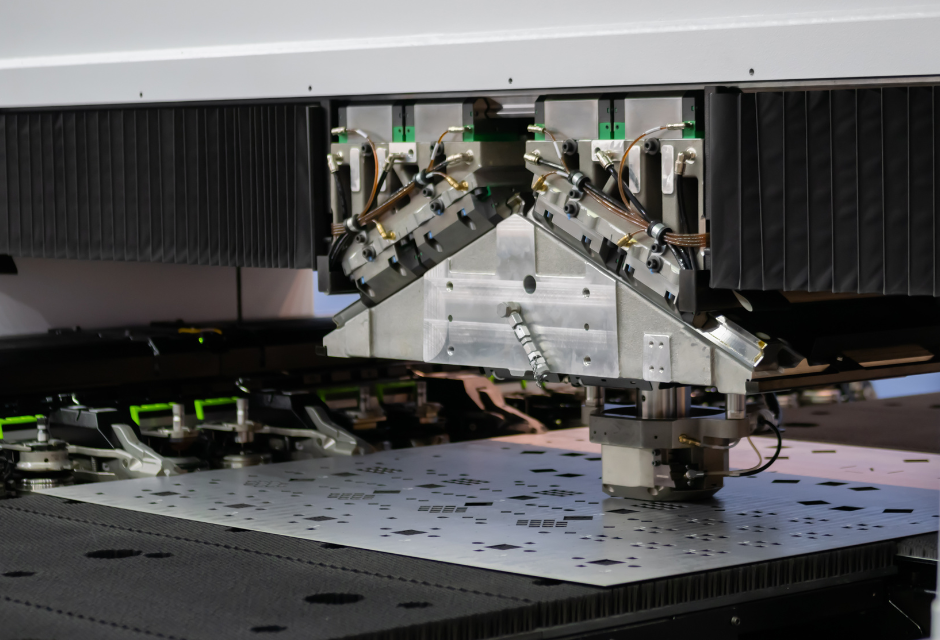
Shearing is an important operation in metalworking. Good use of this process can lead to more efficient productivity. However, there are various types of machines to be used, and there are certain points to be considered in processing. Without a proper understanding of these factors, it is impossible to improve productivity.
In this article, we will provide a detailed explanation of the basic knowledge of the shearing process.
For more information about Taiga, click here.Table of Contents
What is shirring processing?
This is the process of cutting sheet metal materials such as aluminum and stainless steel. The work is generally performed using a special machine with upper and lower blades. The upper blade is slightly angled and the lower blade is horizontal to the material. The principle of cutting the material is the same as that of scissors used in daily life.
What type of machine?
Next, let's take a closer look at the different types of shearing machines.
mechanical shear
A machine in which the "ram" is driven by the rotational motion of the flywheel. The processing speed is extremely fast, making it ideal for cutting thin sheets. The simple structure makes maintenance easy, but the impact during cutting tends to be large, resulting in vibration and noise.
They are also not good at cutting thick metals, and most are not compatible with plates larger than 6 mm.
Hydraulic shear
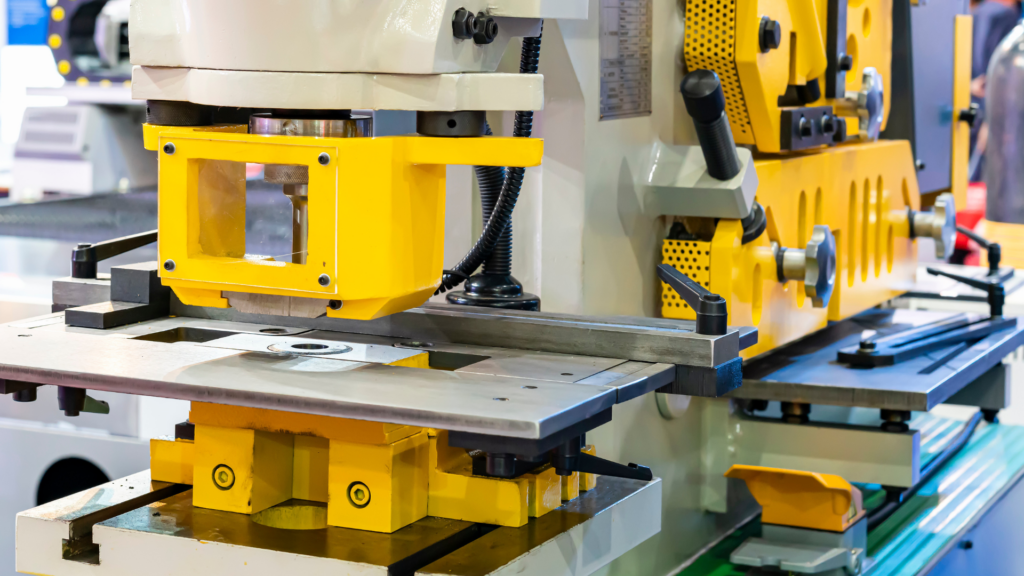
As the name implies, this is a processing machine that uses hydraulic pressure. The speed is almost the same as the mechanical type, but the hydraulic pressure provides stable power, allowing even thick materials to be cut smoothly. Many companies have introduced these machines because they can finish cross sections cleanly and produce little shock and vibration noise.
However, daily maintenance is essential due to the risk of problems caused by oil leaks.
cornershire
These are machines that excel at V-shapes and notches. While the mechanical and hydraulic shearing machines introduced earlier cut materials in straight lines, corner shears are used for a completely different purpose. This machine is often used to make box-shaped products, for example.
stomping shear
As the name implies, this is a machine in which the blade is operated by pedaling with the foot. This is the most primitive type of shearing machine currently being developed.
However, thin metal sheets such as zinc and copper and resin plates can be adequately processed.
vibroshire
A shearing machine is a machine that shears by vibrating the blade. Basically, shearing machines are good at processing straight lines, but vibro shears can also shear curves.
In recent years, it has been used less frequently, partly because of the advent of laser processing machines.
Other Cutting Machines
In addition to shearing machines, the following cutting machines may be used to cut plates
- Laser Processing Machines
- Plus Processing Machine
- disk grinder
Let's take a closer look at each of these.
Laser Processing Machines
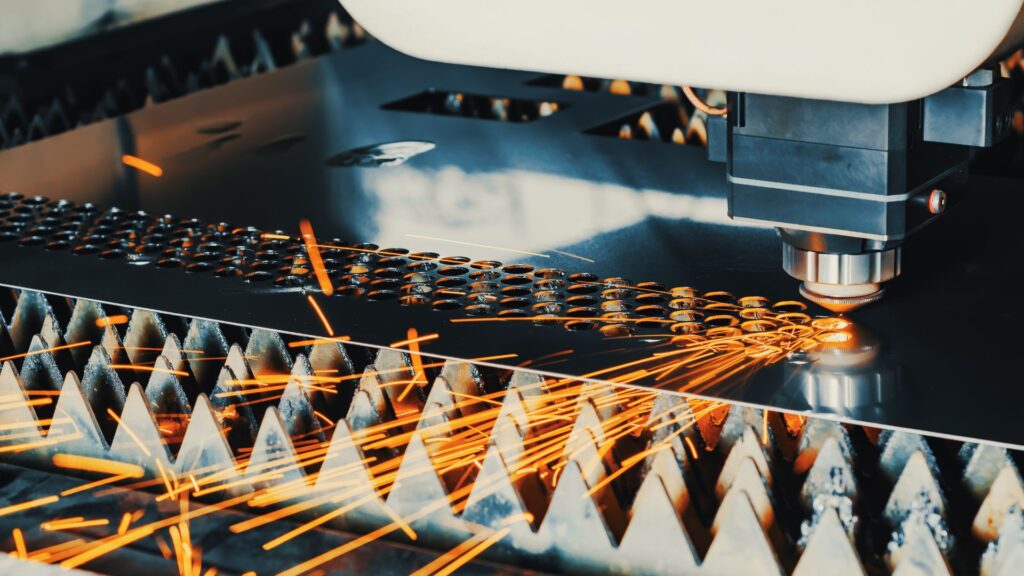
A laser cutting machine is a machine that cuts metal by irradiating it with a laser. Complex cutting, marking, and engraving are often performed with these machines. Also, since the heat from the laser melts and cuts the metal, it is less likely to have "burrs" or "chatter" on the cross section.
However, they are more costly than the shearing machines introduced earlier, so it is said that they should be used for mass production.
Plasma processing machine
A plasma cutting machine is a machine that uses electrical energy from arc discharge to cut metal. Basically, they are used only for cutting metal materials.
It is superior to laser cutting machines in terms of cost, but the beauty and quality of the cut is slightly lower.
disk grinder
Disk grinders are handheld cutting machines. A grinding wheel is attached to the tip and rotates at high speed to cut metal.
Basically, it is used for grinding small items and is not well suited for cutting sheet metal materials.
Typical manufacturers and their characteristics
Typical manufacturers that have deployed shearing machines include
- Amada
- Aizawa Ironworks
- Komatsu Industries
Amada is a major manufacturer of sheet metal machines in general and is quite well known. The company handles a wide variety of machines, including mechanical and hydraulic as well as automatic shearing.
Aizawa Ironworks is a manufacturer of mechanical shearing and press brakes. We also deal in automatic shearing systems and "servo shearing" utilizing servo motors.
Komatsu Industrial Machinery handles sheet metal machines in general and mainly sells hydraulic shearing machines. They are famous for their high operability and are often introduced in educational institutions.
Points to be aware of when processing
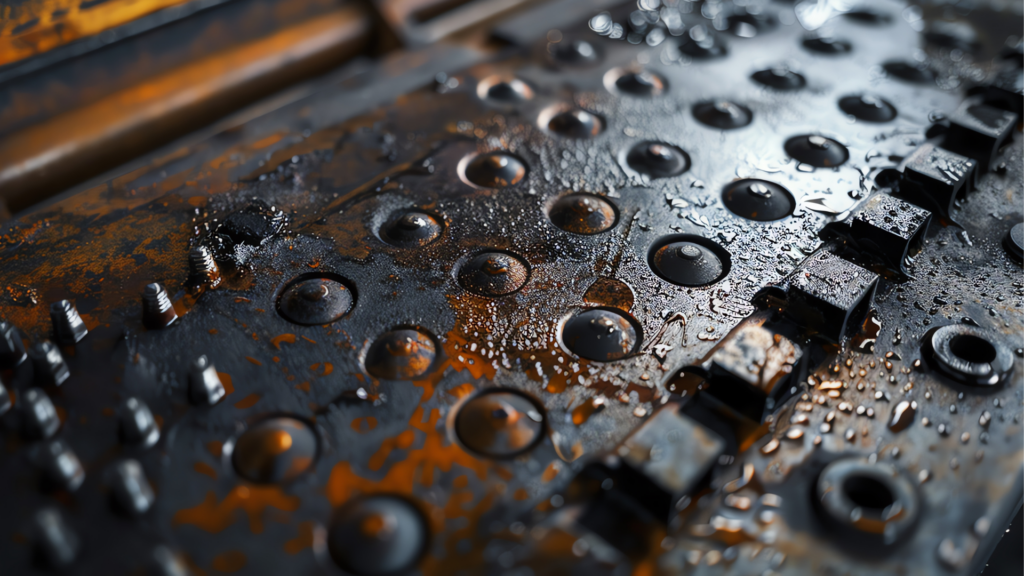
Next, let's take a closer look at the key points of the shirring process.
Adjust clearance
The gap between the blade and the cutting edge is called "clearance," and if this gap becomes too small, "burrs" and "run-out" are likely to occur. To maintain quality, the clearance must be adjusted each time when processing.
By doing so, we can extend the life of the blade as well as the quality.
Adjust shear angle
Blades attached to shearing machines are not installed in a straight line, but are angled. The angle is called the "shear angle" or "rake angle," and it is important to note that if the angle is not adjusted appropriately, "deflection," "twisting," or "warping" is likely to occur. The larger the shear angle, the less force is exerted during cutting, thus extending the life of the blade, but this also makes it more prone to the deformation described above, so be sure to adjust the angle appropriately.
Devise a board layout
In the shearing process, it is necessary to minimize waste as much as possible. To achieve this, it is necessary to take board in consideration of yield.
Yield is the ratio of production volume to input materials; the higher the yield, the less waste.
Plate removal has a significant impact on the total cost of the project, so let's try to get as much processed material as possible.
Note the maximum plate thickness.
Each shearing machine has its own maximum plate thickness. Simply put, this is "the upper limit of the plate thickness that can be processed," and using a material of a thickness that is not compatible with that machine will increase the possibility of failure.
To avoid such problems, select the best shearing machine for your material.
Cautions for shirring process
Although it is a basic rule, when performing shearing processing, please keep your hands away from the operating parts. Although shearing processing is a very convenient processing method, it is also a dangerous one. Putting your hands or body close to the moving parts while they are in motion can cause an accident.
Also, stay away from the back where the material comes out after processing, as it is dangerous.
Order your shirring process from "Taiga"!
Shearing is an important operation in metalworking. However, there are many machines available, each of which supports a different processing method and usage. It is also a very dangerous process, so if you are not comfortable with in-house processing, it is recommended that you ask an outside contractor to do the work. However, there are many companies that support shearing processing, so you may be wondering where to request it.
In such cases, Taiga can help.
Taiga is a manufacturing matching platform that connects users and partners. If you are interested in Taiga, please feel free to contact us.
Summary
Shearing is the process of cutting sheet metal materials such as aluminum and stainless steel. It is an indispensable operation in metalworking, and its skillful use can lead to improved productivity.
However, as mentioned above, there are a variety of shearing processing machines, and advanced knowledge and skills are required during processing. Therefore, it is recommended to consider outsourcing when necessary.
If you are interested in finding the right production partner or affiliate for your company, please take advantage of Taiga, a manufacturing matching platform that connects users and partners.
For more information about Taiga, click here.