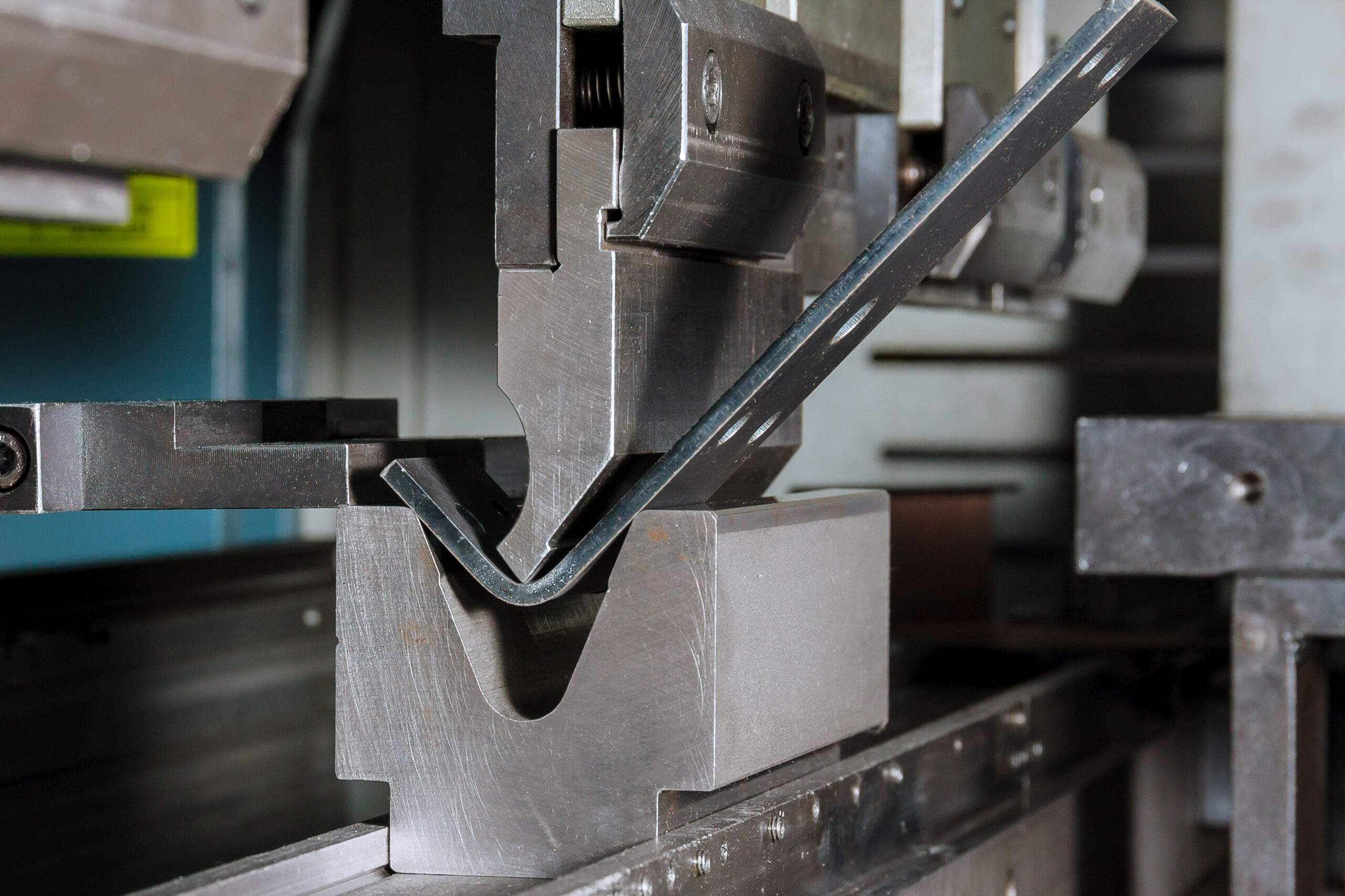
板金加工は、金属の代表的な加工方法です。
板金を使っての製品製造を検討しているとき「溶接加工はどんなシーンに使われる?」「板金加工には種類がある?」といった疑問を持つ方も多いかもしれません。
今回の記事では、板金の溶接加工の概要やメリット、デメリットに加えて、板金溶接加工の種類ごとの特徴を解説します。
板金溶接加工を依頼できる業者の選び方についても紹介しますので、ぜひ参考にしてください。
Taigaで技術提案を受ける目次
板金の溶接加工とは?
板金の溶接加工とは、2枚以上の板金を溶かして接合する方法です。
接着剤やネジなどでの接合方法とは異なり、板金を溶かすことで一体化するため、強度の高い接合を実現できます。
なお、板金の溶かし方には、加熱や圧力などさまざまな方法があります。
板金溶接加工のメリット
板金溶接加工には、以下のようなメリットがあります。
- 気密性が高い
- コストダウンにつながる
- 作業に柔軟性がある
板金溶接では板金を溶かして接合するため、接合面の気密性が高いメリットがあります。
そのため、船舶や航空機材などの接合の気密性が求められるものの接合にも向いています。
接着剤やネジなどの材料を使わずに接合でき、複雑な形状でもほかの加工方法と比較するとコストを抑えながら製作が可能です。
溶接方法によっては特別な機器や設備が不要なケースもあり、屋内・屋外と作業場所も選びません。
状況に応じた作業環境を柔軟に選べるのも、板金溶接加工のメリットです。
板金溶接加工のデメリット
板金溶接にはメリットが多いものの、以下のようなデメリットもあります。
- ひずみや残留応力が発生することがある
- 接合した部分は分解できない
- 作業者の技量によって出来栄えが左右される
板金溶接では、接合するために板金の一部を加熱や圧迫するため、不均一な膨張や収縮が発生し、ひずみや残留応力の原因となります。
そのため、手作業で溶接を行う場合、溶接の出来栄えや品質が作業者の技量によって異なるため安定性に欠ける点がデメリットです。
また、板金を溶かして接合するため、接合した部分を分解することはできません。
ネジのように取り外しができないため、接合した部分を分解したいときには、壊す必要があります。
板金溶接加工の3つの種類
板金溶接には、融接・圧接・ろう接の3種類があります。
それぞれの加工方法ごとの特徴を解説します。
融接による溶接加工
融接とは、接合する板金を加熱して溶かして溶接する方法です。
アーク溶接、レーザー溶接、ガス溶接の3種類があります。
アーク溶接
アーク溶接とは、放電によって発生する火花(アーク)の熱によって金属を溶かし、溶接する方法です。
一般的に、溶接は火花を散らしながら作業するイメージを持つ人も多くいますが、この作業がアーク溶接にあたります。
アークを発生させるのは、高い電圧をかけた母材と溶接棒、または電極の間です。
アーク溶接の中にも、マグ溶接・ミグ溶接・ティグ溶接といった種類があります。
レーザー溶接
レーザー溶接とは、レーザーを照射した熱によって金属を溶かして接合する溶接方法です。
アーク溶接やガス溶接よりも、精密な溶接ができるメリットがあります。
ただし、強力なレーザーを使用する分、作業環境を整える必要があり、屋外などでは作業ができず柔軟性に欠ける点はデメリットです。
ガス溶接
ガス溶接とは、アセチレンガスなどを燃焼させて発生した熱によって溶接する方法です。
アーク溶接のように火花が散ることもないため、いろいろな場所で作業できるメリットがあります。
ただし、ガスによって加熱される範囲が広く溶接に影響が出る点はデメリットです。
圧接による溶接加工
圧接とは、板金を重ねて圧力と電圧を同時にかけて発生する抵抗熱によって板金を溶かし、溶接する方法です。
主に自動車のボディなどの溶接方法として活用されています。
スポット溶接とシーム溶接がありますが、いずれも大がかりな溶接装置が必要です。
スポット溶接
スポット溶接とは、溶接部分に挟んだ電極の電流をホチキスのように複数に打ち込んで接合する手法です。
シーム溶接
シーム溶接とは、溶接部分をローラーの電極によって線で連続して接合する方法です。
高い機密性が期待できるため、船体や燃料タンクといった気密性を担保したい製造に向いています。
ろう接による溶接加工
ろう接とは、接合部分のみを加熱して溶接する方法です。
他の溶接技術と異なり、母材は加熱しません。
ろう付け
ろう付けとは、融点が450℃以上の金属に採用されるろう接方法です。
融点の低いはんだを使い、精密機器や電子部品の接合を行う「はんだ付け」も、ろう接に含まれます。
【板金の素材別】溶接加工の注意点
溶接では、さまざまな種類の板金の接合が可能ですが、使用する金属の性質を踏まえて溶接を行う必要があります。
覚えておきたい、板金の種類別の板金加工の注意点を解説します。
鉄
鉄の溶接では、可能な限り炭素の含有量が少ない低炭素鋼を選ぶことがおすすめです。
鉄には炭素が多く含まれているため、温度が急激に変化すると鉄内部の結晶構造が変化し、割れや粘り強さの減少の原因となります。
鉄の溶接において選択肢になるのは、SS材(一般構造用圧延鋼材)や、SM材(溶接構造用圧延鋼材)です。
なお、鉄を溶接する際の手法は、TIG溶接や被覆アーク溶接が向いています。
ステンレス
ステンレスは種類によって組成が大きく違うため、使用するステンレスの種類によって溶接時の注意点や取り扱い方も異なります。
溶接の際は、できる限りオーステナイト系に分類されるSUS304やSUS316などの溶接に向いているステンレスを使用しましょう。
また、フェライト系のSUS430やマルテンサイト系のSUS410は溶接には不向きのため、避けるのが無難です。
アルミニウム
アルミニウムは融点があまり高くない一方で、空気中の酸素と結合すると融点の高い酸素被膜を形成する性質を持っています。
そのため、酸素被膜を溶かそうとすると中のアルミが溶けすぎてしまい、母材ごと溶け落ちてしまうリスクがあります。
さらに、熱伝導性が高い分、溶接の熱が母材へ伝わりやすくゆがみやすいため、溶接にはあまり向いていません。
アルミニウムを溶接する場合、溶接部の効率的な加熱やスピーディな溶接作業の進行が必須です。
なお、アルミニウムの溶接には、TIG溶接が向いています。
板金溶接加工の主な用途や製品例
溶接は、ネジなどを使って行う機械的接合と比較すると、接合部分が広いため破損の可能性が低くなるのがメリットです。
また、金属同士を溶かして接合するため、金属原子同士が結合することから気密性と強度の高い接合も実現できます。
板金溶接加工は、このような特徴やメリットを活かして、以下のような用途や製品に活用されています。
- 気密性が求められる自動車や航空機などの構造物
- 有毒ガスの漏洩リスクを防げる配管
- 溶接による補修
特に、漏洩すると人体に危険が及ぶ有毒ガスが通る配管などには、溶接技術が欠かせません。
まとめ
板金溶接加工の特徴やメリット、溶接時の金属別の注意点や主な用途を解説しました。
溶接は板金同士の接合方法としては代表的であり、気密性の高さなどのメリットもあります。
ただし、板金の種類によっては溶接が難しいこともあり、溶接に適した板金の選定や高い技術も必要です。
板金溶接での製品製造を検討しているなら、板金溶接の実績が多くある業者へ依頼することで、納得のいく製品製造につながるでしょう。
CFRP加工を活用した部品製造を検討している方は、ぜひ「Taiga(タイガ)」をご活用ください。
Taigaは、無料で経験豊富な業者に相談できるサービスです。
難易度の高い部品や新規部品の開発、少量生産、試作から量産まで、コストを抑えつつ効率的に進めることが可能です。
Taigaで技術提案を受ける