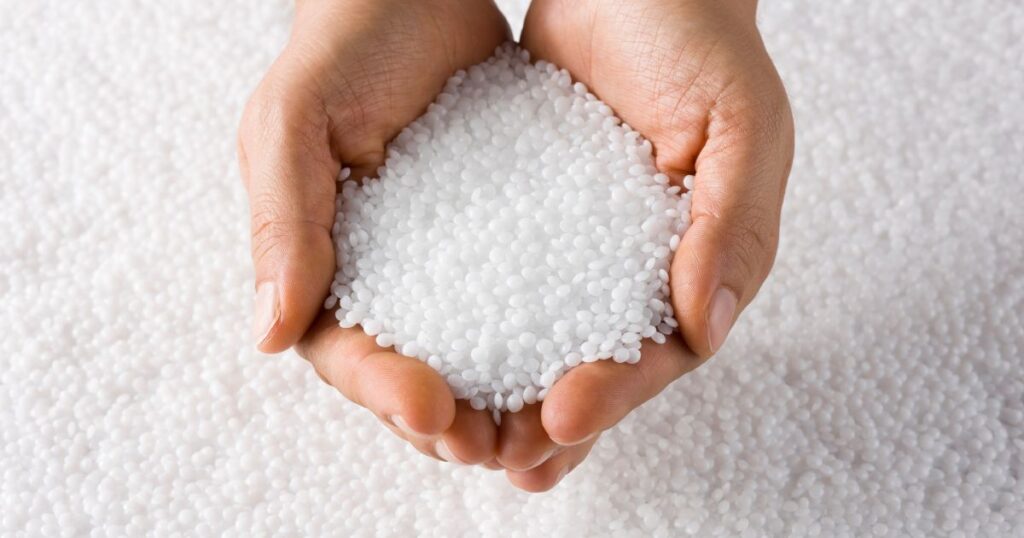
射出成形で使われている主な樹脂の種類と特徴を解説します。
熱硬化性樹脂
熱硬化性樹脂とは、加熱すると硬化する樹脂です。
線状の3次元構造の高分子を持っており、加熱すると軟化したあとに化学反応により硬化します。
一度加熱して硬化したものは、再加熱しても溶けません。
そのため、耐熱性を要求される部品や箇所に使用されます。
熱可塑性樹脂
熱可塑性樹脂とは、熱を加えると柔らかくなる樹脂です。
線状の高分子を持ち、加熱すると軟化し、冷却すると固化します。
また、加熱すると再度軟化するため、繰り返し使用することが可能です。
主にバケツ、コップ、密封容器などの家庭用品をはじめ、さまざまな製品に採用されています。
なお、熱可塑性樹脂は、さらに汎用プラスチック、エンジニアリングプラスチック、スーパーエンジニアリングプラスチックの3種類に分類できます。
それぞれの特徴について、以下で詳しく見ていきましょう。
汎用プラスチック
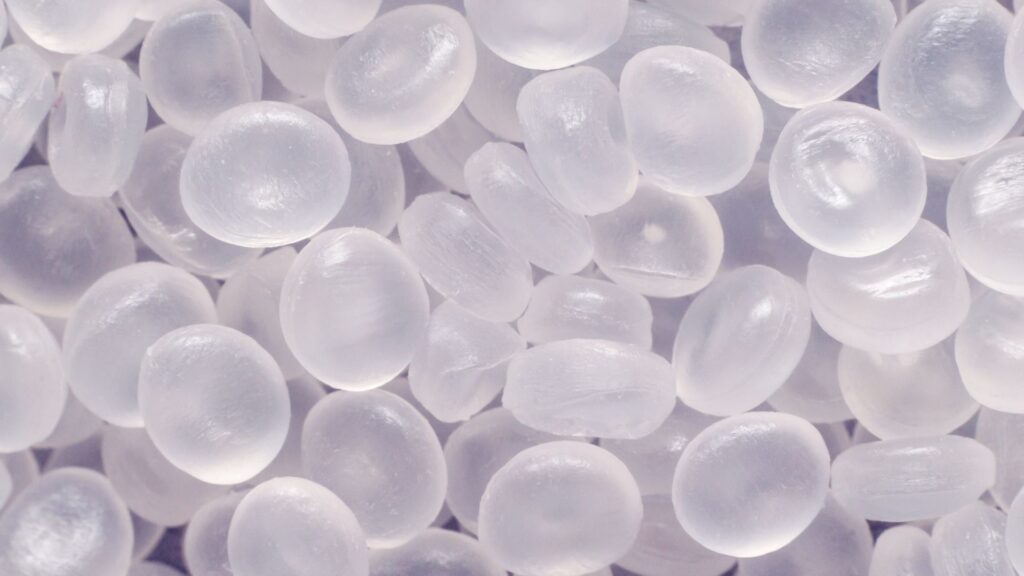
汎用プラスチックは、以下の特性を持つ熱可塑性樹脂のことです。
- 熱変形温度100°C未満
- 引っ張り強さ500kgf/cm²未満
- 耐衝撃5kgf.cm/cm未満
加工がしやすいうえ価格が安価のため、大量生産に向いています。
汎用プラスチックは、プラスチック生産量の約80%を占め、日用品や工業製品、家庭用品など幅広い製品の材料に採用されてます。
一方、耐熱性や機械的強度などの性能はあまり高くありません。
代表的な汎用プラスチックには、以下のものがあります。
- ポリエチレン(PE)
- ポリスチレン(PS)
- アクリロニトリルスチレン樹脂(ASまたはSAN)
- アクリロニトリルブタジエンスチレン樹脂(ABS)
- ポリプロピレン(PP)
- ポリ塩化ビニル樹脂(PVC)
- メタクリル樹脂(PMMA)
- ポリエチレンテレフタレート(PET)
エンジニアリングプラスチック
エンジニアリングプラスチック(エンプラ)とは、以下の特性を持つ熱可塑性樹脂のことです。
- 熱変形温度100°C以上
- 引っ張り強さ500kgf/cm²以上
- 耐衝撃5kgf.cm/cm以上
汎用プラスチックよりも機械的強度や耐熱性にすぐれているのが特徴です。
代表的なエンジニアリングプラスチックには、以下のものがあります。
- ポリアミド(PA)
- ポリカルボナート(PC)
- ポリアセタール(POM)
- 変性ポリフェニレンエーテル(m-PPE)
- ポリプチレンテレフタレート(PBT)
- GF強化ポリエチレンテレフタレート(GE-PET)
- 超高分子量ポリエチレン(UHPE)
スーパーエンジニアリングプラスチック
スーパーエンジニアリングプラスチックとは、長時間の耐熱性が150℃以上の熱可塑性樹脂です。
特に耐熱性、高温時の機械的強度では、エンプラを上回ります。
代表的なスーパーエンジニアリングプラスチックは、以下の通りです。
- ポリフェニレンスルフィド(PPS)
- ポリアリレート(PAR)
- ポリサルホン(PSU)
- ポリエーテルサルホン(PES)
- ポリエーテルエーテルケトン(PEEK)
- ポリエーテルイミド(PEI)
- ポリアミドイミド(PAI)
- 液晶ポリマー(LCP)
- ポリイミド(PI)
- ポリアリレート(PAR)
- ポリスルホン(PSF)
- ポリテトラフルオロエチレン(PTFE)
その他のプラスチック樹脂
その他のプラスチックには、以下のようなものがあります。
- フッ素樹脂
- 熱可塑性エラストマー
- ポリメチルペンテン(PMP)
- 生分解性プラスチック(バイオプラスチック)
- 繊維素系プラスチック
樹脂の射出成形の流れ
樹脂の射出成形は、以下の流れで行います。
- 素材となる樹脂(ペレット)を投入し、溶かす
- 金型に溶けた樹脂を流し込む
- 高い圧力をかける
- 金属内部を冷やし、樹脂が固まるのを待つ
- 十分に固まったら金型を外し、製品を取り出す
なお、射出成形の具体的な流れについては「」でも解説しているので、あわせて参考にしてください。
【射出成形以外】プラスチック成形法の種類
プラスチック樹脂の射出成形以外の成形方法を以下にまとめました。
成形方法 | 特徴 |
押出し成形法 | 長尺成形品の成形加工 |
ブロー成形法 | 中空製品を押し出し、膨らませる成形方法ボトル製品の基本的成形方法 |
真空成形法 | シート材の熱加工成形 |
フィルム成形法 | 熱ロールと冷却ロールを使用し、シートやフィルムを成形 |
樹脂の特性や成形物によって、適切な成形方法は異なるため、加工業者と相談しながら最適な方法を選ぶようにしましょう。
まとめ
樹脂の射出成形の種類やメリット、デメリット、手順を解説しました。
射出成形は樹脂の成形加工ではもっとも一般的な手法ですが、多くの加工方法があり製品に応じた素材選びも求められます。
樹脂の射出成形を検討しているなら、作りたい製品に応じた樹脂素材を選び、高い技術をもって成形を行える加工業者を選ぶことが重要です。
樹脂の射出成形を活用した部品製造を検討している方は、ぜひ「Taiga(タイガ)」をご活用ください。Taigaは、無料で経験豊富な業者に相談できるサービスです。
難易度の高い部品や新規部品の開発、少量生産、試作から量産まで、コストを抑えつつ効率的に進めることが可能です。
Taigaで技術提案を受ける