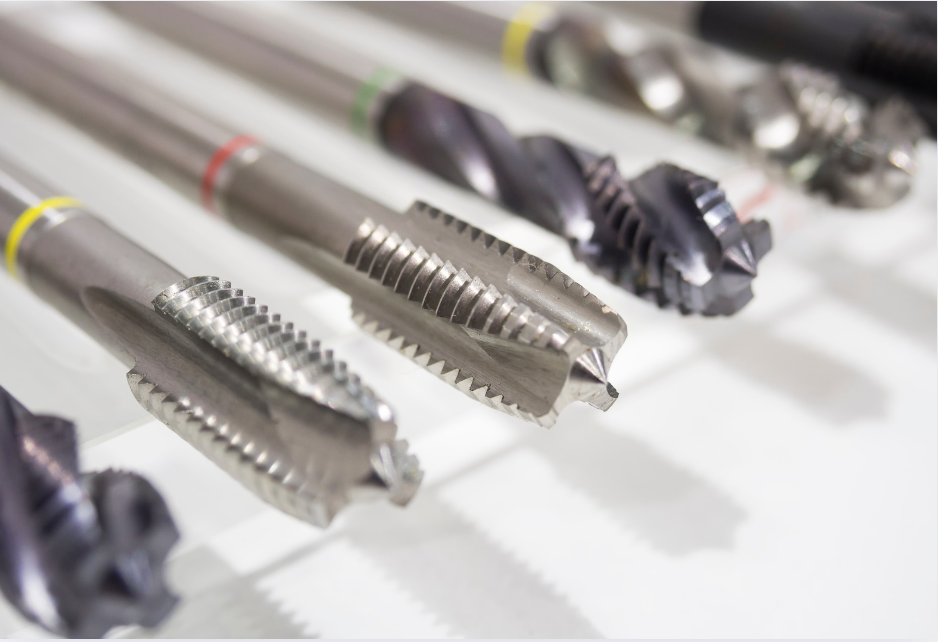
Micromachining cemented carbide is considered extremely difficult due to its high hardness and special material properties.
Therefore, in order to realize high-precision microfabrication on cemented carbide, it is essential to select a fabricator with appropriate machining technology.
This article provides detailed information necessary for product development, including the characteristics of cemented carbide, the difficulties of microfabrication, the latest machining technologies, and how to select a reliable supplier.
Receive technical proposals at TaigaTable of Contents
What is Cemented Carbide?
Cemented carbides are composite materials consisting of hard metal carbides such as tungsten carbide bonded with metals such as cobalt.
Due to its special structure, it has a hardness second only to diamond and excellent wear resistance.
Typically, the metal carbide content is about 80-941 TP3T, and the hardness and tenacity can be balanced and optimized for each application by adjusting the proportion of bonded metal.
The combination of tungsten carbide and cobalt is typical of the metals used in cemented carbides, but there are also cemented carbides with various combinations of titanium carbide, tantalum carbide, nickel, and chromium.
Properties of Cemented Carbide
Cemented carbides have the following characteristics
- Hardness: With a Rockwell hardness (HRA) of about 83-94, it is second only to diamond in hardness, surpassing iron and stainless steel.
- Abrasion resistance: Less prone to wear than other metal materials.
- Compressive strength: High compressive strength, suitable for use in high-load environments.
- Modulus of elasticity: Young's modulus is approximately 2.5 to 3 times that of steel, making it resistant to deformation.
- Heat resistance: Maintains hardness even in high-temperature environments and is suitable for precision metalworking.
- Low thermal expansion: Characterized by low dimensional change due to heat and stability at high temperatures.
- Self-sharpening: new sharp edges are exposed during use, maintaining cutting performance.
- Brittleness: weak to impact and prone to chipping when subjected to sudden force.
While it is superior in various aspects such as hardness, abrasion, compressive strength, and heat resistance, it should be noted that it is weak against impact and prone to chipping.
Reasons why high precision machining of cemented carbides is difficult
The following characteristics of cemented carbide are reasons why high precision machining of cemented carbide is difficult.
- Very high hardness
- Prone to brittle fracture
- Low thermal conductivity
First, cemented carbide is very hard, so it requires a different approach than normal metal machining.
Diamond grinding wheels, which are harder than cemented carbide, are required for grinding, but the high affinity between the two causes severe tool wear and requires long machining times.
In addition, since cemented carbide is sensitive to impact, it is prone to microcracking and chipping under inappropriate machining conditions, resulting in reduced machining accuracy and product defects.
Electrical discharge machining is also possible, but tungsten carbide, the main material used in cemented carbide, has a high melting point (2900°C), resulting in high energy consumption, making the balance between maintaining machining accuracy and economic efficiency a challenge.
Thus, high-precision machining of cemented carbides requires special techniques and expertise, and the number of suppliers who can handle this task is limited.
Method for achieving microfabrication of cemented carbides
To achieve microfabrication of cemented carbides requires advanced machining techniques that take into account their high hardness and special characteristics.
The main processing methods are as follows
- electrical discharge machining
- Laser Processing
- Machining
- LAP processing
- Lathe Machining
Electrical discharge machining allows non-contact, high-precision machining and is ideal for deep hole drilling and micro-pattern formation.
Laser processing uses high energy, which can even process diamonds, to achieve ultra-precision processing with minimal thermal effects.
In grinding, methods such as cylindrical grinding and surface polishing are used, as are wheels and slurry blades containing diamond abrasive grains.
LAP machining uses ultrasonic tools and diamond powder to achieve a mirror finish on cemented carbide materials.
Turning is used to quickly and precisely profile cemented carbide to produce cylindrical shapes and tools.
By appropriately selecting and combining machining methods, the challenges in microfabrication of cemented carbides can be overcome and high-precision machining can be achieved.
Scenes requiring fine machining of cemented carbide
Microfabrication technology for cemented carbides is an innovative technology needed in many industrial fields.
In the aerospace and automotive industries, this technology is attracting attention for its usefulness in enabling high-precision, deep hole drilling and fine grooving, which were difficult to achieve with conventional methods.
In the electronics industry, nano-level precision machining is required for the manufacture of touch panels for smartphones and various sensors, and cemented carbide microfabrication technology is utilized.
In the medical device industry, carbide molds are used to manufacture precision surgical instruments and implants, for which advanced microfabrication technology is essential.
In addition, the latest machining technologies have produced a wide variety of products that take advantage of the characteristics of cemented carbide, including fine holes of 0.1 mm, high-quality products with a flatness of 1/100, and mirror-finished lens molds.
How to choose a contractor for microfabrication of cemented carbides
When outsourcing cemented carbide microfabrication, select a supplier based on technical capabilities and reliability.
Below is a detailed explanation of what you can look for to identify a reliable vendor.
Is the company ISO 9001 certified?
ISO 9001 certification is an indicator that a contractor's quality management system conforms to international standards.
ISO 9001-certified vendors have a consistent quality control system from design to delivery, with appropriate record keeping at each stage of the processing process.
We also constantly optimize our quality control system through regular audits and take proactive measures against potential problems.
However, certification is not mandatory, and actual technical skills and equipment must also be verified.
Do you have equipment dedicated to microfabrication?
Specialized equipment is essential for microfabrication of cemented carbides.
Reliable vendors have state-of-the-art equipment and technicians who can operate it properly.
For example, check for high-performance equipment such as ultra-precision 5-axis machining centers, femtosecond laser cutting machines, and high-precision wire EDM machines.
By hiring a vendor with a wide variety of specialized microfabrication facilities and equipment, you can not only meet diverse processing needs, but also achieve both high-precision processing and cost reductions.
Do you have experience in microfabrication of cemented carbides?
It is important to check the track record of the vendor to determine their processing skills.
Polishing and finishing processes by engineers greatly affect the dimensional accuracy and surface roughness of products.
Machining cemented carbide requires extensive knowledge and expertise, as it is highly difficult to set machining conditions and requires repeated trial runs to obtain optimal results.
In addition, they must be able to deal with technical issues such as thermal management during machining, tool wear control, stress management and deformation prevention.
Other keys to producing high quality products include the use of appropriate cooling fluids, tool selection and maintenance, machining sequence, and the use of proper fixturing methods.
Use processing examples and customer evaluations to determine if the engineer is capable of managing these factors comprehensively.
Time to delivery and processing costs
Delivery time and cost are also important selection criteria for cemented carbide microfabrication. A reliable supplier should be able to clearly present the following information
- Lead time: 2 weeks from order placement for prototypes, 4 weeks for first lot in mass production, etc.
- Mass production capacity: up to 100,000 units per month, etc.
- Cost structure: breakdown of initial cost and unit cost, economies of scale in mass production
- Price fluctuation factors: Explanation of additional processes due to material cost fluctuations and complex shapes
- Payment terms: prepayment, installment payment, post-delivery payment, and other options
The balance between accuracy and delivery time should also be considered when selecting a vendor.
Companies specializing in high-precision processing can handle difficult requests with special equipment and inspection devices, but delivery times tend to be longer.
On the other hand, companies that emphasize rapid production can handle a wide range of lot sizes with their well-equipped facilities, but they cannot always provide high-precision products.
It is important to select the appropriate contractor for your request.
Summary
Microfabrication of cemented carbides is challenging, but measures and machining methods exist to overcome the challenges.
High-precision microfabrication can be achieved by choosing a supplier with appropriate processing methods and advanced technology.
If you are considering manufacturing parts utilizing cemented carbide, please contact us.Taiga."Please make use of the following
Taiga is a free service that allows you to consult with experienced contractors.
We can efficiently proceed with the development of difficult or new parts, small-lot production, prototyping, and mass production while keeping costs low.
Receive technical proposals at Taiga