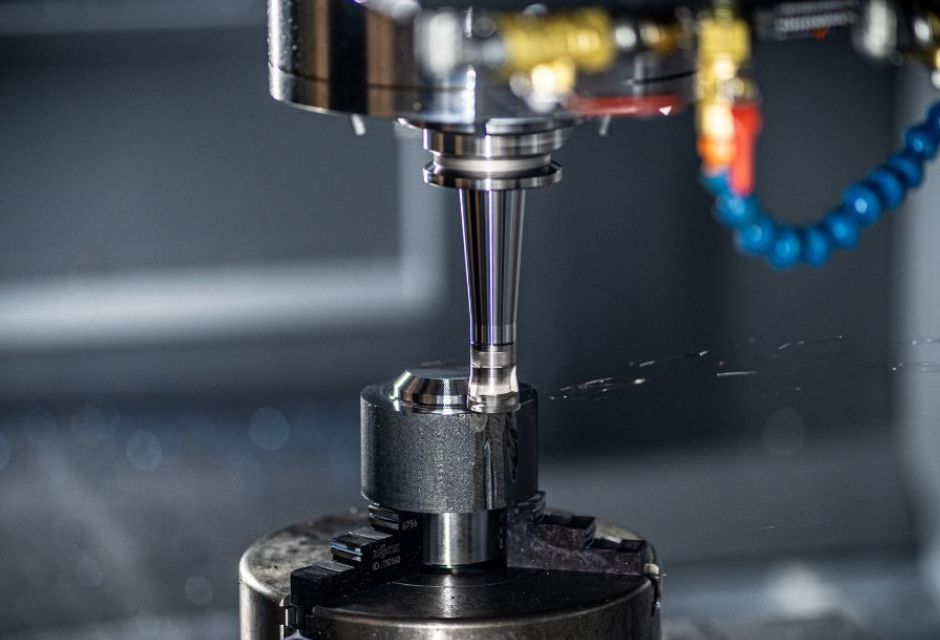
Cutting of CFRP involves issues such as machining time, shortened tool life, burrs, and delamination (delamination). These problems can affect product quality and productivity, and appropriate measures must be taken in CFRP machining.
For successful cutting of CFRP, it is important to understand the characteristics of the material and to select appropriate tools, cutting conditions, and processing methods.
By reading this article, you will gain a better understanding of CFRP cutting and learn how to efficiently manufacture high-quality products.
For more information about Taiga, click here.Table of Contents
Problems when cutting CFRP
CFRP is used in various fields due to its high strength and lightweight characteristics, but there are unique challenges in cutting.
Here are three problems when cutting CFRP.
- Processing takes time
- Decrease in tool life occurs
- Burrs, delamination, etc. occur.
Processing takes time
Because of its high strength, CFRP causes severe tool wear when cutting. Therefore,It is difficult to increase the processing speed, resulting in longer processing times.
CFRP is made by integrating carbon fibers and resin, so it also has the characteristics of resin parts melting and carbon fibers becoming wispy during processing.
Therefore, one of the problems is that processing time must be spent to maintain the quality of the finished product.
Decrease in tool life occurs
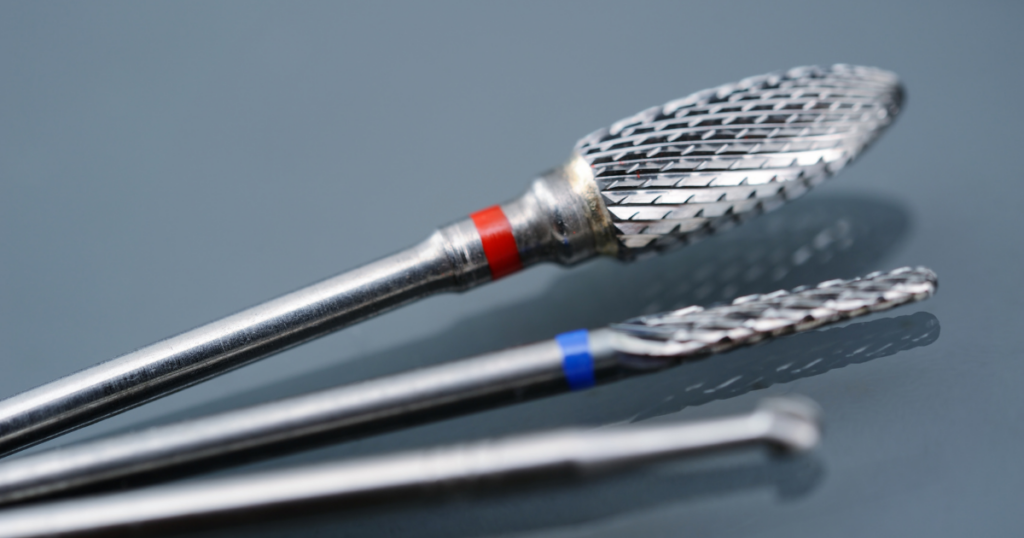
When cutting CFRP, the possibility of reduced tool life increases.
This is because the carbon fiber in CFRP is very hard and the cutting edge is worn or scraped by the tool as it rubs during cutting. In addition, the high cutting temperature during CFRP machining may cause thermal degradation of the tool.
To extend tool life, it is recommended that diamond-coated tools be used.
In fact, in our CFRP machining experiments, we have found that when diamond-coated tools are used for cutting, no degradation is observed, while for other tools, the cutting edges are frictionally damaged.
Burrs, delamination, etc. occur.
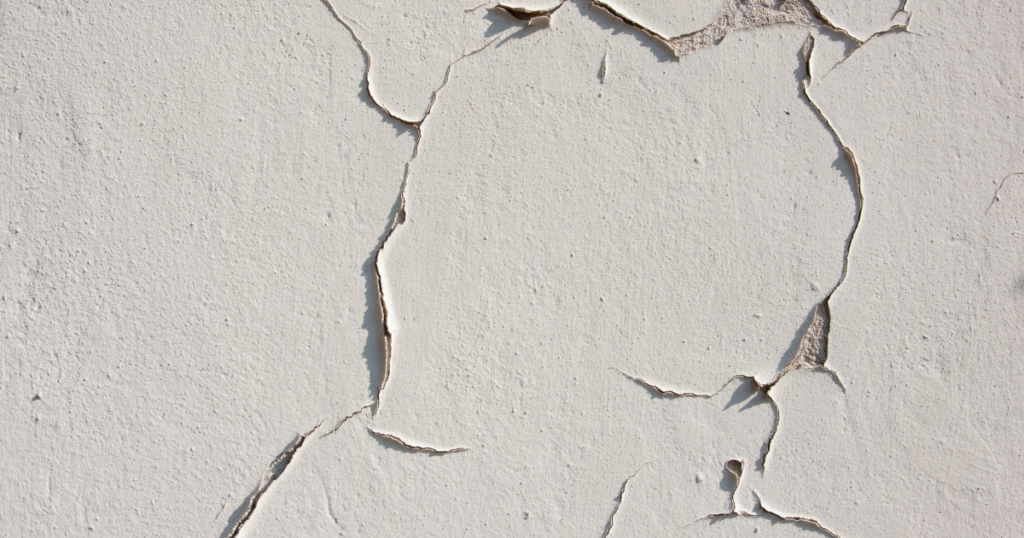
Burrs and lamination (delamination) in the cutting process of CFRP have become an issue.
The structure of CFRP is a combination of carbon fiber and resin, which causes the adhesion between the layers to weaken during cutting. When burrs and delamination (delamination between layers) occur, the strength and durability of the entire structure are reduced and the service life is shortened.
In the CFRP machining experiments, burrs were observed with DLC-coated tools, carbide lithod tools, and high-os base metal TiN-coated tools, except for diamond-coated tools.
Therefore, it may be better to use diamond-coated tools to reduce the occurrence of burrs and delaminations.
How to perform cutting of CFRP
In light of the above issues, this chapter details specific methods for successfully cutting CFRP.
- Use wear-resistant tools.
- Optimize cutting speed according to fiber direction
- Devise processing methods
- finishing workmanship
Use wear-resistant tools.
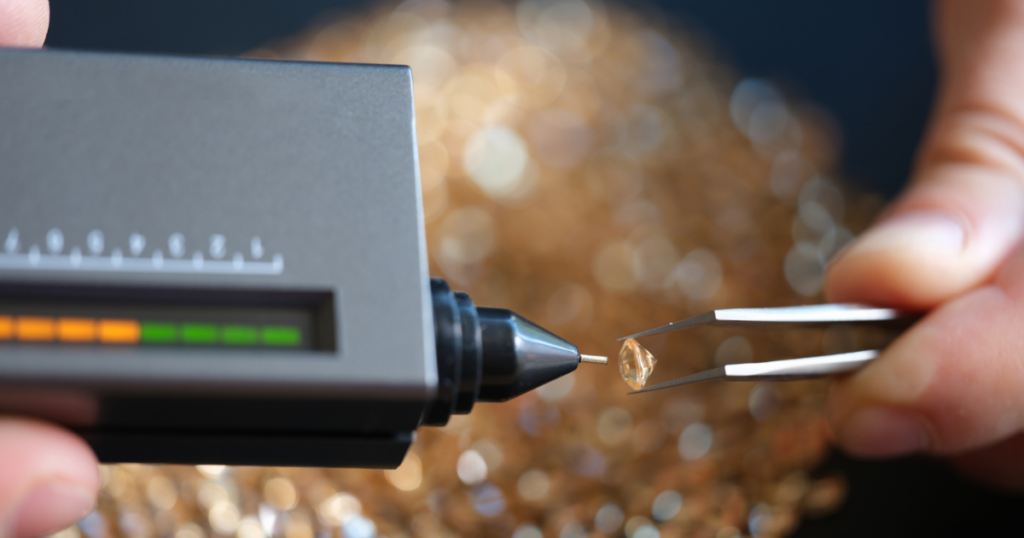
First, it is important to select tools with sharp cutting edges that resist friction.
Examples include CBN tools (cubic boron nitride), PCD tools (polycrystalline diamond), and diamond-coated tools.
These tools minimize burrs and delaminations that tend to occur during cutting operations, and provide a smooth, high-precision finish.
These tools can also withstand the high abrasiveness of carbon fiber for a longer period of time, thus extending tool life and reducing the frequency of replacement.
Optimize cutting speed according to fiber direction

For smooth cutting of CFRP, it is important to optimize the cutting speed according to the fiber direction.
This is because the structural property of CFRP, anisotropy, and the resulting differences in cutting behavior have a significant impact on machining quality and efficiency.
Yamaguchi Prefectural Industrial Technology Center "Yamaguchi Prefectural Industrial Technology CenterStudy on Grinding Hole Drilling in Carbon Fiber Reinforced Plastics
According to the report, "We found that by cutting from the start of machining to the third exit layer at high speed, and machining the two exit side layers (about 0.5 mm) at low speed, the machining time can be reduced while maintaining the machined part.
Devise processing methods
Down-cutting is the recommended processing method for CFRP.
Down-cutting is a method in which the cutting edge of the tool cuts in the same direction as the material travels, preventing burrs and delaminations.
Another reason we recommend the down-cut process is that the processed surface is stable and can be completed with a smooth finished surface.
finishing workmanship
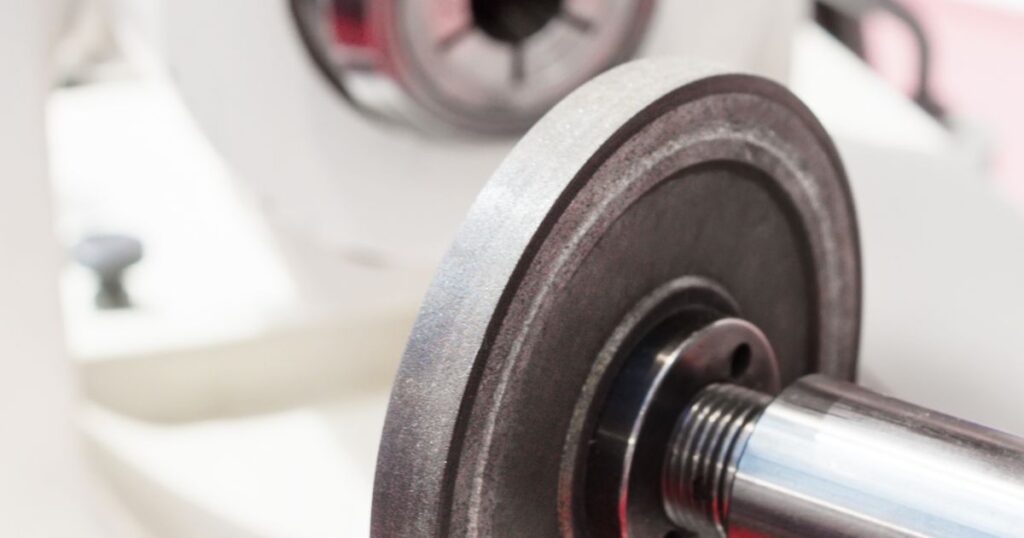
Finishing is to remove the damage layer caused by rough machining,It is important to perform the grinding process using an electrodeposited diamond wheel.
Electrodeposited diamond grinding wheels are manufactured by fixing diamond particles to a metal substrate, which increases the retention of the abrasive grains and improves the cutting ability.
Especially for difficult-to-machine materials such as CFRP, machining with electrodeposited diamond grinding wheels is the best choice because the grinding wheels are required to have low wear and long life.
Points to keep in mind when cutting CFRP
Here are three points to keep in mind when cutting CFRP.
- Measures against dust inhalation, water, cutting fluid, etc.
- CFRP dust must be disposed of as industrial waste
- Tool selection based on test machining, etc.
Measures against dust inhalation, water, cutting fluid, etc.
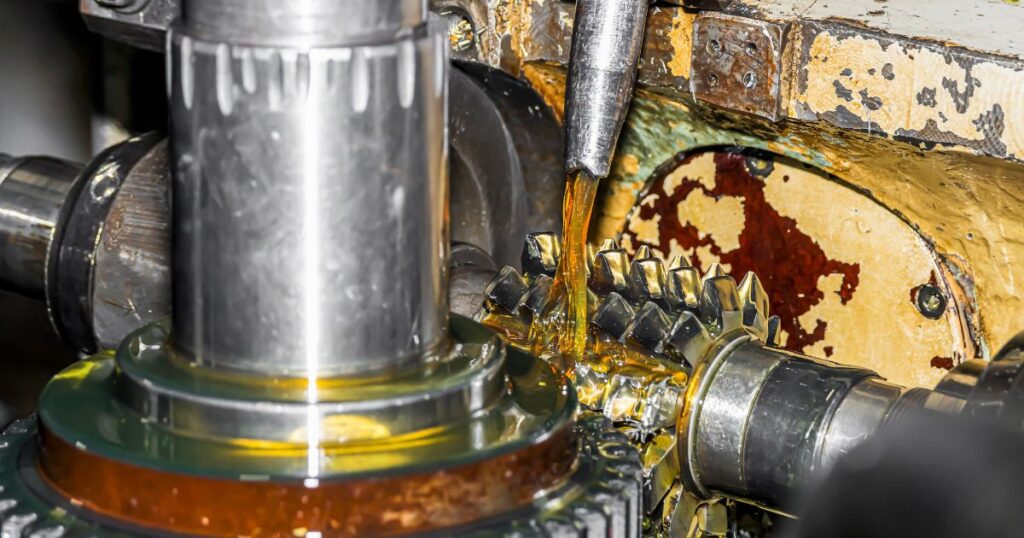
When cutting CFRP, it is necessary to take measures such as dust inhalation, water and cutting fluid.
This is because inhaling the dust generated during the cutting process of CFRP may adversely affect the respiratory system. In addition, dust can enter the interior of the machine, which can cause malfunctions.
Therefore, it is important not only to wear personal protective equipment, but also to provide an adequate supply of cooling water and cutting fluid to reduce dust dispersion.
CFRP dust must be disposed of as industrial waste
Dust generated during the cutting process of CFRP is classified as industrial waste "waste plastic.Therefore, it must be disposed of in accordance with the Industrial Waste Disposal Law.
Specifically, they are required to hand over the waste to a specialized processor as industrial waste.
Tool selection based on test machining, etc.
In cutting CFRP, it is important to select appropriate tools based on test machining.
CFRP has a wide variety of carbon fibers, resins, and processing methods, and each material has different characteristics. Therefore, the same tool is not applicable to all CFRP materials.
To improve machining accuracy and ensure quality, it is essential to select the optimal tool for the target CFRP material.
Summary
In this article, we have described the methods and problems of performing cutting operations on CFRP.
In the cutting process of CFRP, the long machining time and short tool life are issues. To solve these problems, appropriate tool selection and machining methods are important. The use of diamond-coated tools and down-cutting can prevent burrs and delamination and achieve a smooth finish.
Taiga" for manufacturing difficult components
Taiga utilizes state-of-the-art technologies such as sheet metal fabrication, CNC machining, and 3D printing to support the manufacture of complex shapes and new parts.
Flexible support for prototyping and R&D, making the most of materials and ideas. Our experienced engineers solve problems and provide comprehensive support from design to manufacturing.
If you are considering manufacturing parts utilizing the CFRP cutting process, please contact us.Taiga."Taiga is a free service that allows you to consult with experienced contractors.
We can efficiently proceed with the development of difficult or new parts, small-lot production, prototyping, and mass production while keeping costs low.
For more information about Taiga, click here.