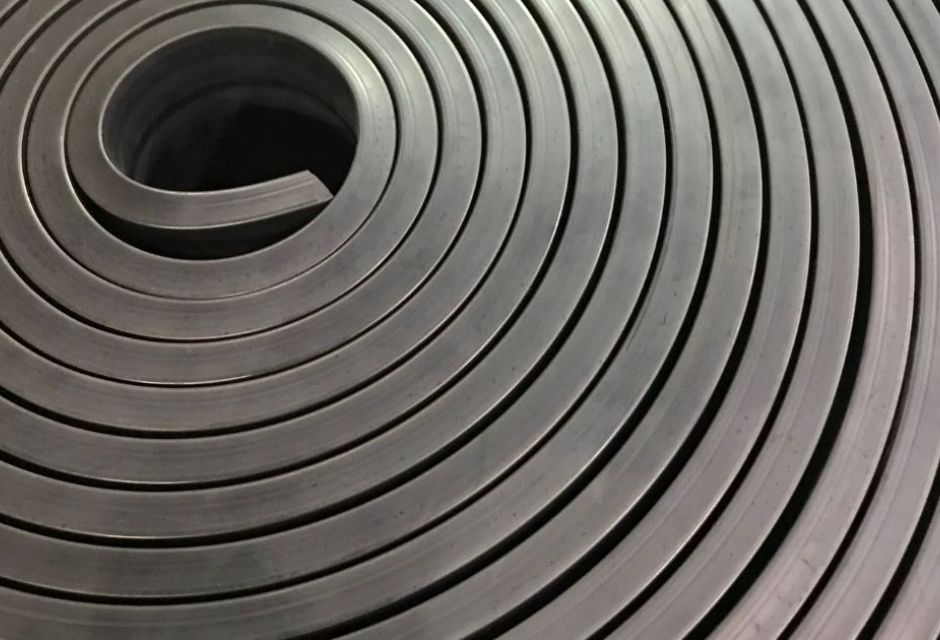
Rubber injection molding is suited for mass production of parts with complex shapes and is used in a wide range of industries, from electronics to automotive and industrial parts.
However, some people who are considering manufacturing products or parts using rubber materials may ask, "What are the characteristics of rubber materials?" What is injection molding? Many of you may have questions such as, "What are the characteristics of rubber materials?
This article therefore provides detailed information useful for product development personnel, including the advantages and disadvantages of rubber injection molding, specific manufacturing processes, and even molding defects and their countermeasures.
We will also compare with rubber molding methods other than injection molding and help you choose the best manufacturing method, so please refer to our website for more information.
Receive technical proposals at TaigaTable of Contents
What is rubber injection molding?
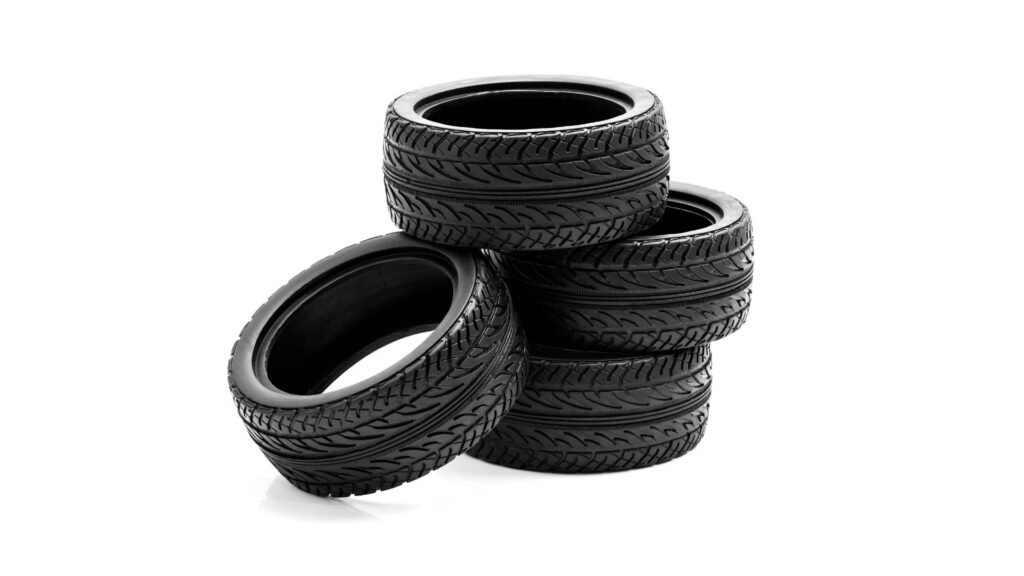
Rubber injection molding is a manufacturing process in which rubber material that has been heated and melted is injected into a mold at high pressure.
Although the initial investment is higher due to the need for molds, it is an economical manufacturing method in the long run because unmanned production is possible through automation.
It is also suitable for parts with complex shapes and mass production, and is used in a wide range of industries, including office automation equipment parts, packing, and medical equipment.
Injection molding is possible with many rubber materials, although the choice of rubber materials is limited to those with high flowability, such as silicone and nitrile rubbers.
Injection molding, which can efficiently produce high-quality products, is attracting attention as an indispensable technology for modern manufacturing.
Difference between insert molding and injection molding
Insert molding and injection molding are molding technologies with different manufacturing processes and applications.
Injection molding is a method in which plastic resin is melted at high temperature and pressed into a mold to solidify it, and is suitable for mass production. Insert molding, on the other hand, is a molding technique in which metal or different material parts are placed inside the mold and resin is injected around them.
One of the advantages of insert molding is that by integrating dissimilar materials, it eliminates the need for post-processing and leads to cost reduction.
Because it improves strength and durability compared to adhesion in subsequent processes, it is particularly useful in applications where durability is important, such as automotive parts where adhesion between rubber and metal is required.
Advantages of choosing injection molding as a molding method for rubber
Rubber injection molding offers the following advantages
- Accuracy.
- Capable of molding complex shapes
- Almost no post-processing required
- Short curing time
- Lower unit cost per product
By pressurizing and injecting highly fluid rubber, the material is evenly distributed throughout the mold, enabling the molding of precise and highly accurate shapes.
It also supports the molding of minute holes and complex curved surfaces, allowing for a high degree of design freedom and the manufacture of complex parts.
Since there are few parting lines or gate marks that tend to appear during the molding process, the finished product is very close to the finished product, so little or no post-processing is required.
Furthermore, the latest technology that precisely controls temperature and pressure reduces the time required for molding, which is a nice feature.
Disadvantages of using injection molding for rubber molding
On the other hand, the following disadvantages exist in rubber injection molding
- High initial cost
- Not suitable for small-lot or low-volume production
- Limited materials available
- High maintenance costs for molds
In injection molding, it costs a lot of money to fabricate molds and prepare injection molding machines.
Small-lot production is not suitable due to the high initial cost.
In addition, the materials that can be used are limited to silicone rubber, nitrile rubber, polyurethane, and other highly flowable rubbers, so the choice of materials is limited.
Periodic maintenance of the molds will also be required, so running costs will need to be considered as well.
Injection molding flow of rubber
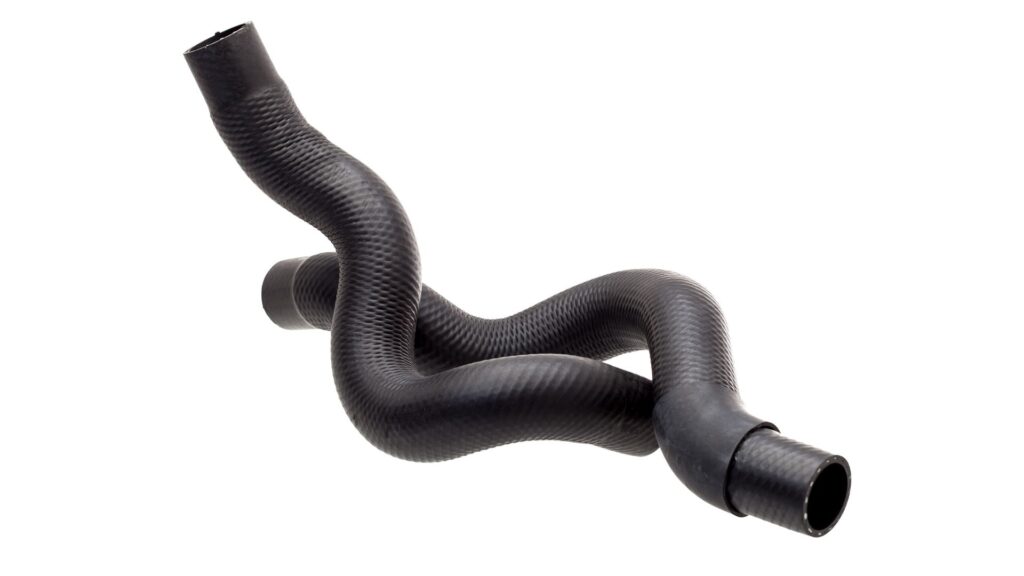
Rubber injection molding is a precision manufacturing process that involves multiple steps to produce a product.
Below is a brief look at the rubber injection molding procedure.
kneading operation
Since rubber materials cannot be used for molding in their raw state, they must be kneaded with a cross-linker or filler to give them elasticity.
First, the molecular structure is softened by "kneading," then vulcanizing agents and pigments are added by "kneading," and forming materials are made by a kneader or roll machine.
In the mixing process, it is important to maintain material uniformity while strictly controlling temperature and time.
The mixing balance and mixing condition here greatly affect the performance of the final product, such as the strength and hardness of the rubber.
Cutting and mold clamping
The rubber material kneaded in the roller machine is prepared into sheets and cut into appropriate sizes according to the product.
Next, the cut material is placed in the injection molding machine and proceeds to the mold clamping process to close the mold.
Mold clamping is the process of applying strong pressure to the mold to prevent it from opening under pressure when the mold is filled with rubber.
Proper pressure setting increases dimensional accuracy and prevents rubber leakage.
Injection Molding
Once the mold is tightened, the heated and melted rubber material is injected into the mold.
It is important to precisely control injection speed, pressure, and temperature to ensure that the entire mold cavity is filled uniformly.
If the molding conditions are not set correctly, defects such as sink marks, short shots, and weld lines may result. Therefore, advanced technology is required for injection setting during molding.
After injection, the rubber is vulcanized (cured), maintaining pressure and temperature to ensure the specified shape and strength.
Finishing
Once molding is complete, carefully open the mold and remove the product.
The speed and angle of mold opening must be carefully designed and adjusted because they affect quality.
The removed product may have burrs (excess rubber) or gate marks, which are removed in the finishing process.
Dimensional and visual inspections are also performed as needed, and products are cleaned and packed ready for shipment.
Common molding defects in rubber molding
Injection molding of rubber can result in a variety of molding defects.
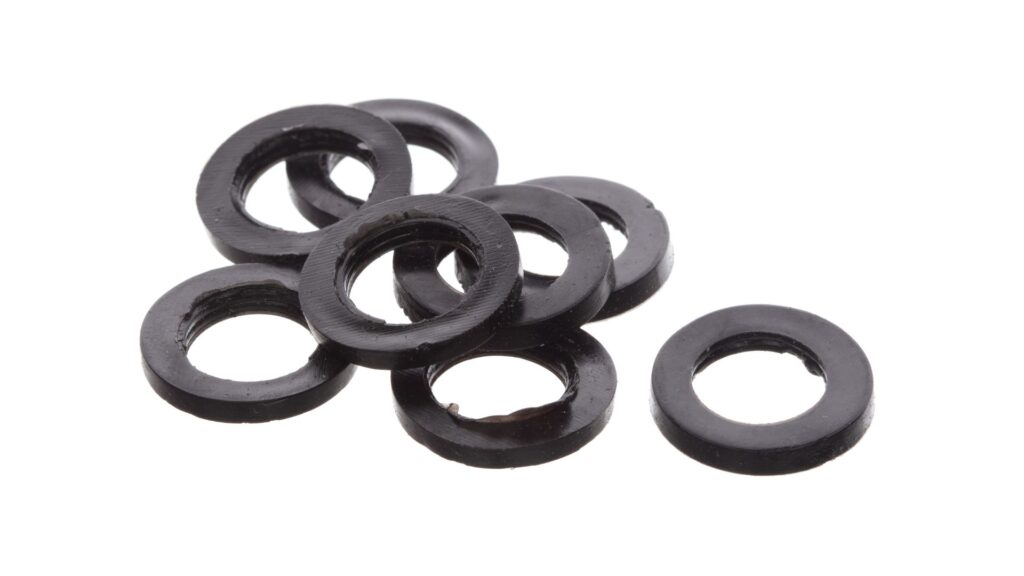
Typical molding defects are as follows
- Short shot (underfilled)
- Burr (overhang)
- Weld line (confluence line)
- Hike (backlinding)
- Air (bubble)
- foaming
- wane (of the moon)
- deformation
- contamination by foreign substances
These defects cause problems such as reduced product strength, poor appearance, and reduced precision.
To prevent molding defects, it is necessary to optimize molding conditions, review mold design, select materials, and improve the work environment.
Rubber molding methods other than injection molding
Other than injection molding, the main rubber molding methods include compression molding, press-fit molding, extrusion molding, and machining.
The advantages and disadvantages of each are as follows
Molding Method | Advantages | demerit |
Compression molding | Low tooling cost, simple equipment, minimal materials used | ・Lots of burrs and thick products have low dimensional accuracy. |
Press-in molding | High dimensional accuracy, capable of molding complex shapes, suitable for metal inserts | Complex mold structure, expensive, large amount of scrap |
Extrusion molding | ・Continuous production of long products is possible・Efficient production | Limited cross-sectional shape, Difficult to mold complex shapes |
machining | No tooling required, small-lot production, molding of complex shapes possible | ・High unit price per product・Sophisticated technology is required for some shapes |
Compression molding is relatively inexpensive and simple, but has accuracy issues.
Press-fit molding is also suitable for complex shapes with high accuracy, but its drawback is its high cost.
Extrusion is suitable for the production of long products, but offers limited flexibility in shape.
Thus, each molding method has its advantages and disadvantages.
Based on the characteristics of each, it is important to select the best molding method according to the product shape, production volume, and required accuracy.
Summary
Rubber injection molding is an efficient manufacturing method that can mass produce parts with high precision and complex shapes.
Although the initial investment is high, it has excellent characteristics in terms of productivity and quality.
However, because of material limitations and the risk of molding defects, comparisons with other molding methods should be made according to product requirements and production scale.
In many cases, the injection molding of rubber materials will be done by a processing company.
Since each supplier has different moldable materials and manufacturing experience, please check carefully whether the supplier can handle rubber materials as well as has molding experience for the product or part you wish to manufacture.
Through the selection of appropriate molding methods and collaboration with specialized suppliers, we are able to develop and manufacture high-quality rubber products.
If you are considering manufacturing parts utilizing injection molding, please contact us.Taiga."Taiga is a free service that allows you to consult with experienced contractors.
We can efficiently proceed with the development of difficult or new parts, small-lot production, prototyping, and mass production while keeping costs low.
Receive technical proposals at Taiga