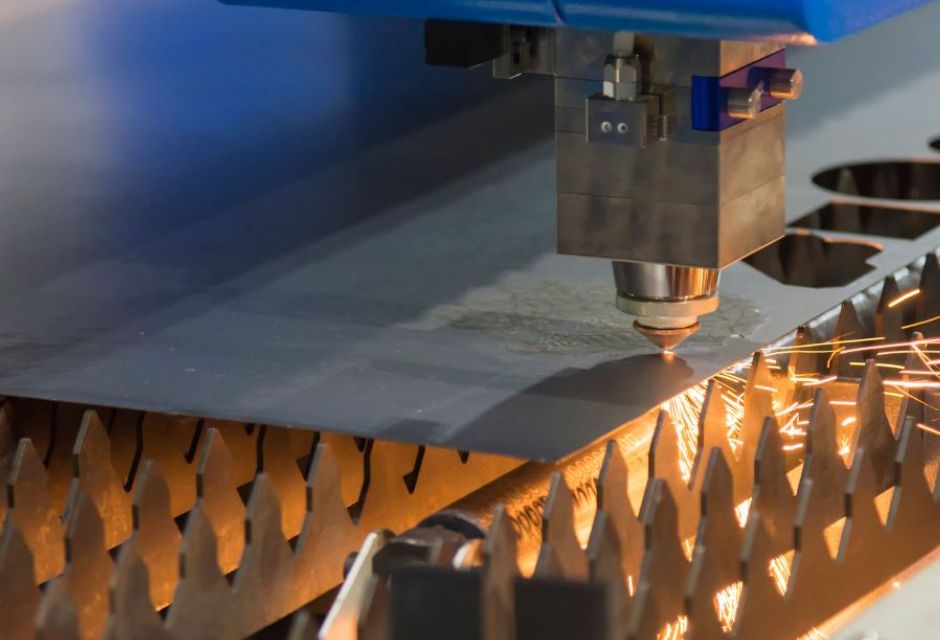
Precision sheet metal processing is known as a technology for processing products that require higher processing accuracy and dimensional tolerances than ordinary sheet metal processing.
The main applications are in the field of equipment manufacturing that requires high precision, such as medical equipment, automotive parts, and electronic devices.This article explains the characteristics of precision sheet metal processing, as well as its advantages and disadvantages.If you are considering introducing precision sheet metal fabrication, please use this article to help you make your choice.
For more information about Taiga, click here.Table of Contents
What is precision sheet metal processing?
Precision sheet metal processing is a technology to process metal sheets with high precision, mainly using thin metal materials of 0.1 mm to 3 mm in thickness.
Unlike general sheet metal processing, precision sheet metal processing requires stricter dimensional control and more advanced processing techniques. Precision sheet metal processing is suitable for manufacturing more precise parts and is widely used in fields such as electronics, automobiles, aerospace, and medical equipment.
Difference between precision sheet metal processing and ordinary sheet metal processing
There are differences between precision sheet metal processing and ordinary sheet metal processing in terms of processing accuracy, applications, and types of materials. Please see below for a summary of the characteristics of each.
Precision Sheet Metal Processing | Normal sheet metal processing | |
Machining accuracy | High precision (accuracy in the millimeter to micro range is required) | General accuracy (±0.1mm to ±0.5mm) |
use | Fields requiring high precision, such as electronics, automobiles, aircraft, and medical equipment | Relatively large structures such as building materials, furniture, industrial machine parts, etc. |
material | Mainly thin sheet metal (1-3 mm) | Metal sheets of various thicknesses |
Production scale | Many small to medium volume productions from prototypes | Mainly medium to high volume production |
cost | high | comparatively low price |
This table shows that there is a clear distinction between the applications and product areas for which each processing method is suitable.
What are the features of precision sheet metal processing?
Precision sheet metal processing is characterized by the following five features
- Very high accuracy
- Various processing is possible
- Improved manufacturing efficiency
- Long-term durability expectations
- Cost-effective
Very high accuracy
First,The feature of this product is its extremely high machining accuracy.
Specific standards for precision sheet metal processing are dimensional tolerances of ±0.1 mm to ±0.05 mm or less. For this reason, they are valued in the field of equipment manufacturing, which requires a high degree of precision.
In particular, it is utilized in medical equipment, aerospace, automotive, electronics, and other fields where the slightest dimensional error directly affects product performance and safety.
Various processing is possible
A major feature of precision sheet metal processing is the ability to manufacture products by combining a variety of processing technologies, including cutting, bending, drilling, welding, and assembly.
By utilizing these technologies, products with complex shapes can be manufactured, and even better design finishes can be achieved. The ability to efficiently and flexibly manufacture products that meet a wide range of needs is the appeal of precision sheet metal processing.
Improved manufacturing efficiency
Precision sheet metal fabrication can be produced efficiently by performing multiple processes in a single facility, eliminating the time and labor required by outsourcing and travel.
In addition, the introduction of CAD/CAM systems and automation technologies that enable design data to be reflected in the machine will enable speedier production.
In particular, the latest laser cutting machines, NC benders, and other processing machines can be automated and numerically controlled, enabling fast and stable processing.
Long-term durability expectations
Precision sheet metal processing can be expected to provide long-term durability through high-precision machine technology and finishing treatments.
Meeting high standards improves the conformity of parts to each other and further increases the strength of the product after assembly. The use of highly durable metal materials is another characteristic that makes these products durable over long periods of time.
Cost-effective
Precision sheet metal processing can flexibly respond to sudden design changes through the use of digital technology and versatile processing machinery.
Therefore,It can shorten time-to-market for products and, consequently, reduce costs.
Material waste can be further reduced by optimizing material placement during the design phase using CAD software.
Flow of precision sheet metal processing
Precision sheet metal processing is an integrated process from product design to completion. Here we will introduce the seven steps of the precision sheet metal working process.
- Design and Drawing
- Selection and procurement of materials
- Blank processing (punching)
- Bending Process
- Drilling Process
- Welding Process
- Assembly/Inspection
1. Design and drawing
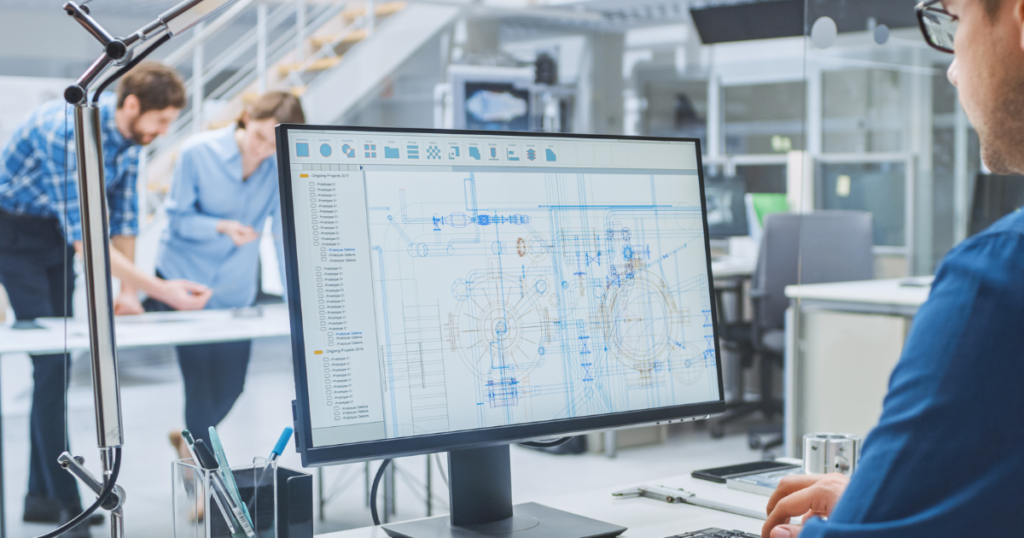
First,This is the creation of product design drawings in response to customer requests.
Specifically, we simulate the machining process and select cutting routes and tools. We also create digital models using CAD software to optimize precision sheet metal processing.
Since design errors directly affect processing and product quality, it is important to fully check material properties and processing methods at the design stage.
2. Selection and procurement of materials
Once the blueprint is completed, the drawing is developed to show the shape of the metal sheet in plan view, and the shapes and dimensions of the parts to be used are confirmed.
Based on the drawings, materials and processing machines are selected and even procured.
Since material quality directly affects processing accuracy and product durability, it is important to select materials that meet JIS and ISO standards.
3. Blank processing (punching)
Once the materials have been procured,Blanking (punching) is performed using press machines and lasers.
Blanking is a method of cutting out a specific shape from a material (mainly metal). This process creates the material for the next use.
4. Bending
Then the material made by the blank process,Bending to specified angles and shapes by press brakes and roll bending.
Bending is an important process for creating the three-dimensional shape of a product. At this time, adjustments must be made to prevent excessive or insufficient bending depending on the rebound and thickness of the material.
5. Drilling
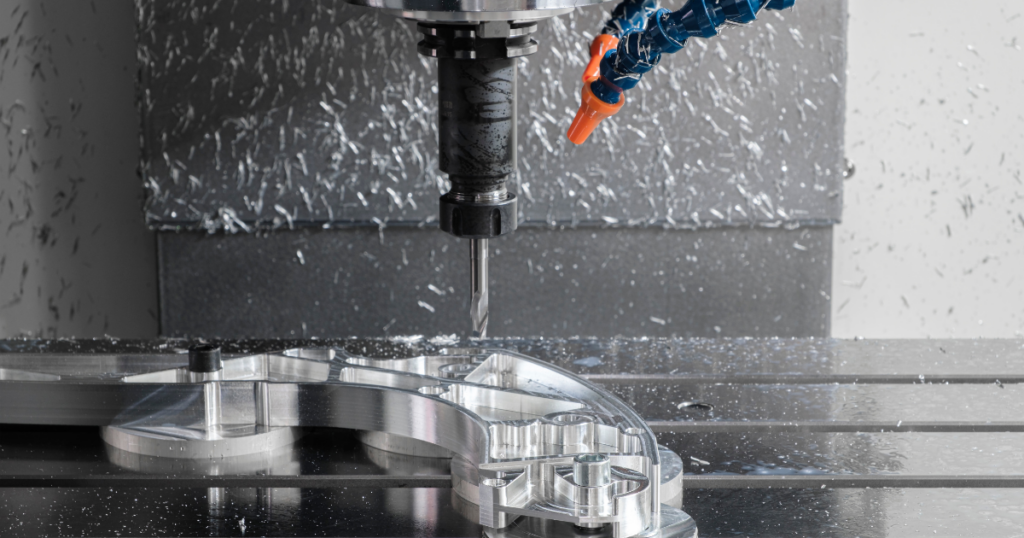
Next to bending process,Drilling process.
As the name implies, holes are drilled in appropriate parts of the material for screws, bolts, and wiring. The occasion of use depends on the type and depth of the hole to be drilled.
For example, a turret punch press is used to drill holes continuously using multiple dies, laser processing is used to drill small holes, and drilling is used to drill deep holes.
At this time, it is important to remove burrs around the hole to ensure the quality of the finished product.
6. Welding process

After bending and drilling are completed, welding is performed if necessary.Welding is an important process for joining parts together, and techniques such as TIG welding, MIG welding, and spot welding are used.
Here, it is important to control the welding heat so that the material is not thermally deformed. Remember to also check for uniform strength at the welding site.
7. Assembly/Inspection
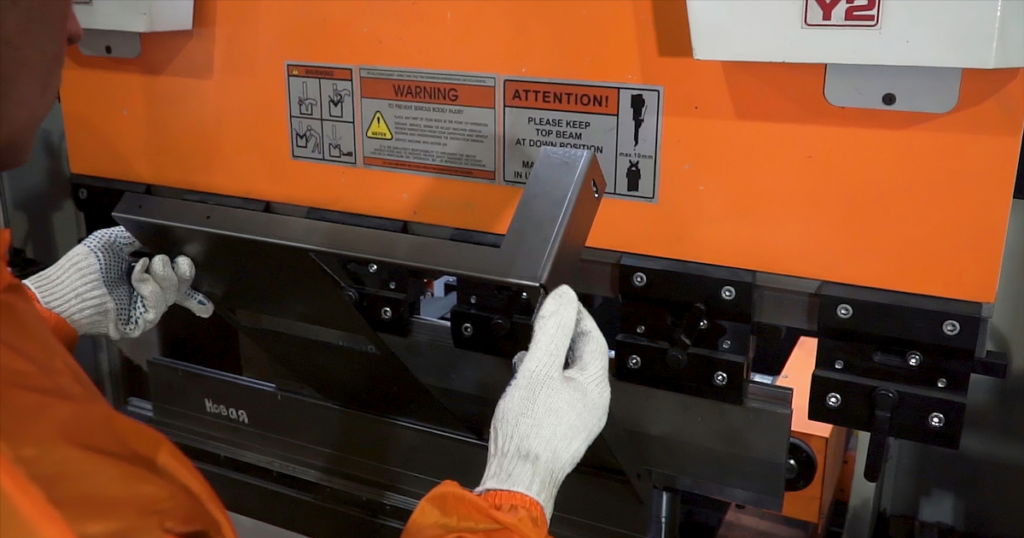
Once the welding process is complete, the surfaces are finished and assembled.After the necessary parts are assembled, the process ends with a final inspection to ensure that the product meets the accuracy and quality requirements of the design.
Properly performed based on inspection standards for strength, dimensions, appearance, etc. In the unlikely event that a product exceeds the design tolerance range, the cause will be identified and the product will be reworked.
Summary
In this article, we have described in detail the characteristics of precision sheet metal fabrication and the process from design to assembly.
Precision sheet metal processing is a processing technology that achieves high precision with dimensional tolerances of ±0.1 mm or less, and is widely used in fields such as medical devices, automobiles, aerospace, and electronic devices.
The entire process, from design to assembly, is carried out in an integrated manner. By making full use of CAD/CAM systems and the latest machining equipment, complex shapes and high quality workmanship are achieved.
Taiga" for procurement of small-lot production
Taiga" is a manufacturing platform that supports parts remanufacturing and high-mix low-volume production, shortening delivery times and reducing costs. Taiga" is a manufacturing platform that supports shortened delivery times, reduced costs, and increased efficiency at the manufacturing site.
If you are considering manufacturing parts utilizing precision sheet metal fabrication, please contact us.Taiga."Taiga is a free service that allows you to consult with experienced contractors.
We can efficiently proceed with the development of difficult or new parts, small-lot production, prototyping, and mass production while keeping costs low.
For more information about Taiga, click here.