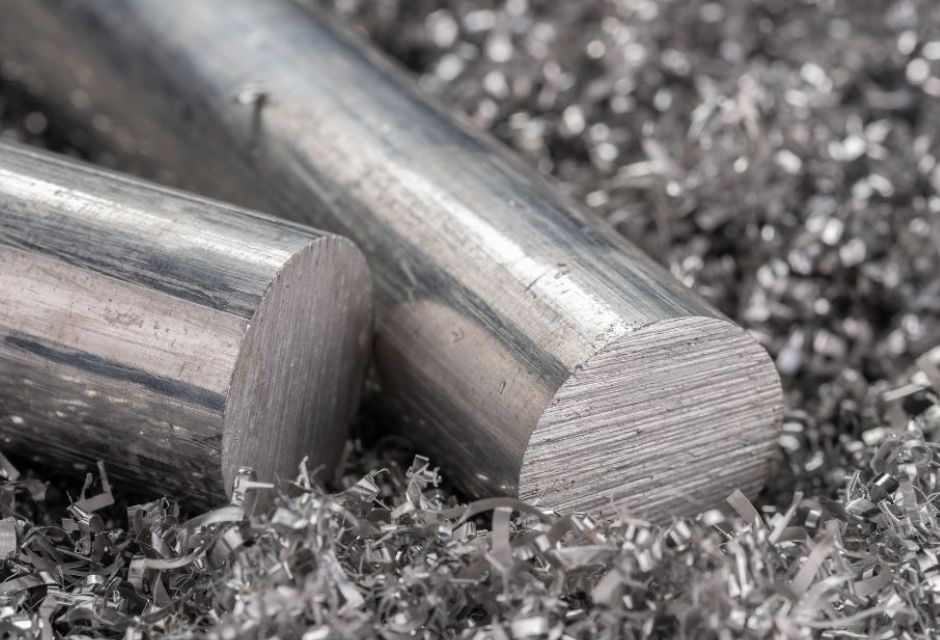
Aluminum is one of the easiest metals to process and is often used as a cutting material.
However, in order to maintain quality in the cutting process, one must understand the characteristics of aluminum and the precautions to be taken when machining.
In this article, in addition to the reasons why aluminum is suitable for cutting, we will explain how to cut aluminum, what to look out for, and what to do to ensure success.
For more information about Taiga, click here.Table of Contents
Six Advantages of Using Aluminum for Cutting
Aluminum is often used as a cutting material for a variety of reasons. Below we look at six advantages of choosing aluminum as a cutting material.
Aluminum is a good material for cutting
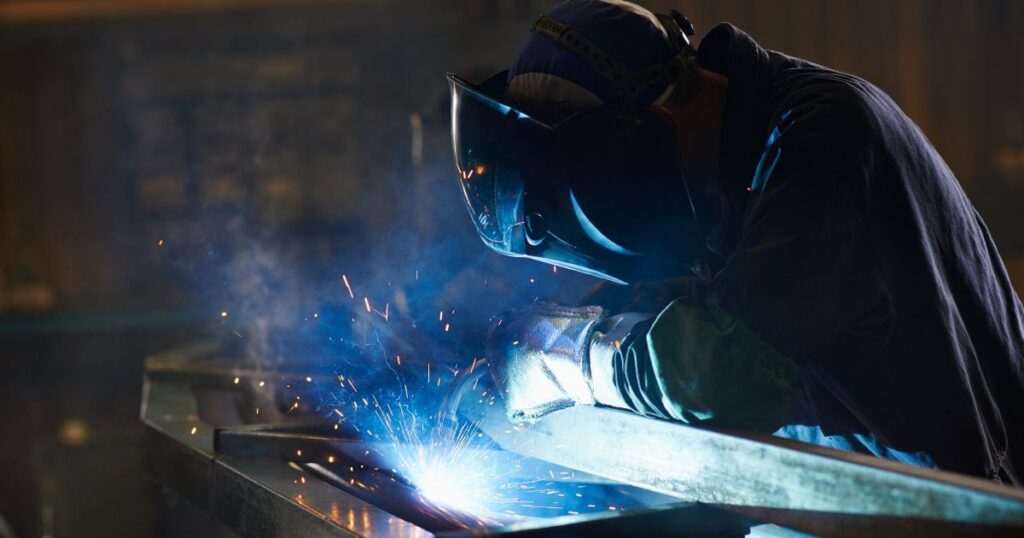
Aluminum is a metal that is more compatible with cutting processes and easier to process than other metals.
Let's compare the machinability index rate, a measure of a metal's resistance to cutting, between aluminum and other metals.
- Aluminum: 240 to 140
- Copper alloy: 100 to 70
- Steel: 85 to 50
- Cast iron: 90 to 50
The more *values, the easier it is to cut.
Aluminum also has a low melting point and is easy to melt, making it suitable for casting and joining. Various shapes can be produced by combining cutting and other processing methods.
High strength, suitable for light weight
Aluminum is a strong metal by nature.
Strength can be further increased by alloying it with other metals such as magnesium or manganese, or by heat treatment.
In addition, aluminum itself is lightweight, making it easy to handle and effective in reducing product weight. Compared to iron and copper, for example, aluminum weighs only about one-third as much.
Large distribution volume and excellent cost performance
Aluminum is the most widely distributed and inexpensive of the metals available.
It is also highly processable, making it easy to keep processing costs low, making it an excellent cost-performance material.
Resistant to corrosion and rust, with little or no toxicity
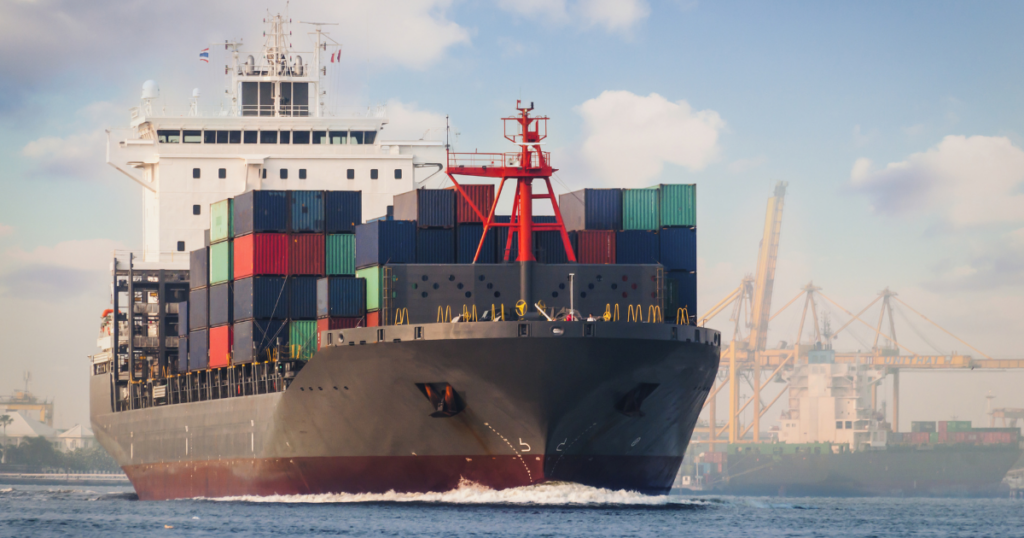
Aluminum has the characteristic of forming an oxide film on its surface in air, which makes it resistant to corrosion and rust.
Therefore, it would be suitable as a material for automobiles, ships, and buildings used outdoors.
In addition, aluminum is an odorless metal with almost no toxicity and is unlikely to cause adverse effects on the human body.
As a result, they are used in a variety of applications, including food and pharmaceutical packaging, beverage cans, medical equipment, and household vessels.
However, A2000 series aluminum contains a large amount of copper (Cu) to improve strength.
Copper is susceptible to oxidation, so surface treatment with anodizing is necessary to improve corrosion resistance.
Can be used as a non-magnetic conductor
Aluminum is not magnetic, making it a suitable material for precision machinery and other components.
The electrical conductivity of aluminum is about 60% of copper, but its specific gravity is about one-third that of copper, so it can conduct about twice as much current as copper of the same weight.
Therefore, it can be used as a conductor for electric wires, etc.
Excellent thermal conductivity and reflectivity
Although inferior to copper and silver, aluminum also conducts heat easily. The thermal conductivity of aluminum is about twice that of brass and about three times that of iron and stainless steel. Its ability to easily heat and cool can be utilized in a wide range of products.
Mirror-polished aluminum also has a higher reflectivity than other metals.
The purer the aluminum, the higher the reflectance.
Because it can reflect infrared rays, ultraviolet rays, electromagnetic waves, and various heat rays, it is often used as a reflector for heating and lighting equipment.
In addition, high reflectivity means a beautiful surface finish after processing.
Features of Aluminum Cutting|Is aluminum machining difficult?
Although aluminum is suited for cutting, the process may not proceed well without an understanding of aluminum's properties and characteristics.
Since the melting point of aluminum is lower than that of other metals at 660°C, the friction generated during the cutting process can melt the material, causing it to arrive at the cutting edge and harden.
Note that if aluminum adheres to the rake surface or cutting edge of the tool and hardens, the machined surface will become jagged and machining accuracy will be greatly reduced.
It is also important to note that its high thermal conductivity makes it susceptible to distortion when heated. In addition, aluminum tends to stretch more easily than other metals.
When aluminum is stretched during cutting, burrs are likely to occur. Burrs can cause a reduction in product quality, and also cause time-consuming deburring in the post-processing steps after the cutting process.
Thus, cutting aluminum is not an easy task.
It is necessary to pay attention to various aspects and select the appropriate processor to ensure a satisfactory processed product.
Types of Aluminum Used in Cutting Processes|Which is Easier to Cut?
Since there are many different types of aluminum, it is important to know the characteristics of each and choose the right material.
Below is a description of the characteristics of each type of aluminum used in the cutting process.
1000 series
Series 1000 is pure aluminum with a purity of 99% or higher.
Due to its high purity, it has high electrical and thermal conductivity and excellent workability.
On the other hand, it is less strong than aluminum alloys.
2000 series
Series 2000 is an aluminum alloy containing copper (Cu).
While strong and easy to cut, copper is not highly resistant to corrosion due to its tendency to oxidize.
Generally, anodizing is performed to improve corrosion resistance before use.
3000 series
Series 3000 is an aluminum alloy containing manganese (Mn). It has improved strength while maintaining the corrosion resistance of pure aluminum.
Although it is often used for aluminum cans and building materials due to its good formability, it is not often used for cutting materials.
4000 series
Series 4000 is an aluminum alloy with improved heat resistance and wear resistance due to the addition of heat-resistant silicon (Si).
Because of its low coefficient of thermal expansion, it is also used as a material for forging pistons, but is rarely used as a cutting material.
5000 series
Series 5000 is an aluminum alloy containing magnesium (Mg).
Magnesium improves corrosion resistance and strength and has excellent machinability, so it is widely used as a cutting material.
6000 series
Series 6000 is an aluminum alloy containing silicon and magnesium.
They are characterized by improved strength and corrosion resistance compared to Series 5000. Some of them have copper added to increase the strength to about that of steel SS material (general structural rolled steel).
7000 series
Series 7000 is an aluminum alloy containing zinc (Zn) and magnesium.
Copper-added A7075 is called superduralumin and is the strongest of the aluminum alloys.
Cautions in Cutting Aluminum
Although aluminum is a highly machinable metal, it should be noted that depending on the shape of the workpiece and the type of aluminum, there is a possibility of welding to the cutting tool during machining.
Welding can cause component cutting edges and must be prevented.
In addition, aluminum alloys have a high coefficient of linear expansion among metal materials and expand easily with heat.
Therefore, the heat generated during the cutting process can change the dimensions.
When cutting thin shapes, heat and residual stress during machining may cause deformation such as distortion and warping.
Thus, in cutting aluminum, many things need to be taken into account.
4 Tips for Successful Aluminum Cutting
Below are four tips for successful aluminum cutting.
Cutting at high speed
Working at a faster cutting speed reduces welding of the components.
In addition, cutting resistance is lowered and the cutting surface becomes smoother.
Use sharp blades with low cutting resistance
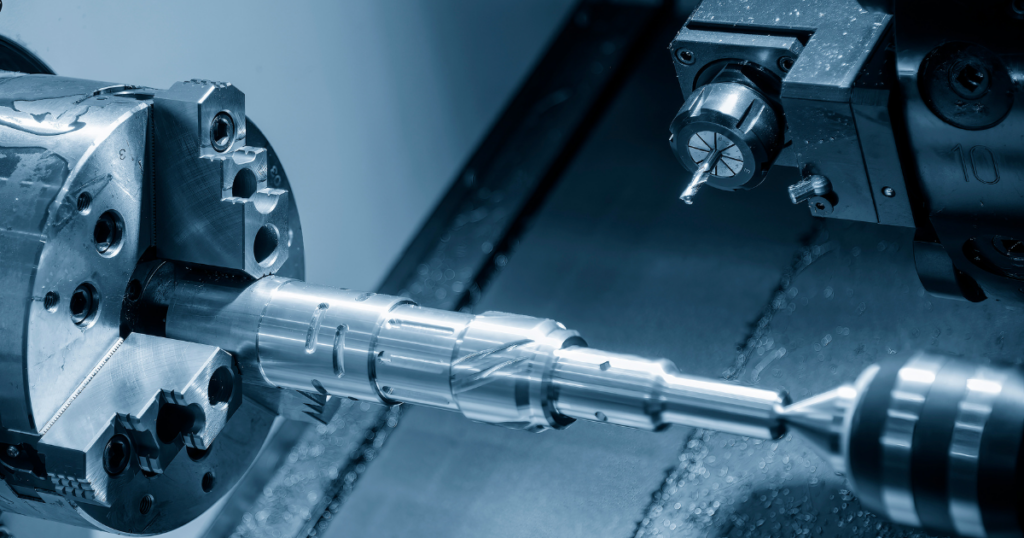
Use sharply shaped tools for cutting aluminum.
Sharp cutting edges provide less cutting resistance, resulting in a smoother sharpened surface.
Remove chips frequently.
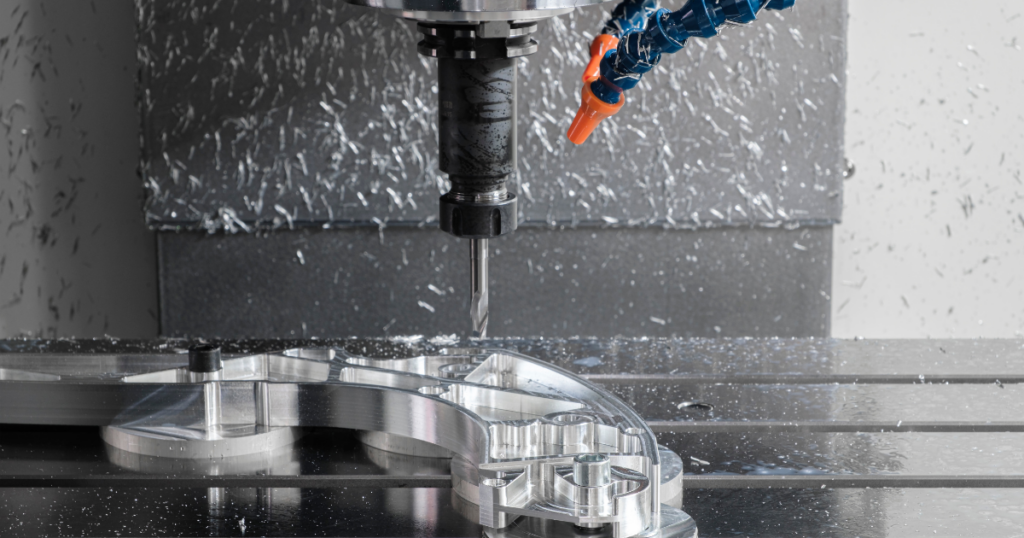
During processing, frequently remove chips that may cause surface scratches or welding.
Especially when making holes by cutting, chips tend to accumulate in the hole, so adjust the amount of cutting at one time and remove them frequently.
Use cutting oil (coolant)
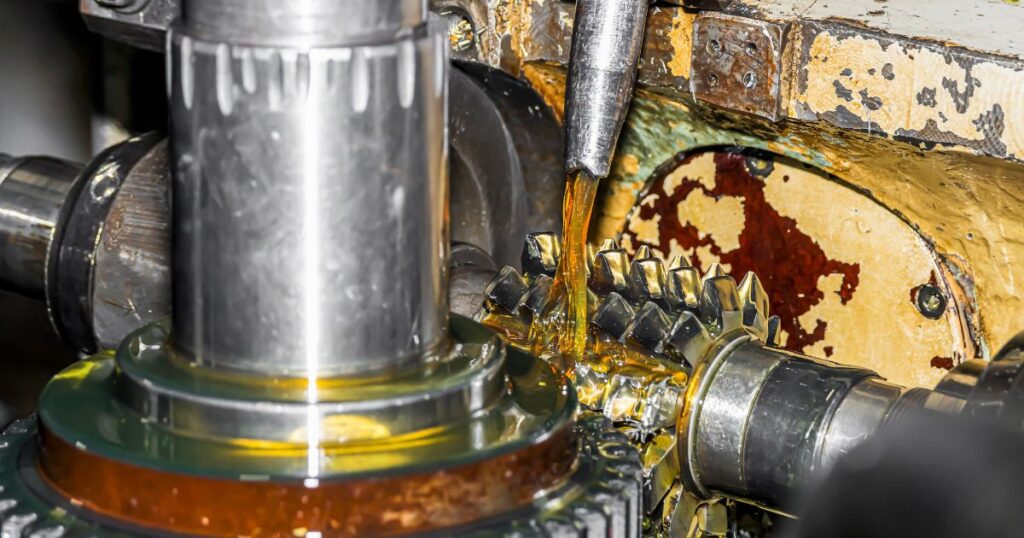
Aluminum chips, with their low specific gravity, float easily in cutting oil, reducing the risk of welding.
It is also important to use cutting fluid to prevent chips from adhering to cutting tools.
Summary
An overview of aluminum cutting, materials, processing methods, and precautions were explained.
While aluminum is an easy material to cut, it also requires processing to suit the material and to prevent welding.
Choose the right fabricator to achieve high quality aluminum product manufacturing.
Aluminum is a good choice if you are considering manufacturing parts utilizing the cutting process.Taiga."Taiga is a free service that allows you to consult with experienced contractors.
We can efficiently proceed with the development of difficult or new parts, small-lot production, prototyping, and mass production while keeping costs low.
For more information about Taiga, click here.