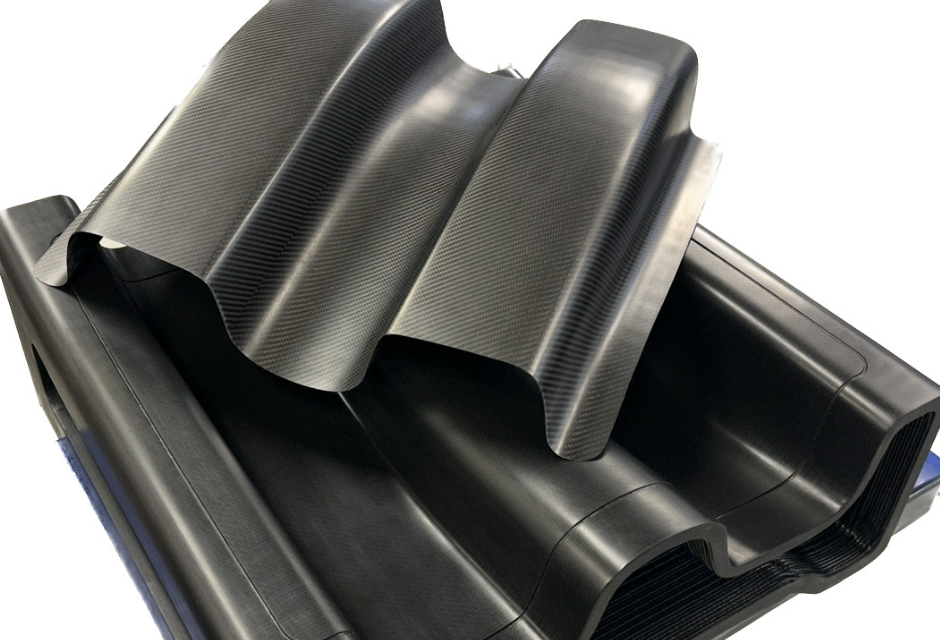
Autoclave molding is one of the processing and molding techniques for carbon.
While autoclave molding has advantages, it also has disadvantages, and care must be taken during processing.
In this article, we will explain the advantages and disadvantages of autoclave molding in addition to what it is.
Please refer to the autoclave molding procedure as well.
Table of Contents
What is autoclave molding?
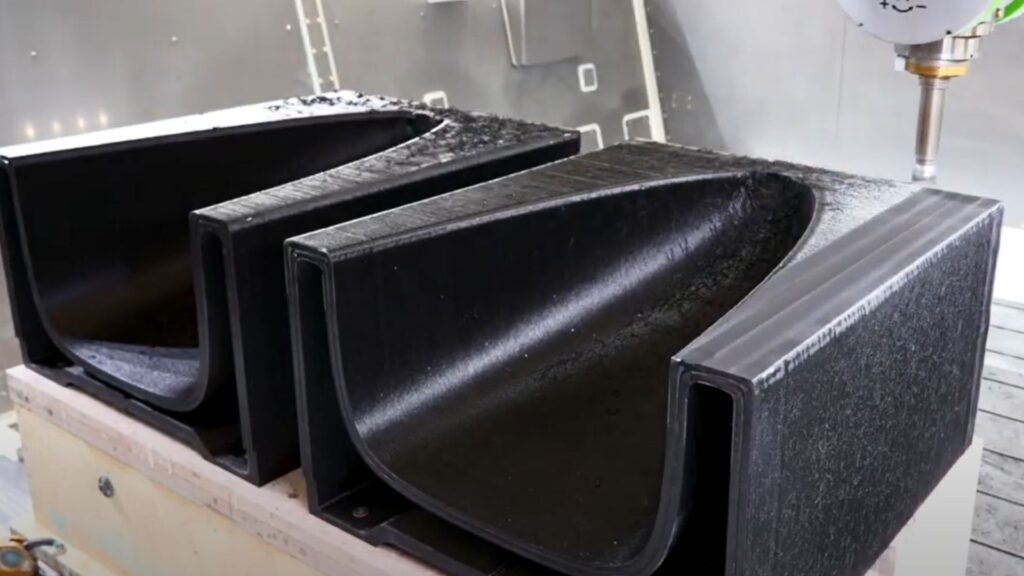
Autoclave molding is a method of molding using a pressure vessel called an autoclave.
When pressure is applied to a container with material in it, the remaining air inside is released and the material is formed.
By programming pressure and temperature to suit the product, even difficult-to-process materials can be generated appropriately.
In addition, autoclave molding can be used to mold a variety of materials, including the following
- prepreg
- CFRP
- CFRTP
- liquid molding
Advantages of Autoclave Molding
The advantages of autoclave molding are explained.
High degree of freedom in design
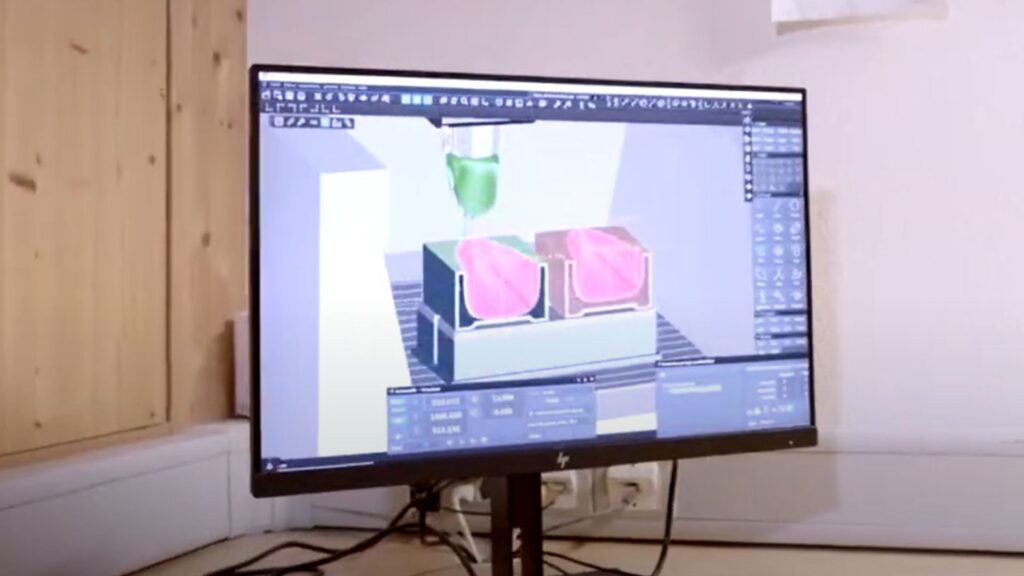
Autoclave molding is characterized by a high degree of freedom in design.
A wide range of product manufacturing can be realized, including large and small parts as well as parts with complex shapes.
High quality molding is possible
Autoclave molding is a molding method that applies pressure during molding.
Since the applied pressure is usually as high as 0.3 MPa or 2 MPa at the maximum, the generation of air bubbles (voids) can be suppressed.
In addition, since compressed air is used to pressurize the material, pressure is applied evenly to the material, enabling high-quality, high-precision molding.
When carbon fiber, such as carbon, is used as a material, the properties can be maximized, resulting in more precise molding.
Molding dies are inexpensive and suitable for small-lot production
Molds for autoclave molding are less expensive to produce than molds used for other molding methods such as press and injection molding.
Since the cost of die fabrication is reduced, it is suitable for mass production as well as for small-lot production and prototype manufacturing.
Disadvantages of autoclave molding
While autoclave molding has advantages, it also has disadvantages.
The disadvantages of autoclave molding that should be remembered are described in turn.
Not suitable for mass production because of the time required for molding.
Autoclave molding is a method of compressing and forming by feeding air into a pressure vessel and heating the air. Therefore, it takes about 1-8 hours to reach the molding pressure and temperature.
Because of the time required for molding, it is not suitable for mass production.
However, another method to reduce the heating time for autoclave molding is to heat the material and mold directly.
Costly to install equipment
Although autoclave molding is less expensive to produce molds, the cost of the molding processor itself is very expensive.
Because of the initial cost of installing equipment, it will be more costly than molding methods that do not require expensive equipment.
However, if the molded product is small, there is a method to introduce a small model autoclave with relatively low installation cost.
Autoclave molding procedure
Specific procedures for autoclave molding are explained.
Creation of molds for molding
First, we design and fabricate the mold to which the material prepreg is attached.
Autoclave molds for molding have the same role as molds used in casting and injection molding.
A wide range of materials are employed in molds, depending on the product used, as follows
Mold Materials | feature |
Metal mold (aluminum alloy, steel, etc.) | The product can be used from prototype to mass production, has high durability, is relatively easy to order, has high heat resistance and can withstand CFRTP molding, and has a wide range of options for outsourcing. |
Pearl board (plasterboard) type | The low coefficient of thermal expansion allows for greater molding precision, and the brittleness of the molds means that they have a short lifespan. |
FRP type | ・Typing and small-lot production ・Inverted molds can be made inexpensively from product and master molds ・High thermal expansion coefficient, causing thermal shrinkage from the mold making stage ・Short mold life due to thermal degradation ・Hand lay-up FRP molding skills are required |
CFRP type | Molds that overcome the weaknesses and disadvantages of FRP molds |
In order to ensure smooth demolding after molding, the surface of the mold is coated with a mold release agent.
The following types of mold release agents should be used depending on the specifications required for the molded product.
- Baked onto the mold surface for repeated use
- Every time application type where the mold release agent itself is broken.
- A sheet is attached to the surface of the mold.
Cutting of prepreg
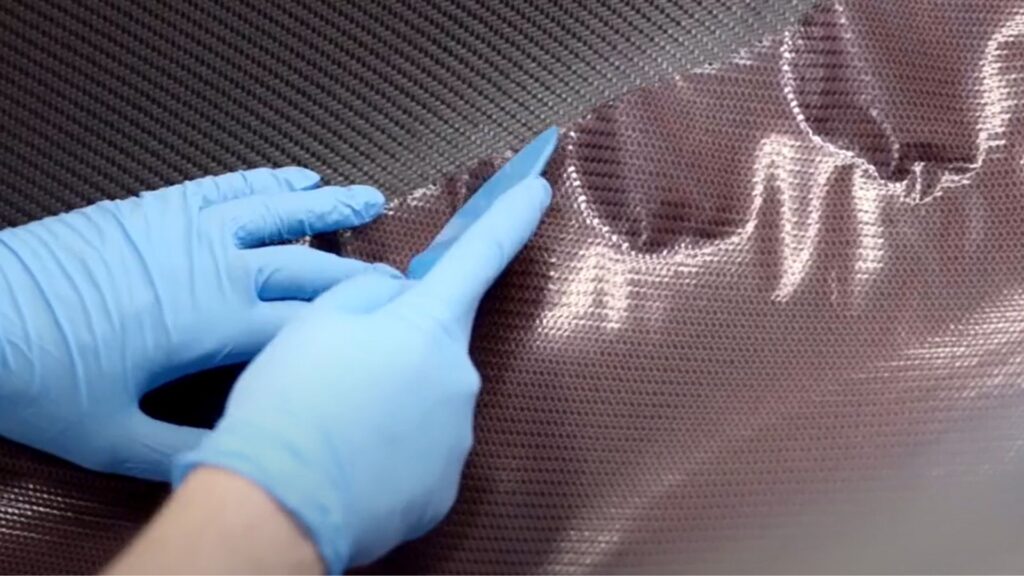
Next, the prepreg is cut.
Prepreg comes in sheet form, with a typical thickness of 100 µm to 250 µm.
Prepregs are cut using a cutting machine to maintain dimensional accuracy and quality of the cut surface.
However, cutting machines are expensive, so for prototypes or small production runs, cutting may be done by hand.
Laminating prepreg
Cut prepreg is attached to the mold and laminated.
Unlike press forming of metal sheets, autoclave forming allows partial stacking of prepreg sheets to partially vary the plate pressure of the molded product to reinforce or increase the rigidity of the structure.
The carbon fibers are arranged so that they line up in the direction in which the material's properties, such as strength and rigidity, are desired to be expressed, and the stacking design is performed while considering the combination and stacking order.
The key to stacking is not to simply stack the prepreg sheets in a flat shape, but to stack them along the mold. If there are curved surfaces, etc., ingenuity will be required at the point of cutting.
Once lamination is complete, the prepreg is sealed with an airtight plastic film for pressurization on top of the prepreg.
bagging
Bagging is the process of pulling out the air contained between the sealant and the mold.
If air remains in the prepreg during curing, it can cause voids to form inside the molded product.
Vacuuming is performed to ensure that no air remains between the layers of prepreg, the mold, and the sealant.
Curing by pressurization and heating
The prepreg is placed in a pressure vessel (autoclave) and pressurized and heated to cure.
Although it depends on the type and shape of prepreg used, autoclave molding generally takes several hours to complete.
If the temperature of the molded product is unevenly distributed inside the autoclave, deformation may occur.
It takes a long time to heat a molded product while controlling the temperature so that the entire product rises uniformly.
remove from a mold
After molding is complete, remove the molded product from the mold.
Although the surface of the mold is treated with a mold release agent, it is still attached by adhesive force.
To prevent damage, do not attempt to remove it by force.
finishing workmanship
The following finishing and post-processing operations are performed on products removed from the mold as required.
- Trimming of outer circumference
- Smooth end faces
- Surface Treatment
- Drilling, etc.
Summary
The overview of autoclave molding, its advantages and disadvantages, and the procedures of the molding process are explained.
Although autoclave molding uses a die, it is a processing method suitable for prototyping and small-volume production.
However, it is important to take into account the disadvantages such as the time required for molding and the higher initial cost.
In order to achieve satisfactory autoclave molding, it is important to select a processor with the technology and experience appropriate for the scene and product shape you wish to produce.
If you are considering manufacturing parts utilizing autoclave molding, please contact us.Taiga."Taiga is a free service that allows you to consult with experienced contractors.
We can efficiently proceed with the development of difficult or new parts, small-lot production, prototyping, and mass production while keeping costs low.
For more information about Taiga, click here.