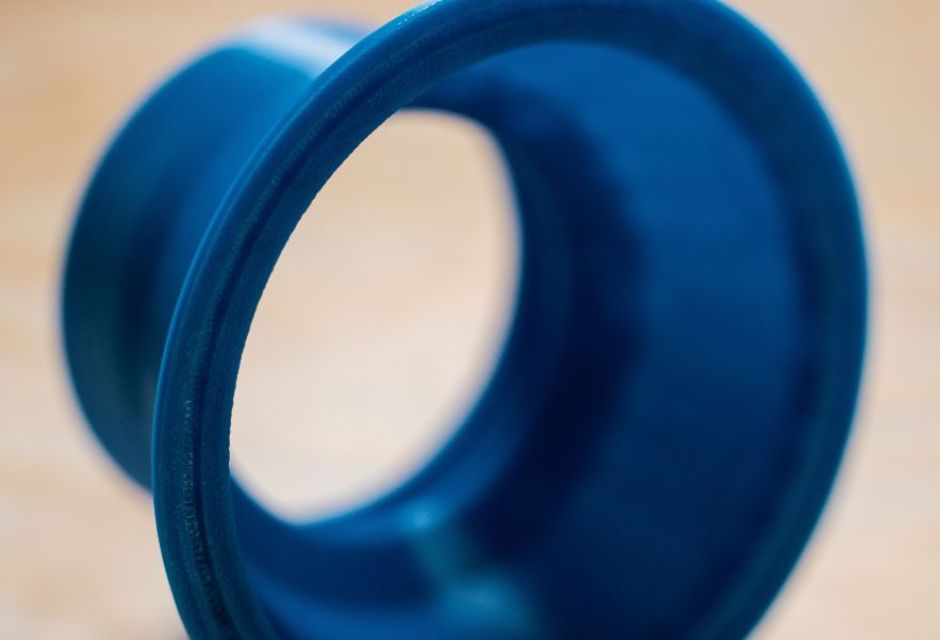
Many people may consider cutting in the manufacture of plastic products.
However, "I heard that cutting resin is difficult, is it true?" What kind of resin material is used in the cutting process? What are the resin materials used in the cutting process?
This article will provide an overview of resin cutting, processing methods, and resin materials used.
For more information about Taiga, click here.Table of Contents
What is resin cutting?
Cutting is a method of cutting, cutting, or otherwise processing plastic or other resin materials with a cutting tool.
While "injection molding," in which melted resin material is placed in a mold and cooled for molding, is suited for mass production, "cutting" is suited for small-lot production because the material is molded one at a time.
Advantages of cutting resin
The advantage of cutting resin is the ability to produce highly precise products.
In resin cutting, the dimensions of the product are numerically controlled by computer.
As a result, even products with complex shapes can be machined with high precision and stable quality.
Also, taking advantage of the characteristics of resin, more complex shapes can be made by combining cutting with welding and other processes.
Is it difficult to cut resin?
Among cutting processes, resin processing is one of the most difficult.
Resin has lower thermal conductivity than other materials and is prone to thermal expansion and deformation after cooling.
During machining, the area where the tool makes contact must be reduced in consideration of frictional heat, and dimensions after cooling must be considered in light of deformation.
Processing method used in cutting resin
The following is a step-by-step explanation of the machining methods used in resin cutting.
Lathe Machining
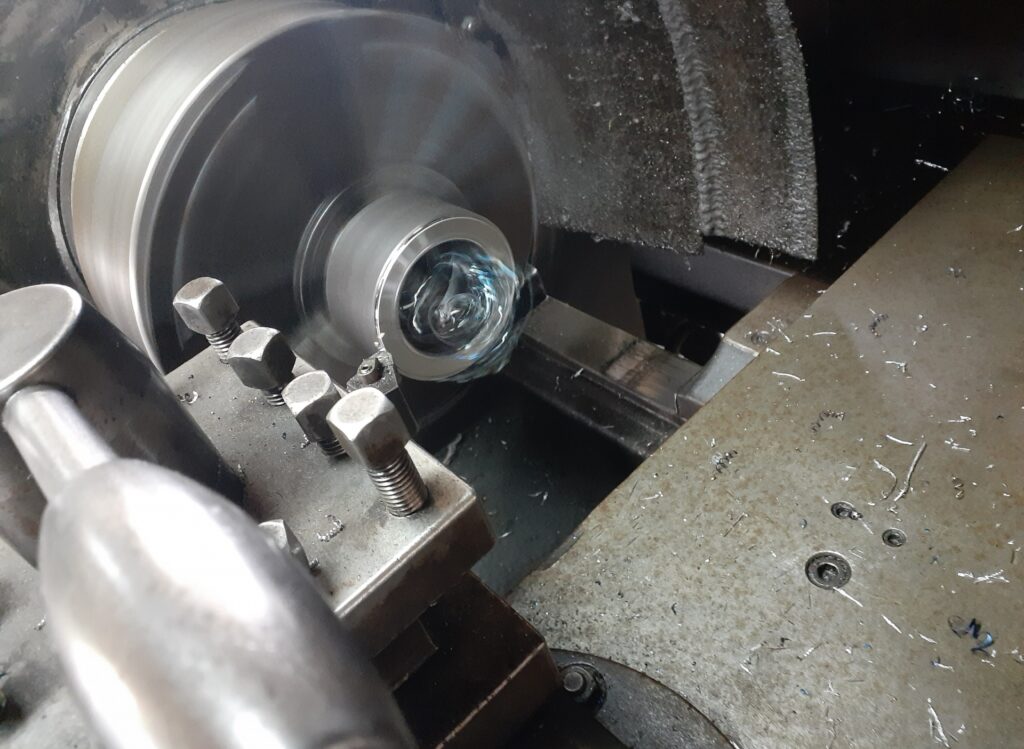
Turning is a method of machining by applying a tool to a rotating material.
Because of its ability to process in micron units, it is employed in the machining of products and parts that require high precision.
In addition, by using different tools for different machining operations, the following machining operations can be performed.
- Outer Diameter Cutting
- Internal diameter grinding (hole drilling)
- edge cutting
- Threading (Female thread)
- bevelling
- taper cutter
- Drill hole drilling
- Grooving and plunge cutting
milling
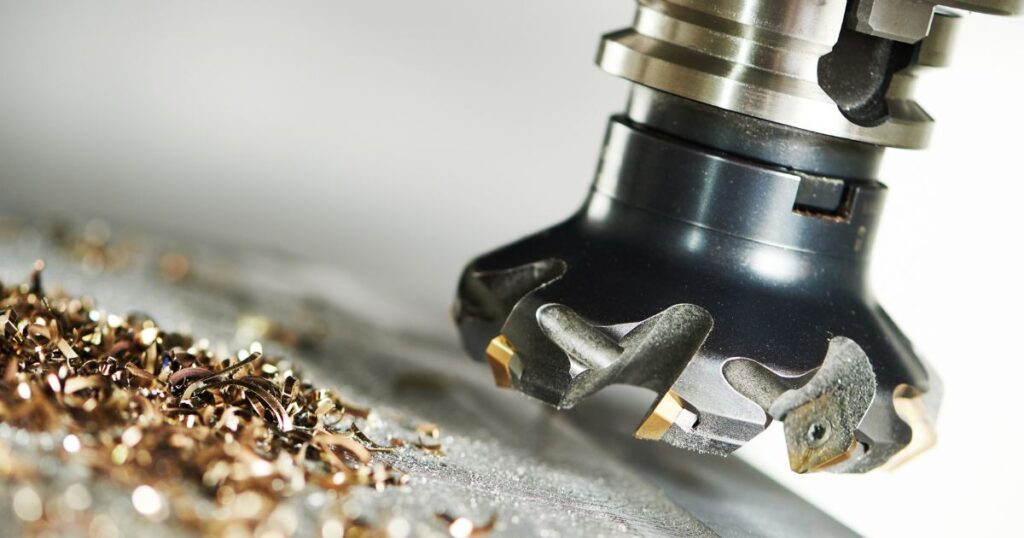
Milling is a forming process in which a high-speed rotating cutting tool is pressed against a stationary material.
We specialize in the following types of processing
- plane-turning
- difference in level
- groove
- arranging the thickness of something
- endmill
- Drilling and other processing
- thread cutting
3 Main Resin Materials Used in Cutting Processes|Which is Suitable?
There are two main types of resins
- Thermoplastic resin (thermoplastic plastic): softens when heated and solidifies when cooled
- Thermosetting resin (thermosetting plastic): cures when heated
In many cases, thermoplastic resins are used in resin cutting.
Below are some typical thermoplastic materials.
General Purpose Plastics
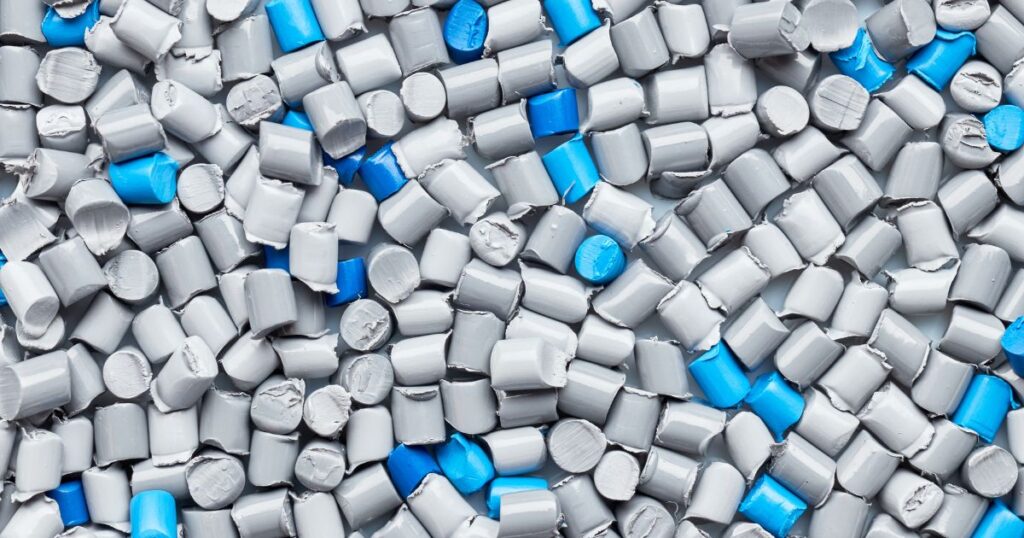
Commodity plastics are common resins used in a wide range of applications.
Mainly, the following materials are used as cutting materials
- PP (polypropylene)
- PE (polyethylene)
- PMMA (acrylic)
- PS (Polystyrene)
- PVC (polyvinyl chloride)
- ABS resin, etc.
engineering plastics
Engineering plastics (engineering plastics) are resins with high mechanical properties, heat resistance, and chemical resistance.
Often used in demanding industrial applications, the main materials include the following
- PA (nylon/polyamide)
- 6 nylon
- 66 nylon
- MC nylon (MC901)
- POM (polyacetal)
- Duracon (polyacetal POM)
- UHMWPE (Ultra High Molecular Weight Polyethylene)
- PC (Polycarbonate)
- PET (polyethylene terephthalate)
- PBT (Polybutylene terephthalate)
- PVDF (polyvinylidene fluoride), etc.
super engineering plastic
Super engineering plastics (super engineering plastics) are resins with higher performance characteristics than engineering plastics.
The main materials include the following
- PTFE (Teflon)
- PEEK (polyetheretherketone)
- LCP (Liquid crystal polymer)
- PPS (polyphenylene sulfide)
- PI (Polyimide)
- PAI (Polyamide-imide)
Thermosetting resin may be used for some productions.
Thermosetting resins are less versatile than thermoplastics, but have higher heat resistance and strength.
Therefore, depending on the production, the following thermosetting resins are also used as cutting materials.
- phenol resin
- epoxy resin
- urethane resin
Procedure for cutting resin
From here, the procedure for cutting resin is explained.
Modeling backwards from the production
First, we examine the fabrication method according to the information on the workpiece to be fabricated, referring to prototypes and fabrication data.
If requirements for fabrication have not been determined, modeling is performed while keeping the following points in mind.
- Design of workpiece
- strength
- Performance, etc.
Decide on the resin material and processing method to be used.
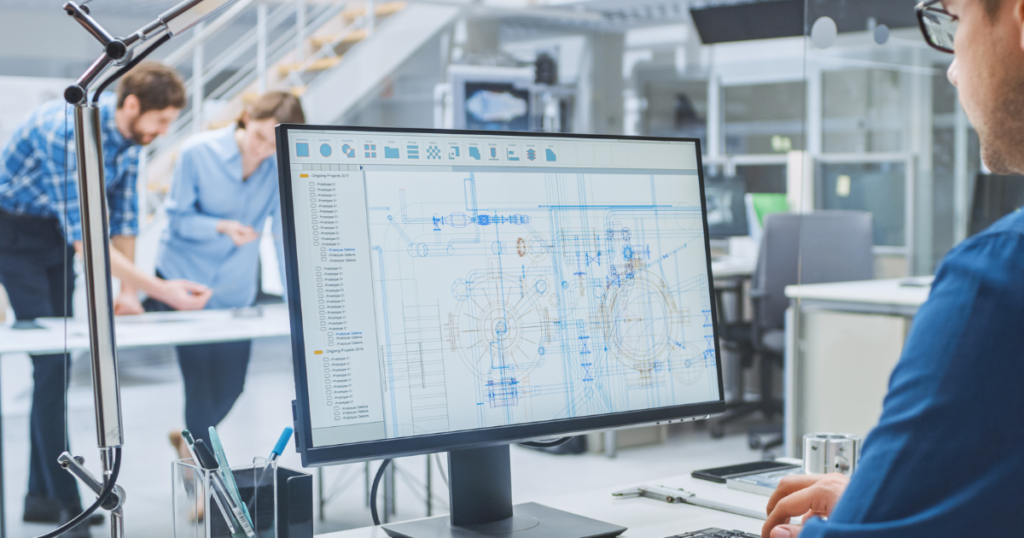
Based on modeling and drawings, the resin material, processing method, and size to be used are determined.
Before starting fabrication, prepare the following to make the product as per the drawings.
- production plan
- check diagram
- QC Process Chart
- inspection report card
Preparation of processing machines, tools and programs
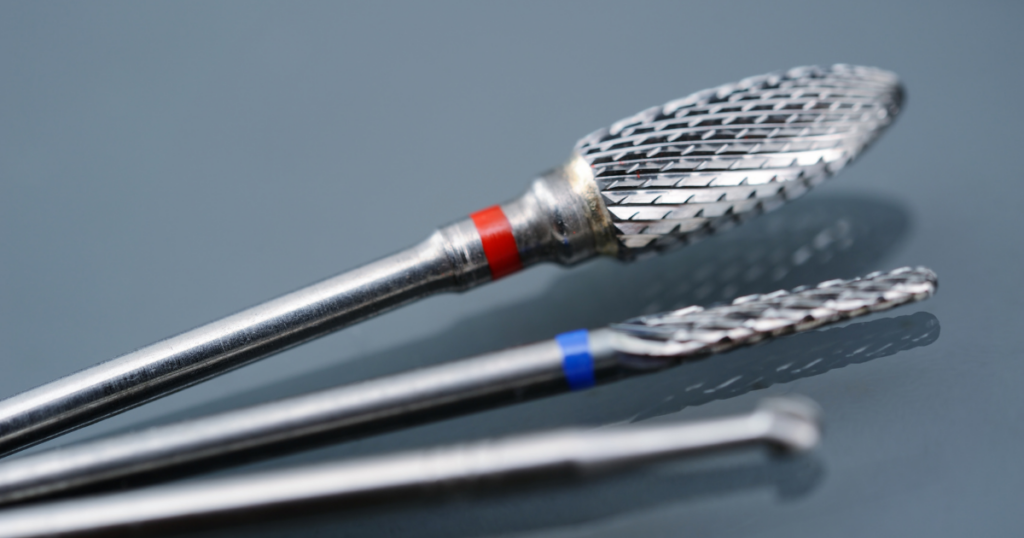
Next, we prepare the machining center and cutting tools according to the processing content.
When ready, set the cutting tool and material on the machine and make fine adjustments such as positioning.
Note that if an NC lathe, NC milling machine, or machining center is used for machining, a program must be created.
Some processors will manage the program data so that the same product can be manufactured when reordered.
Perform cutting of resin
Resin cutting is performed using a processing machine.
Resin has the property of deforming depending on temperature, so be sure to control the temperature thoroughly.
Periodic inspections are also conducted during the cutting process.
Inspections during the process lead to early detection of problems and assurance of product quality.
Finishing touches.
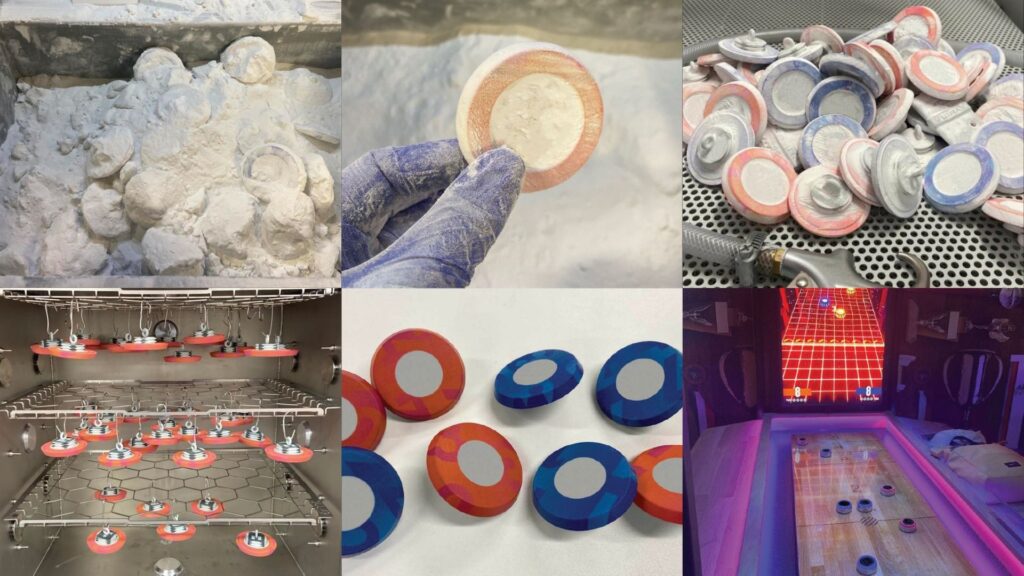
After machining, finishing processes such as deburring and blast finishing are performed to complete the product.
Upon completion, inspect the shipment to ensure that the product and materials meet quality standards.
After shipping inspection, the work is completed by packing the product to protect it from
Things to keep in mind when cutting resin
The key to cutting resin is to have a firm grasp of the properties of the resin material to be used.
Even if a resin is selected for product manufacturing, it may not be suitable for cutting.
If you choose a material that requires secondary processing to ensure quality, it will have a negative impact on labor, delivery time, and cost.
When deciding on the resin material to use, it is important to seek input from the processor as well as your own wishes.
In addition, cutting conditions are very important for resin cutting.
To make high-quality resin products by cutting, carefully determine the following cutting conditions.
Type of cutting process | Cutting conditions |
Lathe Machining | Cutting speed (peripheral speed) Depth of cut Feed rate Cutting time |
milling | Cutting speed (peripheral speed) Feed rate per blade Table feed rate Cutting time |
Summary
The outline and advantages of resin cutting, methods used in cutting, and precautions to be taken during processing are explained.
While cutting can be performed with high precision, it must be done after carefully assessing the properties of the resin.
Select a processor that can perform processing with high technical capabilities, including appropriate material selection and thorough temperature control.
If you are considering manufacturing parts utilizing plastic cutting processes, please contact us.Taiga."Taiga is a free service that allows you to consult with experienced contractors.
We can efficiently proceed with the development of difficult or new parts, small-lot production, prototyping, and mass production while keeping costs low.
For more information about Taiga, click here.