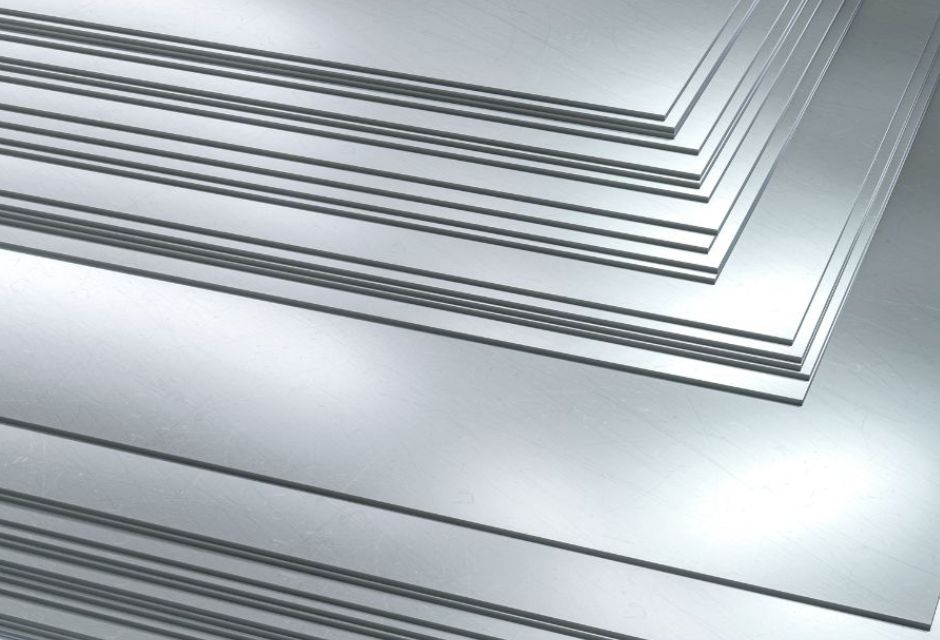
Aluminum is used in the manufacture of a wide variety of products because it is a lightweight and strong material.
However, aluminum is also a difficult metal to process into sheet metal due to its characteristics.
Therefore, it is important to process aluminum using appropriate methods and procedures based on its characteristics.
This article describes the features, methods, and procedures of aluminum sheet metal fabrication.
Receive technical proposals at TaigaTable of Contents
Characteristics of Aluminum Used in Sheet Metal Working
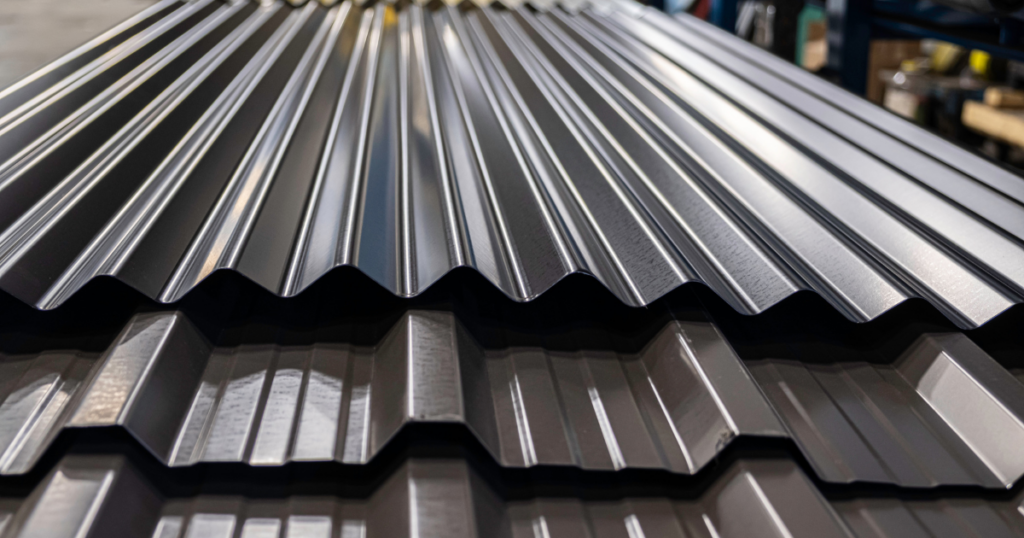
Aluminum has the following characteristics
- Lighter than other metals
- High strength
- Adding other metals will increase strength.
- Resistant to rust and corrosion
- Surface treatment (anodizing) further increases corrosion resistance
- High flexibility and low melting point, making it easy to process
- Excellent heat and electricity tradition
Aluminum's lightness and strength make it possible to reduce the weight of various products.
The automotive industry, in particular, is promoting the development of products that switch from steel to aluminum for parts to reduce product weight and address environmental issues.
In other industrial equipment sectors, we can expect to see a shift from steel to aluminum components.
Aluminum is also used in a variety of other products, including
- Covers and frames for mechanical and electronic components
- Furniture (office desks, tables, storage racks, etc.)
- Housing facilities (sinks, sashes, mailboxes, etc.)
- Parts for vehicles (airplanes, bullet trains, etc.)
Types of aluminum used for sheet metal working
Aluminum can be broadly classified into "pure aluminum" and "alloy aluminum.
Pure aluminum is aluminum with a purity of 99.9%.
Alloy aluminum, on the other hand, refers to aluminum to which other metals have been added.
Aluminum is described and classified as "Axx series" according to the metal to which it is added.
Please refer to the following list of additives and characteristics of each type of aluminum.
Aluminum Types | addition | feature |
A1000 series | nashi (Pyrus pyrifolia, esp. var. culta) | High workability and low strength |
A2000 series | Copper and magnesium | A2017 and A2024 are also called "duralumin" and "super duralumin"; they are as strong as steel and have slightly lower corrosion resistance. |
A3000 series | manganese (Mn) | ・Used as a material for aluminum cans・High strength・High corrosion resistance |
A4000 series | silicon | Improved heat and abrasion resistance |
A5000 series | magnesium (Mg) | High corrosion resistance, excellent workability, high strength |
A6000 series | Magnesium and silicon | ・High strength, high corrosion resistance, used in materials for joint parts (bolts, nuts, etc.), ships, vehicles, etc. |
Three Reasons Why Sheet Metal Working of Aluminum is Difficult
Aluminum is one of the most difficult metals to process into sheet metal.
The following is a step-by-step explanation of the reasons why sheet metal working of aluminum is difficult.
Soft material, easily scratched and dented
Aluminum is softer than other metals.
Below is a comparison of aluminum and other metals in terms of Brinell hardness (unit: HB), a measure of the hardness of metals.
- Aluminum: 15HB
- Copper: 35HB
- Iron: 112HB
- Stainless steel (iron + chrome + nickel): 1250HB
The lower the value for Brinell hardness, the softer and the higher the value, the harder.
The values will show how soft aluminum is compared to other metals.
Aluminum, which is the softest of metals, is easily scratched or dented, so it must be handled with great care during processing, transportation, and storage.
Difficult to weld process
Aluminum also has a lower melting point than other metals.
- Aluminum: 660 °C
- Copper: 1084.5 °C
- Iron: 1536 °C
- Stainless steel (iron + chrome + nickel): 1400-1500°C
If the melting point is low, welding will cause the aluminum itself to melt, making processing difficult.
Also, because of its high thermal conductivity, thermal deformation may occur during processing, or the melted material may not melt properly.
The following techniques will be required when welding aluminum
- Heat input control to aluminum
- Reduced welding time
- Creating a factory environment
Aluminum's low melting point and high thermal conductivity make it suitable for casting processes but unsuitable for welding.
Low strength, easily damaged
Compared to other metals, aluminum is characterized by low strength and low impact resistance.
If aluminum is dropped or bumped, it is often scratched or damaged. Care should be taken during processing and handling.
However, aluminum can be strengthened by adding other metals.
Because of aluminum's tendency to bond with other elements, various types of aluminum alloys exist.
For example, there is "Geraldine" in the A2000 series aluminum, which is aluminum with copper and magnesium added.
Duralumin is highly resistant to deformation and flame retardant, so it is used as a material for duralumin cases, which are used to transport precision instruments and cash.
Super Geraldine," also an A2000 series aluminum, is a metal utilized in industrial products.
Aluminum Sheet Metal Processing Methods
The main processing methods for aluminum sheet metal are as follows
- Bending Process
- Cutting Process
- Drilling Process
Bending is generally used, but other processing methods are also used depending on the shape and purpose of the workpiece.
The characteristics of each processing method are explained.
Bending Process
Bending is a method of processing aluminum sheet metal by bending it into various shapes.
There are "roll bending" and "bender bending (press bending)" depending on the processing method.
roll bending
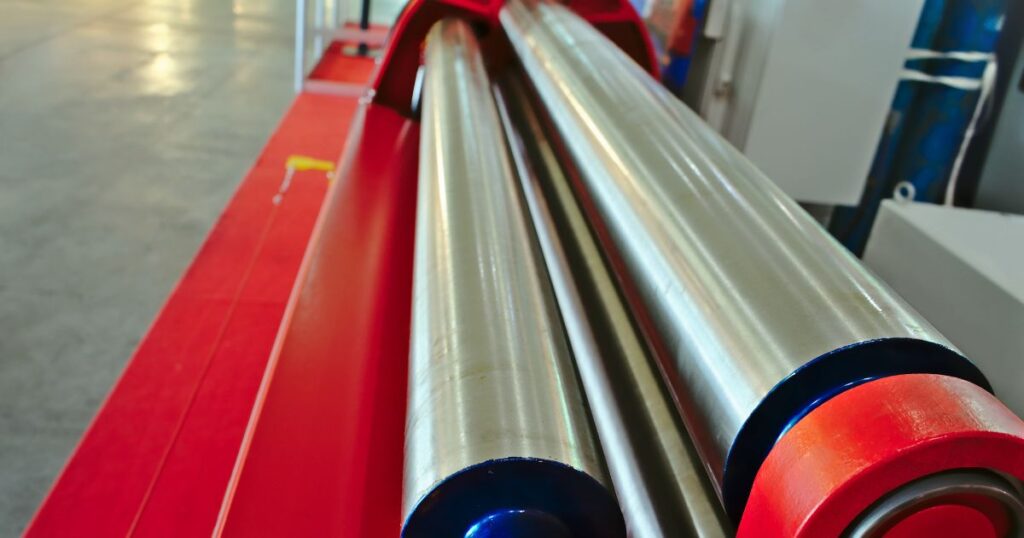
Roll bending is a processing method of bending aluminum sheet metal through a special machine.
It is used to produce circular cylindrical workpieces.
By changing the diameter of the roll, the diameter of the bend can be changed.
However, it should be noted that cracks are more likely to occur when the sutra is small.
Bender bending (press bending)
Bender bending (press bending) is a processing method in which an aluminum sheet material is placed between a die and a punch and bent by sandwiching it.
A wide range of shapes can be processed, including V-bending, L-bending, and Z-bending.
Vendor bending has the advantage of high production speed and can be used for mass production.
However, in some cases, know-how is required, such as pressure calculations and selection of the most suitable mold.
Cutting Process
Cutting is a processing method in which aluminum sheet metal is cut with a tool.
The following tools are mainly used for cutting aluminum
- Plastic Cutter
- disk grinder
- Electric Jigsaw
Aluminum can be cut more easily than other metals because of its lightweight and soft nature.
However, the cut cross section is sharp, so care should be taken.
In addition, because of the high strength of aluminum alloys, tools must be selected according to the type of aluminum to ensure safe and proper cutting processes.
Drilling Process
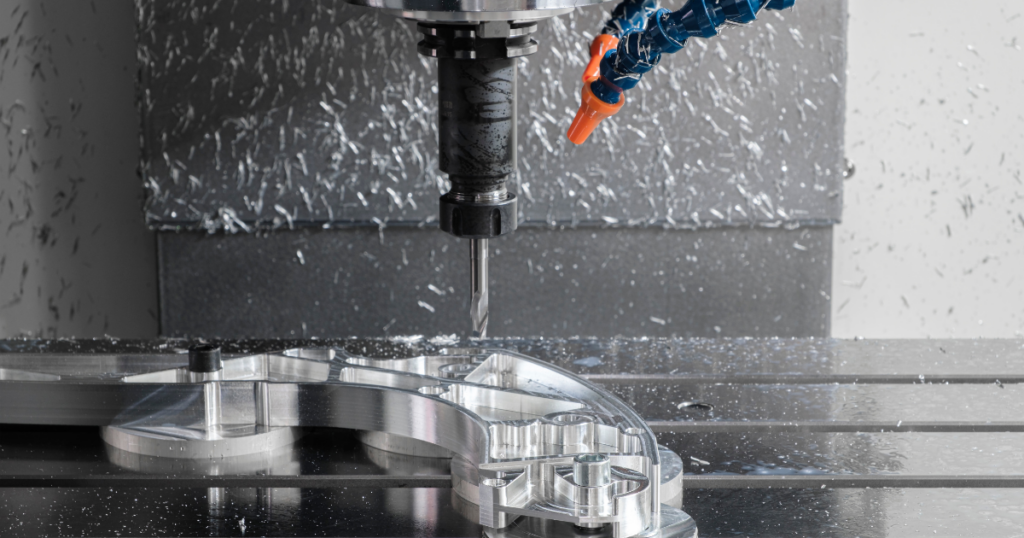
Drilling is a processing method of drilling holes in aluminum sheet metal.
The following tools are used for machining
- electric drill
- center punch
- (iron) hammer
When drilling, burrs may occur and chips may be welded to the blade.
It will be necessary to prevent welding by increasing the speed of the drill, for example.
Aluminum Sheet Metal Processing Procedures
The processing procedure for aluminum sheet metal is as follows
- Design the workpiece.
- Procure aluminum sheet metal to be processed
- Processing by machine (either cutting, drilling, or bending)
- Combine and weld workpieces
- Perform finishing such as deburring
- Perform assembly
- Warehousing finished products
- Ship and deliver as needed.
The ability to request all steps of the fabrication procedure depends on the aluminum sheet metal processor.
Some companies process aluminum sheet metal but ask other companies to do the assembly, while others offer the entire process from machining to assembly, warehousing and delivery.
When choosing a processor, carefully check which processes can be requested.
Summary
In this article, we have explained the characteristics of each type of aluminum, as well as processing methods and procedures, along with the reasons why sheet metal processing of aluminum is difficult.
Aluminum is used as a material for a wide range of products, from daily necessities to industrial parts.
Sheet metal working of aluminum is difficult and requires high technology.
When requesting processing, choose a supplier that offers appropriate processing methods depending on the type of aluminum and the product to be produced.
If you are considering manufacturing parts utilizing aluminum sheet metal fabrication, please contact us.Taiga."Taiga is a free service that allows you to consult with experienced contractors.
We can efficiently proceed with the development of difficult or new parts, small-lot production, prototyping, and mass production while keeping costs low.
Receive technical proposals at Taiga