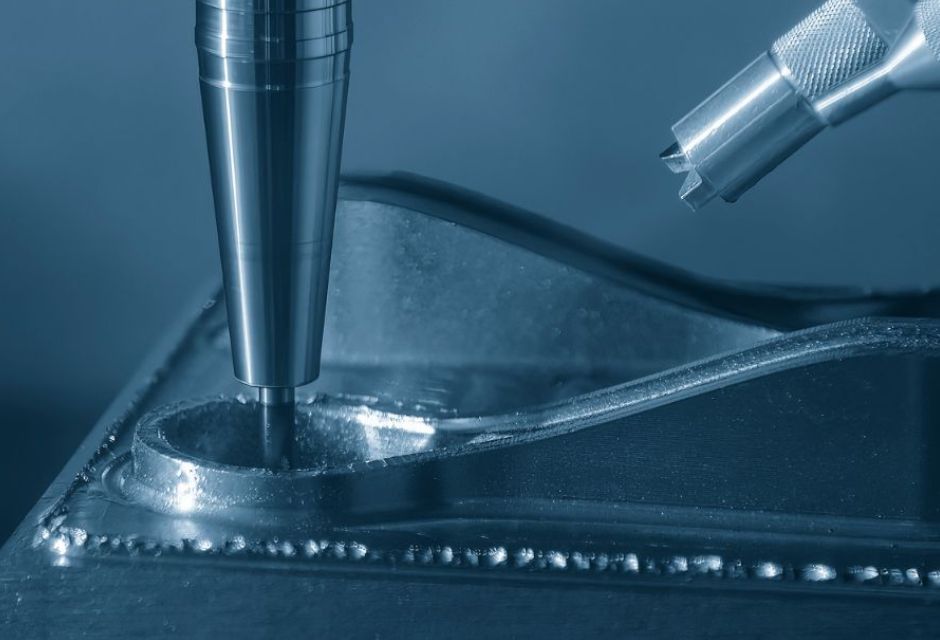
Injection molding is a processing method used primarily in the molding of plastic products.
Recently, however, it is also gaining attention as a forming method for metal products and parts.
This article will provide an overview of metal injection molding, its differences from similar molding methods, and its advantages and disadvantages.
Please refer to the metal injection molding procedure as well.
For more information about Taiga, click here.Table of Contents
What is Metal Injection Molding?
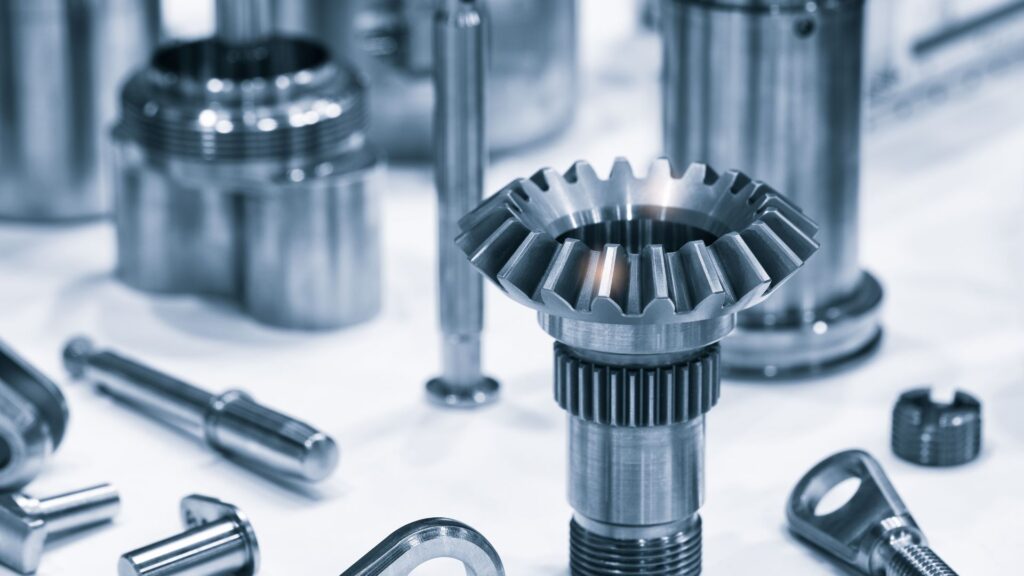
Metal injection molding is a molding method that combines and applies resin injection molding and metal powder metallurgy technologies.
The English term "Metal Injection Molding" is sometimes translated as "MIM.
Unlike general resin injection molding, injection molding is performed using 10 micron-level fine metal powder as the raw material, with no melting, but by adding a connecting element.
Therefore, even materials that are difficult to process, such as titanium and stainless steel, can be processed into complex shapes.
Metal injection molding is one of the molding methods that have been attracting attention in recent years, with the potential to be employed in the manufacture of parts for automobiles, precision machinery, electrical equipment, communications equipment, and medical devices.
Difference between casting/forging and metal injection molding (MIM)
Casting and forging are also methods of shaping metal using molds.
Casting is a technique in which molten metal is poured into a mold and then cooled to harden.
Forging refers to a method of forming ingots by clamping them in a die and pressing and stretching them.
Metal injection molding is a completely different molding method, as metal powder and resin are mixed and injection molded in a mold.
Difference between sintered alloy and metal injection molding (MIM)
Sintered alloys are formed by pressing metal powders.
Metal injection molding uses molds to perform injection molding, which is more precise than sintered alloys and allows for more complex shapes.
Advantages of Metal Injection Molding (MIM)
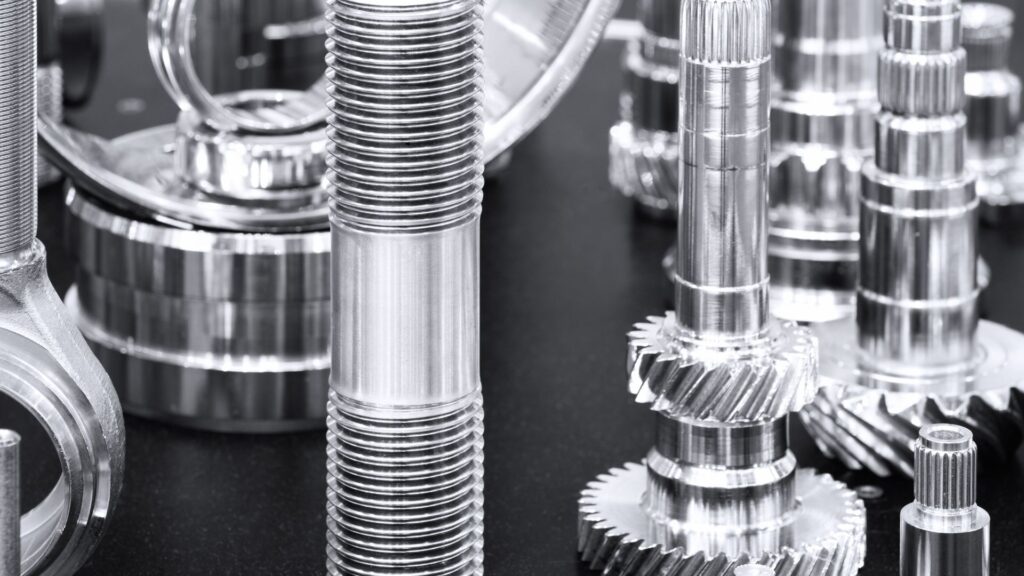
There are many advantages unique to metal injection molding.
Complex shapes can be formed from difficult-to-machine metals.
Metal injection molding can also be used to process the following difficult-to-machine materials that are difficult to cut.
- tungsten carbide metal
- titanium (Ti)
- stainless steel
- Tungsten, etc.
In addition, metal injection molding does not generate chips and material loss.
Even with expensive materials, processing can be achieved with material efficiency in mind.
Suitable for mass production
Metal injection molding uses molds, making it suitable for mass production. Once a mold is made, even difficult-to-process materials can be produced in a short time.
Another advantage is that complex shapes can be easily processed by using molds, allowing for mass production while reducing costs.
High-precision machining is possible.
Metal injection molding is capable of high-precision processing because it does not dissolve the material, but instead dewaxes and sinter the molded part. It is also suitable for manufacturing parts that require high quality and high precision, such as parts with uniform standards.
Disadvantages of Metal Injection Molding (MIM)
While metal injection molding has many advantages, it also has disadvantages.
Know-how is required to set molding conditions
While the materials used in metal injection molding have high fluidity, they tend to solidify easily due to their high thermal conductivity.
Therefore, the following molding defects are likely to occur, and accurate molding condition settings are required for stable molding.
Common molding defects | condition |
short shot | Material does not fill the mold sufficiently |
burr (e.g. on a machined edge) | Material protrudes from the joints of the mold |
Japanese dock (plant) (Rumex japonicus) | Material shrinks during cooling |
weld line | Lines occur at the confluence of materials |
void | Hollow space inside the product |
marks indicating the Japanese meaning of the texts of Chinese classics | Product is bent. |
flow mark | Traces of flow appear on the surface of the product |
jetting | Material sprays into the mold and splashes out. |
Since it is more difficult to set molding conditions than general injection molding, advanced technology and know-how are essential for processing.
Secondary processing is required in some cases.
In metal injection molding, burrs and shorts occur during processing, and in some cases secondary processing is required.
Secondary processing naturally requires more labor and time, so costs will be higher than for general injection molding using resin materials.
Another disadvantage of metal injection molding is that non-product parts such as sprues and runners are molded.
Be aware that additional costs may be incurred due to secondary processing needs and material waste.
Not suitable for small-volume production
Metal injection molding is not suitable for low-volume production because of the use of molds.
Since the fabrication of a mold involves not only costs but also a creation period, a certain amount of production time and initial costs are incurred even for small-quantity production.
As an extreme example, even if you want to make only one part, you need to make a mold, which is not suitable for low-volume production.
Design constraints.
Metal injection molding requires a design that takes into account the draft angle to remove the product from the mold.
In addition, large injection molding machines and molds are required to mold products of larger sizes.
Even if the design constraints could be met, production costs would likely be higher.
Metal injection molding (MIM) procedures
The following is a description of the metal injection molding process steps.
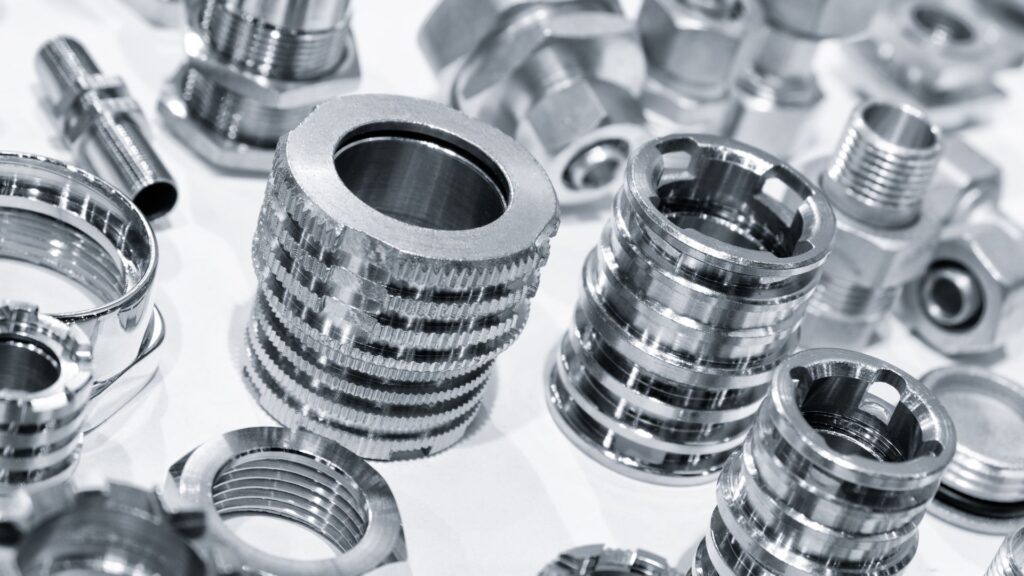
kneading
First, the raw metal powder and organic binder (binder) are uniformly mixed together under heat and pressure. The organic binder is a raw material consisting of a binder, a plasticizer with a wax component, and a lubricant.
This process is called "kneading.
granulation
Pelletizing is a process in which materials are mixed in a pelletizer and squeezed out under pressure to form pellets.
The material produced by granulation is called feedstock.
Injection Molding
Once the material is ready, injection molding is performed by the molding machine.
Items molded by metal injection molding (green parts) are made larger than originally required because they contain binders.
removal of fat
Degreasing is the process of removing wax components such as plasticizers and lubricants contained in the binder.
This can be done in one of the following three ways
Methods of degreasing | feature |
Solvent degreasing | Dissolve wax by solvent |
Thermal degreasing | Heat to evaporate wax |
Catalyst degreasing | Degreasing with catalyst gas while heating |
If proper degreasing is not performed, wax components will remain as carbon during the next sintering process, adversely affecting the composition of the metal.
In addition, parts after degreasing (brown parts) are prone to deformation and cracking due to the wax component being removed, and must be handled with care.
sintering
After degreasing, brown parts are heated in a sintering furnace and sintered.
Sintered parts are called silver parts and are characterized by a smaller volume due to the loss of the binder.
secondary processing
Secondary processing such as sizing (coining) is performed as necessary for thread processing that requires high dimensional accuracy.
Metal injection molding materials can also be heat-treated, plated, painted, or otherwise surface treated in the same way as ordinary metal materials (wrought materials).
examination
In metal injection molding, the following inspections are performed depending on the part to be manufactured.
- Dimensional Inspection
- Inspection of sintering density
- chemical test
- Non-destructive testing (e.g. X-ray)
For example, chemical testing is used to control carbon content, and nondestructive testing is used to check for cracks and other internal destructions.
Summary
We have provided an overview of metal injection molding, its differences from other molding techniques, its advantages and disadvantages, and its procedures.
Metal injection molding is the molding method of choice for mass production of high-precision metal products.
On the other hand, high technology is required to generate and manage materials, and the creation of molds involves time and cost.
In order to achieve satisfactory product manufacturing with metal injection molding, it is important to select and hire a processor with a proven track record.
If you are considering manufacturing parts utilizing injection molding, please contact us.Taiga."Taiga is a free service that allows you to consult with experienced contractors.
We can efficiently proceed with the development of difficult or new parts, small-lot production, prototyping, and mass production while keeping costs low.
For more information about Taiga, click here.