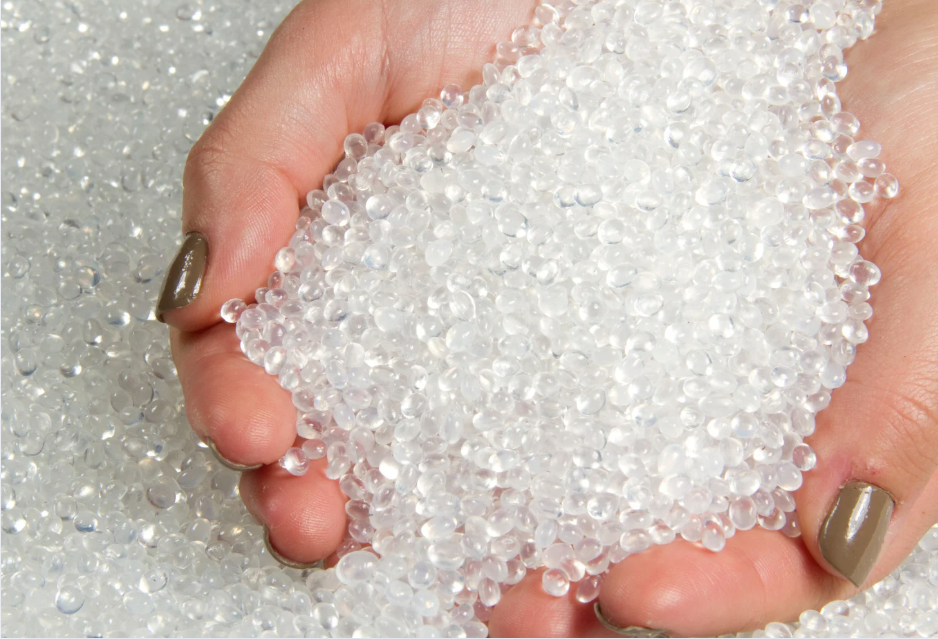
PEEK is one of the high-performance super engineering plastics.
When you are considering manufacturing a product using PEEK as a material, you may be asking yourself, "Is PEEK suitable for cutting? Cutting or injection molding? or "Which is better suited for cutting or injection molding?
This article provides an overview of the cutting process for PEEK and its advantages and disadvantages.
Please refer to the following section for an explanation of key points and precautions to be taken when cutting PEEK.
Receive technical proposals at TaigaTable of Contents
What is PEEK? High performance resin suitable for cutting process
PEEK (Poly Ether Ketone) is a high-performance super engineering plastic called poly ether ether ketone resin.
It boasts excellent resistance to friction, heat, and radiation, including heat resistance up to 260°C.
It has excellent hardness, mechanical properties, flame resistance, dimensional stability, and insulation properties, as well as the highest chemical resistance of any engineering plastic.
Taking advantage of its characteristics, it is often used as a component for parts in environments where solvents or corrosive gases are used or where high temperatures are reached, such as automobile and aircraft parts.
Difference by PEEK grade
The properties of PEEK vary depending on the grade.
The differences by grade are as follows
grade | feature | Main PEEK types |
Standard grade (natural grade) | Excellent machining accuracy with high basic performance | PEEK 90GPEEK 151GPEEK 381GPEEK 450GPEEK-HT G22 |
Glass fiber reinforced grade | Reinforced with glass fiber for greater strength and rigidity than other grades | PEEK 90GL30PEEK 150GL30PEEK 450GL30 |
Carbon Fiber Reinforced Grades | Reinforced with carbon fiber for greater strength and rigidity than other grades | PEEK 90CA30PEEK 150CA30PEEK 450CA30 |
High sliding grade | Carbon and PTEF compounding Enhanced for ease of movement while slipping and sliding | PEEK 150FC30PEEK 450FC30 |
Advantages of PEEK Cutting Process
Although PEEK is a difficult-to-machine material among engineering plastics, it is easier to cut than metals.
This section describes the various benefits of cutting PEEK.
High-precision, high-quality finishing is possible
Cutting allows machining with high precision in both dimensions and surface roughness because there are no thickness restrictions on the material as long as the machine can handle it.
This makes PEEK suitable for processing in fields that require micron-level precision, such as semiconductor devices, medical equipment, and electronic components.
Fast delivery and low-cost production
Cutting does not require the fabrication of dies, which is necessary for casting and forging processes.
There is no need for the time and costs incurred in mold fabrication, and fabrication can be done immediately with 3D-CAD data.
In particular, we can provide fast turnaround and low-cost production for small-lot production of PEEK-based products and prototypes.
High flexibility in processing
In addition to having no restrictions on material thickness, cutting is characterized by a high degree of machining flexibility due to the availability of various machining tools such as "5-axis milling machines" and "multi-axis (multitasking) machines.
In addition to the top surface, the machine can process PEEK from the front/back and right/left sides, enabling PEEK to be processed into more complex shapes.
Disadvantages of PEEK cutting process
While cutting PEEK has its advantages, it also has its disadvantages.
This section describes the disadvantages of cutting PEEK that you should keep in mind.
Cost is higher for mass production.
The disadvantage of cutting is that it is more expensive for mass production.
Cutting process produces chips, which are wasted material, because the process is carried out while cutting the material.
Chips can be difficult to reuse, and if the material itself is expensive, the cost is likely to be high.
In addition, the greater the amount of cutting, the longer it takes to process, which further reduces production efficiency when complex shapes or high precision is required.
Although the time and costs incurred in mold fabrication are unnecessary, it is important to remember that the processing method using molds is often more cost-effective for mass production.
Workmanship is easily influenced by the skill of the processing engineer.
Cutting PEEK requires a variety of skills, including knowledge of tool selection and processing techniques to produce high-precision products.
The more complex the product shape, the more complicated the machining procedure becomes.
Remember that even in the same cutting process, the skill of the operator can easily affect the workmanship.
It's hard to keep making the same thing.
Continuous cutting operations will cause wear on the cutting tools used, which will affect dimensions, surface roughness, etc.
Note that each machined part needs to be controlled in order to make the same thing by cutting with PEEK.
Difference between cutting and injection molding in PEEK
Since PEEK is a thermoplastic resin, injection molding is an option in addition to cutting.
The differences, advantages and disadvantages between cutting and injection molding in PEEK are compared below.
processing method | feature | Advantages | demerit |
Machining | Cutting, milling, and drilling workpieces using machine tools such as lathes, milling machines, and machining centers. | PEEK is also available for precision processing | Not suitable for mass production |
Injection Molding | A processing method in which soft materials are extruded into a mold and cooled and solidified to form a product. | Suitable for mass production | Surface accuracy is inferior to machining, making it difficult to create complex shapes |
Points to keep in mind when cutting PEEK
This section describes points to note when cutting PEEK.
Know-how is required to adjust cutting conditions
Due to the high hardness of PEEK, cutting tools may wear or chip if appropriate cutting conditions are not set during cutting.
If the blade is selected incorrectly, the blade itself may break.
Since adjusting cutting conditions and infeed methods requires know-how, it is important to request processing by a contractor with sufficient knowledge and skills.
In some cases, prior heat treatment is necessary to prevent distortion.
Depending on the shape of the item to be cut, the heat generated during the cutting process may cause distortion.
When cutting thin-walled parts and other distortion-prone shapes, heat treatment must be performed in advance.
Appropriate cutting tools must be selected.
Because PEEK is an extremely hard material, the tools used in cutting tools are subject to severe wear, a characteristic that tends to shorten tool life.
It is important to select tools that can cut PEEK stably, such as carbide cutting tools or tools with coatings that have high hardness.
Scenes in which PEEK cutting is used
The following list describes scenes in which PEEK cutting is used and specific products.
field | Specific Processing Examples |
medical industry | Bone fixation devices Healing caps Temporary abutment teeth Gingival former used during the healing phase of dental implants Catheters in the dental field Implant treatment devices, etc. |
aerospace industry | Aircraft Brake Systems |
food industry | Robot arm used in picking and packaging processes |
Summary
The following is an overview of the cutting process of PEEK, advantages and disadvantages of cutting, differences from injection molding, and points to note when cutting.
PEEK is easy to cut among engineering plastics, making it suitable for cutting when complex shapes or one-of-a-kind products need to be produced quickly.
However, cutting workmanship depends on the skill of the engineer and requires know-how in adjusting cutting conditions and selecting appropriate tools.
When considering cutting PEEK, consider hiring a contractor with strong technical capabilities and a proven track record.
If you are considering manufacturing high-precision plastic parts, please contact us.Taiga."Taiga is a free service that allows you to consult with experienced contractors.
We can efficiently proceed with the development of difficult or new parts, small-lot production, prototyping, and mass production while keeping costs low.
Receive technical proposals at Taiga