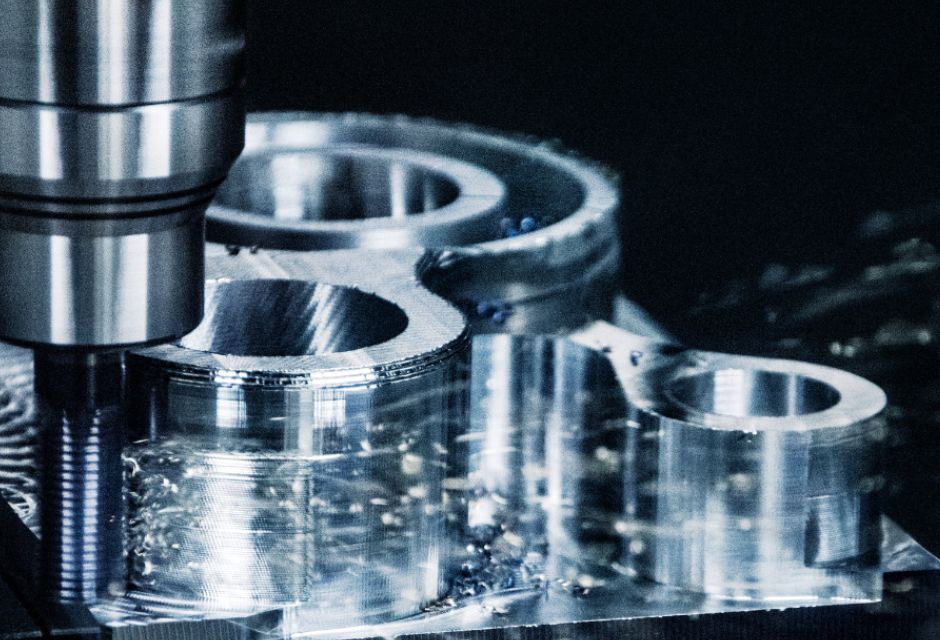
Milling is one of the most accurate metalworking processes. Therefore, many people are considering manufacturing products by milling. However, some people may have questions such as, "What are the advantages and disadvantages of milling?" or "What kind of machining can be done?" and "What kind of machining can be done?
In this article, we will discuss the advantages and disadvantages of milling, as well as the types of machining and tools used.
For more information about Taiga, click here.Table of Contents
What is milling?
Milling is a machining process in which a metal is shaved into a desired shape by a blade rotating at high speed, and is also called milling process.
The advantage of using different cutting tools is that they can be used for various machining operations.
For machining, we mainly use a machine called a milling machine and cutting tools appropriate for the material.
There are two types of milling machines: vertical milling machines, which have a vertical spindle for mounting tools, and horizontal milling machines, which have a horizontal spindle.
What is the difference between turning and milling?
To a processing method similar to milling,Lathe MachiningThere are The differences between turning and milling are as follows
Lathe Machining | milling | |
processing method | Processing by pressing a fixed cutting tool against a rotating material | Processing by pressing a rotating cutting tool against a stationary material |
Cutting tools used | byte | End mill front face milling cutter |
Processing specialties | Machining of outer circumference and inner surface of cylindrical objects | Plane linear groove |
Advantages of Milling
Milling offers the following advantages
- Can be processed into a wide range of shapes
- Finish processing is also available
Milling can be used to form shapes that are difficult to form with other machining methods, provided that the tools used are appropriate.
In addition to cutting materials, it can also perform finishing operations to smooth the surface of processed products.
Disadvantages of milling
The disadvantage of milling is that some shapes, such as triangular shapes, cannot be formed.
Although some measures can be taken by devising processing methods, keep in mind that there are limitations.
Milling Types
The features of each type of milling process are described in turn.
plane-turning
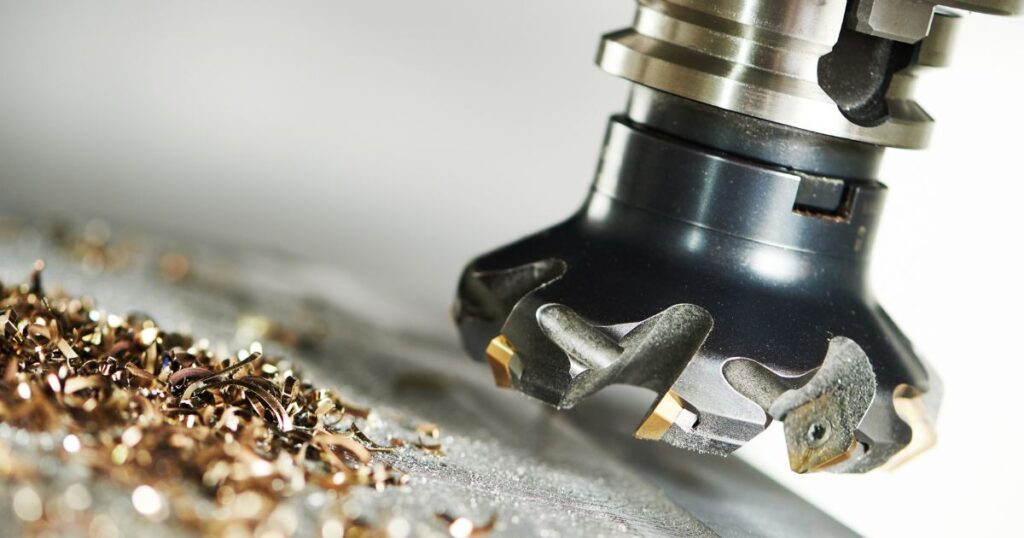
Flat milling is a milling process to cut a flat surface of material.
Machining is performed on a vertical milling machine with a front face milling cutter and end mill.
Even with a horizontal milling machine, flat surface machining is possible if a flat milling machine is attached.
However, there is a disadvantage that the spindle projection tends to be longer, making it difficult to ensure surface accuracy.
side processing
Side milling is a milling process to cut the side of a material.
Cutting is performed with the outer edge of an end mill attached to a vertical milling machine.
If the area to be machined is large, it is possible to attach a front milling machine to a horizontal milling machine.
Step and step machining
Step machining (step machining) is a milling process that uses an end mill or side milling cutter to create a step in the material.
When wide, shallow steps are desired, a vertical milling machine can be used with a front face milling machine to cut a large area for efficient machining.
When making a step with a difference in height, it is common to use an end mill on a vertical milling machine and a side milling machine on a horizontal milling machine.
hole processing
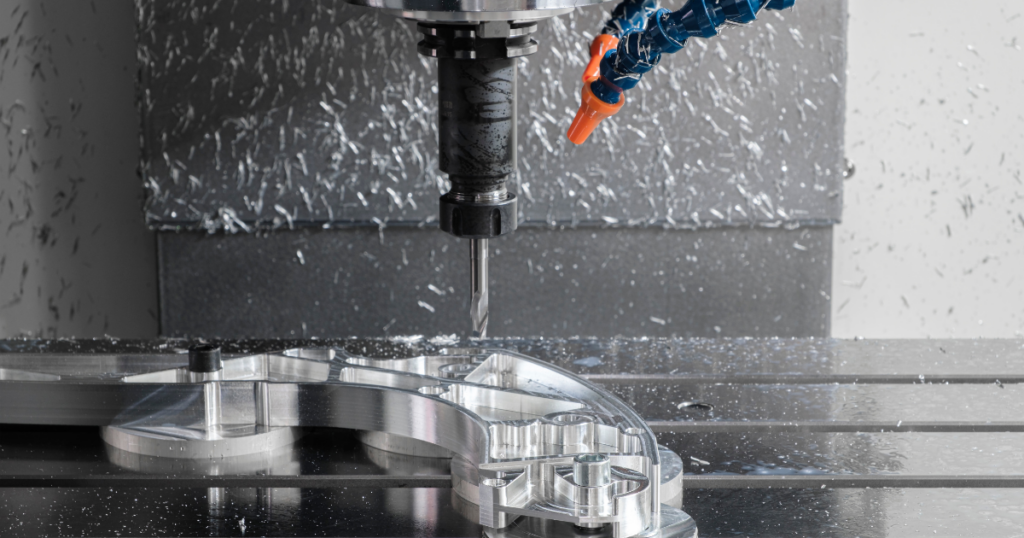
Hole drilling is a process in which holes are made in a material using tools such as drills and reamers.
In addition to drilling, we also offer boring and internal finishing.
Groove processing
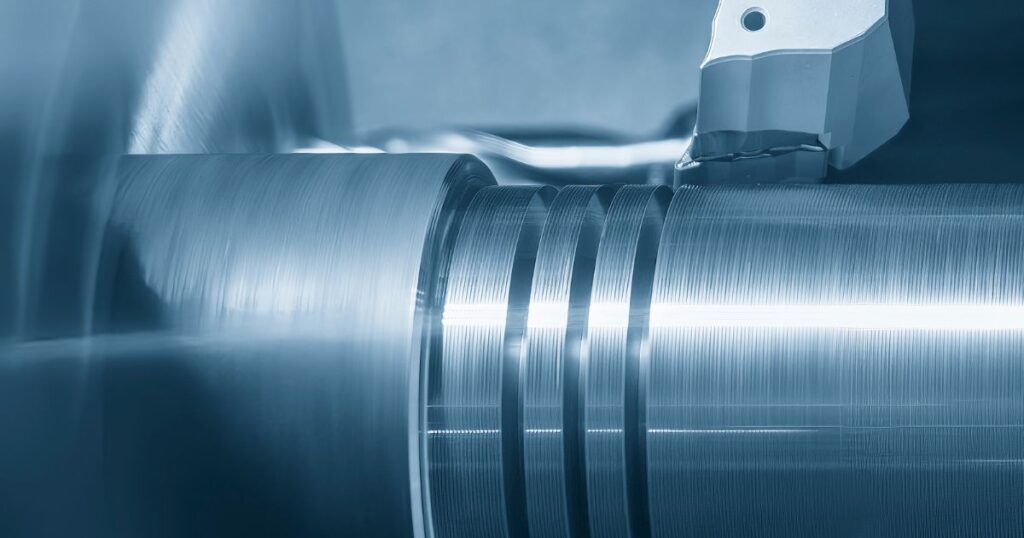
Grooving is a process to dig a groove in a material.
By using different tools, a wide range of groove types can be machined, including
- Pocket machining to make a square recess with an end mill
- Helical machining to create a round recess with an end mill
- Keyway machining to secure parts rotating with end mills
- T-slot milling for bolt fitting applications
- Dovetail milling with dovetail milling machine
Curved surface processing
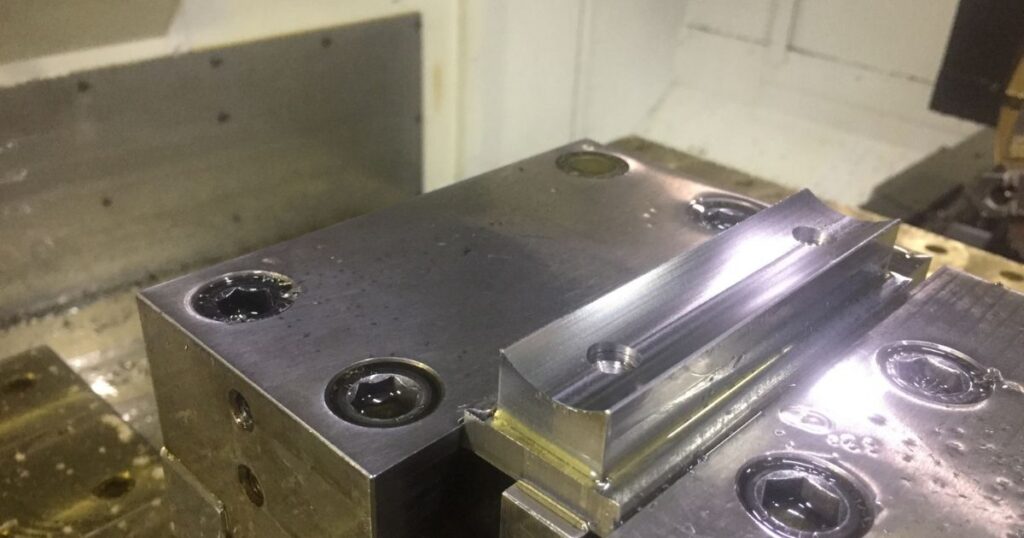
Curved surface machining is a machining method to form complex three-dimensional shapes, also known as three-dimensional machining.
Curved surfaces can be machined by moving the material back and forth and the tool up and down.
For more complex shapes, programmed NC milling machines and machining centers are sometimes used.
Four machines used for milling
Milling is also characterized by the use of a variety of machines depending on the material and the shape to be processed.
The following is a step-by-step explanation of the features of the four machines used in the milling process.
General-purpose milling machine
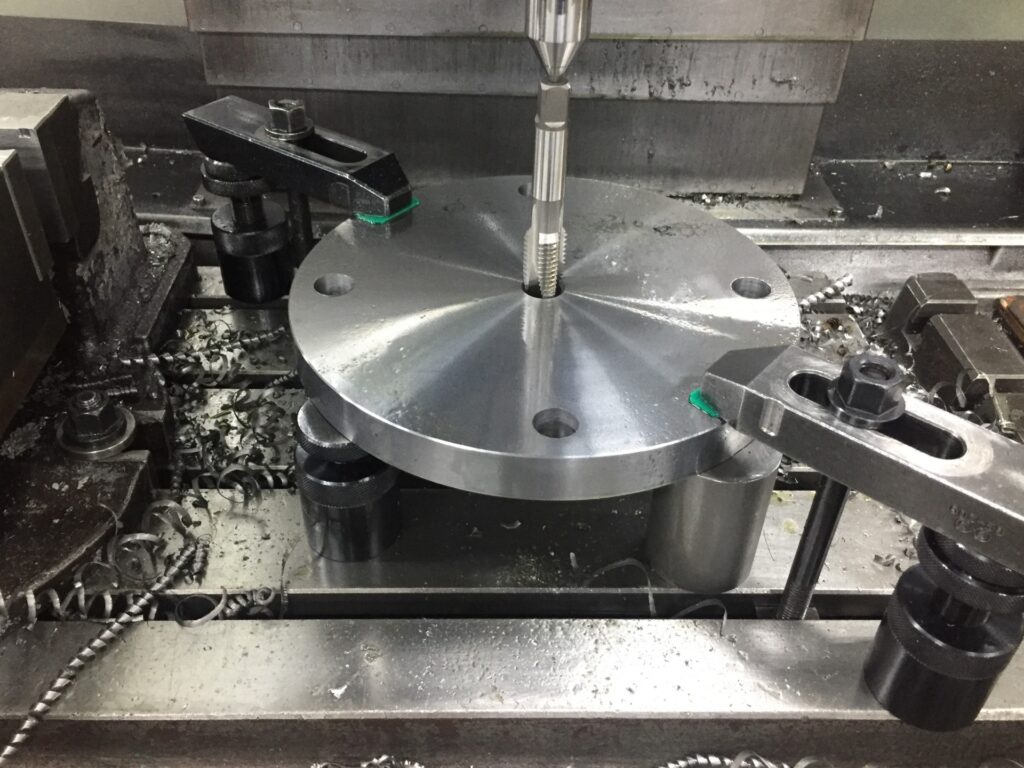
A general-purpose milling machine is a milling machine that is manually operated by the operator with cutting tools attached.
Because general-purpose milling machines are manually operated, the workmanship varies depending on the operator's experience and skill.
High precision and high quality finish is possible when machined by skilled workers.
NC milling machine
NC milling machine (Numerical Control) is a milling machine that uses a computer to numerically control the conditions for machining.
The NC milling machine is not dependent on the skill of the operator, as machining proceeds according to the program.
Adjustment of each process is also controlled numerically rather than manually, enabling more stable machining accuracy than with general-purpose milling machines.
machining center
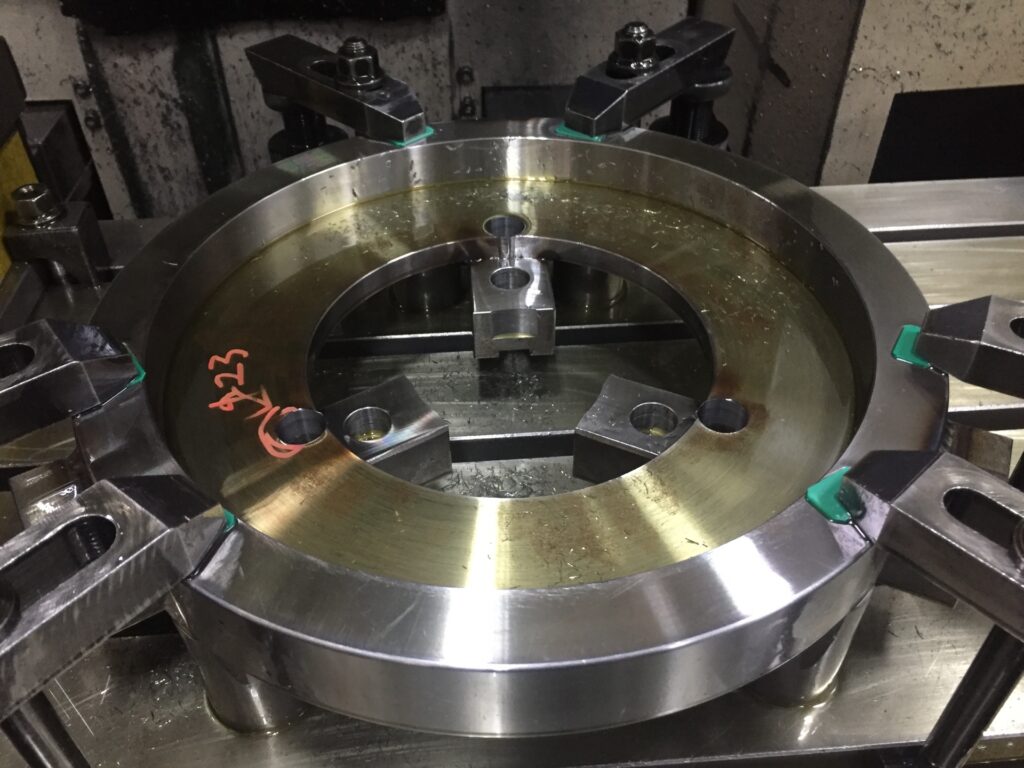
Machining centers are NC milling machines that can be numerically controlled and are equipped with an automatic tool change function.
Conventional milling machines can only attach one tool, but machining centers can set multiple tools at the same time.
The advantage is that manual tool changes are not required, making milling more efficient.
NC Gear Cutting Machine
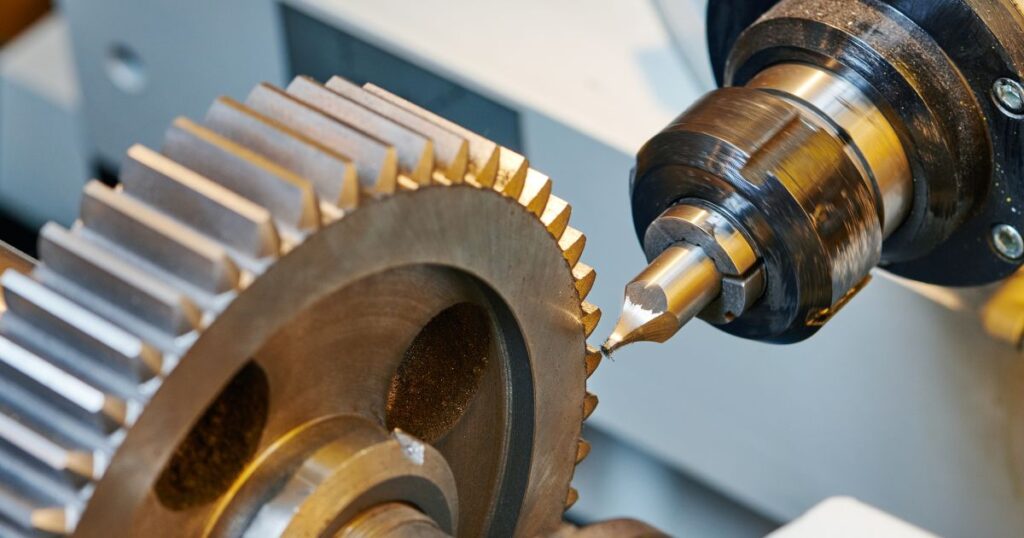
NC gear milling machines are milling machines used for gear machining.
The process is performed by rotating a special cutting tool called a "hob."
NC gear cutting machines can easily adjust the number of teeth to be machined, the shape and size of the gear, and can be used to machine the following gears.
- spur gear
- helical gear
- Worm gears, etc.
Five tools used in milling
In milling, various machining processes are possible by changing the tools to be installed.
This section describes the characteristics of the five tools used in milling.
frontalis milling
A face milling tool is a tool with multiple cutting edges around the circumference of a circle, also called a face mill.
It is mainly used on vertical milling machines and is one of the most used tools in milling operations.
Face milling machines flatten the surface of the material by rotating and moving in parallel.
The advantage is that a wide area can be shaved at a time, allowing for efficient machining.
flat milling machine
A flat milling cutter is a cylindrical tool with a blade on its outer circumference.
Attached to horizontal milling machine for flat surface machining.
Compared to frontal milling, it features higher cutting efficiency but lower accuracy.
Therefore, it will most likely be used for rough machining.
ditch milling cutter
A groove milling cutter is a tool with a circular blade that rotates at high speed and, as the name implies, is used to create grooves in machining. It has a higher cutting speed than groove milling using an end mill and enables high-precision machining.
It is used when many long, deep grooves are desired because it can efficiently create clean grooves.
side milling cutter
A side milling cutter is a disk-shaped tool with cutting edges on the periphery and both sides, also called a side cutter.
It is attached to horizontal milling machines and used when machining grooves and side faces.
There are also different types of side milling cutters, such as the grated milling cutter, which is suitable for slit-like grooving, and the metal saw, which has a thinner thickness from the center to the cutting edge.
endmill
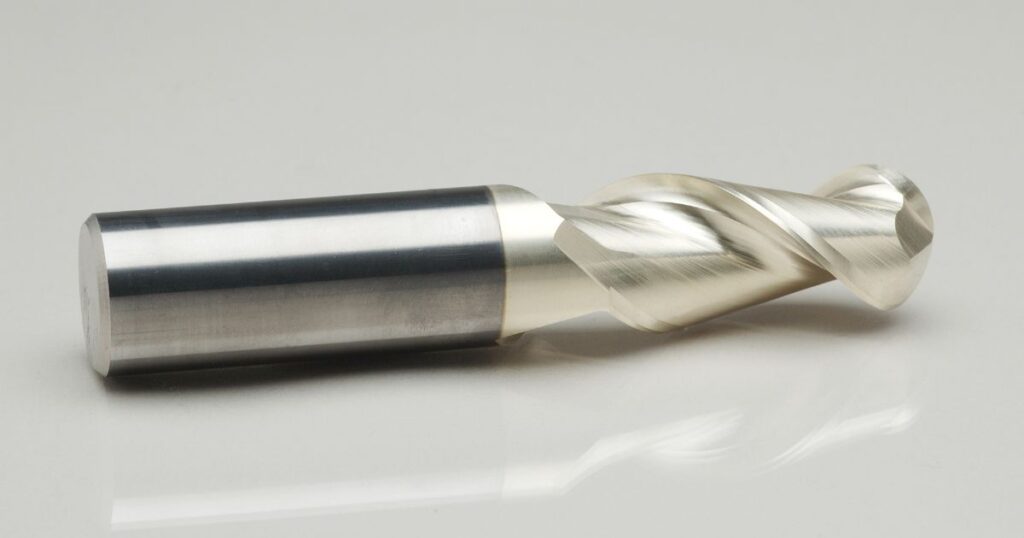
End mills are long, slender, drill-like tools that can be used for a variety of machining operations, including flat, step, and groove machining.
The advantage is that a single tool can process a wide range of shapes, eliminating the need to change tools.
There are several types of end mills, including square end mills with flat tips and ball end mills with spherical tips that excel at machining curved surfaces.
Summary
This article provides a detailed overview, advantages, and disadvantages of milling.
Milling can be performed in a wide range of machining processes by using a variety of tools and machining methods.
If you are looking for a way to manufacture products that could not be made with other processes, consider milling.
If you are considering manufacturing parts utilizing the milling process, please contact us.Taiga."Taiga is a free service that allows you to consult with experienced contractors.
We can efficiently proceed with the development of difficult or new parts, small-lot production, prototyping, and mass production while keeping costs low.
For more information about Taiga, click here.