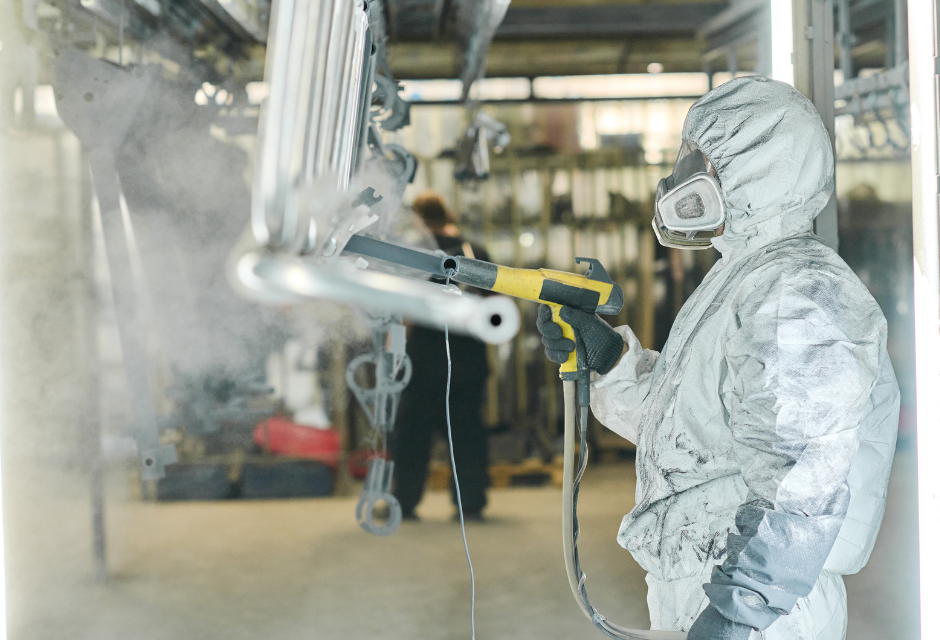
Powder coating is attracting attention as an environmentally friendly coating technology. Compared to conventional solvent coating (liquid coating), it has a great many advantages and has been introduced in various fields.
Many of you reading this article are probably interested in powder coating.
In this article, we will explain in detail what powder coating is and what are its advantages and disadvantages.
For more information about Taiga, click here.Table of Contents
What is powder coating?
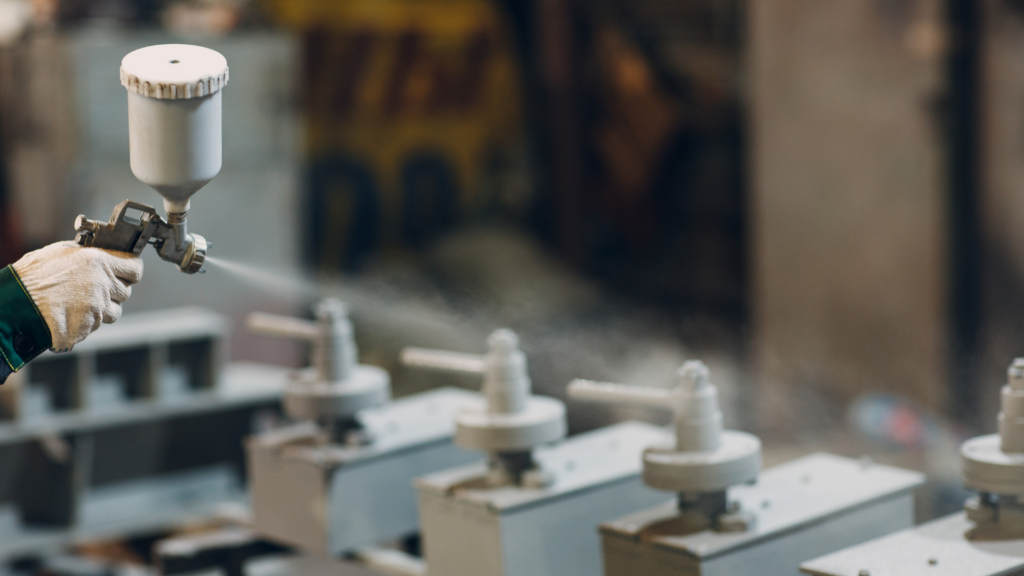
Powder coating is a method of applying paint that has been crushed into powder form. It is also known as "powder coating.
Powdered paint is applied to the object and melted at high temperature before drying.
Powder coatings can be thermosetting, such as epoxy and polyester, or thermoplastic, including polyethylene and nylon. Both are characterized by their ability to thicken the coating film, which helps prevent rust.
Advantages of Powder Coating
The advantages of powder coating are as follows
- A thick coating can be formed even with one coat.
- Gentle on the human body and the environment
- High durability and rust resistance
- Cost-effective compared to solvent coating
Let's take a closer look at each of these.
A thick coating can be formed even with one coat.
The paints used in powder coating have larger particles than solvent paints. As a result, they adhere better to object surfaces, including edges, and can form a thicker coating film with a single coat.
It also has excellent corrosion resistance and is less likely to rust or peel than solvent coating, requiring less frequent re-coating.
Gentle on the human body and the environment
Another advantage of powder coating is that it is friendly to the human body and the environment. Powder coating contains no VOCs (volatile organic compounds) or solvents that can cause environmental pollution, thus reducing various risks, including sick building syndrome.
It is also an eco-friendly coating that is friendly to both the human body and the environment because of its low risk of ignition and low CO2 emissions.
High durability and rust resistance
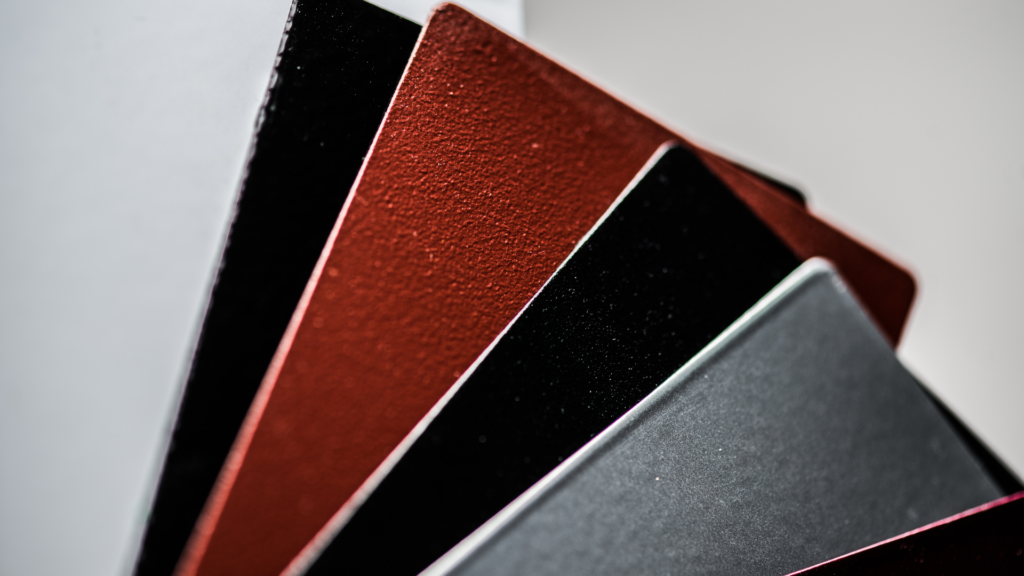
Powder coating, in which the paint is heated to dry and cure, not only thickens the coating but also enhances its durability.
Specifically,
- Impact resistance
- heat-resisting property
- chemical resistance
- corrosion resistance
- Anti-corrosive
and other improvements can be expected, making it easier for the product to last longer.
Cost-effective compared to solvent coating
Powdered paints are said to have higher adhesion efficiency than liquid paints. High adhesion efficiency means that a large area of paint film can be formed with a small amount of paint.
In addition, powder coatings do not contain solvents, allowing for the recovery and reuse of the paint.
This makes it easier to reduce costs and environmental impact.
Disadvantages of powder coating
Such powder coating also has the following disadvantages.
- Difficult to form thin coating films
- Construction can only be done in a factory with dedicated equipment.
Let's take a closer look at each of these.
Difficult to form thin coating films
Powder coating is a coating method that excels at forming thick coating films. Therefore, it is slightly more difficult to form a thin coating film.
Strictly speaking, it is possible to make the coating film thinner, but if it is finer than a certain level, electrostatic repulsion may occur, reducing efficiency and productivity. In particular, please note that it is extremely difficult to form a coating film that is less than 30 microns in thickness.
If thin coatings are intended to be formed, solvent coating is recommended instead of powder coating.
Construction can only be done in a factory with dedicated equipment.
Powder coating dries and cures with the help of static electricity and heat. For this purpose, large hot-air drying furnaces and spray guns are required. Therefore, it is impossible to apply the coating at a coating company or site that does not have these facilities.
If you do not have your own powder coating equipment, you will need to hire an outside contractor, so be sure to find one you can trust to ensure a smooth installation.
Powder Coating Types
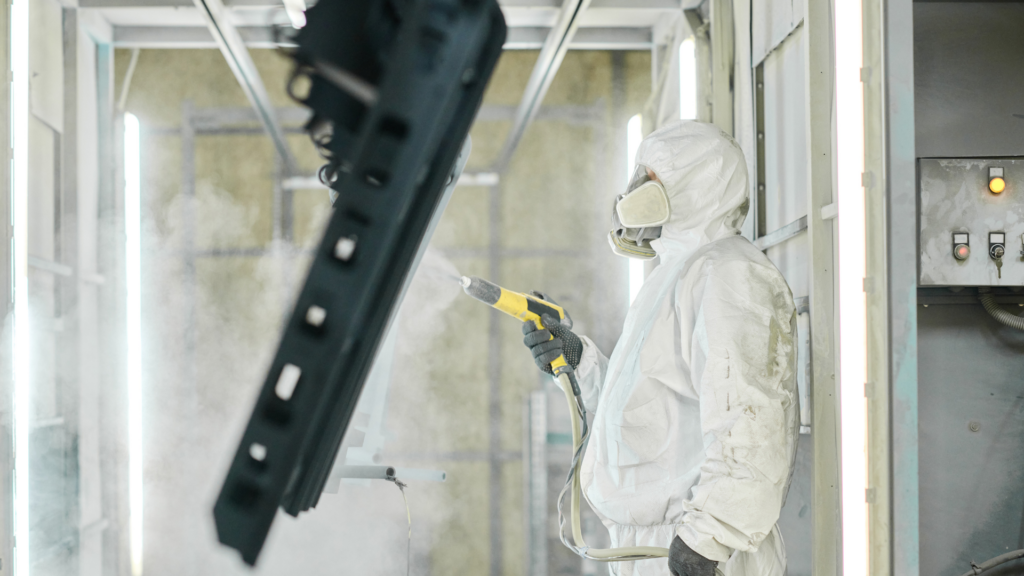
Powder coating can be broadly classified into the following two types
- Electrostatic powder coating method
- Fluid Dip Coating Method
Let's take a closer look at each of these.
Electrostatic powder coating method
The electrostatic powder coating method is a method of coating using the force of static electricity. The object is connected to ground and positively charged, and a spray gun is used to inject negatively charged powder paint.
In this coating method, the following process is commonly used while using thermosetting powder coatings.
[Construction Procedure of Electrostatic Powder Coating Method].
- pretreatment
- Drainage drying
- Powder coating
- Baking and drying
- Cooling
The electrostatic powder coating method has few restrictions on the shape and size of the object, and is characterized by its ease of obtaining a uniform film thickness.
Note, however, that painting is not possible on materials that do not conduct electricity.
Fluid Dip Coating Method
In the fluidized dip method, the object is heated and the powder coating is placed in a container called a fluidized dip tank in which compressed air is used to fluidize the powder coating. Simply put, the paint is melted by heat and adhered to the object.
This coating method is generally applied by the following process while using thermoplastic powder coating.
Flow Dip Coating Procedure
- pretreatment
- preheating
- Fluid Immersion
- post-heating
- Cooling
The fluidized dip coating method is characterized by its ease of thick film coating and the fact that it does not require powder coating recovery equipment. It is also possible to coat materials that do not conduct electricity.
Note, however, that the coating must be less than or equal to the size of the fluidized dip tank.
Common problems and countermeasures for powder coating
Powder coating often causes the following problems
- Powder coating peels off
- Surface rusting
- Wavy coating surface
As for the cause of the powder coating peeling off,
- pretreatment (programming, programing)
- Incompatibility of material and paint
- Baking conditions are not appropriate
This may be the case.
To prevent such problems, it is important to carefully perform pretreatment, select the right paint for the material, and perform baking under the correct conditions.
The causes of surface rusting include,
- Insufficient adjustment of the substrate
- Oil stains and moisture buildup
- Low rust-preventive performance of paint
- Paint film is thin
- High humidity
This may be the case.
To prevent such problems, it is important to take measures such as adjusting the object's surface by polishing, etc., reviewing sanitation, and thickening the coating.
The cause of waviness of the paint film surface is,
- Insufficient or excessive film thickness
- Voltage is too high.
- Leave for a long time
- Temperature is too high.
This may be the case.
To prevent such problems, it is important to adjust the film thickness and voltage appropriately.
Typical types of powder coatings
There are two main types of paints used in powder coating
- Thermosetting Powder Coatings
- Thermoplastic powder coating
Let's take a closer look at each of these.
Thermosetting Powder Coatings
Thermosetting powder coatings are coatings with the characteristic of irreversibly curing as a result of accelerated chemical reaction upon heating.
This paint does not dissolve once cured,
- durability
- chemical resistance
- heat-resisting property
It can form a coating film with
Typical types are as follows
- epoxy-based
- Epoxy polyester-based
- Polyester type
- acrylic
- fluorinated
Each resin system has different applications and conditions, so select the most suitable paint after considering the object and its characteristics.
Thermoplastic powder coating
Thermoplastic powder coatings are coatings with the characteristic of softening upon heating and hardening upon cooling. Since the process is reversible, heating and cooling can be repeated.
Typical types are as follows
- vinyl chloride-based
- Polyethylene-based
- Nylon type
Among these, vinyl chloride and nylon types are often used as road materials because of their excellent corrosion resistance and weather resistance.
What equipment is needed for powder coating?
As explained earlier, powder coating requires specialized equipment and tools.
Below is a detailed look at the minimum equipment requirements.
powder booth
Powder booths are designed to prevent foreign matter from entering the facility. This is an indispensable facility for improving coating adhesion efficiency.
It also helps with things like normal air intake and paint collection.
powder spray gun
A powder spray gun is a machine used to spray powder paint onto an object. In most cases, an electrostatic gun type is used.
Components of an electrostatic gun
- Electrostatic Gun
- controller
- Paint tanks
- Paint supply equipment
Feed Center
A feed center is a control system for powder coating. Thanks to this control system, it is possible to contain the powder during operation and make sophisticated color changes.
This makes the feed center an essential facility for a clean, safe, yet productive environment.
pump
The pump is a device that draws powder from the paint tank, atomizes the powder stream, and transfers it to the spray gun. This equipment plays an important role in ensuring efficient and accurate painting.
Therefore, a product with high precision must be used.
If you are looking for a place to order powder coating, "Taiga" is a good place to start!
Powder coating is more environmentally friendly than solvent coating and has many advantages in construction.
However, because the work cannot be performed without specialized facilities and equipment, outsourcing must be considered if the company does not have the facilities in-house. Powder coating requires advanced technology, so it is important to carefully select a contractor if you choose to outsource the work.
The Taiga is useful in such cases.
Taiga is a platform that connects users and partners to provide smooth and safe manufacturing from design to delivery.
Many useful functions are provided, such as a drawing editing function that allows multiple people to coordinate their perceptions, a chat function, and a management function that allows batch management of drawings, quotations, and projects. Re-purchasing can also be done with a single click, which is convenient when you want to order the same part again.
Please feel free to contact "Taiga" for smooth and safe ordering of powder coating.
Summary
Powder coating, which involves the application of powdered, crushed paint, is more environmentally friendly than solvent coating and offers many advantages in terms of cost and finish. In addition, by selecting the appropriate coating material, it is possible to apply the coating to a wide variety of objects, and is currently attracting attention in many industries.
However, powder coating requires specialized equipment, advanced knowledge, and skill. If you are unable to perform the work in-house, it is recommended that you outsource the work to a contractor with extensive experience. However, selecting an outsourcing company for powder coating is not so easy and can be time-consuming.
In such cases, please use Taiga, which supports various manufacturing processes including powder coating.
For more information about Taiga, click here.