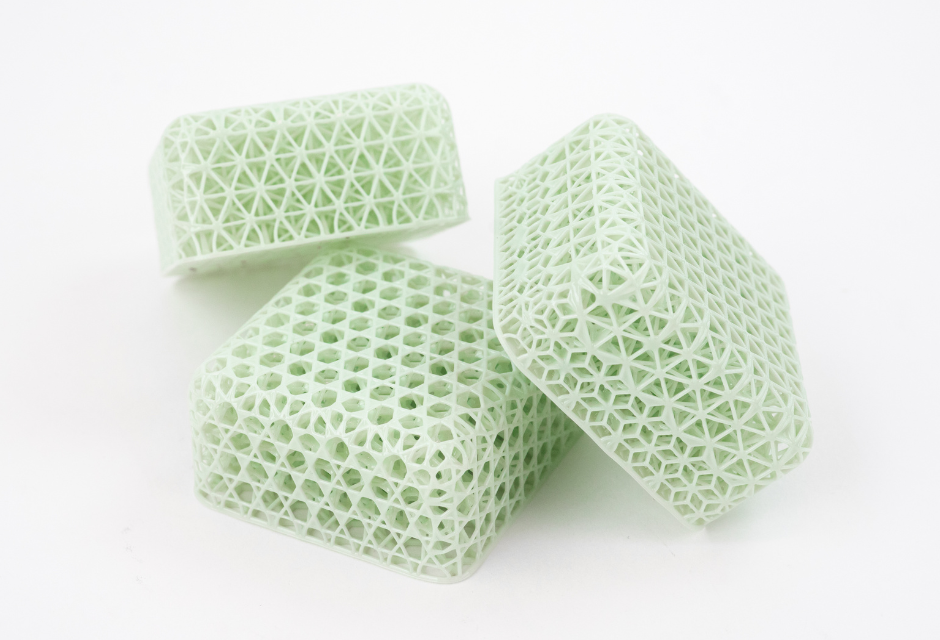
Many people are considering the use of rubber materials in 3D printer fabrication.
But in reality, it is a question of "What kind of product is it best suited for?" What are the advantages and disadvantages?" and so on.
This article therefore provides a detailed explanation of the features, advantages, disadvantages, and cautions of rubber filaments for 3D printing.
If you want to know how to properly use rubber filament for 3D printing, please refer to this page.
Receive technical proposals at TaigaTable of Contents
What is rubber filament for 3D printing?
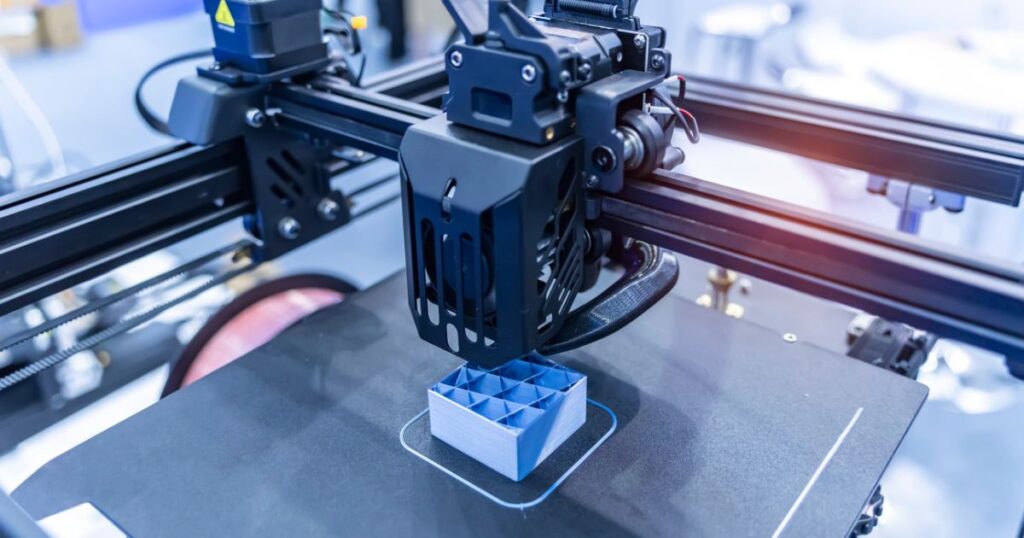
Rubber filament for 3D printing is a rubber material that has been attracting attention in recent years in 3D printing.
It has excellent flexibility and elasticity, and is available in TPU (thermoplastic polyurethane) and TPE (thermoplastic elastomer) types. Due to their characteristics, they are utilized in shoe soles, anti-vibration parts, prototype parts, etc., where impact resistance and abrasion resistance are required.
It is often used in situations where durability and flexibility are needed, but the technical hurdles are higher than with regular filament, requiring knowledge of correct print settings and handling.
Types of rubber used for 3D printing
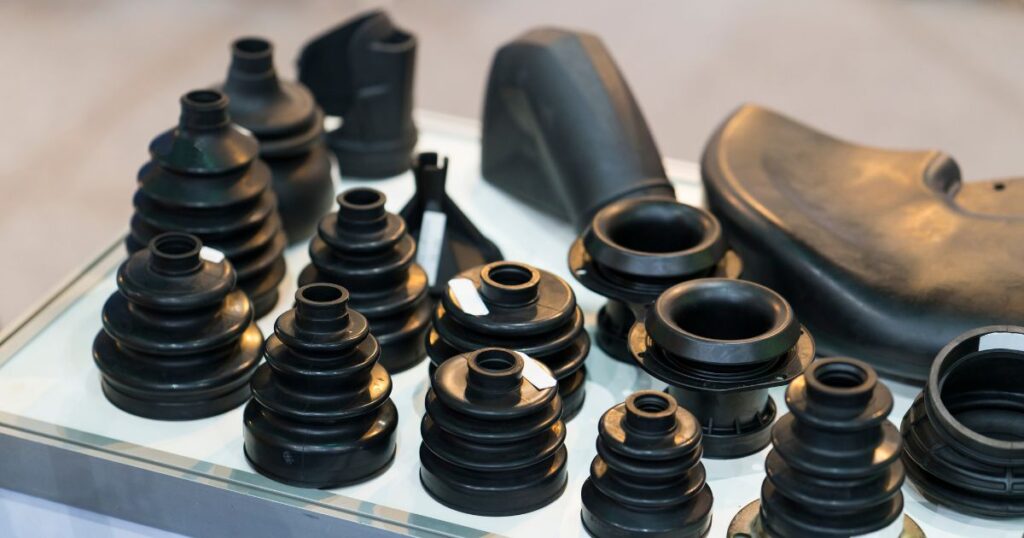
There are three main types of rubber used for 3D printing
- TPU (thermoplastic polyurethane-based)
- TPE (thermoplastic elastomer-based)
- TPC/PBAT (polyester-based)
Each will be explained.
TPU (thermoplastic polyurethane-based)
TPU (thermoplastic polyurethane-based) is a material that combines rubber-like elasticity and durability.
High abrasion and impact resistance makes it suitable for products that are subjected to high loads, such as shoe soles and anti-vibration parts.
Because of its flexibility and ability to maintain its shape, it is also used for handrails for escalators.
On the other hand, appropriate temperature control is required during printing, so care must be taken to adjust the print speed.
TPE (thermoplastic elastomer-based)
TPE (thermoplastic elastomer-based) filaments are characterized by their flexibility and rubber-like feel.
It is mainly used in applications such as toys, medical parts, and grips, and is suitable for situations where softness is required. However, due to its low heat resistance, care should be taken as its performance may deteriorate in high-temperature environments.
The flexibility of the material makes it easy to handle for first-time users of rubber filaments.
TPC/PBAT (polyester-based)
TPC and PBAT (polyester-based) are materials with high heat resistance and are attracting attention in applications requiring environmental friendliness.
It also has excellent chemical resistance, making it suitable for industrial parts and products that come in contact with chemicals.
PBAT is also used for food packaging and flexible films.
However, the strength of the material itself is not strong, so it is very important to check the strength of the material before manufacturing.
Advantages of using rubber for 3D printing
There are three advantages to using rubber for 3D printing
- High durability and elasticity
- Flexible and suitable for a wide range of situations
- Excellent shock resistance and vibration absorption
Each will be explained.
High durability and elasticity
Rubber filament is a material characterized by high durability and elasticity.
Durability refers to the property of resistance to damage when subjected to strong impact or pressure, while elasticity refers to the ability to return to its original shape after deformation.
In addition, rubber filaments are highly resistant to abrasion and tension, providing stable performance over a long period of time.
This makes it suitable for products that are used repeatedly, such as shoe soles and anti-vibration parts, as well as for manufacturing parts that require strength and flexibility.
Flexible and suitable for a wide range of situations
Rubber filament is a highly flexible material suitable for a wide range of situations.
Because of its high shock absorption and vibration dampening effect, it is widely used in environments where loads are applied, such as automobile parts, sporting goods, and shoe sole materials.
It is an excellent choice for products requiring flexibility.
Excellent shock resistance and vibration absorption
Molded objects made of rubber filaments are highly resistant to impact and absorb vibration.
In particular, materials such as TPU and TPE deform and absorb shock when impact is applied, preventing damage.
It is also excellent at absorbing vibration as well as shock, and is therefore often used in products that are subject to external shock, such as smartphone cases and components with anti-vibration functions.
Disadvantages of using rubber for 3D printing
There are three disadvantages to using rubber for 3D printing
- Requires high technology for printing
- Not suitable for modeling that requires high precision
- Higher material costs compared to common filaments
Each will be explained.
Requires high technology for printing
3D printing of rubber filaments requires high technology.
Rubber materials tend to clog nozzles more easily than common filaments, and filaments can be deformed during modeling.
In addition, due to its heat-sensitive characteristics, it must be properly cooled.
Therefore, it is essential to adjust temperature and printing speed when using rubber filaments.
Since it can be challenging for beginners, when requesting 3D printing, carefully check if the company has experience in modeling with rubber filaments.
Not suitable for modeling that requires high precision
Due to its soft nature, rubber filament is a material that is prone to imperfect adhesion between layers (thin layers that are layered when creating objects with a 3D printer).
Therefore, it is not suitable for modeling that requires high precision.
The soft nature of rubber filaments also makes them susceptible to vibration and machine movement during printing. For example, when making fine designs or complex parts, the edges may blur and the surface may not be smooth.
Accuracy requires careful adjustment of printer settings as well as the selection of quality filaments.
Higher material costs compared to common filaments
Rubber filaments tend to be more expensive than common filaments, making them more cost-effective.
At the time of use, efforts must be made to reduce waste by determining the amount needed.
Scenes for which rubber 3D printing is suited
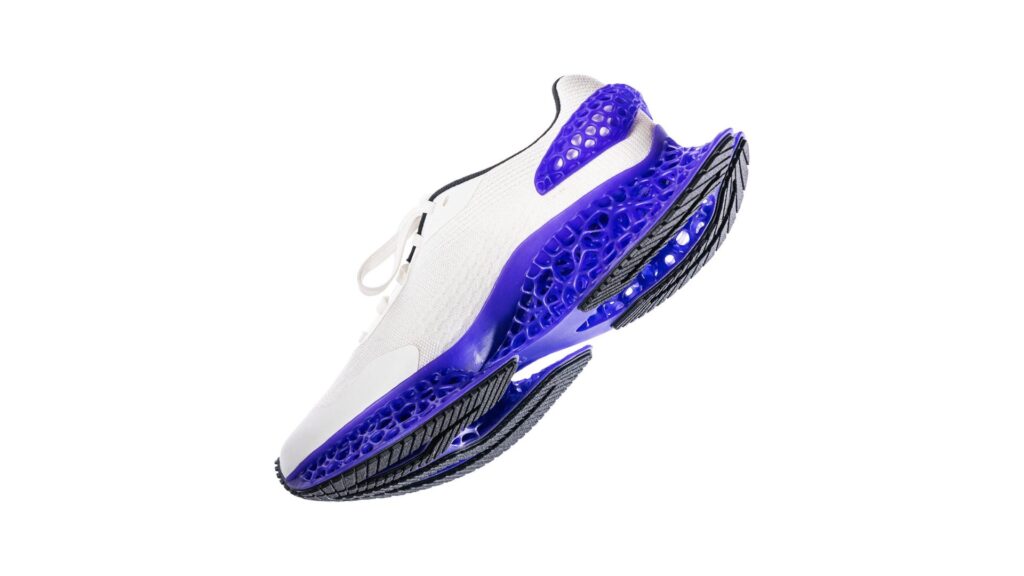
The table below summarizes the situations in which rubber 3D printing is suitable and why, and should be of interest to anyone considering the use of rubber filaments for 3D printing.
Scenes for which rubber 3D printing is suited | reason |
Phone case | Shock-absorbing material, effective in absorbing shock when dropped |
Shoe sole | Excellent cushioning and durability |
medical instruments | Can manufacture custom-made instruments to suit the patient. |
Points to keep in mind when 3D printing with rubber
There are three things to keep in mind when 3D printing with rubber
- Use a special nozzle for rubber filaments
- Set appropriate temperatures
- Set a slower molding speed
Each will be explained.
Use a special nozzle for rubber filaments
Rubber filaments tend to clog nozzles due to their flexibility and elasticity.
Therefore, it is recommended that a dedicated nozzle be used.
It is also important to set the nozzle diameter large enough to allow soft materials to pass through smoothly.
Besides, regular nozzle maintenance will reduce the risk of clogging.
Set appropriate temperatures
When using rubber filament, adjust the temperature setting of the printer appropriately.
Rubber filaments are highly viscous and can cause nozzle clogging if the temperature is too low.
Conversely, if the temperature is too high, the filament may melt and the shape of the modeled object may be destroyed.
It is important to set the temperature based on the manufacturer's recommendations and make fine adjustments as necessary.
Set a slower molding speed
Since rubber filaments have high viscosity, too fast a molding speed is likely to cause nozzle clogging and shape distortion.
By setting a slower molding speed, the filament is extruded evenly and stable molding is possible.
Slowing down the molding speed can also be expected to improve the accuracy of the product.
Summary
Rubber filaments for 3D printing have excellent flexibility and elasticity properties and are used in a variety of applications, such as shoe soles, anti-vibration parts, and prototype part fabrication.
On the other hand, since modeling requires advanced techniques and settings, it is important to prepare in advance and understand the characteristics of the material itself. In order to achieve highly accurate modeling using rubber materials, it is essential to select a specialized company that meets your company's needs.
By choosing the right contractor, you will get the results you expect.
If you are considering manufacturing or prototyping products or parts using 3D printing, please contact us!Taiga."Taiga is a free service that allows you to consult with experienced contractors.
We can efficiently proceed with the development of difficult or new parts, small-lot production, prototyping, and mass production while keeping costs low.
Receive technical proposals at Taiga