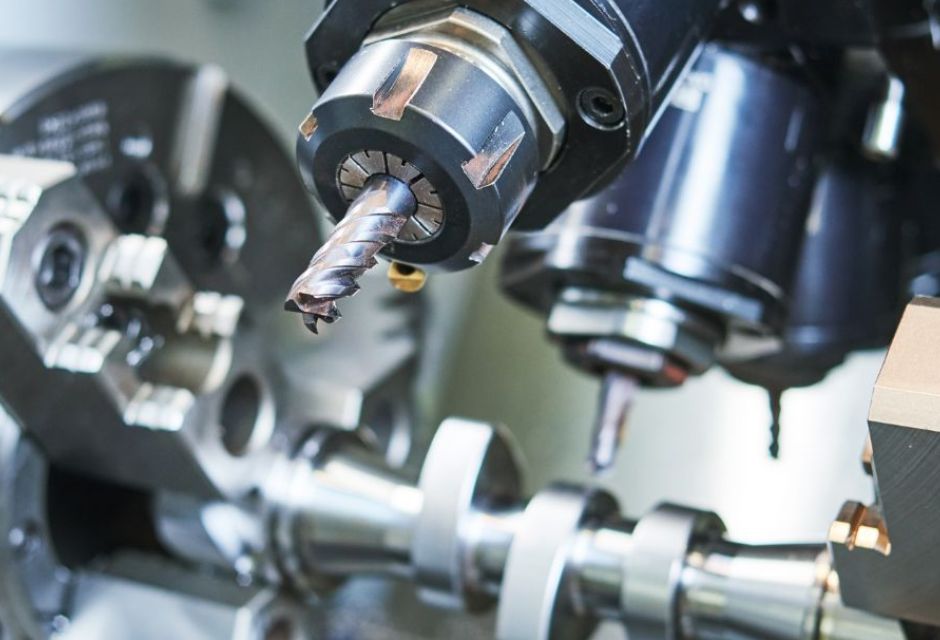
- I want to know the advantages and disadvantages of precision cutting.
- I want to know what materials can be used in precision cutting.
Many people are considering requesting precision cutting services but have these questions.
This article therefore provides an overview of precision cutting, its advantages and disadvantages, and the materials that can be used.
Please refer to this section for information on the difference between ultra-precision processing and nano processing.
Receive technical proposals at TaigaTable of Contents
What is Precision Cutting?
Precision cutting is a machining method that can achieve high-precision cutting.
First, we will explain each of cutting and precision machining.
What is Cutting

Cutting is a machining process that uses cutting machines such as milling machines and lathes.
Cutting blades are attached to the cutting machine, and the rotating blades cut the material into the desired shape.
The following types of cutting operations are available depending on the shape to be machined and the tools to be used.
- Drilling," using a drilling machine, lathe, or milling machine and a rotating drill to make a cylindrical hole in the material
- Boring" using a special bite (boring bar) to spread it wide
- Milling," in which a cutting tool is rotated to cut a fixed workpiece
- Flat shaving" in which the work piece is moved back and forth and a fixed waist-breaking tool is applied to shave a flat surface
- Form grinding" in which a horizontal reciprocating tool is applied to a fixed workpiece.
- Vertical cutting" in which a bite that reciprocates up and down is applied to a fixed workpiece.
- Broach cutting," a step-by-step cutting process using a tool called a broach
- Sawing," which uses a saw with a continuous blade to cut materials
In addition, major cutting applications include the following
- Trial production of draw molded products
- Small quantity production
- Deep-drawn thin plate products that cannot be simply manufactured
- When a notch is applied as a secondary process
precision machining
Precision machining, as the name implies, is a method of processing materials into desired shapes with a high degree of precision.
Specifically, the ability to make adjustments on a scale of approximately 1/1000 mm constitutes precision machining.
When it has a machining accuracy of 1/1000 μm, it is called ultra-precision machining and can be processed with an even finer system.
Advantages of Precision Cutting
The advantages of precision cutting are as follows
- Processing can be done in a short period of time due to no tooling time
- No tooling costs incurred
- Capable of processing a wide range of materials
- Complex shapes can be handled as long as the machine can handle them.
Precision cutting does not use dies in machining because the material is cut as it is.
This reduces the time and cost required for die fabrication, enabling shorter and lower-cost processing.
In addition to metals, high-precision processing can also be applied to plastics and wood.
There are no restrictions on thickness as long as the machine can handle it, so complex shapes can be processed.
Precision cutting is suited for small-lot production of prototypes and other products that need to be manufactured one by one with quality control.
Disadvantages of Precision Cutting
Precision cutting has the following disadvantages
- Not suitable for mass production
- Longer machining time depending on the shape to be machined
- Material costs due to swarf
- Need to manage blades
Precision cutting is not suitable for mass production because it does not use dies.
It takes a great deal of time and effort to cut and process each material one by one.
If mass production is required, the time required for processing will be longer and the cost will be higher.
In addition, precision machining always produces chips because of the cutting of the material.
Depending on the shape and size of the material to be machined, a large amount of chips may be generated, resulting in higher material costs.
Besides, depending on the frequency of machining and the material, the cutting machine blade will wear out. Proper management of cutting tools is also required to maintain high precision and to finish products to the designed dimensions.
Materials capable of precision cutting
Precision cutting is available for a wide range of materials, including
- aluminum (Al)
- stainless steel
- iron
- brass
- titanium (Ti)
- hardened steel
In addition, the main shapes that can be produced by precision cutting are as follows
- circular box
- square framing (in a house, temple, screen, etc.)
- odd-shaped goods
- Complex shapes, etc.
However, the materials and shapes that can be handled by precision cutting vary from processor to processor.
When considering a request for precision cutting, be sure to check whether the company can handle the material and shape you wish to process.
Frequently Asked Questions about Precision Cutting
Here are some frequently asked questions about precision cutting.
What is the difference between precision machining and ultra-precision/nano machining?
While precision machining refers to machining methods on the micro scale, ultra-precision machining refers to machining methods on the nano scale.
In ultra-precision machining, it is possible to achieve machining on a scale of up to 1/1000 μm.
Another process that is similar to ultra-precision machining is nanofabrication.
Nanofabrication is a generic term for ultra-precision processing technology that uses cutting, etching, and other methods to achieve nm (nanometer) level precision or an error of 1 μm or less.
Nanofabrication cannot be handled by ordinary industrial machinery.
The following machinery and work environment must be in place for processing.
- Nano Processing Machine
- Room temperature maintained at about ±0.2°C
- Factory with a structure that isolates vibration from the outside
What is the difference between cutting and grinding?
Grinding is a process in which a grinding wheel is applied to the work material while rotating to remove the surface.
It is used for the purpose of finishing by shaving the surface rather than cutting the material into the desired shape.
After the grinding process, the surface is also characterized by a smooth finish.
It also has high dimensional accuracy and can process hard materials that are difficult to process by cutting.
However, it should be noted that the machining time is longer than that of cutting because the amount of material that can be removed at one time is smaller.
What is the difference between cutting and turning?
Turning is a method of machining by pressing a tool against a rotating material and removing the surface.
It is used for processing cylinders, cylinders, and other circular objects.
The lathe, a specialized machine tool, is equipped with a tool called a bite, which is also a specialized tool, to perform machining.
Complex shapes can be machined by changing the rotation speed of the material or using multiple bites.
Summary
This article provides an overview of precision cutting, its advantages and disadvantages, and how it differs from similar processing methods.
Precision cutting is suited for small-lot production and is an option when high precision is a priority.
Although precision cutting is applicable to a wide range of materials, the actual materials and shapes that can be handled vary from processor to processor.
When requesting precision cutting, carefully check whether the company can handle the material and shape of the object you wish to produce, and select the appropriate company.
If you are considering manufacturing parts utilizing precision cutting, please contact us.Taiga."Taiga is a free service that allows you to consult with experienced contractors.
We can efficiently proceed with the development of difficult or new parts, small-lot production, prototyping, and mass production while keeping costs low.
Receive technical proposals at Taiga