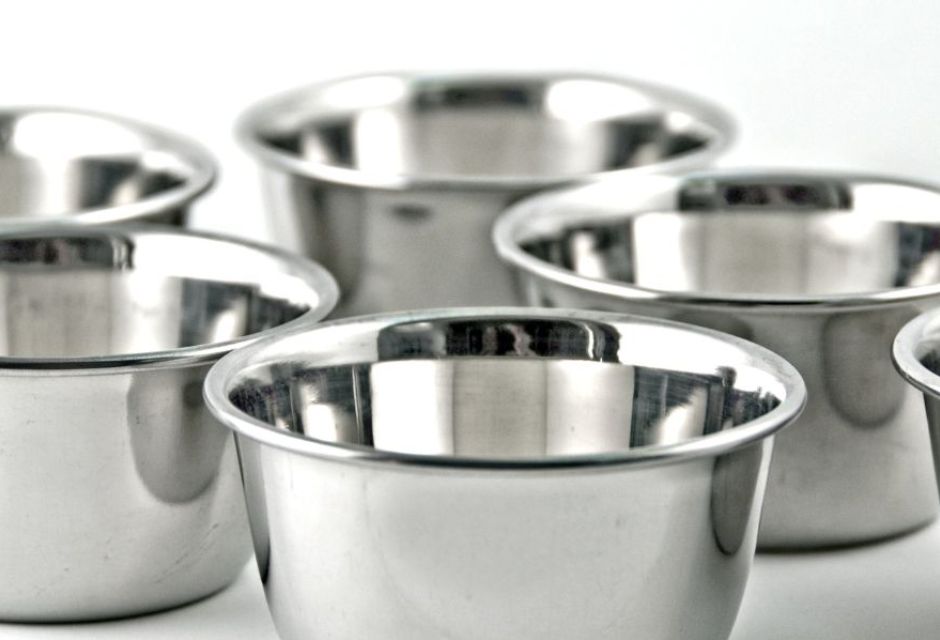
Drawing" is one of the metal forming methods.
While it is used as a processing method for a wide range of products, many people may have questions such as "I don't know the difference between press working, drawing, and bending," or "I want to know the advantages and disadvantages of press drawing.
In this article, we will provide an overview of the drawing process and its advantages and disadvantages.
We also introduce shapes that can be made by the drawing process and the processing procedure.
For more information about Taiga, click here.Table of Contents
What is Drawing? What is press working and deep drawing?
Drawing is a metal sheet forming method in which a sheet of metal is formed by "drawing" it into the desired shape.
It is also called "press drawing" because it is classified as a "press process" in which metal is pressed and processed.
Since the metal sheet is squeezed and processed, there are no seams, and it is possible to create beautiful curved lines.
Drawing is classified into the following two types of processing methods depending on the depth of drawing.
- Shallow drawing: For processing into shallow shapes
- Deep drawing: For processing into deeper shapes
Difference from overhang processing and spatula drawing
There are two processing methods that can produce products with shapes similar to those of the drawing process: the "overhanging process" and the "spatula drawing process.
The overhang process is a press working method in which a single plate is fixed and a punch is pressed into the plate to produce an uneven product.
Although it is not possible to create deep shapes as in the drawing process, it can be combined with drawing to create products with complex shapes.
Spatula drawing is a method of processing by pressing a spatula against a rotating plate.
While molding can be done with little force, processing takes time.
Therefore, this processing method is suited for small-lot product manufacturing.
Advantages of Drawing
The drawing process has the following advantages
- Products of various depths and shapes can be made by changing the mold.
- Suitable for mass production due to short processing time
- Molds can be used over and over again to reduce processing and mass production costs.
- Processing can be completed only by press process.
- High yield and productivity
- Stable quality of processed products
- High strength of manufactured products due to hardening during processing
- Easy production control due to small number of processes
In particular, once a mold is made, it can be used repeatedly, making it suitable for mass production.
Disadvantages of Drawing
The disadvantages of the drawing process are as follows
- High degree of processing difficulty, and if pressure is not properly adjusted, wrinkles, warping, and other defects are likely to occur.
- Specialized equipment is often required for processing, limiting the number of clients.
- Mold production time required
- High initial cost of mold fabrication
- High material costs
- Material selection with high squeezability is necessary
- Burden and expense of mold management and maintenance
Another processing method is likely to be more cost-effective for low-volume production, especially since it is expensive to make molds.
Six shapes that can be produced by the drawing process
In the drawing process, six main shapes can be processed.
The six shapes that can be produced by the drawing process are explained along with typical product examples.
Cylindrical drawing
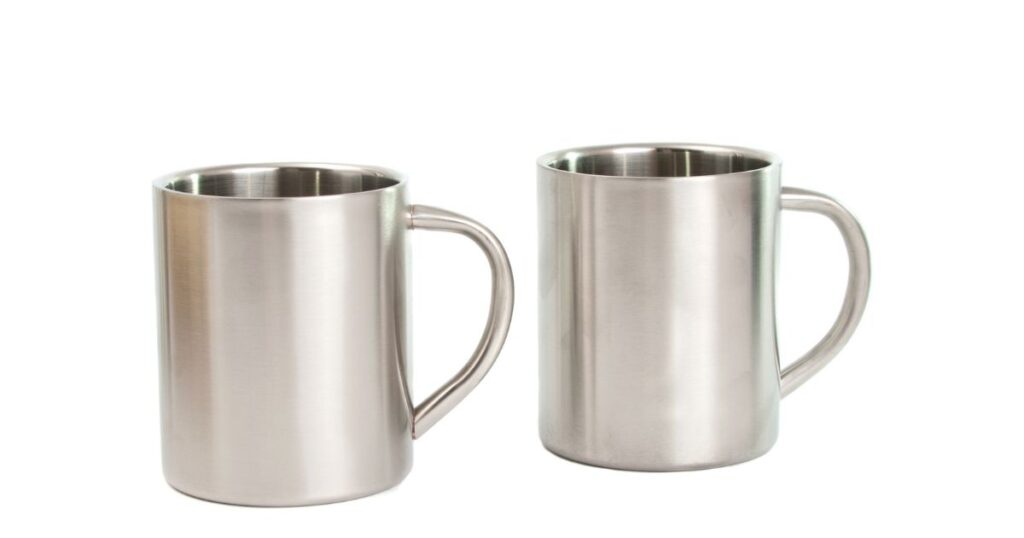
Cylindrical drawing is a drawing process to form a plate material into a cylindrical shape.
The process is characterized by even pressure and stable forming.
This is one of the most basic drawing processes and is utilized in the processing of cups and bowls.
Square Cylinder Drawing
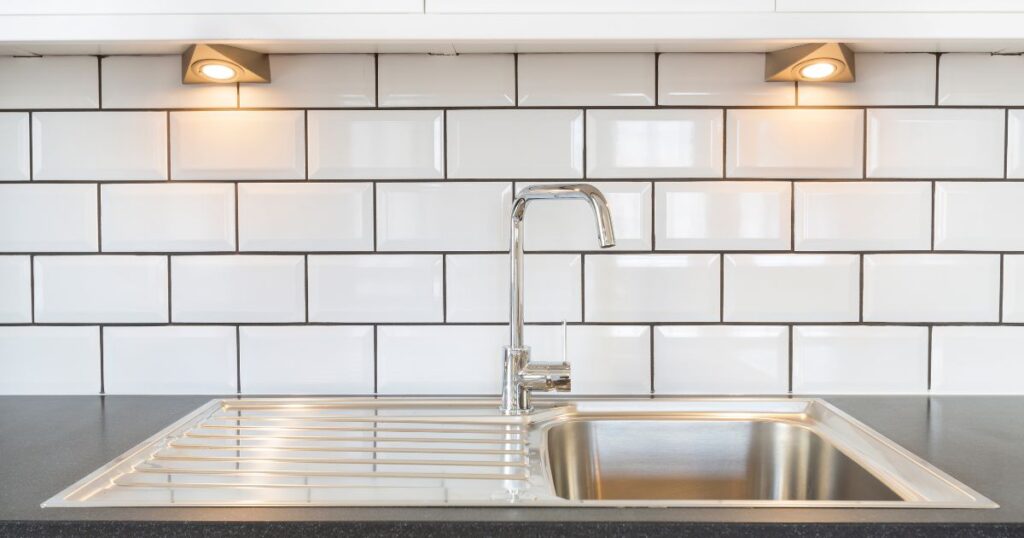
Square-tube drawing is a drawing process to form a plate into a rectangle.
It is utilized in the processing of stainless steel kitchen sinks and lunch boxes.
Metal tends to accumulate in the corners, causing wrinkles and warping, so proper pressure adjustment is required for processing.
Deformed Drawing
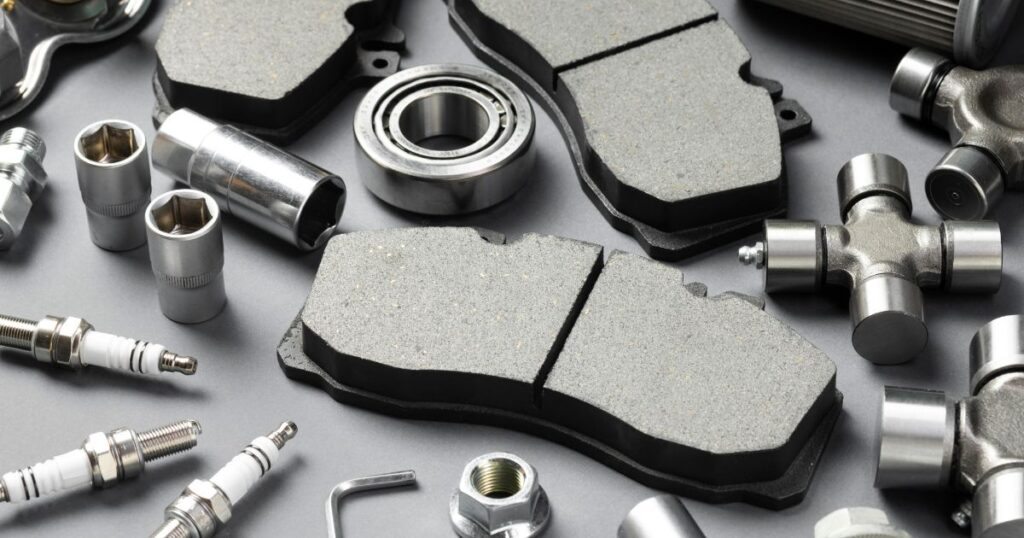
Deformed drawing is a drawing process to form plate materials into complex shapes such as round, square, and perforated.
It is utilized in the processing of automotive parts, electronic parts, etc.
Conical Drawing
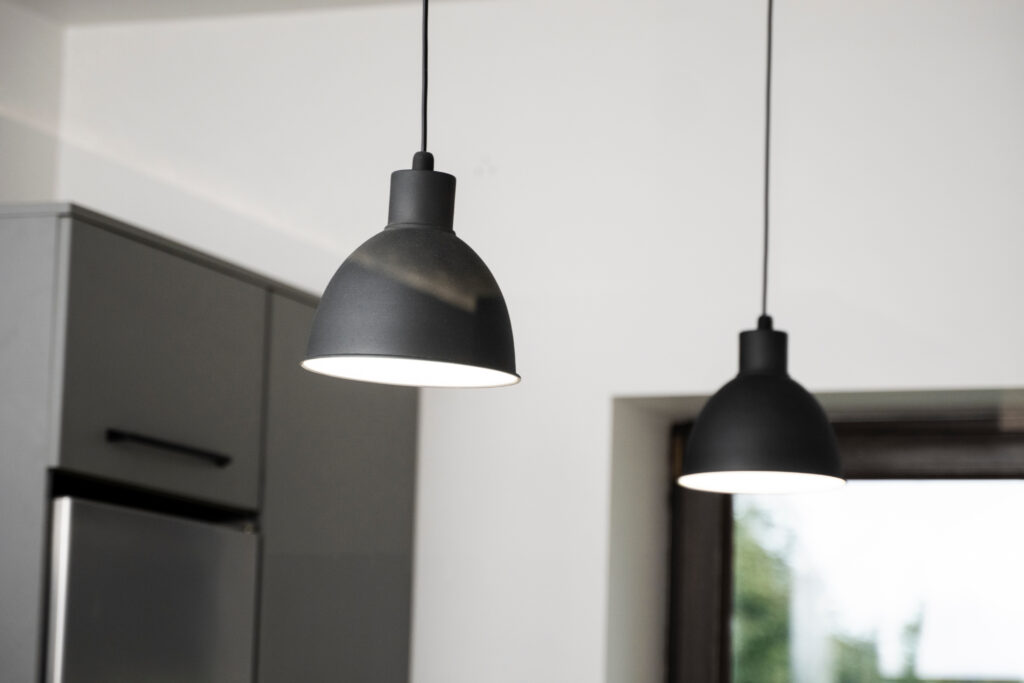
Conical drawing is a type of cylindrical drawing.
Plates can be processed into tapered (conical) shapes with the cross section tapering toward the tip.
Typical examples of major processed products are lighting fixtures and tumblers.
Because the shape of the processed product is complex, it requires more technical skills than other drawing processes.
pyramid drawing
Conical drawing is a drawing process that can form tapered sides, similar to conical drawing.
In conical drawing, the side of the cone is a circle, whereas in pyramidal drawing, the side of the cone is flat.
This process is mainly used for machining parts, and although it is less difficult than conical drawing, it is more difficult than other drawing processes.
spherical drawing
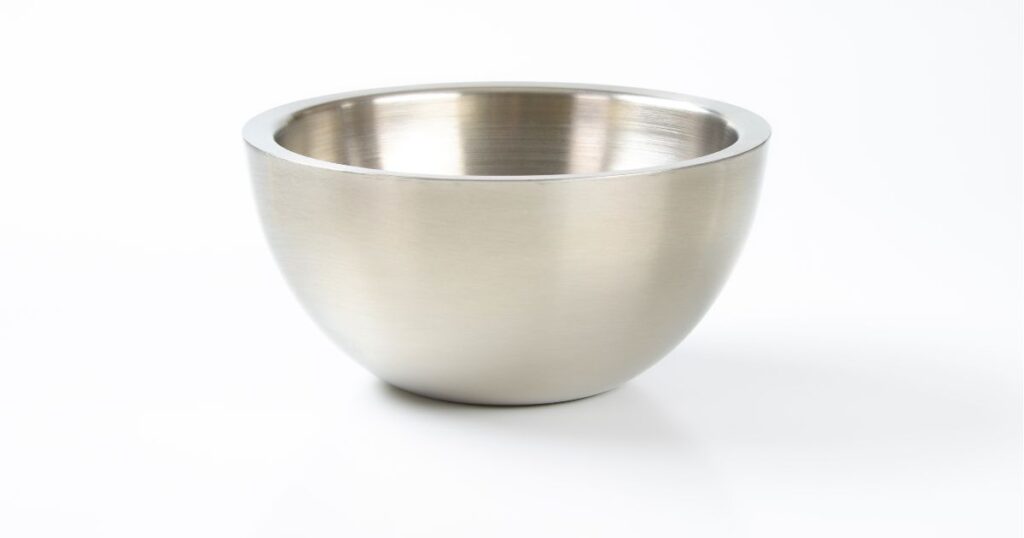
Sphere-head drawing is a drawing process in which the bottom surface is formed into a hemispherical shape by means of a hemispherical punch and hydraulic pressure.
It is utilized in the production of cooking bowls and other products.
Drawing Procedure
Here are some specific steps in the drawing process.
1. Determine shape, material, press machine, etc.
First, the blank dimensions and shape of the fabrication are calculated.
Next, materials are selected based on the opportunity characteristics of tensile strength, yield point (proof stress), elongation, and hardness according to the shape.
Once the material is determined, the appropriate press machine is determined based on the liquid lubricant based on post-processing cleaning and cooling properties and the results of the drawing force calculations.
2. Design and create molds
We design and create dies for the drawing process.
Radius, diameter, and clearance can be calculated based on the number of times the material is bent, deformed, or drawn to prevent cracking or wrinkling.
3. first aperture
The first drawing process, the drawing process, is performed.
First, the metal sheet is set in the lower die (die) and secured with a wrinkle holder to prevent wrinkles during processing.
Next, the plate is pressed into the upper die (punch), where pressure is applied to form it.
4. Re-desqueeze
Since the depth of squeeze is limited at one time, re-drawing is performed as needed.
By repeating the process according to the depth and height of the workpiece to be formed, it is possible to squeeze it down to the desired shape.
5. Trim unnecessary parts.
The ears, which are excess meat around the molded product, are trimmed off by the trimming process.
Depending on the shape of the product and its application, a portion of the ear may be flattened (restriking) and left as a flange.
A flange is a protrusion in the form of a brim, which improves the bonding and strength of parts.
More than just press work! Types of Drawing Processes
We will now introduce a special drawing process that differs from the normal drawing process.
Warm drawing (deep drawing with peripheral heating)
Warm drawing is a drawing process in which wrinkle holders and dies are heated by heaters to improve the workability of metals.
The part that is sandwiched between the wrinkle suppressor and die (blunge area) is heated while the punch side is cooled during the drawing process, resulting in a stronger product.
It is used as a drawing method for materials with low workability, such as stainless steel plate SUS304 and aluminum.
Warm drawing requires special press machines equipped with heating and cooling devices such as heaters and coolers.
Ionizing (wringing process)
Ioning is a process used to squeeze a product formed by the drawing process even deeper.
After drawing, the metal is re-drawn using a punch with a small clearance.
The advantage of this re-drawing is that the "squeezing" results in a thinner and more uniform plate thickness, and a deeper and more precise finish.
Opposed hydraulic pressure molding method
Opposed hydraulic forming is a drawing process that uses liquid pressure instead of either the punch or die used in the drawing process.
Along with pressure from the top of the material, hydraulic pressure from the bottom is applied to mold the material, enabling the molding of deep shapes.
An opposed hydraulic press is required for processing.
Dailless Forming
Dieless forming is a drawing process that does not use dies and press machines.
3D forming can be performed from the original material by a push rod held by a vertical machining center or an industrial robot.
Since die-less forming does not require the creation of a dedicated die, die fabrication time and cost can be reduced and drawing can be performed.
It is not suited for mass production, but mainly for prototype molding and small lot processing.
Summary
In this article, we explained the outline, merits and demerits of press drawing, shapes that can be processed by press drawing, procedures, and special drawing processes.
Drawing is a processing technology that can achieve a variety of shapes.
On the other hand, it is prone to cracking and wrinkling, so high processing technology is required.
It is advisable to find a processing company that specializes in squeezing and consult with them once.
If you are considering manufacturing parts utilizing the drawing process, please contact us.Taiga."Taiga is a free service that allows you to consult with experienced contractors.
We can efficiently proceed with the development of difficult or new parts, small-lot production, prototyping, and mass production while keeping costs low.
For more information about Taiga, click here.