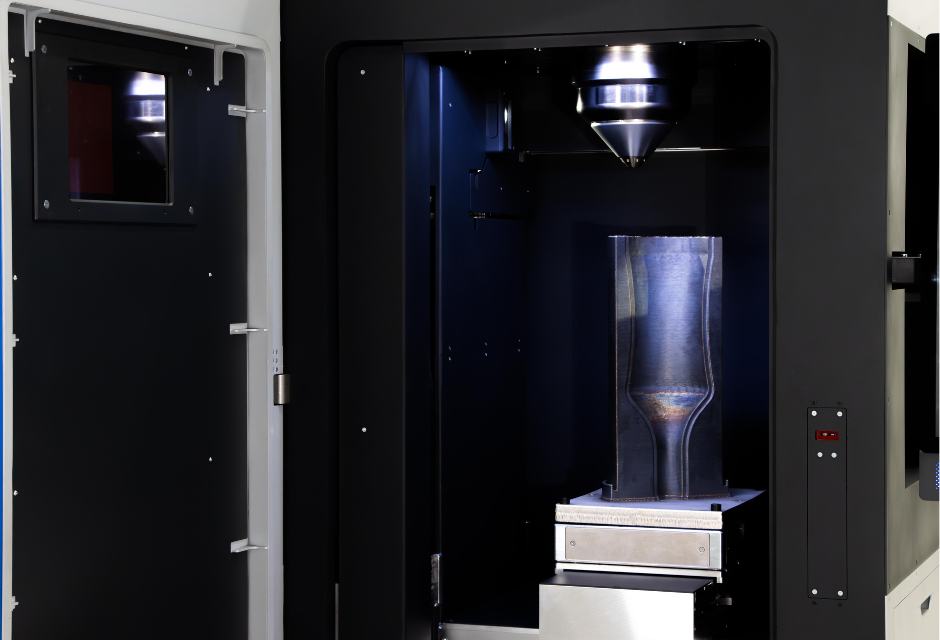
As an innovative manufacturing technology, metal 3D printing is at the forefront of product development.
It is becoming a major option for many manufacturers because of its ability to achieve complex shapes and a high degree of design freedom that cannot be achieved with conventional machining methods.
This article therefore provides a thorough explanation of metal 3D printing, from its structure to its advantages and disadvantages, to provide useful knowledge for those in charge of product development.
For more information about Taiga, click here.Table of Contents
What is Metal 3D Printing? How Metal Printing Works
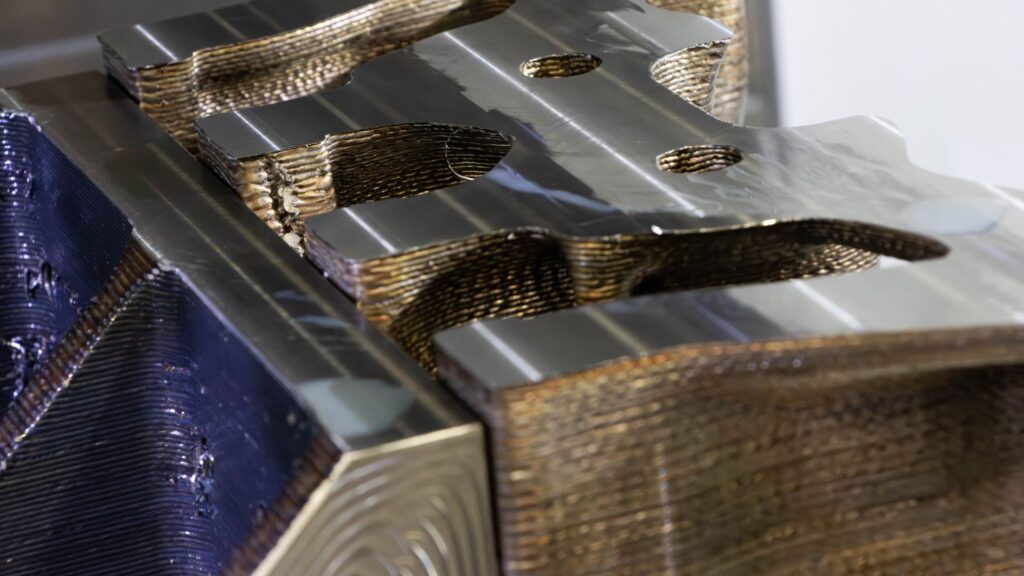
Metal 3D printing is a technology to create three-dimensional objects by layering metal powders based on 3D CAD data.
The powder bed forming (PBF) method is often used for molding, in which metal powders are stacked in layers while melting and solidifying with a laser or electron beam.
Metal powders such as stainless steel and titanium alloys can be used, and complex shapes and hollow structures can be realized.
Another advantage is that it can produce high-strength, heat-resistant parts without the need for specialized molds.
Advantages of Metal 3D Printing
The benefits of metal 3D printing are explained.
Suitable for modeling complex shapes
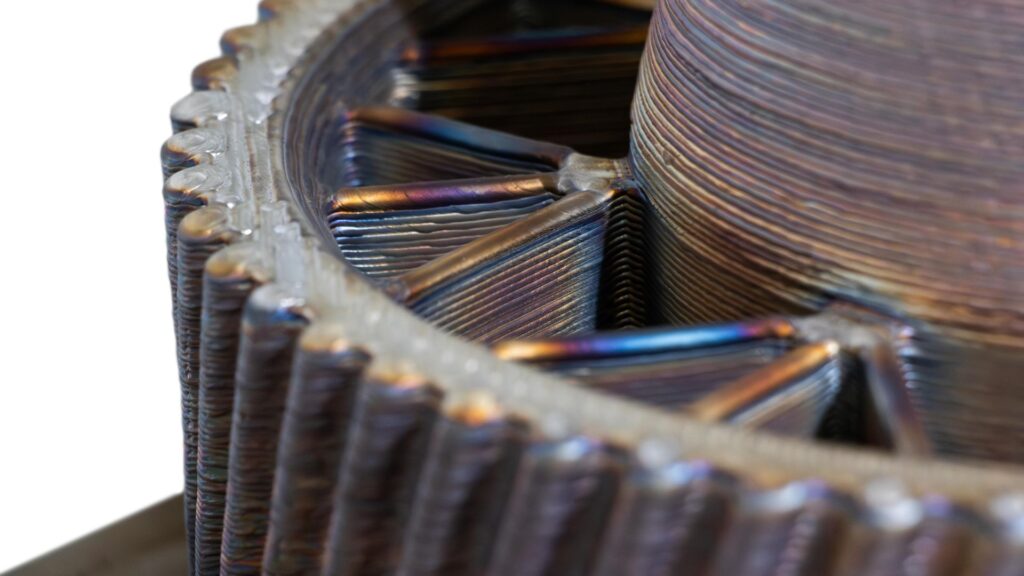
Metal 3D printers are capable of modeling complex shapes that are difficult with conventional metal fabrication.
By repeating the process of melting metal powder little by little with a laser, it is possible to form parts that cannot be reached with tools and shapes that cannot be formed by casting.
The high degree of freedom in design is also attractive, allowing for innovative modeling, such as lightweight hollow structures and mesh structures.
Can be formed by taking advantage of the characteristics of metals
Metal 3D printers can use a variety of metal materials to maximize product performance.
Using metal materials such as stainless steel, aluminum alloys, titanium alloys, and copper, we can manufacture parts with high strength and heat resistance that cannot be achieved with resin materials.
Any shape can be formed while maintaining the strength, heat resistance, and other characteristics required for the product.
Production costs can be reduced
Because 3D printing technology does not require the fabrication of molds, it can significantly reduce the cost of prototyping and low-volume production.
The ability to easily create prototypes reduces the cost of later modifications. In addition, the integration of parts and weight reduction can help reduce the cost of materials themselves.
Can reduce the weight of moldings
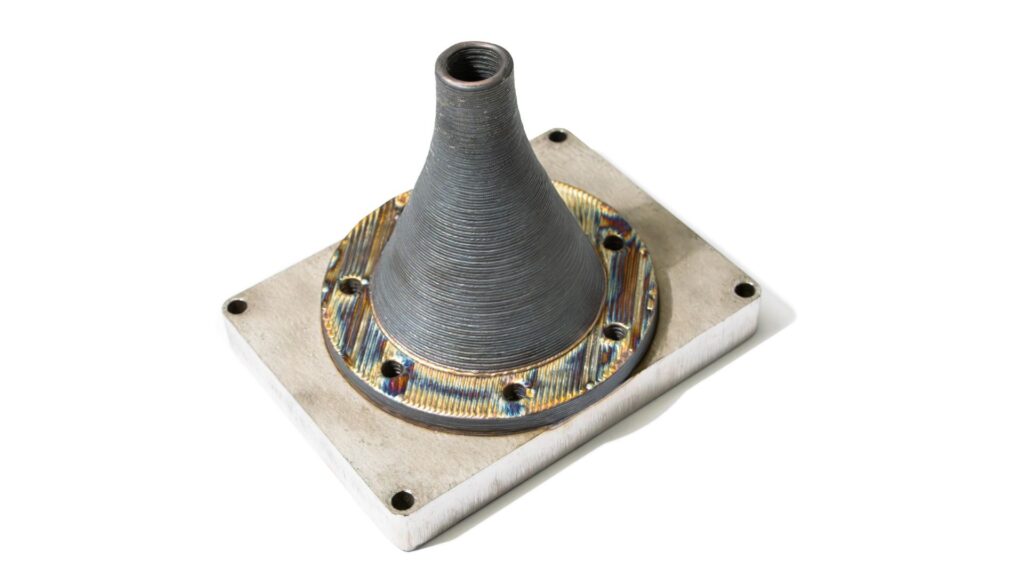
Metal 3D printers can also produce parts with internal structures such as hollow or lattice structures.
This makes it possible to reduce weight while maintaining strength.
In the manufacture of aircraft and automobiles, the ability to efficiently make parts with complex geometries, which was difficult to achieve with conventional methods, has made it possible to improve product performance while reducing the number of parts.
Disadvantages of metal 3D printing
On the other hand, metal 3D printing has some disadvantages.
Accuracy of molding is coarse.
The accuracy of metal 3D printing is inferior to that of conventional machining, with a limit of about ±0.1 mm in actual measurement.
Therefore, keep in mind that post-processing is required for areas where higher precision is required.
Since additional processes may increase labor, time, and manufacturing costs, the accuracy required for the product and the characteristics of the technology must be carefully considered.
Limited in size and production volume
Current metal 3D printers are limited in the size of parts that can be produced, and multiple parts must be combined to produce large products.
Also, since the products are sculpted one at a time over time, it is not suitable for mass production. If you are aiming for mass production, keep in mind that it takes longer than other manufacturing methods.
Requires know-how in design and print setup
Effective use of metal 3D printing requires 3D CAD operating skills and expertise in modeling.
Specifically, a wide range of know-how will be required, including the design of appropriate placement and support structures, understanding of the characteristics of modeling methods, and the use of specialized software.
Without this knowledge, it is important to work with specialized contractors and designers, as it will be difficult to create and design a production method that meets your objectives.
High installation and running costs
The introduction of a metal 3D printer requires a high initial investment, with the cost of the main unit alone amounting to more than 30 million yen.
In addition, significant costs will be required to develop the installation environment, including inert gas supply and discharge facilities, dust and explosion-proofing measures, and dedicated space.
In addition, the running costs for the metal powder used as material and maintenance are high.
When considering the implementation of metal 3D printing, these costs should be evaluated comprehensively.
Types of metal 3D printing
Here are five types of metal 3D printing.
PBF system
The PBF method is the most common metal 3D printing technology, in which 10-60 μm metal powder is irradiated with a laser or electron beam to melt and solidify layer by layer.
It is capable of high-precision modeling, but the modeling speed is slow and is not suitable for large-size modeling.
There are two types of beams, laser and electron beam, each with different characteristics, making it possible to work with a wide variety of metal materials.
DED method
In the DED method, metal powder or wire is injected through a nozzle and simultaneously melted and stacked by a laser.
Suitable for large parts and repair of existing parts. Large-scale modeling is also possible by adjusting the length of the X, Y, and Z axes.
It requires less post-processing and can mold dissimilar metals, but is less accurate than the PBF method.
FDM
The FDM method is a metal 3D printing technology that melts and laminates filaments containing metal powder.
Since the material is a mixture of resin and metal, degreasing and sintering processes are required after lamination.
While it is relatively inexpensive and easy to handle, the strength and density of moldings are inferior to other methods.
In addition, design and post-process sintering operations must take into account shrinkage during modeling.
Binder jet method
The binder jet method is a method in which adhesives are injected into metal powders to harden them and later sintered.
After molding, the adhesive is removed, and the product is completed through a degreasing and sintering process.
It has a high molding speed and is suitable for large moldings, but there are issues with accuracy and strength.
Typical Applications for Metal 3D Printing
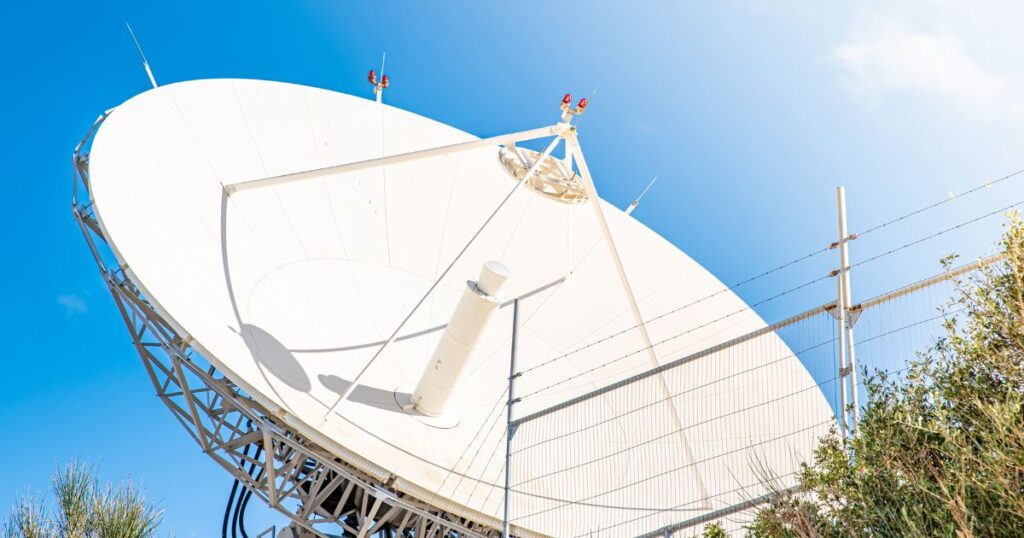
Metal 3D printers are primarily used in the following areas
- aerospace industry
- medical equipment
- Die and mold industry
- automotive industry
- industrial machinery
In the aerospace industry, it is used to manufacture lightweight and complex-shaped components such as diesel fuel injectors and antennas for small satellites.
Other applications include patient-optimized implants and molds with 3D cooling water tubes.
With its high precision and efficiency, it is attracting attention as a next-generation manufacturing technology that will bring new possibilities to various industries.
Summary
Metal 3D printing is a technology that has the potential to revolutionize the manufacturing industry.
However, maximizing the benefits of metal 3D printing requires the selection of an appropriate modeling method and expertise.
When considering the introduction of 3D printing, it is important to fully understand the company's product development needs and the characteristics of metal 3D printing, and to select an appropriate method.
By working with a trusted supplier with expertise, you will be able to develop products that take full advantage of the benefits of metal 3D printing.
If you are considering manufacturing parts using 3D printing, please contact us! Taiga is a free service that allows you to consult with experienced contractors.
We can efficiently proceed with the development of difficult or new parts, small-lot production, prototyping, and mass production while keeping costs low.
For more information about Taiga, click here.