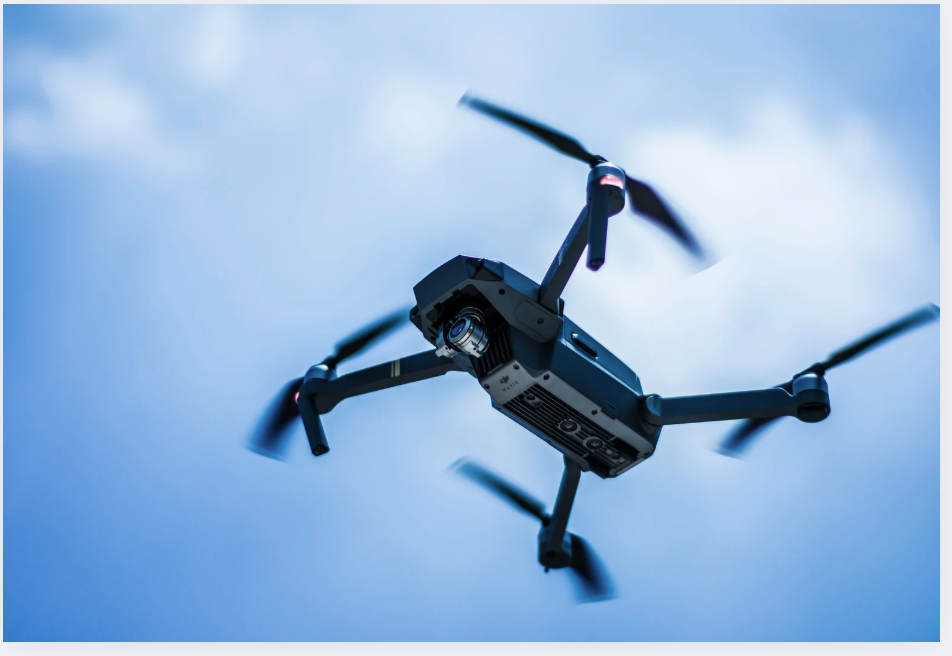
In recent years, "CFRP (carbon fiber reinforced plastic)" has been attracting attention as a material for drone manufacturing.
Nevertheless, when considering drone manufacturing using CFRP, some may have questions such as "I want to know the characteristics of CFRP and how it differs from other materials," or "I want to know how to process using CFRP.
Understanding the characteristics of CFRP materials and processing methods allows for more appropriate supplier selection and design.
Therefore, in this article, the article will explain the advantages of CFRP and its processing methods in drone manufacturing, in addition to its characteristics and comparison with other materials.
Company representatives who are considering drone manufacturing using CFRP are encouraged to refer to the end of this report.
Table of Contents
What is CFRP? Why is it attracting attention in drone manufacturing?
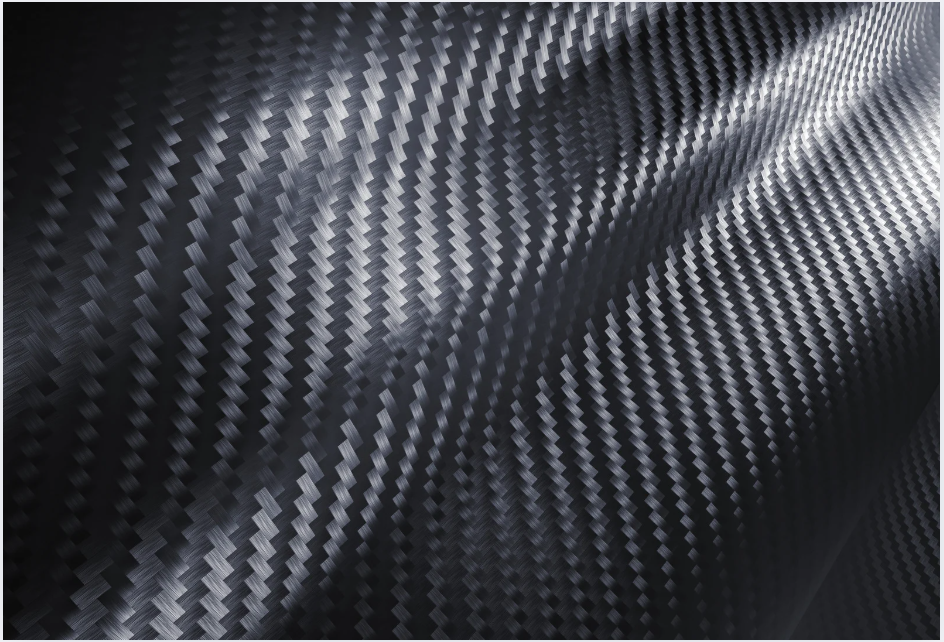
CFRP stands for "Carbon Fiber Reinforced Plastics" and is called "carbon fiber reinforced plastic" in Japanese.
First, we will explain the characteristics of CFRP and how it differs from other materials.
CFRP (Carbon Fiber Reinforced Plastic) Characteristics
CFRP is a type of composite material made by reinforcing plastic with carbon fiber.
Approximately 50-60% of the total is composed of carbon fiber, with the remainder made of epoxy or other resins.
The appeal of composites of plastics and carbon fibers is that each exhibits better properties and characteristics than the other in a single case.
For example, CFPR weighs less than 1/4 of steel because it is lighter and has a lower specific gravity than plastic.
In addition, carbon fiber alone is 10 times stronger than steel, while CFRP is lightweight but has the same or higher rigidity than steel.
Comparison with aluminum and resin materials
Comparing aluminum and CFRP, the weight of CFRP is about one-half that of aluminum, and its vibration damping ratio is about 3 to 4 times that of aluminum.
It is lighter than aluminum, yet offers high vibration suppression and higher fatigue resistance than metals, including aluminum.
In addition, since CFPR is made of carbon fiber in a honeycomb structure, it is not easily degraded or damaged by fatigue like metal.
Although it depends on the orientation of the carbon fiber and the type of resin, thermal expansion does not occur as it does with metals.
Since it does not corrode like metal, it is also suitable for components such as precision equipment, where dimensional changes due to temperature change and deterioration of properties due to corrosion are not allowed.
Comparing resin materials and CFRP, resin is an equidirectional material, whereas CFRP is an anisotropic material combining fiber and resin.
This makes it possible to change the stiffness by changing the orientation and direction of the fibers and the type of material, and to create components with shapes that cannot be fabricated with metals or resins.
Advantages of Using CFRP Processing in Drone Manufacturing
The properties of the CFR also make it suitable as a drone component.
This section describes the benefits of using CFPR in drone manufacturing.
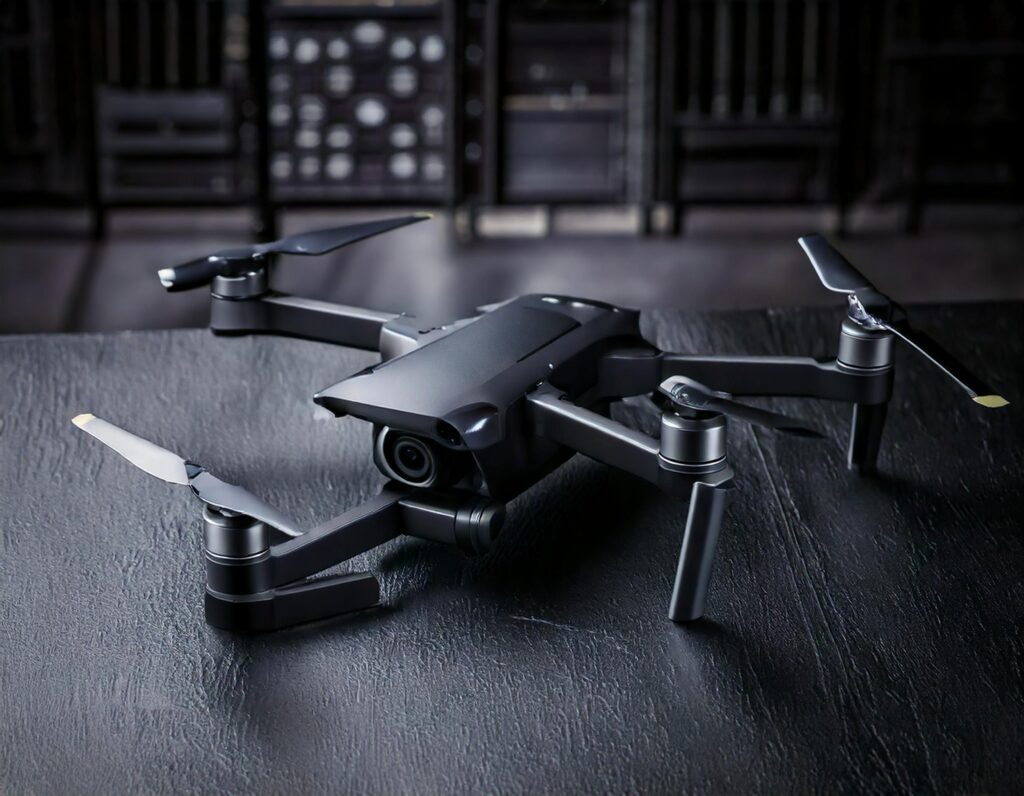
Extended flight time due to weight reduction
The specific gravity of CFRP is around 1.8, about 1/4 the weight of steel, making it possible to reduce the drone's weight.
The advantage of lighter weight is that it increases fuel efficiency and flight efficiency, leading to longer drone flight time.
Improved operability
CFRP can be used to increase the rigidity of drone components.
It can provide strength against tension and torsion, which also improves the operability of the drone.
Increased durability
CFRP has higher strength and modulus of elasticity than metals such as steel.
This allows for improvements in both drone weight and durability, making it possible to produce drones that can fly in a variety of environments.
Main processing methods when employing CFRP in drones
When CFRP is used as a drone material, there are two main processing methods: "cutting" and "3D printing.
This section describes the characteristics of cutting and 3D printing.
Machining
Cutting is a method of processing materials such as resin and metal into the required shape while using cutting tools.
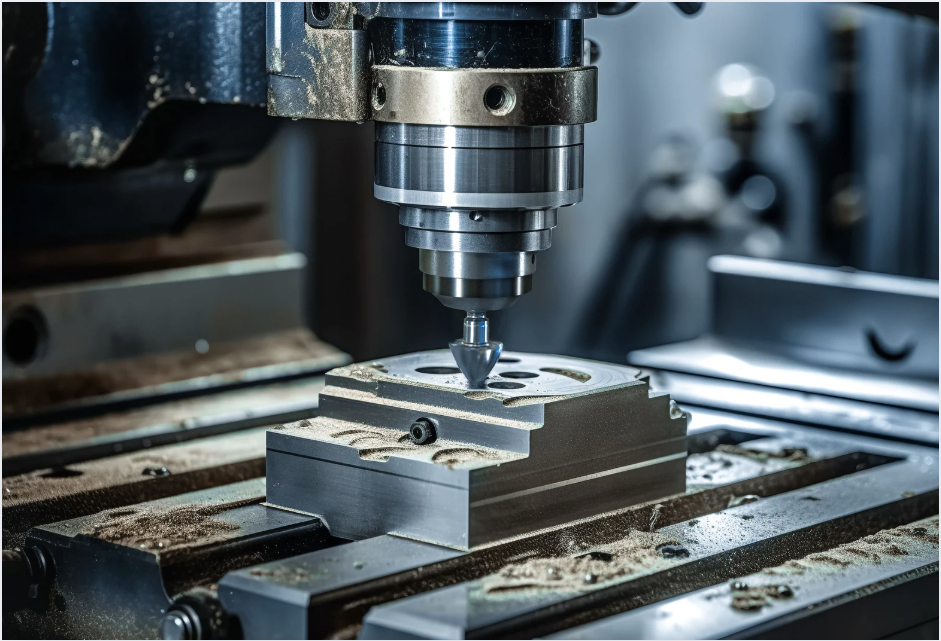
Carbon materials, including CFRP, can also be processed by cutting.
However, cutting CFRP is more difficult.
When considering CFRP cutting, it is necessary to select a processor with a proven track record and technical capabilities.
3D printing
3D printers can also process many materials, including CFRP.
The modeling can be freely changed to some extent according to the characteristics of CFRP, such as model strength, elasticity, and cost, which are important points to be emphasized.
When considering a CFRP-compatible 3D printer, choose the 3D printer you will use based on the equipment and cost considerations.
Examples of CFRP parts commonly used in drone manufacturing
The following is a step-by-step explanation of the parts for which CFRP is often used in drone manufacturing.
frame
CFRP is often used for the frame parts of drones, from those of general drones to those for competitions.
Arm (Pipe)
CFRP is used in a wide variety of drone manufacturing, from small drones for competition and aerial photography to large drones for agriculture and aerial spraying.
Some vendors may have pre-defined dimensions that they can accommodate.
propeller
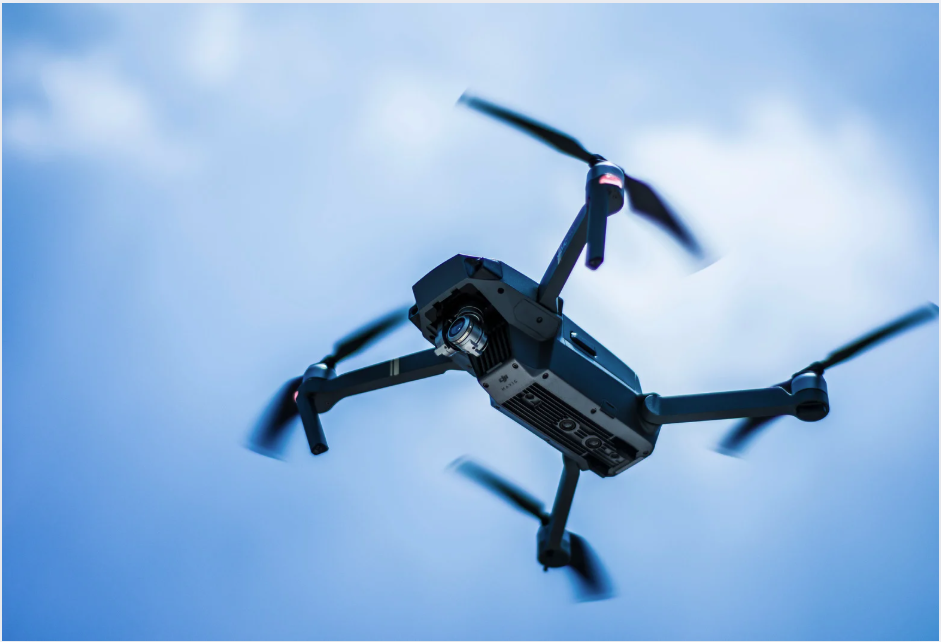
CFRP is also used in many drone propellers.
Since the propellers are quieter in flight than propellers made of other materials, they are ideal for manufacturing drones that require quietness, such as those used for filming.
Another advantage is that the texture of CFRP is used to create a stylish-looking propeller.
Points to Note in CFRP Processing in Drone Manufacturing
When CFRP is used in the manufacture of drone parts, there are various precautions that must be taken during processing.
The following is a step-by-step explanation of the key points to remember for successful drone manufacturing with CFRP.
High degree of cutting difficulty requires skill of the technician.
CFRP is lightweight and durable, and its stiffness can be changed by adjustment.
However, the cutting process is more difficult because the fiber layer tends to delaminate easily and takes time.
If you are considering CFRP drone manufacturing by cutting, you need to choose a supplier with high technology and experience.
Easy tool wear
CFRP has the disadvantage of tool wear during cutting.
This is because the machining process generates tiny carbon particles, which scrape the tool.
Some contractors are not able to handle the cutting process because it can cause the life of the cutting tools to be reduced.
Measures against dust generated during processing
Cutting of CFRP requires countermeasures against dust generated during processing.
The dust generated poses the following risks of adverse effects on the human body
- Itching on skin
- Inhalation may damage the lungs.
- Rubbing while adhering to hands can cause injury.
In addition, dust can get into bearing parts and other parts of the machine, which can act like a file and cause wear and deterioration of the machine.
Keep in mind that CFRP processing requires adequate dust control.
Summary
In this article, we explained the characteristics of CFRP, comparison with other materials, advantages of CFRP in drone manufacturing, and points to note when processing CFRP.
CFRP is often used for drone components due to its advantages such as high strength and light weight.
However, because it is a difficult-to-machine material, machining requires skill.
When considering the manufacture of drone parts that employ CFRP, be sure to ask a reliable supplier with technical capabilities and a proven track record.
If you are considering manufacturing parts utilizing CFRP processing, please contact us.Taiga."Please make use of the following
Taiga is a free service that allows you to consult with experienced contractors.
We can efficiently proceed with the development of difficult or new parts, small-lot production, prototyping, and mass production while keeping costs low.
Register with Taiga