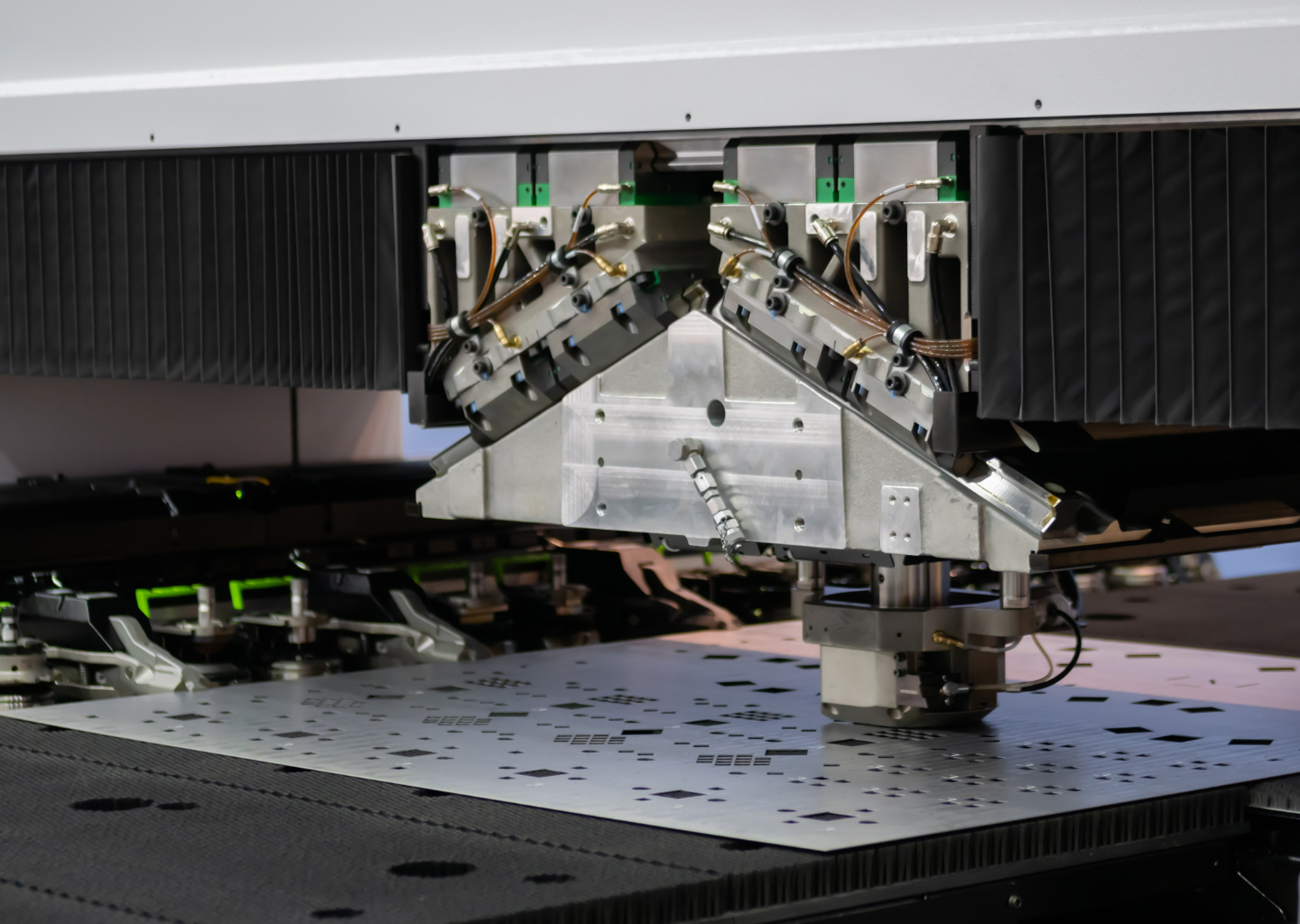
Shearing, an essential process for manufacturing metal products, is utilized in many of the products we see in our daily lives. However, some people may be unfamiliar with the meaning of shear and the mechanism of processing. This article provides an easy-to-understand explanation of shear processing.
Table of Contents
What is shearing?
Shearing is the act of simultaneously exerting forces in opposite directions on an object to displace and cut it. It is easy to understand if you imagine cutting paper with scissors. From a physical point of view, the paper is cut by one blade and another blade moving in opposite directions, clamping the paper and shifting the paper material in opposite directions at the point of contact. When an object is subjected to a force in the opposite direction, it is deformed, and when that deformation exceeds the limits of what the material can withstand, the material is cut by shear.
Shear Processing Mechanism
Shearing is a process that uses shear to cut metal. Two dies, arranged in an upper and lower position, are used to cut flat plate materials. The upper die (punch) moves toward the lower die (die) and presses the plate against it, causing the material to break and be cut. Specifically, the material is set on the lower die (die), and the upper die (punch) applies force to the material to cut it. In addition, a gap called "clearance" is generally secured between the die and punch to improve the quality of cutting.
In shearing, a slight curve (R shape) is formed at the contact area as the punch is pushed into the flat material. Further force creates a shear surface in the material, which widens the cracks. As a result, a fracture surface is formed and the material is eventually cut through.
Difference between shearing and cutting processes
Shear processing is a processing method that uses shear force to cut an object. Cutting, on the other hand, is a general processing method for separating objects. In other words, shearing is a type of cutting process. Depending on the technology and force used, there are different types of cutting processes, such as mechanical cutting, electrical cutting (plasma cutting), gas cutting, laser cutting, and water-jet cutting.
Types and Features of Shearing Processes
Shear processing includes both blank processing for making flat plates and various methods for working the plates. Below we list the main types of shear processing and introduce their characteristics.
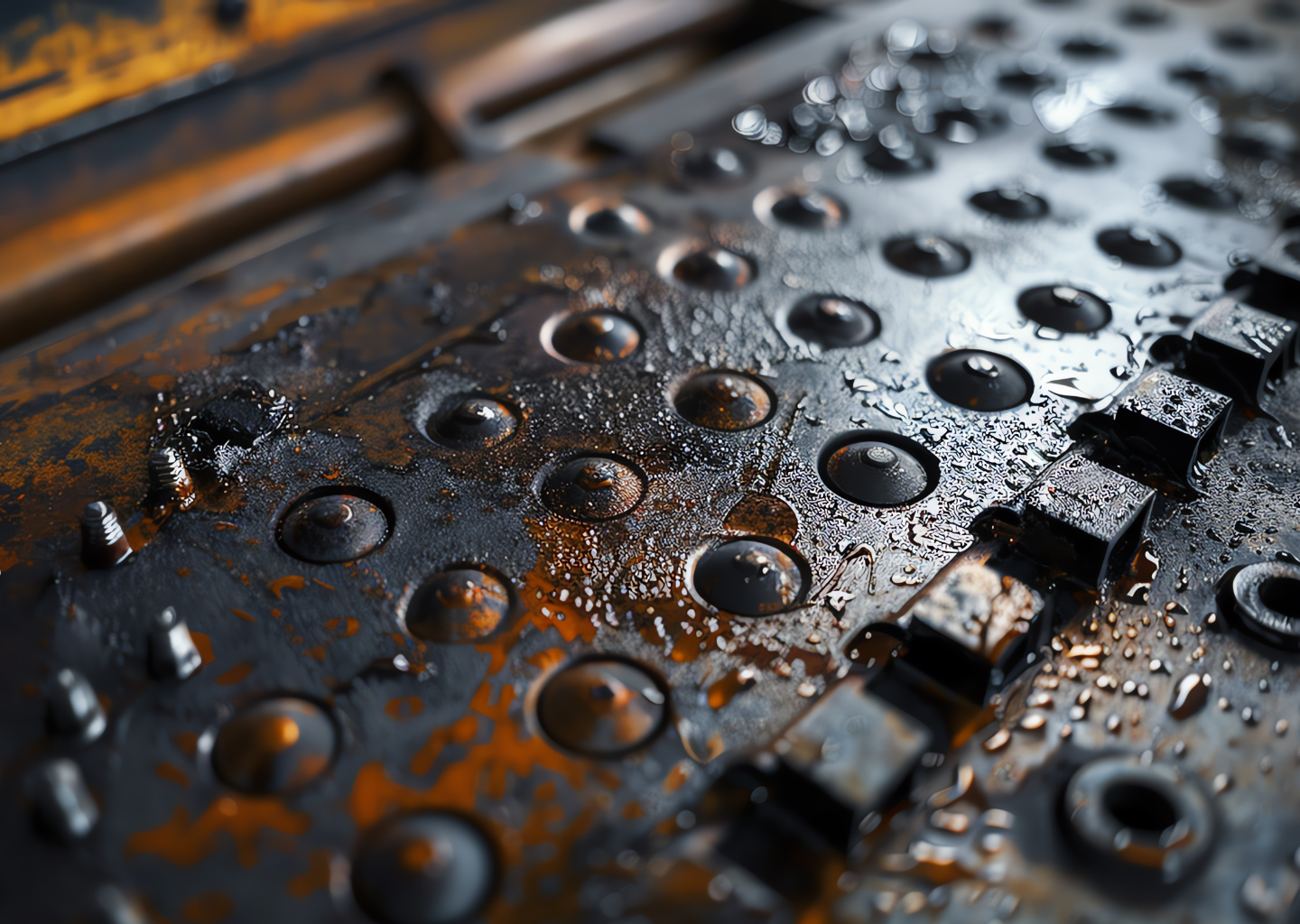
Cutting process (shearing process)
Cutting is a common technique for cutting plate materials and specifically includes a technique known as "shearing processing. In the shearing process, the plate material is cut by clamping it between a die and a punch. It is used especially in the blank process to cut out coils and thicker plate materials.
Separate processing
Separating (separating) is a shearing process for separating materials. It is a widely used process for separating products from materials because it can split a single material into asymmetrical or symmetrical pieces.
Punching (Punching process)
Punching (punching) is a basic processing method, also known as external shape punching. A die is used to punch and cut into a predetermined shape, such as a circle or a rectangle. Since a flat plate is held from the top and bottom and cut, it has the advantage of being less prone to warpage and is often used for blank processing.
Notching process
Notching is a shearing process that uses a dieboard to cut off only a portion of the end of a flat plate. Unlike the method of cutting and separating the entire piece, this process cuts off a portion of the piece. Notching is a processing method often used to ease stress concentration and improve strength by notching the end of the material after cutting.
Infeed processing (slitting)
Cutting (slitting) is a method of making cuts while bending plate materials in a press process after cutting them with a punch. It is often applied to coil materials to control the flow of material during drawing and to prevent wrinkles.
Edge trimming process
Edge trimming (trimming process) is a shearing process to cut off the excess portion as a result of processing. It is used to finish a product by cutting off excess edges left over from drawing or other processes. While a lathe may be used for trimming, shearing with a press is more efficient and easier to maintain constant quality.
Drilling (piercing)
Punching (piercing) is a shearing process in which a hole is punched through a plate material. Using a combination of a piercing punch and a button die, the plate is cut as if it were hollowed out in the manner of a die cutter. The two most common types of piercing are continuous piercing and nibbling, in which holes are punched at a finer pitch than in piercing. The nibbling process is capable of drilling holes of more complex shapes.
Total punching process (compound processing)
Total punching (compounding) is a method of simultaneous drilling and punching that is used to significantly improve work efficiency. Using a die, a circular part can be cut from a flat plate in a single press, and a hole can be drilled in the center of the part.
Specifically, two processes are performed simultaneously by first using a die to cut out an external disk and then using the same die to drill a hole in the center of the disk. This method allows a single press to be used instead of the two processes required in the past, resulting in a significant reduction in time and cost.
Precision shear processing
Precision shearing is a process for creating shear surfaces that are superior to those produced by ordinary shearing. The objective is to minimize the occurrence of sagging*1 and burrs*2 and to improve the cross-sectional shape. The following specific techniques are available
- Shaving process: A process in which the entire cut surface is sheared to eliminate the fracture surface. The end face is shaved 3 to 10% of the plate thickness.
- Fine blanking process: A processing method that suppresses the occurrence of sagging by using a special press machine with a V-shaped plate holder and a reverse plate holder installed.
- Finish punching method: A technique that uses a smaller clearance than the normal punching process to prevent cracking.
- Opposed-die shearing method: A technology that eliminates fracture surfaces and suppresses sagging, using a special double-action press with protrusions on the upper and lower dies.
*1: Uneven cutting surface occurs on the punch side. This refers to the phenomenon in which the plate deforms during cutting and the shear surface is no longer smooth.
*2: This is a microscopic protrusion or sharp part that remains after cutting and occurs on the die side. It is caused by the material remaining without being completely detached during cutting.
Main machines used for shearing
In shearing, the material is mechanically cut using press machines. Here are some of the main machines commonly used in shearing.
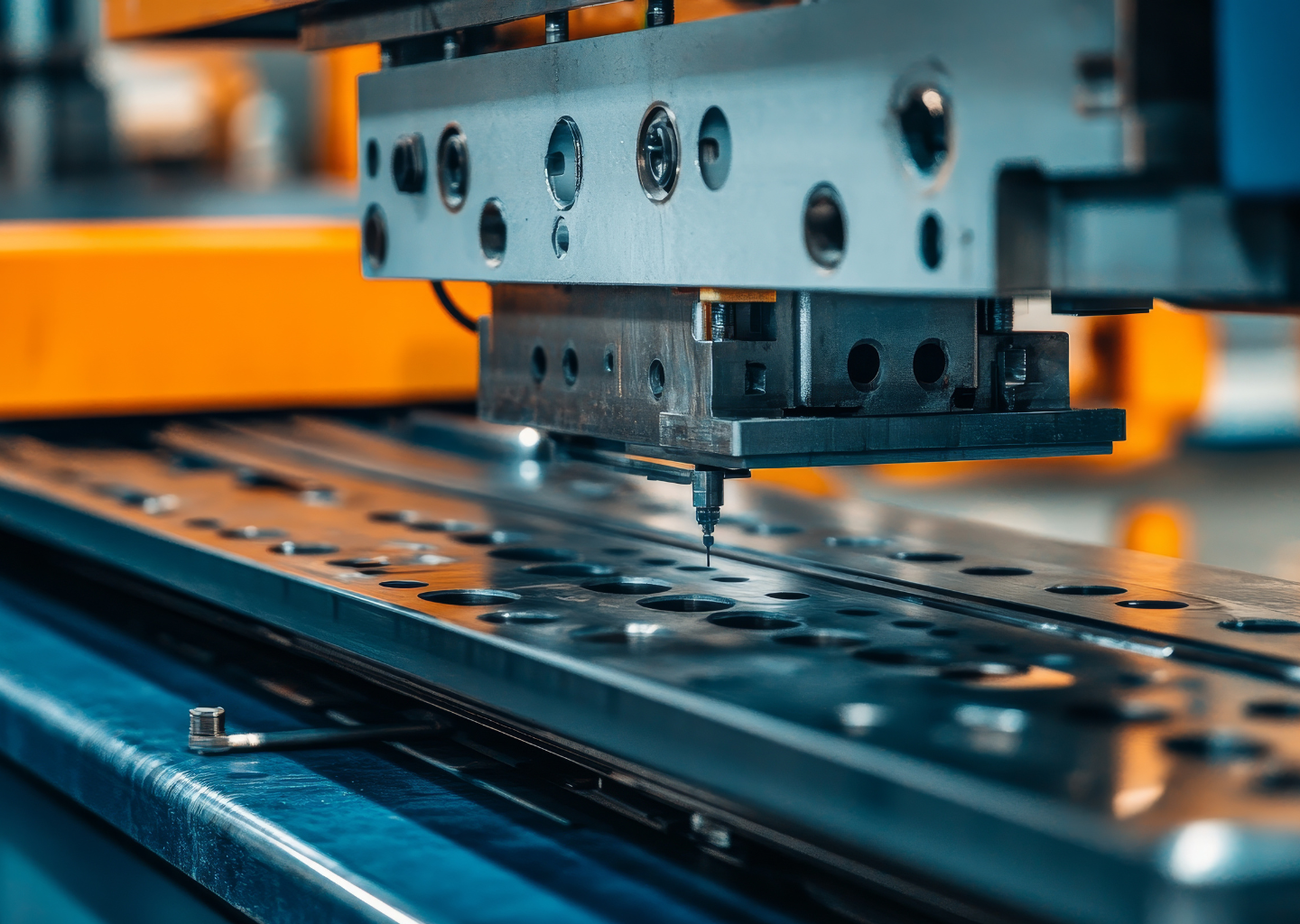
shearing machine
Shearing machines specialize in cutting processes by shearing. It is characterized by blades arranged vertically like scissors, and can efficiently cut materials by applying pressure. However, it is important to note that the plate thickness that can be handled depends on the design of the shearing machine. If the plate thickness is too thin, it will be deformed and difficult to cut. Conversely, if the plate thickness is too thick, it will be physically difficult to cut and the blade may be damaged.
press machine
A press is a machine widely used for shearing. It is a combination of a plate and a die, and pressure is applied by a press. General-purpose press machines are designed to simply press by setting pressure and other parameters, and their high processing speed enables efficient shearing processing. They are also versatile machines that can be used for bending and drawing processes.
turret punch press
A turret punch press is a type of press machine that uses a general-purpose die set. These machines are used for punching and drilling using general-purpose dies such as round or square dies. Since there is no need to create a dedicated die and the press can press at high speed, it is characterized by high production efficiency. They are also widely used in mass production.
fine blanking press
Fine blanking presses are specialized presses used for fine blanking, a type of precision shearing process. It is designed to apply optimum pressure to improve the quality of the sheared surface. This press is one of the most popular machines in the field because it reduces the post-processing steps after shearing, which leads to cost reduction. Another major advantage of this machine is that it can process materials with low processability, such as stainless steel, with high accuracy.
Precautions for manufacturing products by shearing
This section describes the precautions for manufacturing products by shear processing.
Countermeasure against burrs and sagging
To improve the quality of the shearing process, it is necessary to prevent sagging and burring. Ideally, the entire cut surface should have a uniform shear surface, but there will be sagging on the punch side and burrs on the die side. These can be removed by machining, but effective countermeasures are required for precision shear processing as well.
Set clearances appropriately
Clearance must be set appropriately according to the type of material, plate thickness, die shape, and punch speed. If the clearance is too large, material distortion will increase and may require corrective processing. On the other hand, if the clearance is too small, the material cannot be cut, increasing the possibility of problems. Since the optimum clearance value varies depending on the machine used, it is important to set the clearance according to the machine used in your company.
Adjusting board thickness
When shearing, the plate thickness must be adjusted. Although it depends on the machine and material used, a plate thickness of 9 mm or less is suitable for steel plates and mountainous steel, and a bar diameter of 10 mm or less for round steel. It is also important to adjust the clearance between the die and punch according to the plate thickness. Generally, a larger clearance should be set for larger plate thicknesses. Adjust the clearance to the optimum value while checking the occurrence of sagging and burring.
Summary
Shearing is a cutting method that breaks material by applying forces simultaneously in opposite directions. Shearing is performed mechanically using presses and other equipment, enabling high-speed and high-volume production of products. However, in order to precisely shear and finish products, appropriate clearance settings and countermeasures against burrs and sagging are indispensable. When manufacturing products by shearing, it is important to consider these issues while preparing the manufacturing flow and establishing a system for efficient production.
We invite you to start your parts manufacturing with "Taiga" - Taiga is a highly secure and state-of-the-art technology that allows us to manufacture parts according to your needs. Please feel free to contact us first. Let's create new value for your parts together!
For more information about Taiga, click here.