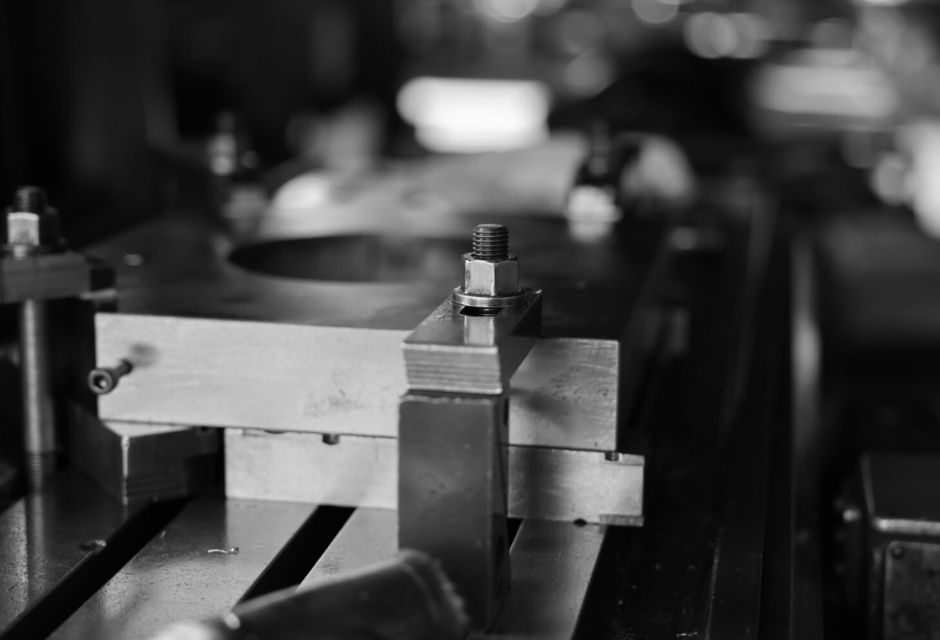
Injection molding requires the fabrication of molds.
But what is an injection mold? What are the design considerations?" and "What are the design considerations?
In this article, we will explain the structure and types of molds used in injection molding, as well as points to note in design.
Please refer to this page for information on the cost of the molds you may be interested in.
Table of Contents
What is an injection mold?
A mold is a metal tool used during plastic working or molding of metal or resin.
In injection molding, softened material is poured into a mold that imitates the shape to be made and cooled to form the product.
Structure and names of injection molds
The structure of an injection mold is as follows
A mold consists of a "core (male mold)" and a "cavity (female mold).
Their respective roles are as follows
(data) item | Core (template) | Cavity (Female) |
role | Forming the inside of the product | Forming the outside of the product |
position | Provided on the movable side mold plate | Provided on the fixed side mold plate |
Main structure | Ejector device (ejector pin) to eject molded product out of mold Ejector pin ejector pin ejecting hole draft angle less than cavity angle (taper) to facilitate molded product ejection | Polished surfaces (mirror finish, chrome plating, etc.) to enhance the appearance of the molded product, as well as the largest possible taper to facilitate molded product removal |
Typical injection mold
There are various types of molds used in injection molding.
Below we will look at the advantages and disadvantages of typical molds.
Mold Structure | Advantages | demerit |
Pin gate type | No need to dispose of runners after products are taken out. | ・Gates remain convex on the surface of the product. ・Filling pressure loss is large, causing appearance defects. |
Submarine gate type | Runner processing after product removal is not required, compact and inexpensive molds, small gate marks on the sides are not convex and less noticeable than pin gates, and runner weight can be reduced compared to pin gates. | ・People are prone to shavings and appearance defects・Heavy filling pressure loss and appearance defects・Need to separate products and runners because they come out of the same place. |
Side gate type | ・Because the gate can be made large, pressure loss is low.・Because the distance between the injection unit and the product can be shortened, runner weight can be reduced. | Runners need to be cut out after molding, and because there are only a limited number of locations where gas venting can be set, gases that have decomposed in the injection unit can easily reach the product. |
Hot Runner Structure | Since only the product comes out, there is no need for runner treatment, less material is used, only a gate mark equivalent to that of submarines is left, and since molten material is injected directly into the product, pressure loss is minimized and the filling rate is stabilized. | ・High tooling and maintenance costs compared to other types of molds ・Molten material is injected directly into the product, so it is easily affected by gases from the decomposition of the material ・Mold structure is more complex, so it is less maintainable than other runner types ・Design changes, etc., are difficult to handle at a later stage. |
pull-through structure | ・Able to form undercut shapes such as screw caps, screws, worms, etc. ・Multiple rotating mechanisms exist. | The rotating parts are constantly rubbing against each other, which causes severe wear and reduces the durability of the mold. |
Slide structure | Undercut shapes can be produced by using a mechanism that moves perpendicularly to the open/close direction. | In the case of multi-cavitation, the die size becomes large in order to secure the width of the slide structure. |
The die that should be used depends on the product and the processing machine, so it is best to consult with the processor to determine the die to be used.
Points to Note in Injection Molding Die Design
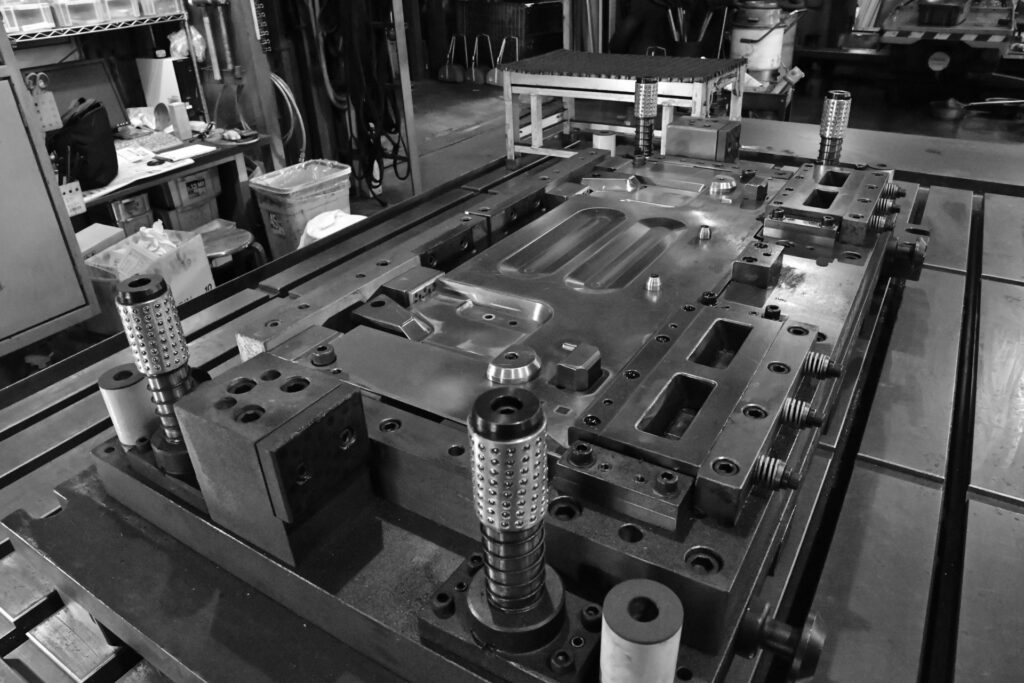
This section describes points to note when designing injection molding dies.
Need to design for injection molding machine
To produce stable products by injection molding, it is necessary to select an injection molding machine with the following capabilities
- Appropriate injection capacity for your product
- Injection pressure
- Mold clamping force
Mold design depends on the type of injection molding machine used.
First, select a molding machine before starting mold design.
Design the shape and structure to fit the molded product
In order to mold with stable quality, the following mold structures should be considered and appropriate molds should be designed.
- Nozzle touch area
- Runner part
- Product part nesting part
- ejector pin
- base
- Guide pins, etc.
Some structures may require secondary processing after molding, so the mold should be designed carefully.
Design with running costs in mind
Molds incur running costs for maintenance and parts replacement.
Select appropriate materials and design them correctly, taking maintenance and durability into consideration.
Not only does this reduce running costs, but it also ensures the accuracy of product quality and extends the life of the molds.
Molds must have draft angles
The draft slope is the slope that is applied to the molded product to pull it out of the mold.
By considering the draft angle, the product can be taken out after injection molding while maintaining its accuracy and quality.
In molds without draft, mold release resistance is likely to damage the product or cause molding defects.
Set the appropriate draft slope according to the structure of the molded product and the mold.
Undercut treatment should also be considered.
An undercut is a shaped portion of a plastic resin molded product that cannot be released in the open/close direction of the mold when the product is removed from the mold.
Molded products cannot be removed with undercuts.
Therefore, it is necessary to install a special mechanism, such as incorporating a slide mechanism in the mold.
Advantages of Injection Molding with Molds
The advantages of injection molding with molds are explained in turn.
Suitable for mass production due to the use of molds
Injection molding using dies has the advantage of mass-producing high-precision products.
In the case of cutting processes that cut resin as it is or casting production using silicon molds, product accuracy tends to vary as production volume increases, and processing time is also required.
In this respect, injection molding using molds can offer significant advantages in terms of product precision and cost.
Compatible with a wide range of materials
There are a variety of plastic resins that are compatible with injection molding.
Even if multiple plastics are used, as long as each has the same degree of shrinkage, a single mold can be used to accommodate material changes.
Able to accommodate minor mold changes
With a single base mold, there is no need to remake the mold even if there are design changes during the process.
The shape can be changed and fine-tuned in the following ways
- Further shave the mold
- Weld and overlay
- Replacing parts of an entry
Injection molding tooling costs
Injection molding die fabrication is expensive and time consuming.
For example, for a mold about the size of a PC mouse, the estimated production cost is about 1.5 to 2 million yen, and the production time is about 1.5 months.
However, the cost and duration of mold fabrication can vary widely depending on the complexity of the part.
A simple mold may be produced for as little as 300,000 yen.
Therefore, when considering injection molding, it is important to consult with a processing company to obtain cost and production time estimates.
Consider the budget and schedule for commercialization, taking into account the costs and timeframe incurred in mold fabrication.
Summary
The structure and types of injection molding dies, as well as their advantages and cautions for die design, are explained.
Injection molding, while capable of mass production of highly accurate products, requires the fabrication of molds.
To achieve satisfactory product manufacturing, be sure to select a processing company with high technology and a proven track record.
If you are considering manufacturing parts utilizing injection molding, please contact us.Taiga."Taiga is a free service that allows you to consult with experienced contractors.
We can efficiently proceed with the development of difficult or new parts, small-lot production, prototyping, and mass production while keeping costs low.
For more information about Taiga, click here.