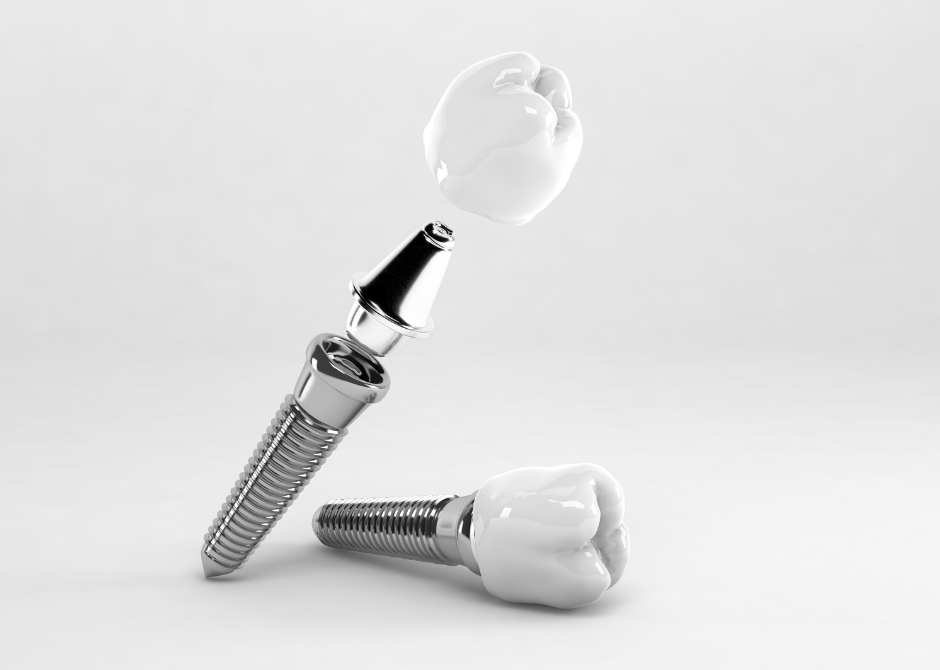
In recent years, cutting has been gaining attention as a processing method used in the manufacture of implants.
Many people may be considering manufacturing implants by cutting, but may have questions such as "I want to know what is suitable for manufacturing implants by cutting" or "I want to know what materials are used for manufacturing implants.
In this article, we will discuss the cutting process used to manufacture implants, its advantages, and what to look for when cutting.
Please refer to this section for information on how to select a vendor to perform cutting work.
For more information about Taiga, click here.Table of Contents
Cutting is the preferred processing method for manufacturing implants
Cutting is a method of machining materials into desired shapes using a variety of tools and machine tools.
Among the many cutting processes, CNC machining for the medical industry is gaining attention as a manufacturing method for implants.
CNC machining for the medical industry is used as a quicker and less costly way to produce medical devices with higher precision than ever before.
By manufacturing implants with medical CNC machining, it is possible to achieve greater precision than previously possible.
Materials used in cutting implants

The material used for cutting implants is titanium material for surgical implants.
Titanium has been widely used in the aviation and space fields and as a chemical plant material due to its high strength, corrosion resistance, and heat resistance.
It is also widely used as a material for implants because of its high biocompatibility, which prevents the body from rejecting it as a foreign substance.
Currently, six types of titanium materials for surgical implants are defined in JIS standards.
Advantages of using cutting for manufacturing implants
The use of cutting in the manufacture of implants offers many advantages.
The following is a step-by-step explanation of the specific advantages of cutting in the manufacture of implants.
High-precision, high-quality finishing is possible
Cutting operations use machining centers, NC milling machines, and other cutting machines and programs.
The program is capable of micron-level dimensional control and numerical control by computer.
Because it can achieve high-precision dimensions even for complex shapes, it is also suited for manufacturing implants, which require precision machining.
Fast delivery and low-cost production
Cutting does not require the fabrication of dies, which is necessary in casting and forging processes.
No cost or time is incurred for mold fabrication, and fabrication is possible only with 3D-CAD data.
For one-off items such as implants or items that are produced in small quantities at the same time, cutting will enable quick delivery and low-cost production.
High flexibility in processing
In cutting, even complex shapes can be machined without difficulty.
In addition, because it is capable of machining with high precision, such as 1/1,000, it can be manufactured to check the mating with another part. Another advantage is that not only dimensional accuracy but also surface roughness can be adjusted.
In addition, we can also control extremely small tolerances, such as 10 micron tolerances, where the human eye cannot tell the difference. Cutting processes utilizing such advanced technologies are also responsible for processing in fields that require precision, such as semiconductor devices, medical equipment, and electronic components.
Can be processed into a wide range of shapes
Cutting is not limited by material thickness as long as the machine can process it.
Some machines support automatic machining by inputting the order of tools and the machining process, thus enabling machining of complex shapes that would be difficult with human labor.
It is also suitable for manufacturing implants, which require precise dimensions to match the user.
Cautions in Cutting Implants
While cutting is a good process for manufacturing implants, there are some points to be aware of during the process.
Here is a step-by-step explanation of the caveats to keep in mind when considering cutting in the manufacture of implants.
Easily deformed during cutting, making machining more difficult
Titanium has a low coefficient of longitudinal elasticity, which makes the material easily deformable during cutting and difficult to machine.
Particular attention should be paid when processing thin materials, as they are easily deformed, resulting in reduced processing accuracy and possible cracking.
Easy tool wear
Titanium has a characteristic of low thermal conductivity, which makes it easy for tools to overheat during cutting.
It is important to note that the heat generated by the cutting process accumulates in the tool and the material to be machined, resulting in severe tool wear.
In addition, the higher the cutting speed, the more cutting heat is generated, which leads to further tool wear due to higher temperatures in the cutting area.
Note that tools will deteriorate quickly if cutting is not performed with proper cooling.
Continuous cutting also generates chips, and the cutting edge may chip or wear due to fluctuations in cutting resistance.
Four key points in cutting implants
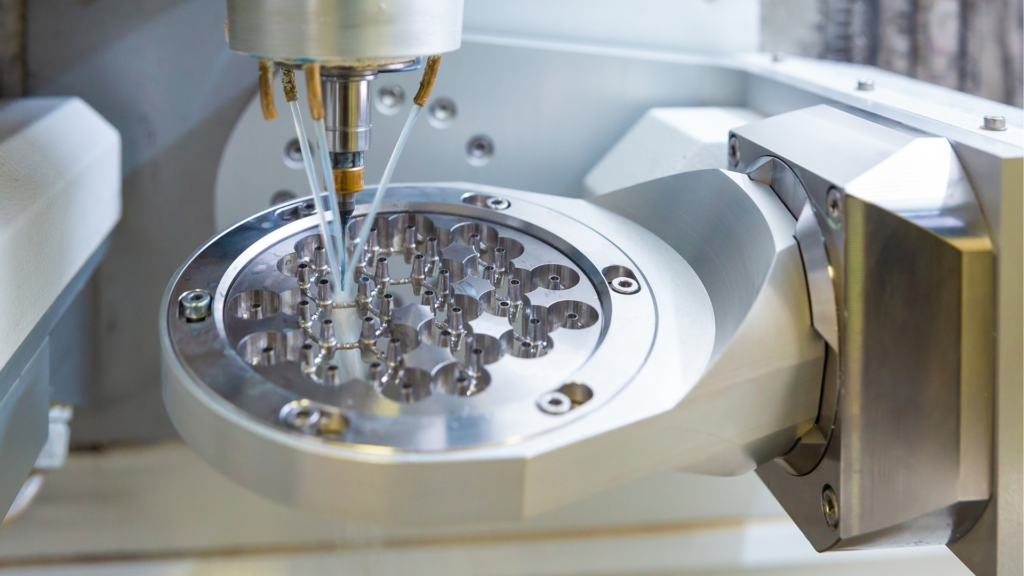
We found that cutting implants requires attention to deformation and tool wear during cutting.
Here are four key points to remember for successful cutting of implant manufacturing.
Cutting at low speed
Cutting at high speeds can cause tool wear and tear due to heat buildup.
Cutting during implant manufacturing should be performed at the lowest possible cutting speed.
Use coolant
The use of coolant effectively suppresses heat during processing.
Coolant should be used aggressively, not only to prevent tool wear, but also to prevent loss of accuracy due to titanium deformation.
Use appropriate tools
Selecting the right tool for titanium implant manufacturing will improve machining accuracy and prevent tool wear.
For example, tools with high-performance coatings or special alloy tools specially designed for titanium should be used for cutting.
Properly manage stresses during processing
Titanium leads to tool wear and heat generation at high feed rates.
To maintain proper feed rate, be sure to properly manage stresses during machining.
How to choose a supplier for cutting implants
The following points should be taken into consideration when selecting a supplier for cutting implants.
- Do you have experience in cutting implants?
- Does it meet quality control standards for medical devices?
Cutting of implants should be performed with various precautions as mentioned above.
A company that has a lot of experience in cutting implants is likely to be able to cut implants with a high level of technical expertise.
In addition, when manufacturing medical devices such as implants, quality control standards must be met to ensure product safety.
Choose a supplier that meets quality control standards, such as ISO 13485, an international quality management system standard specific to medical devices.
Summary
This article provides an overview of cutting for implant manufacturing, the advantages of cutting, cautions, and how to choose a vendor to manufacture implants.
Cutting is a processing method that is suitable for manufacturing implants, which are medical devices, because it can achieve high precision and free shape processing.
Selecting a company that understands the characteristics of titanium, the raw material used to make implants, and that is highly skilled and meets quality control standards for medical devices, will ensure a satisfactory cutting process for the implants.
Considering manufacturing lightweight components?Taiga."Taiga is a free service that allows you to consult with experienced contractors.
We can efficiently proceed with the development of difficult or new parts, small-lot production, prototyping, and mass production while keeping costs low.
For more information about Taiga, click here.