![[Die casting process] Merits and demerits of crossing over with insert molding](https://trytaiga.com/wp-content/uploads/2024/10/671f53babca3066c21cc7066_die-casting-insert-molding-1.png)
Die casting" is suitable for products with complex shapes and thin-walled structures that require high precision, and is used in a wide range of fields such as automotive parts and electronic devices.
What we further recommend is the combination with "insert molding". Integral molding of metal and resin enables increased strength and weight reduction, further increasing the value of the part.
In this article, the advantages and disadvantages of combining die casting process and insert molding will be explained in an easy-to-understand manner, and we hope you will find it helpful in selecting a manufacturing method.
Table of Contents
What is Die Casting?
Die casting" is a method of forming products by pouring molten metal into a die under high pressure. The name is derived from "Die" meaning a mold and "Cast" meaning a casting, and is also written as "die cast" in addition to "die cast.
It is particularly suited for the production of products that require complex shapes and high precision, and is also suitable for mass production because once a mold is made, it can be continuously molded.
Materials used are metals with relatively low melting points, such as aluminum, zinc, magnesium, and brass. Among them, "aluminum die cast" and "zinc die cast" have excellent durability and light weight, and are used in many fields such as automobile parts, home appliances, electronic devices, and precision equipment.
Flow of Die Casting Process
The general flow of die-casting process is as follows.
- Produce die-casting dies
- Melting metals (molten metal)
- Inject molten metal at high pressure
- Cooling
- Remove castings from molds
- Perform finishing (straightening, polishing, painting, etc.)
Pins are essential to die casting molds. For example, core pins (cast pins) are used to form holes or complex shapes in products, while ejector pins (extrusion pins) are used to remove products from the mold after forming. If pins break, productivity is greatly reduced, so expertise in toughness, high-temperature strength, and dimensional accuracy is required. To prevent defects, we recommend that you contact a supplier that specializes in pin fabrication.
Examples of die-cast products
A wide variety of products are manufactured by die casting. Typical examples are listed below.
- Automotive parts (engines, transmissions, shock towers, etc.)
- Electrical and electronic components (computers, copiers, printers, etc.)
- Home appliances (operation panels and structural components)
- Aircraft interior cabin components
- Smart Phone Frames
Especially in automotive parts, die casting process is widely used because it is required to maintain strength while being lightweight.
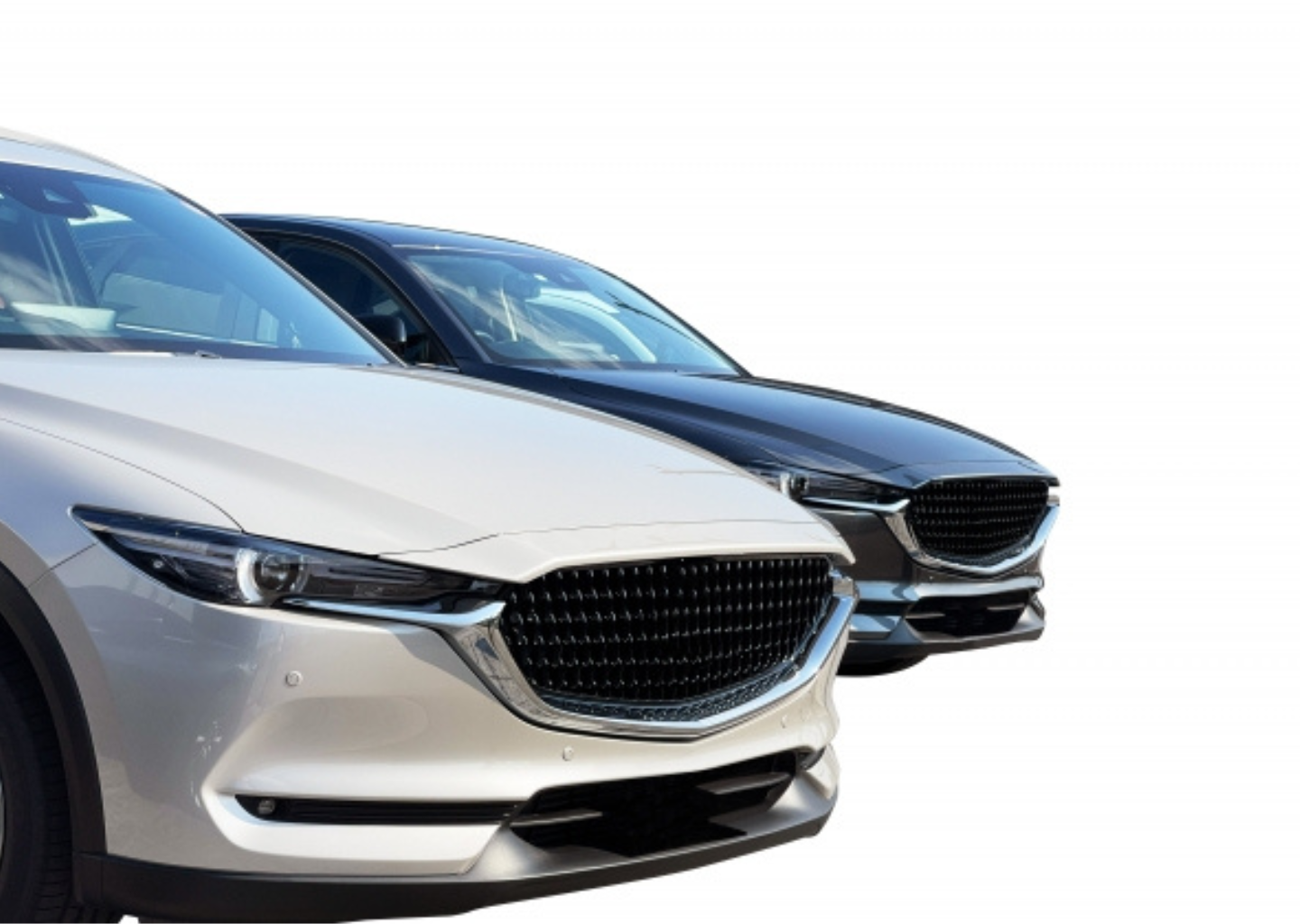
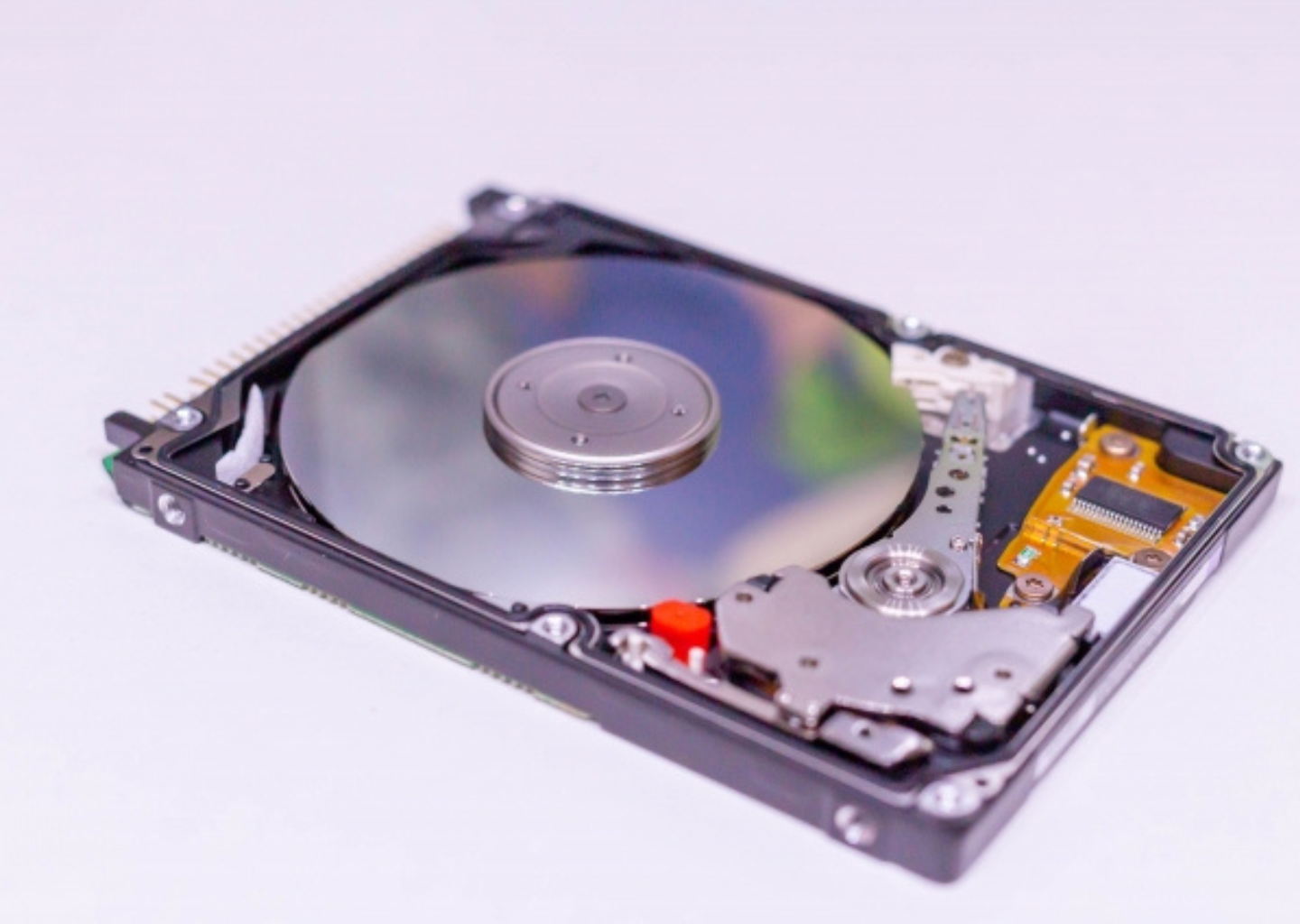
Difference between Die Casting and Casting
Die casting" and "casting" are both processing methods in which molten metal is poured into a mold, but there are significant differences in the processes. First, casting uses gravity to slowly pour the metal into the mold, which tends to lengthen the manufacturing time. The temperature of the molten metal tends to drop during the pouring process, which has the disadvantage of causing "unfilled" products that do not cover every corner of the mold. This can result in uneven or chipped product surfaces.
On the other hand, the die casting process fills the mold with metal under pressure, which reduces the occurrence of unfilled parts and improves the accuracy of the product. To put it simply, it is like pinching the end of a hose. Water pressure increases and is released all at once, right? With die casting, the metal is well distributed inside the mold, so products with complex shapes can be made in a short time.
Quality and production efficiency can be greatly improved by appropriately selecting either "die casting process" or "casting" depending on product requirements.
Combination of insert molding and die casting process
Die casting process is often used in combination with "insert molding" to improve product performance. Insert molding is a molding method in which glass or plastic parts (inserts) are placed in the mold in advance and metal or resin is injected around them to integrate them. This technology allows products to be made from a combination of different materials, which improves strength and durability and makes it possible to produce more functional and higher quality products.
A specific example is the shift lever of an automobile. The inside of the shift lever is composed of metal and the outside is covered with soft resin. These products are not manufactured separately and attached together later, but are molded in a single process by insert molding.
If you are looking for high quality products, we urge you to consider a combination of die casting process and insert molding. This combination is an ideal option for both improved product performance and cost efficiency.
Advantages of Die Casting Insert Molding
The advantages of combining die casting and insert molding are summarized below.
- Can make sturdy parts.
- Complex shapes can also be handled.
- Easy surface treatment
- High productivity
- Lighter and thinner
Each of these will be discussed in detail.
Can make sturdy parts.
By combining die casting and insert molding, products can be formed by integrating different materials such as metals and resins. Compared to combining separately made parts afterwards, the strength of the product is greatly improved because there are no joints. The risk of parts made from different materials splitting or breaking is greatly reduced, resulting in products that can be used for a long period of time.
Complex shapes can also be handled.
When die casting and insert molding are employed, mass production is possible while maintaining quality, even for designs with complex curves and details. This combination is particularly effective for products that require precision, such as automotive parts and internal structures of electronic devices.
Easy surface treatment
Insert molding by die-casting process provides a very smooth surface finish to the product, allowing for smooth surface treatment afterwards. Surface treatment can add functions such as corrosion resistance, abrasion resistance, and antibacterial properties. In this way, the durability of the product is enhanced and its appearance is cleaned up, thereby improving the product value.
High productivity
One of the most important factors in business is manufacturing lead time (production lead time). A long lead time from raw material processing to finished product can lead to the risk of missed sales opportunities and reduced customer satisfaction. Lead time is often the deciding factor in whether or not a client will choose your company, especially when it is difficult to make significant differentiation in terms of quality or cost.
The die casting process uses high pressure to quickly inject metal, resulting in very short forming times. Furthermore, insert molding can integrate different materials in a single process, making it possible to produce high-quality products in a shorter time than if they were manufactured separately. The combination of die-casting and insert molding greatly improves production efficiency, giving us a competitive advantage over our competitors.
Lighter and thinner
By utilizing die casting and insert molding, parts can be made lighter and thinner. For example, automotive parts used to be mostly made of steel, but are now being replaced by lighter alloys such as aluminum. This has led to a reduction in the overall weight of the car, contributing to improved fuel efficiency. In addition, instead of using only metal to make a product, it can be integrated with other materials such as resin to obtain a product that takes advantage of the characteristics of both. Specifically, it is possible to incorporate the lightweight and insulating properties of resin while maintaining the high strength and conductivity of metal.
Disadvantages of insert molding of die castings
While there are many advantages to the combination of die casting and insert molding, there are also disadvantages. Specific issues and countermeasures are described below, which should be fully considered from the product design stage.
High initial cost
Die casting and insert molding require the creation of a mold. Since these molds are very precise, the cost of making them can be expensive. Especially in the case of low-volume production or prototypes, the burden of initial investment may seem large. However, since die-cast insert molding has extremely high productivity, the cost per piece can be significantly reduced when mass production is considered, which may lead to long-term cost savings. It is important to select the most appropriate processing method, taking into consideration the volume of the product, its shape, accuracy, and material.
Warping and cracking
Insert molding in the die-casting process integrates different materials together, so there is a risk of defects due to differences in expansion and contraction of each material. The main problems are as follows
- Warping: Bending and twisting not only causes unsightly appearance, but also interferes with parts and creates gaps during assembly.
- Cracks: Cracks can develop and degrade the quality of the product, as well as cause dimensional misalignment and water leakage.
- Cold shut: The product solidifies before filling and irregular lines (joints) appear.
- Weld line: A condition in which materials are not completely fused together (poor fusion), which may result in loss of strength.
Weld lines are especially likely to occur when materials with different thermal expansion coefficients, such as metal and resin, are combined. This reduces the durability of the product and increases the risk of complaints from suppliers and consumers, as the product is prone to cracking and breaking even with light impacts. It is difficult to completely prevent molding defects, but by hiring an experienced supplier, it is possible to foresee the occurrence of defects and take appropriate countermeasures.
Summary
This article explains the advantages and disadvantages of combining die casting process and insert molding.
Die casting is a method of manufacturing products by pouring molten metal into a mold, and is particularly suited for mass production of complex shapes. By adding insert molding to this process, stronger and lighter products can be produced.
On the other hand, there are disadvantages such as high initial costs and a tendency for manufacturing defects such as warping and cracking to occur. The key to success is to fully understand these characteristics and choose the best manufacturing method for your product.
If you are wondering how to manufacture your products, please visit Taiga, where you can consult with experienced suppliers free of charge. By taking expert advice as you go, you can produce high quality products while keeping costs down. Start by creating an account and take the first step in your new manufacturing journey!
For more information about Taiga, click here.