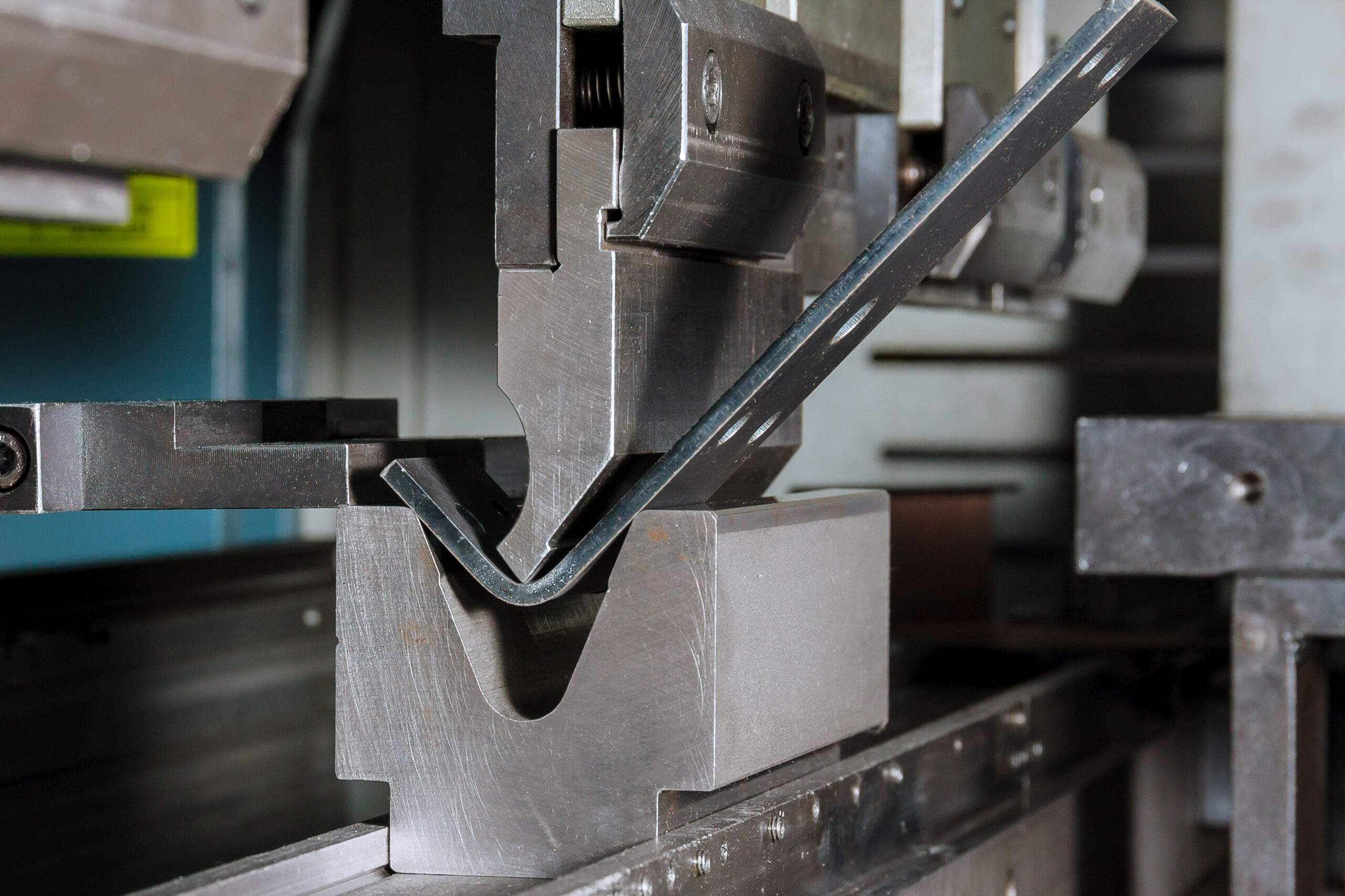
Sheet metal fabrication is a typical metal processing method.
When you are considering manufacturing a product using sheet metal, you may be asking yourself, "In what situations is sheet metal fabrication used?" Are there different types of sheet metal fabrication? and "What are the different types of sheet metal processing?
In this article, we will provide an overview of sheet metal welding processes, their advantages and disadvantages, as well as the characteristics of each type of sheet metal welding process.
Please refer to the following information on how to select a contractor for sheet metal welding fabrication.
Receive technical proposals at TaigaTable of Contents
What is the welding process for sheet metal?
Sheet metal welding process is a method of joining two or more sheets of sheet metal by melting them together.
Unlike joining methods using adhesives or screws, sheet metal is melted to form a single piece, thus achieving a strong joint.
Note that there are various methods of melting sheet metal, including heating and pressure.
Advantages of Sheet Metal Welding Process
Sheet metal welding processes have the following advantages
- Airtight
- Leads to cost reductions
- Flexibility in working
Sheet metal welding melts sheet metal to make the joint, which has the advantage of making the joint surface airtight.
Therefore, it is also suitable for joining items that require airtightness of joints, such as ships and aircraft equipment.
It can be joined without using materials such as adhesives or screws, and even complex shapes can be fabricated at a lower cost compared to other processing methods.
Some welding methods do not require special equipment or facilities, and can be performed indoors or outdoors.
Another advantage of sheet metal welding processing is the flexibility to choose the work environment that best suits the situation.
Disadvantages of Sheet Metal Welding Process
Although sheet metal welding has many advantages, it also has the following disadvantages
- Strain and residual stress may occur
- Joined parts cannot be disassembled.
- Workmanship depends on the skill of the operator.
Sheet metal welding involves heating or squeezing a portion of the sheet metal to join it, which causes non-uniform expansion and contraction, resulting in strain and residual stress.
Therefore, the disadvantage of manual welding is that it lacks stability because the welding workmanship and quality vary depending on the skill of the operator.
In addition, since sheet metal is melted and joined, the joined parts cannot be disassembled.
Since they are not removable like screws, they must be broken when a jointed part needs to be disassembled.
Three types of sheet metal welding processes
There are three types of sheet metal welding: fusion welding, pressure welding, and brazing.
The features of each processing method are described below.
Welding process by fusion welding
Fusion welding is a method of welding by heating and melting the sheet metal to be joined.
There are three types of welding: arc welding, laser welding, and gas welding.
arc welding
Arc welding is a welding method in which metal is melted by the heat of sparks (arc) generated by electrical discharge.
In general, many people have an image of welding as work with sparks, and this work corresponds to arc welding.
The arc is generated between the base metal and the welding rod or electrode with high voltage applied.
There are different types of arc welding, such as mag welding, mig welding, and tig welding.
Laser welding
Laser welding is a welding method that melts and joins metals by the heat of a laser beam.
It has the advantage of more precise welding than arc or gas welding.
However, the disadvantage is that the use of powerful lasers requires a work environment that is not flexible enough to work outdoors.
gas welding
Gas welding is a method of welding using heat generated by burning acetylene gas or other gases.
Because there are no sparks as with arc welding, it has the advantage of being able to work in a variety of locations.
However, the disadvantage is that the gas heats a large area and affects welding.
Welding process by pressure welding
Pressure welding is a welding method in which sheet metal is melted by resistance heat generated by applying pressure and voltage simultaneously to overlap sheet metal.
It is mainly utilized as a welding method for automobile bodies.
Spot welding and seam welding are available, but both require extensive welding equipment.
spot welding
Spot welding is a method of joining by striking multiple currents of electrodes across the weld area like staples.
seam welding
Seam welding is a method of joining welds in a series of lines by means of roller electrodes.
Because of the high degree of confidentiality expected, it is suited for production of hulls and fuel tanks, where airtightness must be guaranteed.
Welding process by brazing
Brazing is a method of welding by heating only the joint area.
Unlike other welding techniques, the base metal is not heated.
brazing
Brazing is a brazing method employed for metals with a melting point of 450°C or higher.
Soldering, which uses solder with a low melting point to join precision equipment and electronic components, is also included in brazing.
Points to keep in mind when welding sheet metal.
Welding can join many different types of sheet metal, but the welding process must be based on the properties of the metals used.
Here are some sheet metal processing notes for each type of sheet metal that you should remember.
iron
For welding steel, it is recommended to choose low carbon steel with the lowest possible carbon content.
Since iron contains a large amount of carbon, a sudden change in temperature will alter the crystal structure inside the iron, causing cracking and a decrease in tenacity.
The options for welding steel are SS material (rolled steel for general structural purposes) and SM material (rolled steel for welded structures).
TIG welding and shielded arc welding are suitable for welding steel.
stainless steel
Since the composition of stainless steel differs greatly depending on the type, precautions and handling methods for welding differ depending on the type of stainless steel used.
When welding, as much as possible, use stainless steel that is suitable for welding, such as SUS304 and SUS316, which are classified as austenitic.
It is also safe to avoid ferritic SUS 430 and martensitic SUS 410, as they are not suitable for welding.
aluminum (Al)
While aluminum does not have a very high melting point, it has the property of forming an oxygen film with a high melting point when combined with oxygen in the air.
Therefore, there is a risk that the aluminum inside will melt too much when trying to dissolve the oxygen coating, and the entire base material will melt down.
Furthermore, its high thermal conductivity makes it less suitable for welding, as the heat from welding is easily transferred to the base metal and easily distorts it.
When welding aluminum, efficient heating of the weld zone and speedy progress of the welding operation are essential.
TIG welding is suitable for welding aluminum.
Main applications and product examples of sheet metal welding processing
The advantage of welding over mechanical joining, such as with screws, is that the joint is wider and thus less likely to break.
In addition, because metals are joined by melting each other, metal atoms bond with each other, making it possible to achieve airtight and strong joints.
Sheet metal welding processes are utilized for the following applications and products, taking advantage of these features and benefits.
- Structures such as automobiles and aircraft that require airtightness
- Piping that prevents the risk of toxic gas leaks
- Repair by welding
Welding technology is especially essential for piping that carries toxic gases that can be dangerous to the human body if leaked.
Summary
Features and advantages of sheet metal welding processes, precautions for each metal when welding, and major applications are explained.
Welding is the typical method of joining sheet metal to sheet metal and has advantages such as airtightness.
However, some types of sheet metal can be difficult to weld, requiring the selection of suitable sheet metal for welding and advanced techniques.
If you are considering manufacturing products by sheet metal welding, hiring a contractor with extensive experience in sheet metal welding will lead to satisfactory product manufacturing.
If you are considering manufacturing parts utilizing CFRP processing, please contact us.Taiga."Please make use of the following
Taiga is a free service that allows you to consult with experienced contractors.
We can efficiently proceed with the development of difficult or new parts, small-lot production, prototyping, and mass production while keeping costs low.
Receive technical proposals at Taiga