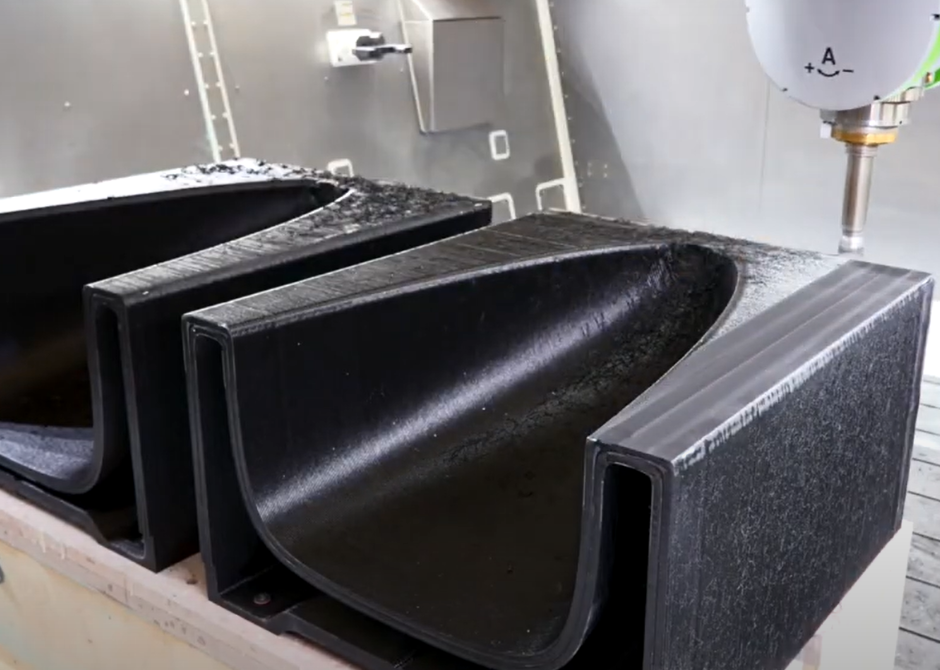
CFRP (carbon fiber reinforced plastic) is utilized as a material for various parts and products by taking advantage of its properties.
However, when manufacturing products using CFRP, there are many questions such as "Is CFRP a flame-retardant material? I want to make a product using CFRP, but is it suitable? Are CFRP suitable for your products?
In this article, we will discuss the advantages and disadvantages of CFRP, as well as whether it is a flame-retardant material and the scenarios in which CFRP is used.
Please refer to the following pages for information on typical CFRP processing methods.
Receive technical proposals at TaigaTable of Contents
What is CFRP (Carbon Fiber Reinforced Plastic)?
CFRP is one of the composite materials in which carbon fiber is added to resin as a reinforcing material.
With the lightness of resin and rigidity comparable to metal, this material is used in a variety of components, including aircraft.
The properties vary depending on the type of resin and carbon fiber used, the length and content of carbon fiber, and the direction of placement.
From here, the advantages and disadvantages of CFRP will be explained in turn based on its properties.
Advantages of CFRP
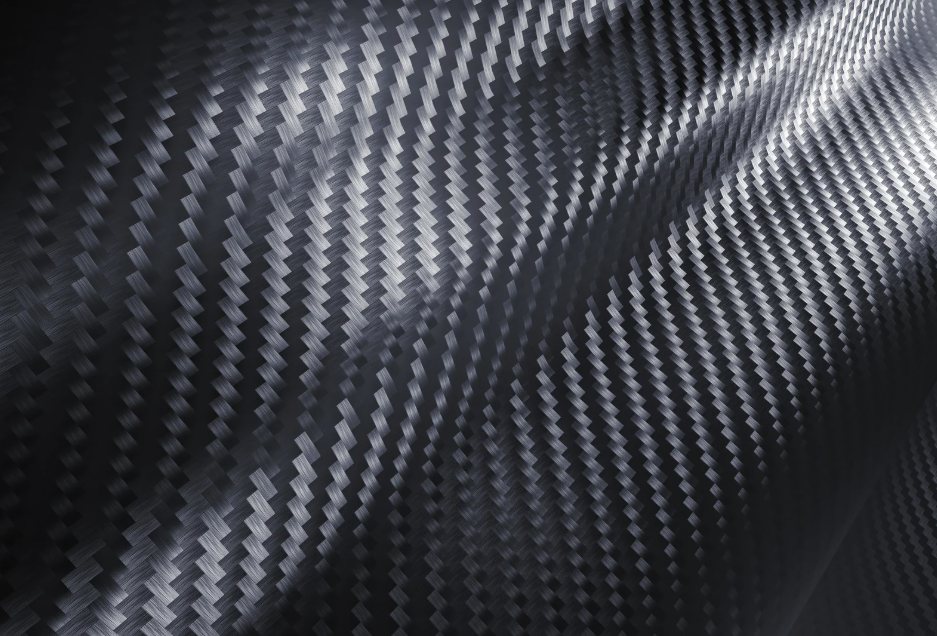
The main advantages of CFRP are as follows
- light (i.e. not heavy)
- strong
- No corrosion
- Hard to thermal expansion
- Integral molding is possible.
CFRP is a material that combines the lightness of resin materials with the rigidity obtained by adding carbon.
It also has characteristics that make it difficult to expand thermally due to the combination of a resin that expands with heat and carbon that shrinks with heat.
This allows for integral molding, which is another advantage over metal in that it allows for more efficient molding.
Disadvantages of CFRP
While CFRP has many advantages, it also has the following disadvantages
- Complicated manufacturing
- Low mass production
- High cost
CFRP is a material that combines two materials of different directions, resin and carbon, and thus requires complex material design during processing. Therefore, it is not suitable for mass production.
Another disadvantage is that CFRP itself is an expensive material, resulting in higher processing costs.
Is CFRP a flame retardant material?
CFRP is a material with a certain degree of heat resistance, but it is less flame resistant than metal.
On the other hand, CFRP is a lightweight material with high rigidity, fatigue properties, and environmental resistance, and is increasingly being used as a component in the automotive, aircraft, and space sectors to reduce weight and improve fuel efficiency.
Therefore, CFRP that combines flame retardancy has been in demand in recent years, and indeed, advances in material property analysis and material development technology have led to research and development of CFRP materials that cover flame retardancy.
Examples of scenes and products in which CFRP is used
This section describes examples of scenes and major products in which CFRP is used.
Aerospace
In the aerospace field, CFRP is used in the following applications to reduce the weight of equipment, improve fatigue resistance, and increase heat resistance and flame resistance.
- Aircraft primary structural materials (wings, tail, fuselage, floor beam)
- Aircraft secondary structural materials (auxiliary wing, directional rudder, elevator rudder, fairing)
- Aircraft interior materials (seats, floor panels, lavatories)
- Rocket components (satellite fairing, interstage, motor case, nozzle throat)
- Satellites (antennas, solar panels, tube truss structure materials)
- Radio telescope (antenna, prop)
Automotive
In the fields of automobiles and motorcycles, CFRP is used to reduce weight, improve safety features such as fatigue resistance, vibration damping, and impact energy absorption, as well as to improve design.
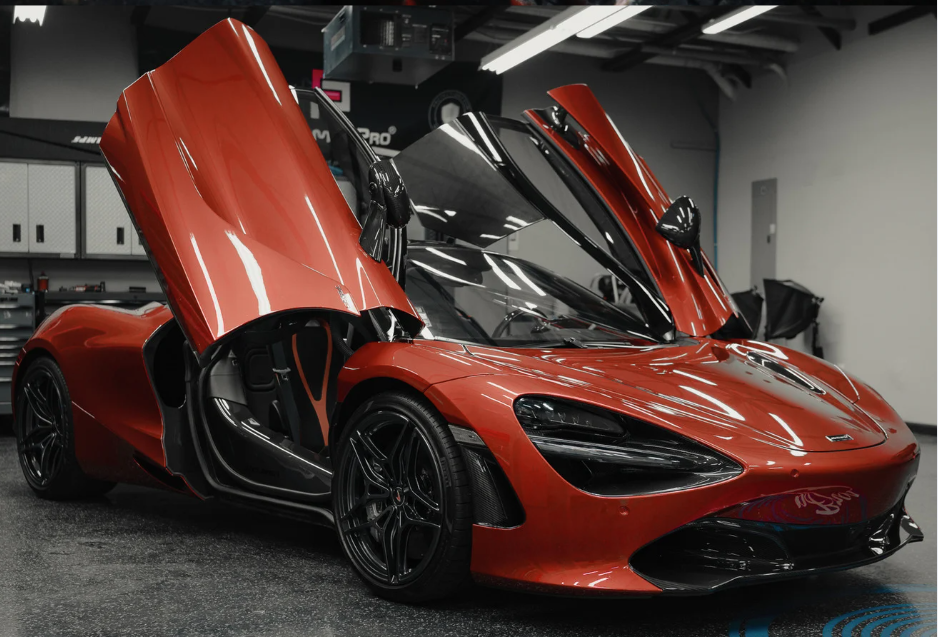
- Automotive structural materials (monocoque body, crash box structure)
- Automotive exterior panels (roofs, hoods, fenders, spoilers)
- Automobile interiors (seat frames, instrument panels)
- Power system (wheels, springs, plate springs, dampers, propeller shafts, transaxles, battery cases)
- Motorcycle structural materials (body frame, swing arm)
- Motorcycle exterior panels (cowl, gear cover, muffler cover)
Medical Field
In the medical and welfare care fields, CFRP is used in the following aspects to reduce the weight of equipment while taking advantage of its X-ray permeability.
- Medical equipment (top panel, cassette, X-ray grid, retractor)
- Welfare and nursing care equipment (wheelchairs, portable wheelchair ramps, prosthetic legs, knee joints, canes, assistive suits)
Other industrial fields
CFRP is also used in a wide range of other industrial components in terms of weight reduction, corrosion resistance, and rigidity, including the following
- Railroad (car body, car bogie, seat, water stop plate)
- Mechanical parts (transport robots, plate springs, robot arms, assist suits)
- High speed rotators (centrifuge rotors, uranium enrichment cylinders, flywheels, industrial rotors, shafts, human silk pots)
- Electrical components (parabolic antennas)
- Civil construction (concrete reinforcement, cables, rods)
CFRP Molding Method
Since CFRP is a material that can be processed in a variety of ways, it is important to select the molding method that best suits the application.
This section describes the characteristics of the main CFRP molding methods.
Autoclave Molding
Autoclave molding is a molding method in which the base material, prepreg, is laminated in a pressure cooker called an autoclave, covered with a bagging film to create a vacuum, then depressurized, and finally heat-cured under pressure.
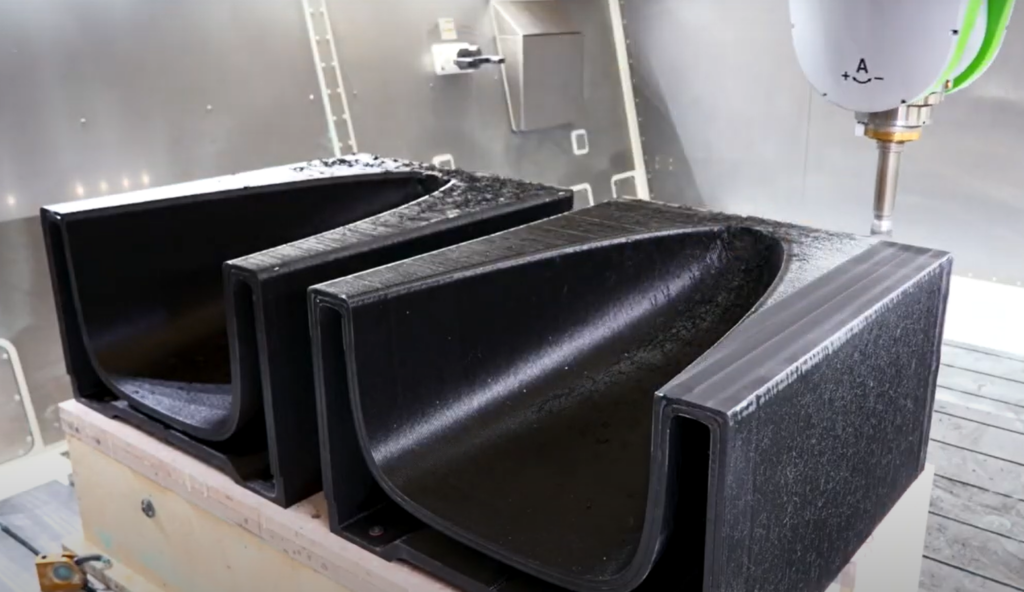
Pressure is expected to improve the physical strength of CFRP.
It is suitable when quality and performance are important, or when you want to manufacture CFRP products with complex shapes.
However, there are drawbacks in processing delivery time and cost due to the high cost of prepreg as well as the long cycle time of the molding process.
Oven Forming
Oven molding is a molding method that uses the same process as autoclave molding up to decompression, but instead of decompression, heat curing is performed by applying vacuum pressure.
Compared to autoclave molding, the cost of processing and materials can be reduced, and it is suitable for large molded products.
However, it is slightly inferior to autoclave molding in terms of performance and quality of processed products, and is not suitable for molding complex shapes.
Pultrusion molding
Pultrusion molding is a molding process in which carbon fibers are drawn into a liquid resin, dipped into a mold, and then passed through the mold and heat-cured.
Also called pull-trusion molding.
It is suitable for processing molded products with a certain cross-sectional shape, such as rods and pipes.
Continuous molding is also possible, which is effective in streamlining the production process.
Filament winding molding
Filament winding molding is a method of molding by heating and hardening filaments as a base material.
Suitable for tubing and tank shaped moldings.
Carbon fiber tow impregnated with liquid resin is wound around a mandrel and then heated.
There are two methods: one is to wind carbon fibers while soaking them in a resin bath, and the other is to wind tow prepregs, in which tows are impregnated with resin in advance.
Filament, the base material, is inexpensive and available, and processing can be automated.
It is suitable when you want to proceed with production while keeping construction period and costs low.
RTM Molding
RTM molding is a molding method that uses a pair of enclosed male and female molds.
Carbon fiber preformed into the shape of the product (preform) is placed in the mold, and liquid resin is press-filled and impregnated before heat curing.
Among RTM molding, when only a female mold is used for curing under vacuum pressure, it is called VaRTM molding (vacuum-assisted RTM).
RTM is for processing small and medium-sized moldings, while VaRTM is for processing medium and large moldings.
Both RTM molding is suited for processing with improved physical properties strength and shape accuracy.
Press molding
Press forming is a method of forming by applying pressure to a mold or sheet and heat curing.
A sheet impregnated with resin such as prepreg or SMC laminated to the mold is used.
Some companies offer press forming methods that strike a balance between cost and processing efficiency and are suitable for processing large products.
Sheet Wrap Forming
Sheet wrap forming is a forming method using an iron core called a mandrel.
The prepreg is wrapped around the mandrel and taped, then heat cured.
It is then decentered and formed, making it suitable for forming pipes and roll shapes.
Summary
In this article, we explained the characteristics, advantages and disadvantages of CFRP, and whether it is a flame-retardant material and how it is processed.
CFRP is a material that is expected to be in high demand in the future in terms of reducing the weight of equipment and devices and improving fuel efficiency.
In terms of fire resistance, research and development of CFRP with enhanced flame retardancy is also underway.
When considering CFRP processing, it is important to request a supplier that handles the appropriate processing method for the product you wish to manufacture.
If you are considering manufacturing parts utilizing CFRP processing, please contact us.Taiga."Please make use of the following
Taiga is a free service that allows you to consult with experienced contractors.
We can efficiently proceed with the development of difficult or new parts, small-lot production, prototyping, and mass production while keeping costs low.
Receive technical proposals at Taiga