![Taiga Interview] Expert Suggestions and Prompt Communication Ensure Smooth Production of First Metal 3D Printing](https://trytaiga.com/wp-content/uploads/2025/04/Taiga-user-interview.png)
The digital manufacturing platform, "TaigaWe asked Hiroyuki Fujii of the Production Division of Kawasaki Sharyo Co., Ltd. what he thought of the Taiga, which he used to study the production of metal 3D printed components of rolling stock and to make prototypes.
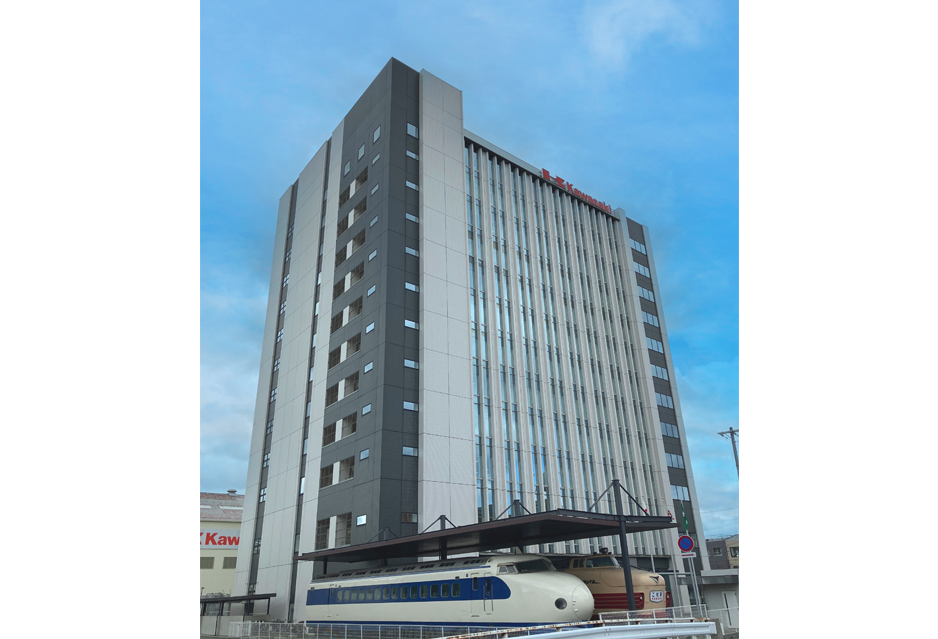
TaigaCan you tell us about the challenges and background you had when you asked
The rolling stock components we manufacture require a high level of safety and quality, which is why welding, for example, requires a high level of skill in the manufacturing process. However, with the retirement of the baby boomers and the decrease in the workforce, it is becoming increasingly difficult to maintain the skill level.
In addition, the business type is high-mix low-volume and requires special jigs and molds for each manufacturing process, and the time and cost required to prepare them are also considered an improvement. In addition, we sometimes receive requests to manufacture again 10 or 15 years later, and at that time, we sometimes have difficulty in preparing manufacturing equipment and skills again.
Under such circumstances, we were considering manufacturing methods that incorporate new technologies with an eye toward the future, without being bound by current manufacturing methods.
I see. Did you have an image of what you wanted to do at that point? Did you have an image of what you wanted to do at that point?
Various technologies such as casting and machining have been considered as new alternatives, but many of them have been difficult to study due to manufacturing efficiency, cost, and instability caused by manufacturing characteristics.
I was attracted to 3D printing because it is possible to manufacture complex shapes without molds or jigs as long as you have the data of the 3D printed model. Also, in terms of material procurement, as long as we only needed to procure wire, we thought it would be possible to cut costs and shorten procurement time. We have been promoting the smart factory concept for several years now, and it was also the time when we were considering the use of 3D printers to improve the efficiency of production preparation. 3D printing is available in various materials such as resin and carbon, but many of the products we manufacture are made of metal. We focused on metal 3D printing because many of the products we make are made of metal.
Among the many companies that handle metal 3D printing technology, I heard that your company can produce large models over 1 meter in size by combining a rotating jig and stacking, and I was interested in your service because I thought this would be a good application for our company.
What was your impression when you were introduced to Taiga by our sales representative?
I had never heard of this form of platform for the manufacturing industry. In particular, I felt that the Taiga was new in that it centralized all of the individual exchanges that were complicated and required the use of multiple tools in the conventional way. I also thought it was an efficient solution for the current era, and felt that it was 'very current.
We expect that this will set a new standard beyond the traditional manufacturing industry in terms of an online platform that allows for rapid response as well as technology proposals.
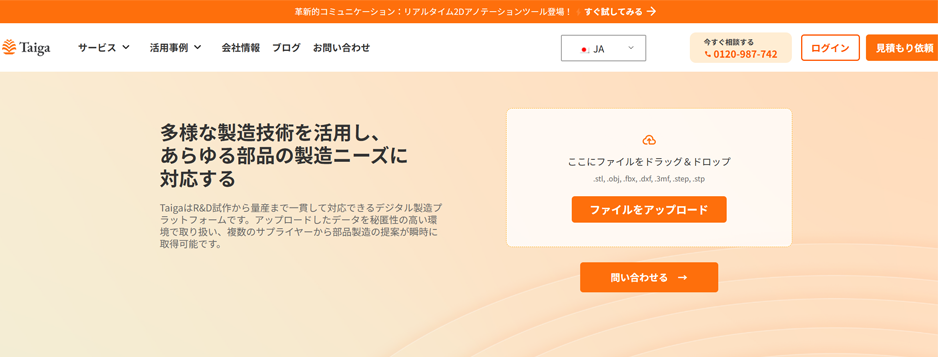
What concerns, if any, did you have when using Taiga for the first time? Were your concerns addressed through the actual service?
Since Taiga is entirely online, I was concerned about the smoothness of the communication with your company. However, in fact, I was impressed by the quick response to my messages from the Taiga representatives and engineers, and the speedy communication.
The Taiga was very attractive because it allowed us to communicate consistently with a single tool.
I am glad to hear that your concerns made a positive impression on us! What else attracted you to Taiga?
The fact that we can receive new proposals that take into account production and quality. We are attracted to receiving suggestions from professionals in the field of technology about things we do not know. We would like to receive more and more suggestions from third parties, as they may help us notice things that we are not aware of.
I also liked the fact that we could communicate with these people by entering comments and illustrations on the drawings on the Taiga. Especially in the technical aspects, there were things that both sides knew and didn't know, so it was good to be able to proceed in such an easy-to-understand and in-depth manner. It was also useful to be able to keep a log of who, when, with whom, how, and what conclusions were reached.
So, did the quality of the deliverables meet your expectations?
Since this was our first attempt to use a DED metal printer, our objective was to confirm what kind of deliverables we would be able to produce. We were able to learn and understand the characteristics of the process, shape restrictions, and the characteristics and defects of the deliverables (in this case, empty walls on the cutting surface) through communication with Taiga personnel and engineers, and we feel we were able to achieve our objective.
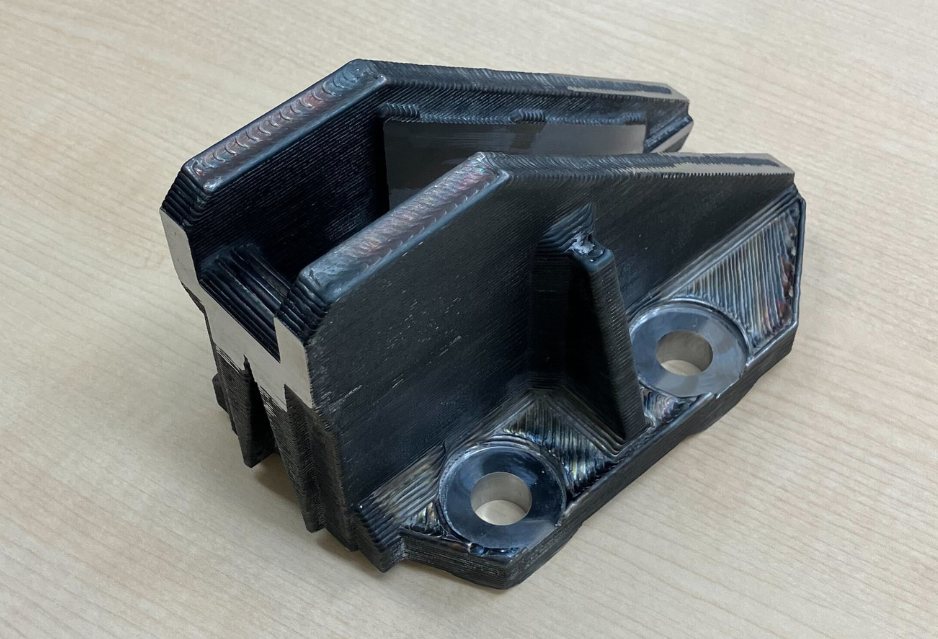
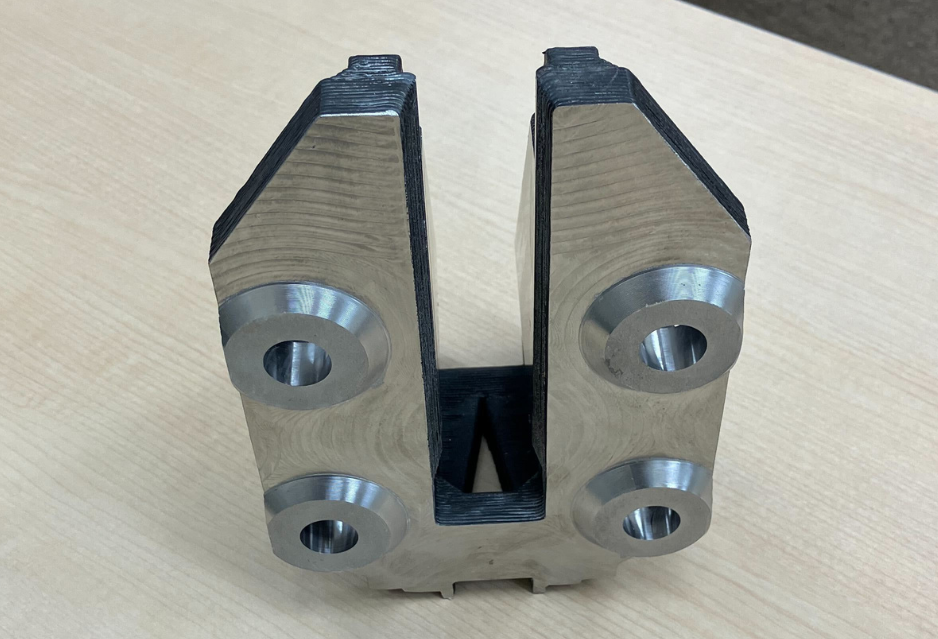
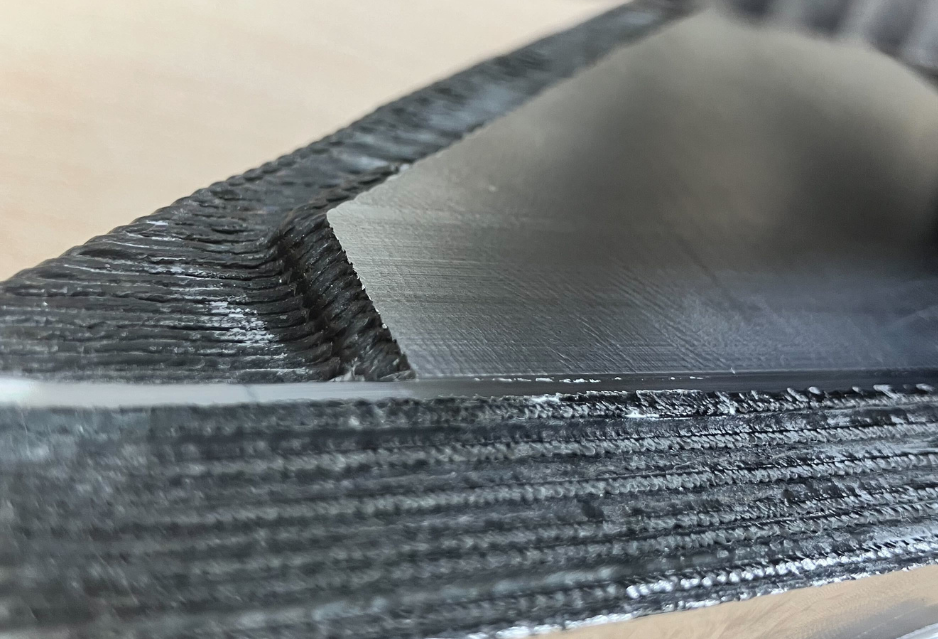
Manufactured product: One of the components that make up a rail car
Specification technology: metal 3D printing
What are your plans for the future? Is there anything you would like to do or are thinking about doing?
In Europe, the use of 3D printing in rolling stock manufacturing is advanced, but I feel that Japan is not so advanced compared to Europe. We would like to be like a first penguin (a pioneer who is the first to adopt new technology) and be ahead of our competitors in Japan. To this end, I would like to continue to explore new approaches and actively adopt new technologies.
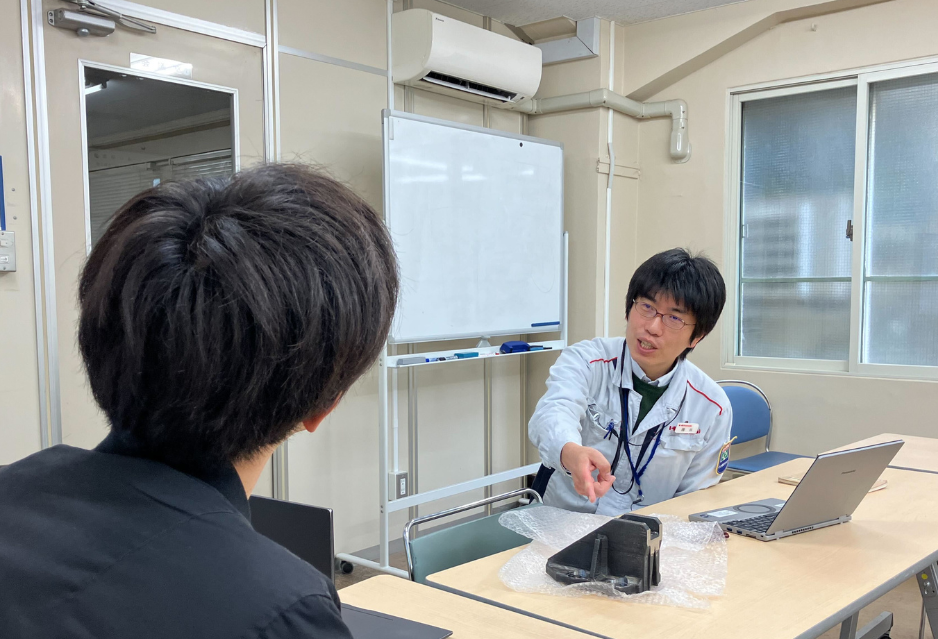
Thank you very much for taking the time to do this interview today!
On Taiga, simply upload your drawings and files and receive free technical proposals from professionals in various manufacturing technology fields, including 3D printing, CFRP machining, sheet metal working, cutting, injection molding, and cold working.
As in the case of Kawasaki Sharyo, we flexibly respond to the diverse needs of our customers, whether they have a new technology they wish to incorporate or want to optimize an existing manufacturing process, and propose the optimal solution.
Receive technical proposals at TaigaKawasaki Sharyo Co.
https://www.khi.co.jp/rail