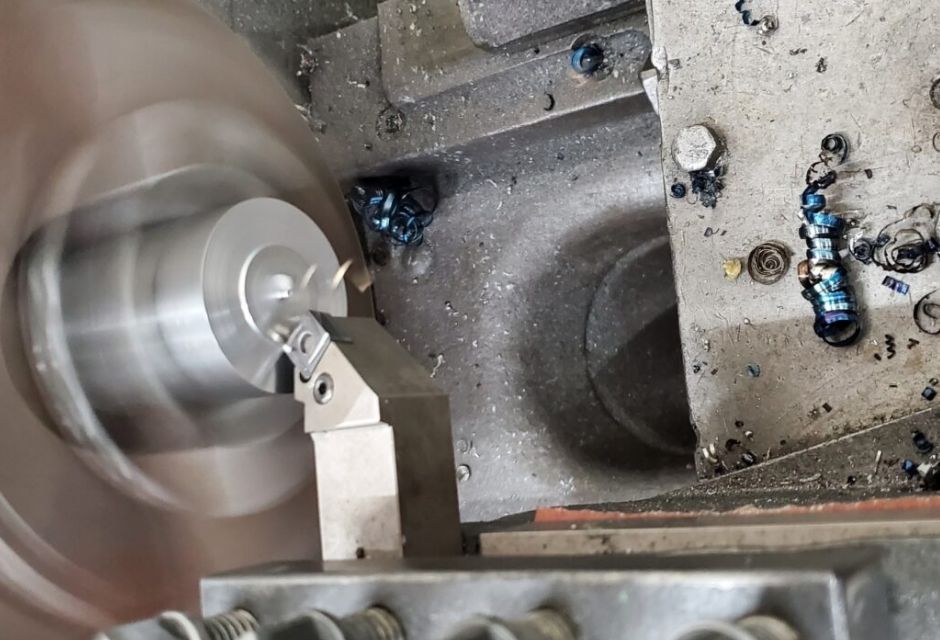
Many people are considering manufacturing products by lathe turning but have questions such as "I don't know the difference between lathe turning and other processing methods" or "I want to know the advantages and disadvantages of lathe turning.
In this article, we will explain what lathe turning is, its advantages and disadvantages, and the characteristics of each type of lathe turning.
Please also refer to the following pages to learn more about the specific characteristics of lathe turning.
Receive technical proposals at TaigaTable of Contents
What is lathe processing?
Lathe turning is a machining process in which a tool is applied to a rotating material to cut and form it into the desired shape. Since the material itself is rotated, it is used to process round products such as disks, tubes, and rings.
In addition to rounding, grooving and drilling are also possible. The following types of machines are used in lathe processing.
Types of Processing Machines | feature |
NC Lathe | General-purpose lathe that operates and processes cutting tools under numerical control with the following three functions: NC device, operation panel, and servo motor. High-precision positioning in increments of 0.001 mm and automatic machining by program are also possible. |
multi-tasking lathe | NC lathe with milling (machining) functionsCapable of processing that cannot be handled by lathe processing aloneCapable of the following milling processes using rotary tools: Drilling holes in locations other than the center of a round bar, processing the outer diameter portion of a round bar into a square or hexagonal shape. |
Difference between milling and turning
Milling is a machining process similar to lathe turning.
Milling is a forming process in which a rotating tool is applied to a fixed material to shave it.
Turning differs from milling in that turning is done by rotating the material, whereas milling is done by rotating the tool.
For more information about the milling process, seeWhat is milling? Explanation of advantages, disadvantages, types, and differences from lathe processingPlease also refer to the detailed explanation in the "How to Use the Craft" section of the website.
Advantages of Lathe Machining
Turning offers the following advantages
- High machining accuracy
- Easy to operate
- Deformed shapes can also be processed.
- Compatible with a wide range of materials
- Suitable for small lot production
- Short-term production is possible
- Low initial cost
Lathe machining can be performed with high precision to the nearest 0.001 mm by using NC lathe processing machines equipped with numerical controls.
It can also handle more than 200 different materials, ranging from free-cutting to difficult-to-cut materials such as iron, stainless steel, copper, aluminum, and resin.
In addition, lathe turning does not require tooling preparation.
As a result, there is no mold production period or cost, allowing production in a short period of time and at a low initial cost.
Disadvantages of Lathe Machining
Although lathe turning has many advantages, it also has the following disadvantages
- High processing unit cost
- Inefficient when material is large
In particular, keep in mind that mass production with lathe turning is likely to be more expensive than machining with dies.
Seven Types of Turning
The following is a step-by-step explanation of the features of the lathe machining process.
Outer Diameter Processing
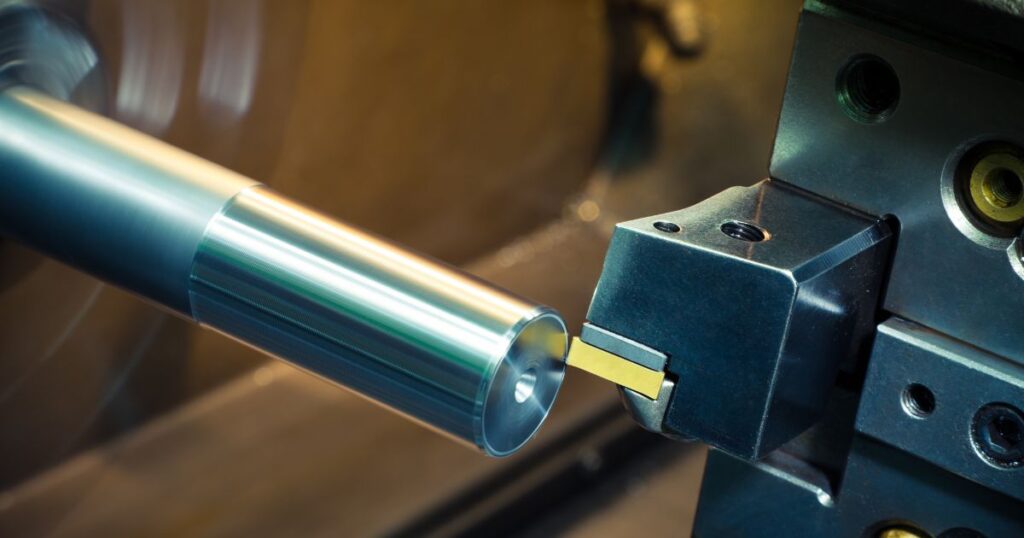
O.D. machining is a machining process to cut the outside of a material.
It is used as the most common method of lathe turning.
O.D. processing can be further subdivided into the following four categories depending on the processing content.
processing method | Contents |
outer-thigh cutter | Can be formed into square and hexagonal shapes by using the side of a machining end mill that reduces the outer diameter by shaving the outer circumference |
cutting in a step | Processing to create staircase-like steps by performing outer rounding multiple times. |
surface cutting | Machining to shave the outer circumference into a curved surface, creating curved and spherical shapes |
knurling | Processing to create a mesh pattern around the perimeter of the material |
Outline machining is used to smooth surfaces or to roughly fit large pieces of material into shape.
Taper processing
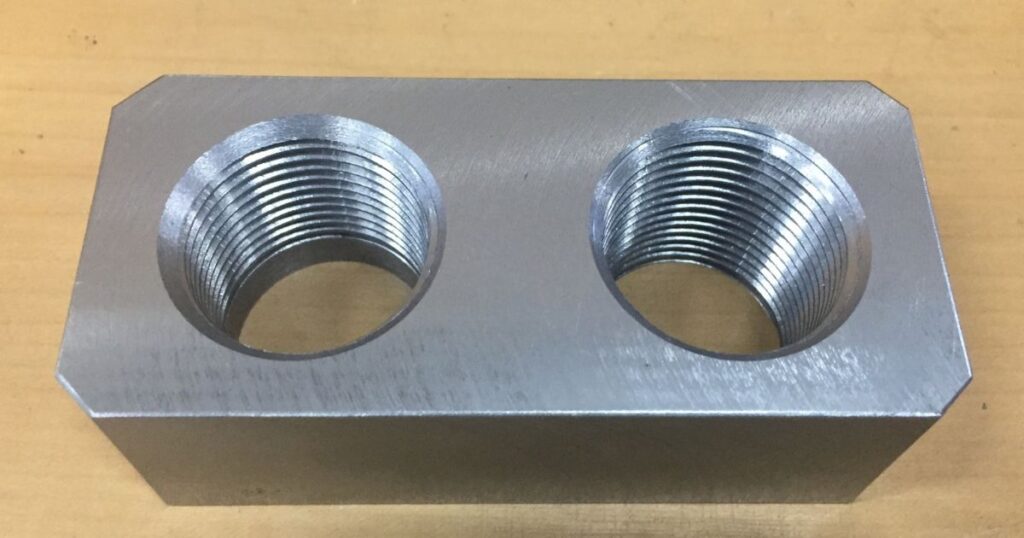
Taper machining is a machining method in which the outer diameter is cut from a cylindrical shape in such a way that the diameter is gradually changed.
It can be processed into a conical shape tapering to the tip.
The basic processing method is the same as that for O.D. processing.
Drilling Process
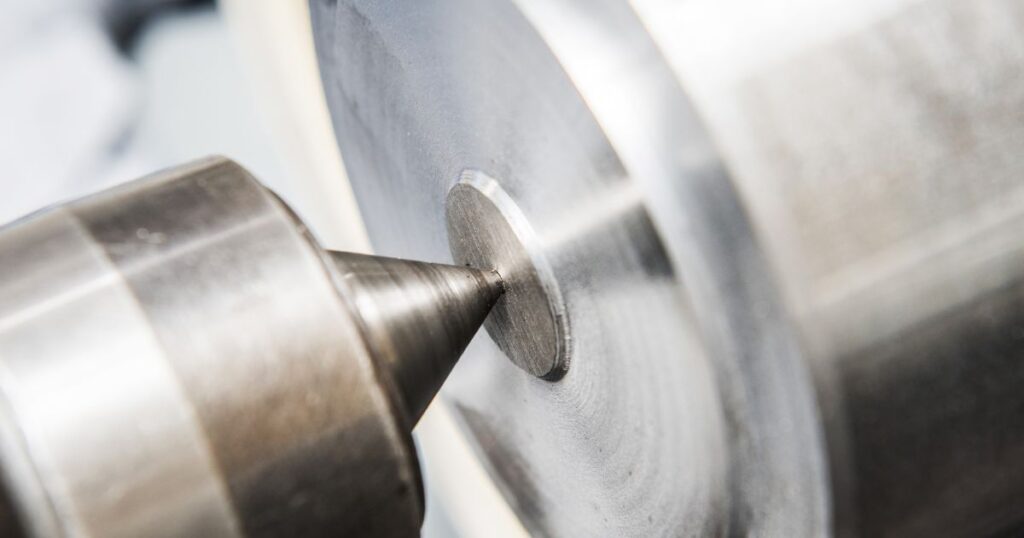
Drilling is a process in which a hole is made in a material using a drill.
The position where the tool is applied is different from that for O.D. machining or taper machining because the material is rotated and the drill is applied from the shaft side to make a hole.
Since shavings tend to accumulate in the hole during drilling, it is necessary to frequently discharge the shavings while drilling.
Inside diameter machining
Inside diameter machining is a machining process in which a tool is inserted inside a material.
It is often used to adjust holes made by drilling.
To perform inside diameter machining, a hole is needed inside the material to allow the tool to enter.
Also, depending on the material, it is necessary to work under conditions where the machined part is not visible, which is more difficult than in the case of OD machining.
Keep in mind that the deeper the hole, the longer the tool needs to be extended, which leads to cracks and breaks, as well as the risk of deflection and vibration that can reduce machining accuracy.
Groove processing
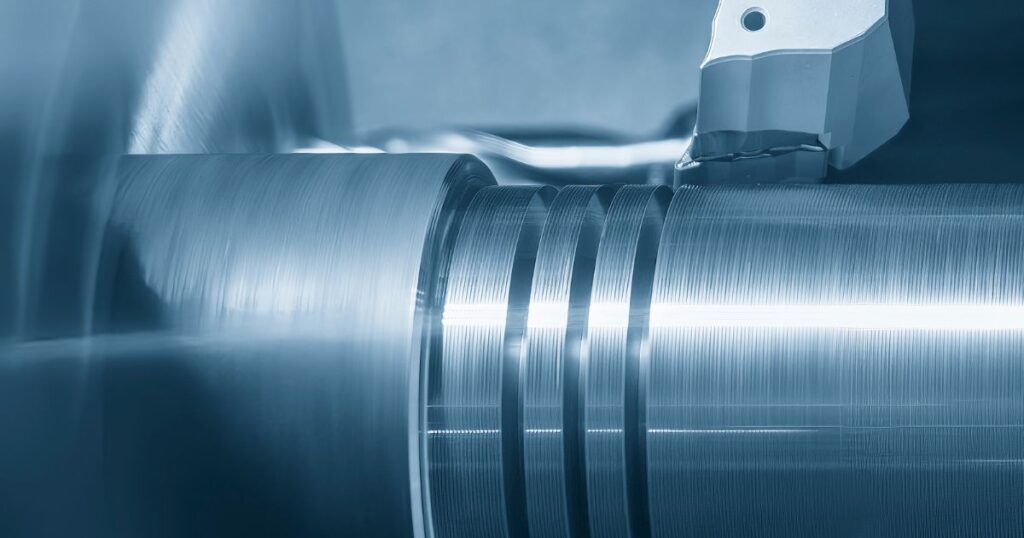
Grooving is a process in which a tool is applied perpendicularly to the material to create a groove.
The tool can be applied and moved vertically, but not horizontally.
piercing through
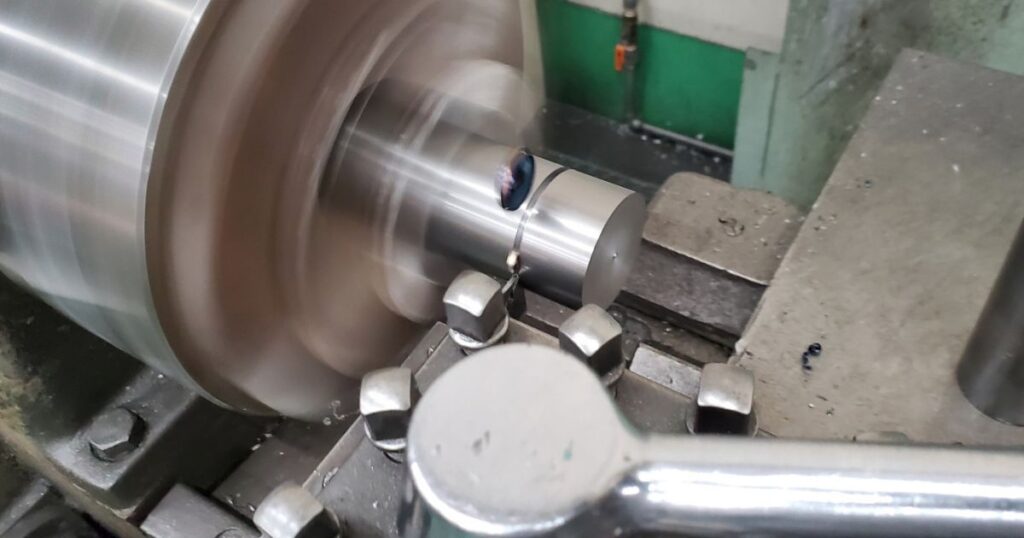
Plunge cutting is a process in which a groove is machined to the center of the material and the material is cut as it is.
In the case of cylindrical materials, if the material is made at the tip and cut off with a butt cutter, machining can proceed in the same manner from the cut-off end face.
Similar to the process of separating a teacup from clay in ceramics and other arts, this method is ideal for separating only the necessary portion from the tip of the material.
thread cutting
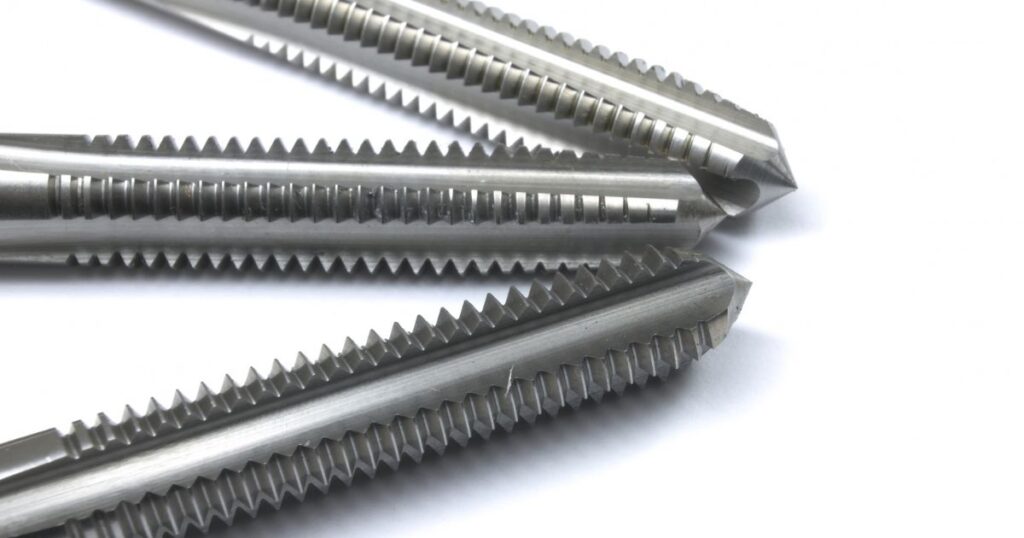
Threading is a machining process in which the tool is advanced in accordance with the rotation cycle of the material to cut out the threads.
There are two types of processing methods: male threading, which creates threads on the outside of the material, and female threading, which creates threads on the inside diameter portion.
Lathe Machining Flow
The machining procedure of lathe turning is explained along with the flow of the process.
Mounting materials and tools on the lathe
First, materials and cutting tools are mounted on the machine.
Positioning and angle adjustment are important during installation.
Note that if positioning and angles are not appropriate, there is a risk of low machining accuracy.
Note that the tools to be used, the installation position, and the angle depend on the material and the desired shape, so a high level of technical skill is required.
Program input of machining details
Next, the program input of the machining content is performed.
On NC lathes, multiple tools can be registered on the machine to allow automatic recall and change of the tool you want to use.
The program sets detailed tools and cutting conditions to be called for each process.
Cutting conditions are conditions that take into account the number of tool revolutions and the amount of material to be cut, according to the material and shape to be machined.
Before starting machining, a "dry run" is performed to ensure that the distance between the material and the tool does not interfere with each other and to confirm that the settings are correct.
perform processing
Once the dry run confirms that the machine works as programmed, the lathe is machined.
The actual machining process involves two steps: rough machining and finishing.
Rough machining is the process of roughly shaving the material to bring it close to the finished product.
Rough machining has the advantage of making it easier to perform fine machining later and reducing the burden on tools and machines.
After rough machining is completed, finish machining is performed.
Finishing operations proceed in the following order: "semi-finishing" in the preparation stage and "finishing" to complete the workpiece. Finishing is a process that requires high precision.
Careful attention is paid to the number of rotations and speed of the material as it is processed.
If burrs appear, sand the surface to avoid damaging the surface.
Summary
This article provided an overview of lathe turning, the differences between lathe turning and similar machining methods, and the types and procedures of lathe turning.
Lathe processing can be achieved with NC lathes to ensure consistent quality regardless of the operator's skill.
Nevertheless, the materials and processing techniques that can be handled vary from processor to processor.
Choose a supplier that can perform the processing that best suits what you want to produce and what you intend to use.
If you are considering manufacturing parts utilizing lathe turning, please contact us.Taiga."Taiga is a free service that allows you to consult with experienced contractors.
We can efficiently proceed with the development of difficult or new parts, small-lot production, prototyping, and mass production while keeping costs low.
Receive technical proposals at Taiga