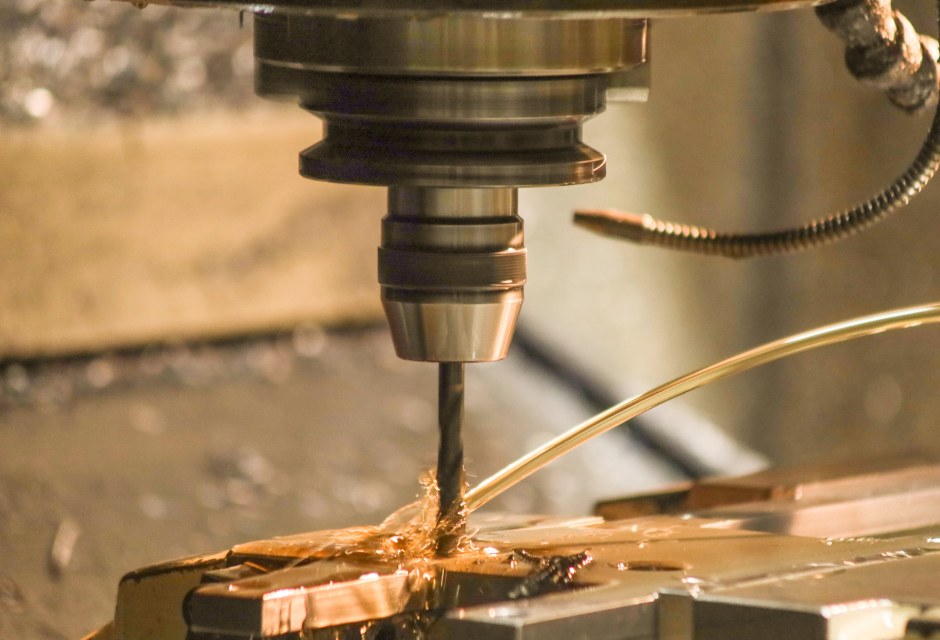
Machining" is a technology that uses a machine to process a product into the desired shape.
There are a wide variety of methods of "machining" in a single word, and it is necessary to select a method and machine according to the material and shape.
In this issue, we will explain the basics of machining, specific machining methods, and typical machine tools in an easy-to-understand manner. Please read to the end to find the optimal machining method and to facilitate your project.
Table of Contents
What is Machining?
Machining" is the art of using a machine to shape metal, plastic, or other materials into a desired shape. In English, it is called "machining" and is an indispensable technology in the manufacturing industry.
For example, parts of various products such as automobiles, aircraft, and precision instruments are made by machining.
Machining is characterized by the final shaping of materials by cutting, scraping, and joining parts together. Please continue reading for a detailed step-by-step explanation.
Difference between machining and metalworking
Machining" and "metalworking" are often confused, but how are they different?
Machining refers to the process of shaping with machines. Metalworking, on the other hand, refers to the overall processing of metals.
In other words, machining is a type of metalworking, which also includes heat treatment and surface treatment.
Types of Machining Methods
Machining is broadly classified into three categories depending on the principle of processing: "removal processing," "forming processing," and "joining processing. Here, we will explain the typical machining methods.
removal process
Removal processing" is a processing method that removes unnecessary portions of a material to create the desired shape and dimensions.
Let's look at the main types of removal processes.
Machining
Cutting" is a processing method that uses a blade to remove metal materials. It is divided into milling, turning, drilling, and other processes.
For example, in milling, a high-speed rotating blade is pressed against a fixed material to cut and shape it. By changing the shape and angle of the blade, it is possible to create a variety of shapes, including flat, curved, and grooved surfaces.
Grinding process
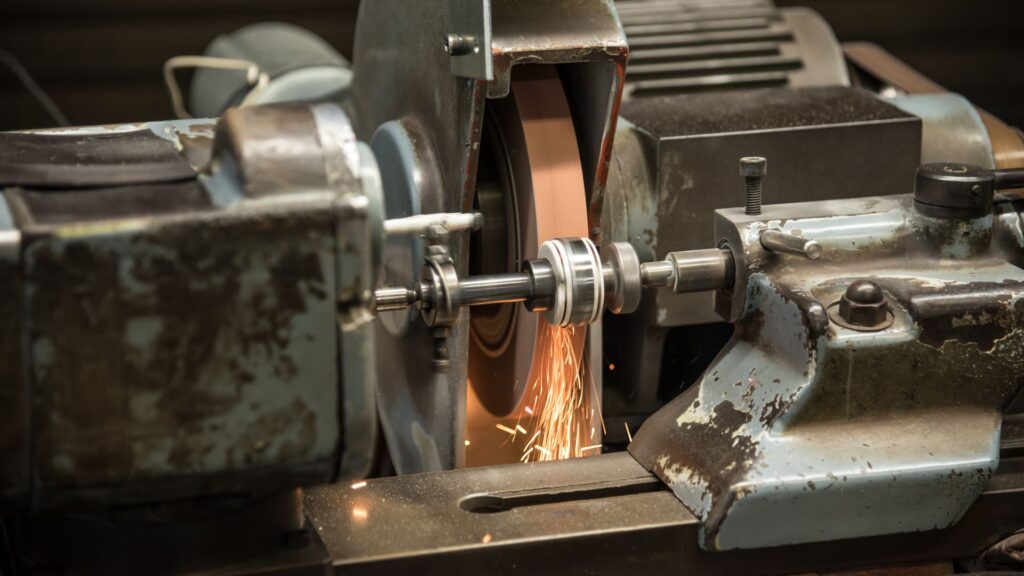
Grinding" is a processing method that uses a high-speed rotating grinding wheel to gradually grind a metal material into shape. It is a time-consuming process because it does not use a blade, but it is suitable for manufacturing parts that require high precision.
Depending on the surface to be processed, it is classified into "surface grinding," "cylindrical grinding," and "internal grinding.
Grinding process
Polishing" is a process for smoothing the surface of a product using a whetstone or abrasive paper. It removes surface irregularities and burrs to improve the appearance and functionality of the product.
In the most common "grinding wheel polishing," the surface is processed by bringing the material into contact with a high-speed rotating grinding wheel. Other methods include "abrasive cloth and paper processing," "lapping and polishing," and "tape polishing.
electrical discharge machining
Electrical discharge machining" is a method of processing metals by melting them with the heat generated by electrical discharge. Since the metal is melted rather than shaved directly, even very hard materials can be processed.
There are two types of EDM: "wire EDM" and "shape carving EDM.
Wire EDM uses a long, thin electrode to cut materials. Because the traveling path is controlled by computer, even complex shapes can be processed with high precision.
Shape carving EDM, on the other hand, is a process in which an electrode shaped to the desired shape is brought close to the material and processed in a carving manner. It is suitable for machining deep grooves and corners, but its disadvantage is that it is costly and time-consuming to manufacture electrodes.
Molding process
Forming" is a process in which a mold is used to deform a material into a specific shape.
Since the mold is fixed, there is little variation in quality, making it suitable for mass production. Below are some typical methods of molding process.
press working
The word "press" means "pressing" in English. As the name suggests, "press working" is a method of processing materials by pressing them with a die.
Thin metal sheets such as steel and aluminum alloys are often used, suitable for lightweight and thin products. For example, spoons and coins are typical examples of press work.
Sheet Metal
Sheet metal processing" is a method of bending, drilling, and punching thin metal sheets between dies. It is mainly used for automobile and home appliance housings.
The use of presses allows for high-precision processing in a short time, resulting in shorter lead times and lower costs. In addition, the ease with which design changes can be accommodated makes it suitable for small-quantity, high-mix production and prototypes.
casting
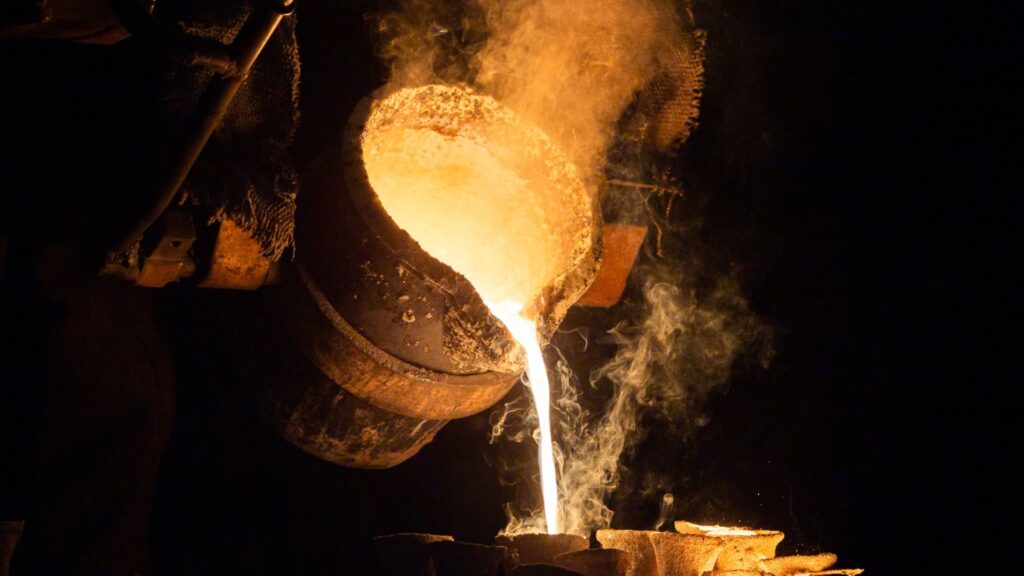
Casting" is a method of molding by pouring molten metal into a mold made of sand or metal.
Casting is characterized by the ability to produce large quantities of products with stable shapes and dimensions because the material is filled uniformly in the mold. It is often used for manholes, iron kettles, frying pans, etc.
forging
Forging is a process in which heated metal is sandwiched between molds and deformed by applying a large force.
Imagine the manufacture of Japanese swords. In Japanese swords, heated metal is beaten to shape, but in machining, a mold is used instead of a hammer to create the desired shape.
Forging makes the metal structure denser and stronger, making it suitable for products that require durability, such as automobile and aircraft parts.
bonding process
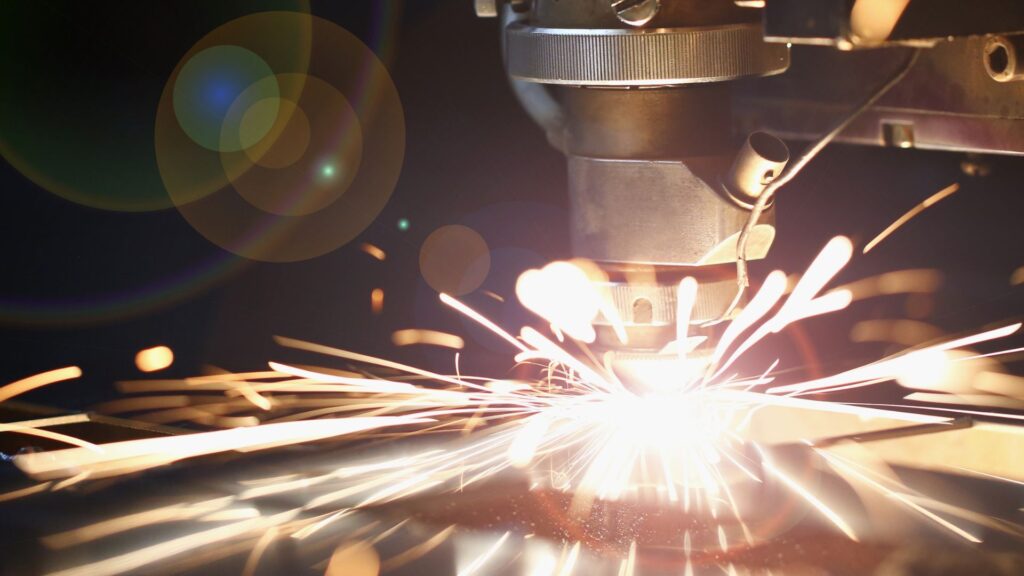
Joining" is a processing method for combining different parts or components to complete a single product. Simply put, it is a technique for "attaching things to things.
Joining processes are indispensable for producing products consisting of multiple parts or products requiring complex shapes and functions, and include the following types of processes.
weld
Welding" is a method of joining two materials by melting their joints, mixing the materials together, and then cooling them to form a single piece. Because the joint becomes very strong, it is used in situations where strength is required, such as in automobiles and construction machinery.
There are a number of welding methods, but the typical method is "arc welding. The high temperatures (approximately 5,000 to 20,000°C) generated by the electric current are used to melt and join metals. Since the temperature is higher than the melting temperature of most metals, it can be used for a wide range of materials.
Solvent adhesion
Solvent bonding" is a method of joining materials together using an adhesive.
Since no heat is generated during bonding, it is suitable for heat-sensitive materials or when heat-induced distortion should be avoided. Another feature is that different materials can be bonded to each other.
However, since the joint strength is lower than that of welding, it must be selected according to the application.
brazing
Brazing" is a method of joining materials by melting a metal with a low melting point and pouring it into the joint. It is easy to understand if you imagine "soldering," which you experienced in junior high school.
The advantage of brazing is that only the joint is heated, without melting the material itself. Since damage to the material is minimized, brazing is often used to assemble precision products or to join heat-sensitive materials.
Machine tools used in machining
Equipment used for machining is collectively called "machine tools. A wide variety of types exist, depending on the application and shape. The following is a list of typical machine tools.
lathe
A "lathe" is a machine in which the workpiece is mounted on a rotating base and a tool is applied to it for cutting. Since the tool is applied to the workpiece while it is rotating, this type of machine is particularly suited for cylindrical machining.
milling machine
A "milling machine" is a machine that shaves a material by rotating a blade. It is especially used to prepare flat surfaces.
Although it seems similar to a lathe, the difference is that in a milling machine, the cutting tool rotates, while in a lathe, the workpiece rotates.
boor-bank drilling machine
A drilling machine is a machine used for drilling and expanding holes. Although lathes and milling machines can also be used for drilling, the advantage of drilling machines is that they can drill more accurate and straight holes.
grinding machine
A grinder is a machine that uses a grinding wheel that rotates at high speed to shave the surface little by little. It is also called a "grinder.
It is utilized for surface finishing of crankshafts, bearings, and other automotive parts.
press machine
A "press" is a machine that forms materials by applying pressure from above and below. It is suitable for mass production because it allows quick processing with simple movements.
Another advantage is the use of molds, which ensures stable quality.
Die casting machine
A die casting machine is a machine that injects molten metal or alloy into a mold for molding. They are speedy because they pour at high speed and high pressure, and are suitable for the manufacture of home appliances and automotive parts, which require mass production.
welding machine
Welders" are machines that use heat and pressure to join parts together. The most common type is the "arc welder," but other types include "MIG welders," "TIG welders," and "laser welders.
Electrical Discharge Machine
An electric discharge machine is a machine that melts and processes metal using heat generated by electric discharge. Electricity is generated between the metal and the machine, and the material is melted and processed at temperatures of 5,000°C or higher. It is especially suited for hard materials.
machining center
A machining center is a machine equipped with a function that automatically changes a variety of tools and performs multiple machining operations in succession. Since multiple machining processes, such as drilling and cutting, can be completed on a single machine, it is used in the manufacture of a wide variety of products.
The system is also efficient and cost-effective because it does not require manual tool changes.
Summary
In this issue, we have explained the basics of machining, specific machining methods, and types of machine tools. Machining is an important technique for shaping materials into desired shapes, and there is a wide range of options.
Therefore, it may not be easy for development personnel to understand all the methods and find the best processing method for their products.
We therefore recommend Taiga.
Taiga provides experienced engineers and technicians to suggest development methods so that projects can be carried out efficiently. It also has a chat function for real-time conversations among project members and a 2D drawing sharing and editing function.
Taiga is free of charge and we encourage you to experience it for yourself.
Receive technical proposals at Taiga