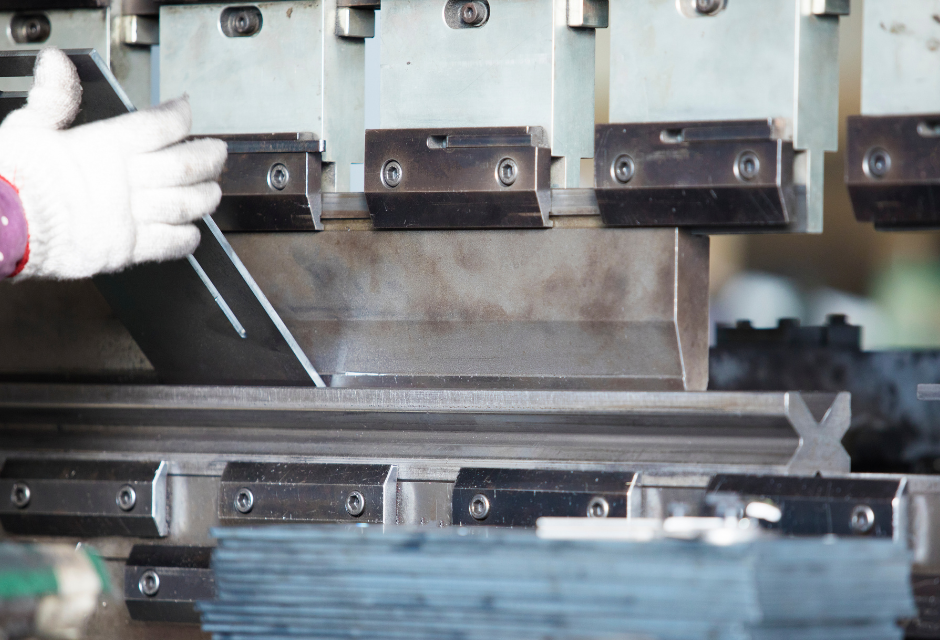
In the process of developing new products and manufacturing prototypes, the selection of a processing method and contractor is a major issue. Pressing is a commonly used method, especially in situations where metals and resins are handled, but you may be at a loss as to its merits and differences from other processing methods.
This article provides an easy-to-understand explanation of the basics of press work, specific processing methods, and types of dies.
For more information about Taiga, click here.Table of Contents
What is press working?
Pressing" is a processing method in which pressure is applied to a material such as metal or resin to form it into the shape of a metal mold. The word "press" means to press or squeeze.
The use of molds provides more stable quality than manual work and is suitable for mass production of the same product. It is also used for a wide variety of products because it can reproduce fine details and complex shapes with high precision.
Examples of stamping products
Many products we see in our daily lives are made by press working. Below are some typical examples.
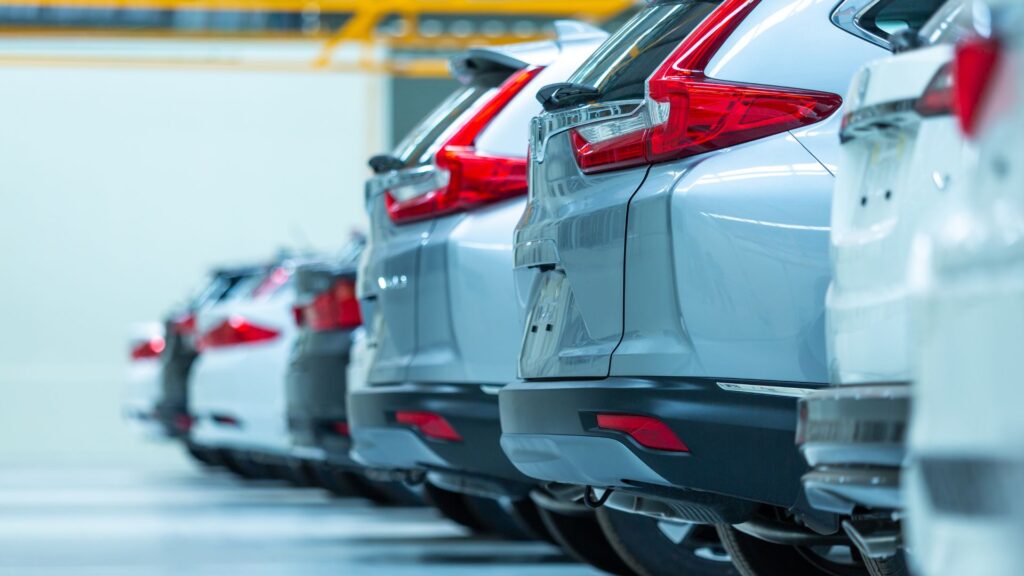
- Automotive parts (body, frame, door, hood)
- Exteriors of electronic devices (notebook computer and smartphone housings)
- Exterior of home appliances (air conditioners, refrigerators, washing machines, microwave ovens)
- Residential water products (kitchen sinks and bathtubs)
- Medical devices (medical clips and joint parts)
- Coins (1 yen coins and 500 yen coins)
- Aluminum and tinplate cans
Difference between stamping and sheet metal/forging
When considering press processing, "sheet metal processing" and "forging" are often compared.
Difference between press work and sheet metal
This method involves bending and cutting metal sheets by hand to finish the product.
Skilled craftsmen's techniques allow for fine adjustments and are especially suitable for products with complex shapes or those that require customization. However, production efficiency is somewhat low because the work is mainly done by hand, making it unsuitable for mass production.
Press work is characterized by high production efficiency because it is performed automatically with a die using a machine. Since large quantities of products can be manufactured at one time with uniform quality, there is little variation from product to product.
It is widely used in industries that require quality stability, such as automotive parts and home appliances in particular.
Difference between stamping and forging
Forging is a process in which a heated lump of metal (billet) is beaten or subjected to strong pressure.
Forging increases strength, making it suitable for parts where durability is important, such as engine crankshafts and tools. However, the disadvantage is that it is difficult and time-consuming to produce complex shapes.
In contrast, press forming uses a relatively thin metal plate (blank) and applies pressure with a die.
It is suitable for manufacturing thin components and lightweight products, and is very efficient in mass production because it can make a large number of products in a short period of time.
Types of press work
There are various methods of press working.
- shear processing
- Bending Process
- Drawing process
- punching (e.g. with a die)
- Punch Press Processing
Understand each processing method and use it according to the shape of the product and its application.
shear processing
Shearing" is a process for cutting metal sheets.
When processing metal, a large piece of material must first be cut into manageable sizes. In the shearing process, force is applied to the metal to cut it, just like cutting paper with scissors.
Specifically, the metal is sandwiched between the "punch (upper die)" and the "die (lower die)" and force is applied in the opposite direction. No matter how hard the metal is, there is a limit to the force it can withstand, and if the force exceeds that limit, the metal is separated and cut.
However, this process disturbs the fracture surface, causing burrs and warping.
If you want to obtain a beautiful cut finish and reduce subsequent cutting and grinding processes, choose "precision shearing".
Bending Process
Bending" is a method of bending metal sheets and tubes into shape, also known as "bending processing. It is a highly versatile processing method because it can bend metal into various shapes and angles.
The bending method is classified into various techniques, but the most typical is "kata-bending.
Material placed on the die (lower die) is pressed into the punch (upper die), and the metal is bent to conform to the shape of the die. Depending on the shape of the finished product, it is divided into "V-bending," "U-bending," "L-bending," "Z-bending," etc.
Drawing process
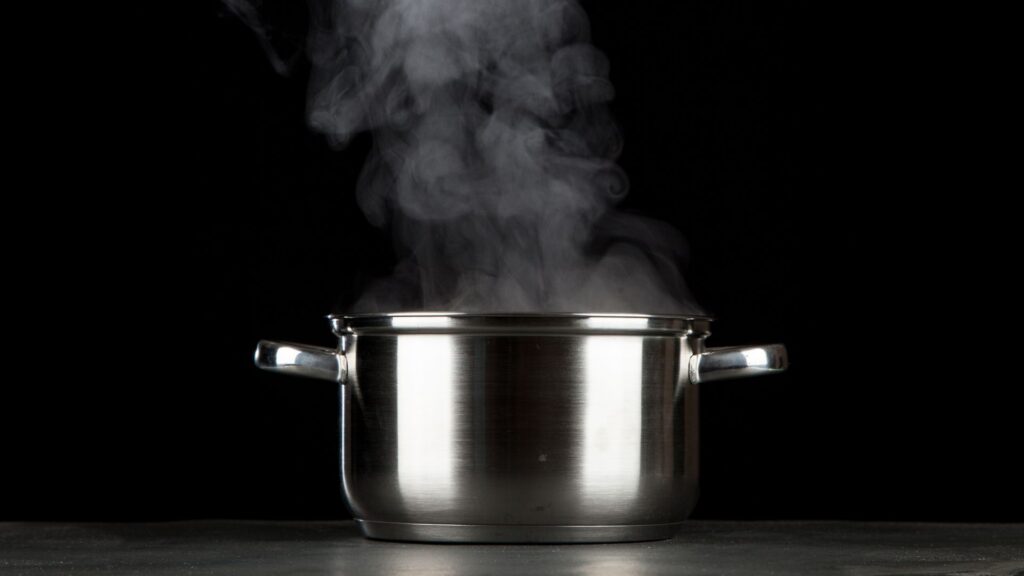
Drawing" is a method of applying pressure to a metal sheet and stretching it to create a container-like product. Easy examples are cups, pots, and bowls.
Formed from a single metal sheet without welding or cutting, its main feature is that it has no seams. This is especially recommended when you want to create products with high durability and low risk of leakage and corrosion.
Drawing processes are categorized into "cylindrical drawing," "square cylindrical drawing," and "deformed drawing" based on the shape of the product. For example, cylindrical drawing efficiently produces cylindrical parts by applying force evenly to a metal sheet.
Drawing is considered one of the most difficult press work processes. Since advanced technology is required for die design and fabrication, not all press manufacturers can handle this process.
If you want to commission a drawing process, look for a manufacturer with extensive experience and expertise.
punching (e.g. with a die)
Punching" refers to the removal of a specific shape or portion from a material using a press machine. There are five major types of punching processes.
- Punching: Hollowing out the part that will become the product (part) from the plate material
- Hole punching: Unnecessary portions are cut out of the product. The remaining part becomes the product.
- Slitting: Cutting into the material while it is still connected, without cutting it completely.
- Half punching (half die cutting) process: Not completely punching out, but only making an uneven surface. Typical is embossing.
- Edge trimming process: Remove unnecessary edge portions. Fine-tuning after molding
Among stamping processes, note that punching is particularly prone to defects such as sagging, burring, and twisting. Dulling" refers to the indentation or depression that is created around the processed portion of the metal as it is formed.
To control such defects, it is important to apply shaving after pre-drilling and to position the material accurately.
Punch Press Processing
Punch press processing is a processing method to cut out or punch holes in metal sheets into desired shapes. It is also called "punching press" or "turret punch press.
Multiple punches (dies) are mounted on a die holder called a "turret," and are automatically changed to perform machining. The advantage of this system is that it can easily perform high-precision machining, which in the past relied on skilled workers.
In addition, since dedicated dies are not required, cost and time can be saved. Since various shapes can be processed simply by rewriting the processing program, another advantage is the flexibility to handle small-lot, multi-variety production as well as large-lot production.
However, the maximum thickness of a metal sheet that can be processed by a punch press is about 3 mm. Any thicker than this will place an excessive burden on the die and machine, resulting in a decrease in processing accuracy.
Therefore, when processing materials with a plate thickness of more than 3 mm, it is better to consider another method, such as a laser cutting machine.
Types of Press Dies
The following three types of dies are used in press work.
- single press
- progressive press
- transfer press
Since each mold has different characteristics, please consult with the manufacturer to determine which mold should be used for production.
single press
In a "single press," one die handles one process.
For example, different dies are used for different processes, such as bending and punching, to proceed. Since the transition from one process to the next is done by hand, it is characterized by a high degree of flexibility, although it is labor-intensive.
In addition, the cost of dies is relatively low, and single presses are often chosen, especially for the production of prototypes and the individual machining of a small number of parts.
progressive press
Progressive presses continuously process multiple processes with a single die.
Simply set the metal sheet into the machine, and various processes such as punching, drilling, and shearing are performed.
As a result, the processing speed is extremely fast, and in some cases more than 200 products can be processed per minute.
Since processing is automatically repeated, mass production is possible while maintaining stable quality. Please take advantage of this system when manufacturing large quantities of the same product, such as automobile parts and home appliances.
However, the disadvantage is that the die structure is very complex, resulting in high die fabrication costs.
transfer press
In "Transfer Press (TRF)," independent dies are used for each process, and multiple processes are performed while materials are automatically transferred.
It is similar to progressive presses in that it performs multiple processes in succession, but differs in that each process is performed with a separate die, allowing it to handle parts with more complex shapes and larger workpieces.
Transfer presses are equipped with a transfer mechanism to move materials between processes. This function sends the material to the die in turn, where it is processed through cutting, bending, and drawing. This automation has the advantage of reducing human error and ensuring high product accuracy.
However, the initial cost is high because design costs are required in addition to the mold fabrication costs. Consider whether or not to introduce this system based on the scale of production and your long-term plans.
Summary
In this issue, we have explained in detail the specific methods of press work and the types of dies.
Pressing is used in many products that are indispensable to our daily lives, such as automobile parts and home appliances, because of its stable quality and suitability for mass production.
However, since different processing methods and molds have different characteristics, the optimal method should be selected in consideration of product specifications, production volume, cost, and other factors.
If you are wondering, "Which processing method is best for my product?" If you are wondering "Which processing method is best for my product?
At Taiga, our engineers have extensive experience in a variety of processing methods, including stamping, and can suggest the best manufacturing method for your company.
There is no charge for using our service. Why not start by creating an account and experience Taiga's services for yourself?
For more information about Taiga, click here.