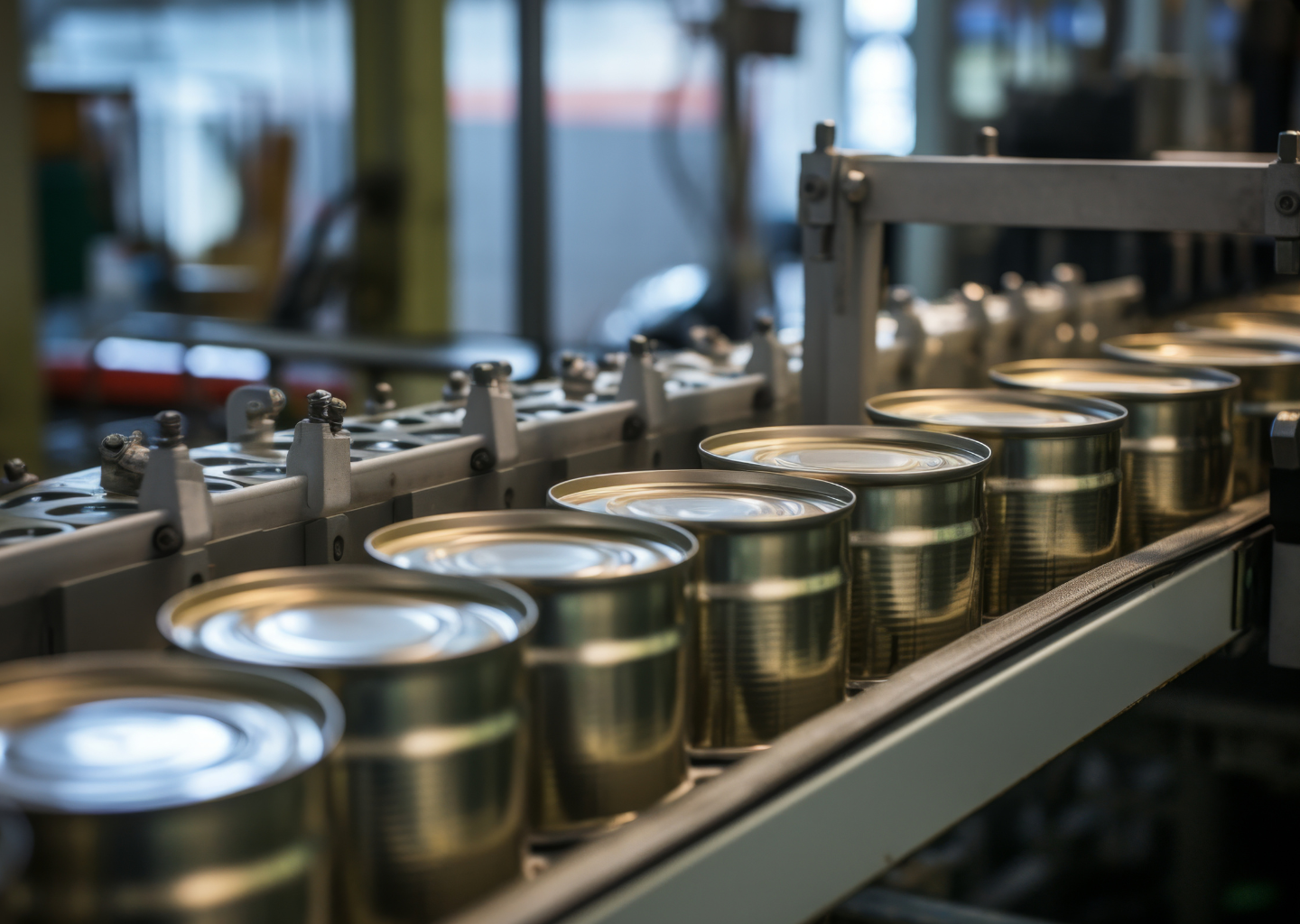
Can manufacturing is a technology that processes metal to produce products such as cans and tanks. There are various methods of metal fabrication, of which sheet metal fabrication is the most well-known. Can manufacturing processes are used for different materials and applications as needed. This article describes in detail the characteristics of can manufacturing, its differences from sheet metal working, and specific work processes. It also explains the key points of business operation based on the work process of can manufacturing.
Table of Contents
What is Can Manufacturing?
Can manufacturing is a metalworking technology used to produce can-shaped products for containers and cases. Typical products include drums and tanks, but machine covers and structural frames are also manufactured by can manufacturing. This technology is also used in the manufacture of parts for large equipment and ships, and combines a wide variety of metalworking techniques.
Difference between canning and sheet metal working
Sheet metal fabrication is a metal working method that uses sheet metal to create products. Because can manufacturing also often starts with sheet metal, it is sometimes referred to as "can sheet metal fabrication. However, can manufacturing differs from general sheet metal processing in that it is specialized for the manufacture of can products. Here we explain the difference between can manufacturing and sheet metal working.
Differences in applications and products
The can manufacturing process produces large tanks, vessels, and other structures. Typical products include oil refining equipment, steam boilers, machine tool frames, industrial ducts, and water tanks for apartment complexes.
On the other hand, sheet metal working is not limited to can-shaped products, but is used to manufacture a wide variety of metal products. Typical products include home appliances, construction materials, and automobile parts, but a wide variety of everyday metal products are also made by sheet metal working. For example, aluminum cans such as beverage and food cans are part of sheet metal products in a broad sense.
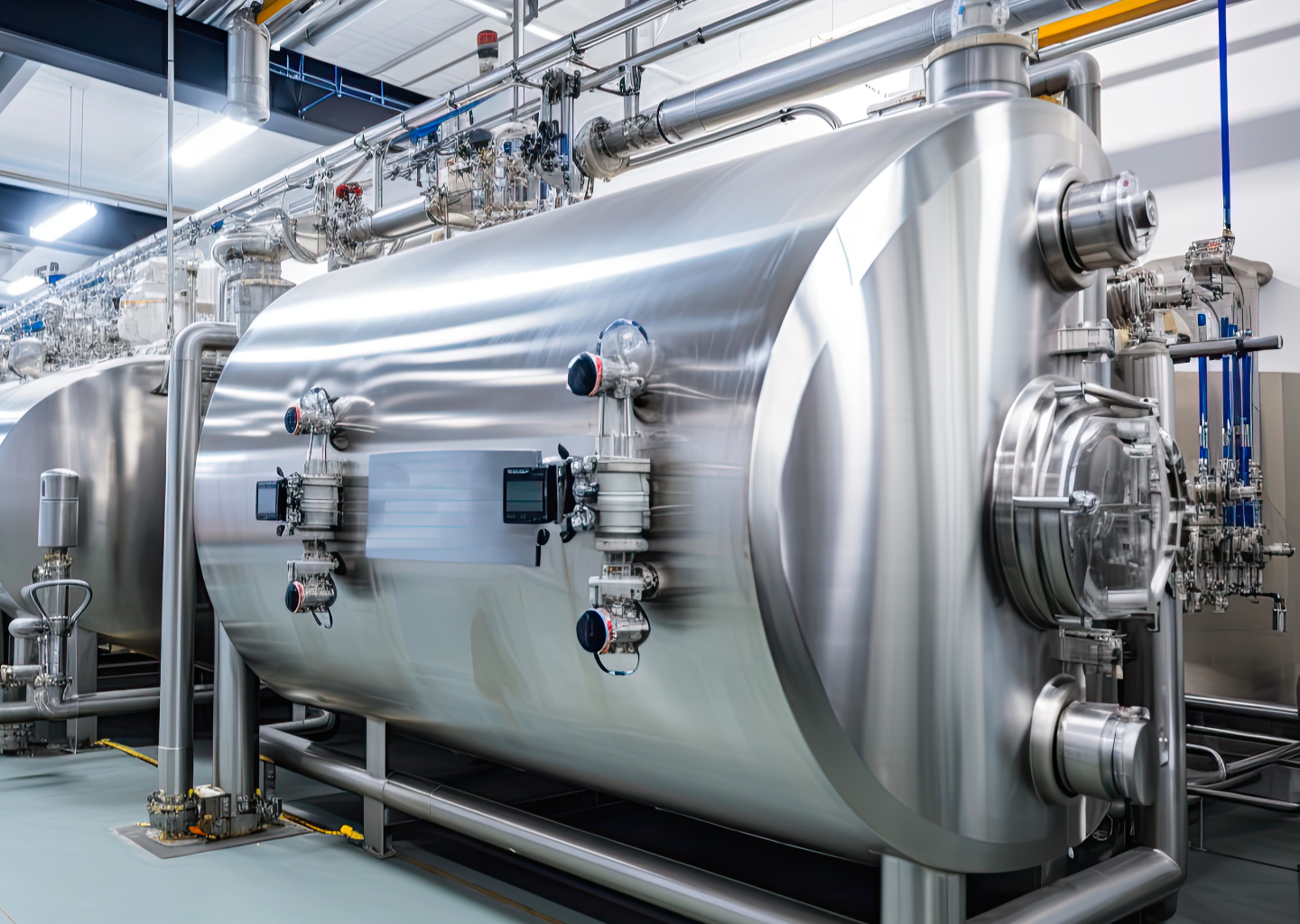
Difference in material and plate thickness
In can manufacturing, thick metal sheets with high strength and durability such as stainless steel, usually 7 mm or thicker, are commonly used. As a characteristic of the can manufacturing process, shaped steel and angle steel are frequently used in addition to plates.
In sheet metal fabrication, on the other hand, soft metals such as aluminum are often used, and thin, lightweight metal sheets are processed to manufacture products. Although stainless steel is sometimes used, metal sheets thicker than 7 mm are rarely used. This processing method is often aimed at cost reduction and efficient mass production using thin metal sheets.
Difference between canning and machining
Machining is one of the processing methods used in can manufacturing. Machining methods that use machines such as machine tools and presses are generally referred to as "machining. Since can manufacturing also uses machines, it is positioned as part of the machining process.
Machining has a wide range of applications and, like general sheet metal fabrication, may involve the use of thin metal sheets or materials such as aluminum or copper. Although manual processing is not included in machining, modern production processes almost always include machining.
Advantages and disadvantages of canning process
Advantages of Canning Process
The can manufacturing process offers the following advantages in terms of product manufacturing.
- Suitable for manufacturing large products
- Suitable for processing high-strength products
- Thick metal sheets are available.
Can manufacturing is ideal for manufacturing large tanks, structures, and other large products. The use of stainless steel and other materials with superior strength and durability make for sturdy products, and the use of metal sheets thicker than 7 mm makes it possible to manufacture products with high pressure resistance.
Disadvantages of canning process
Can fabrication has the following disadvantages when compared to general sheet metal fabrication.
- Requires advanced design skills and processing technology
- Manual manufacturing is often done by hand, making automation difficult.
- Not suitable for mass production because it takes time to manufacture.
- Production costs tend to be high
Can manufacturing requires advanced skills in machining and welding, and the ability to design large structures. Another disadvantage is that it requires a lot of manual work and is difficult to automate, resulting in longer manufacturing times and higher costs.
Work process of can manufacturing
In the can manufacturing process, various processing techniques are combined to finish can-shaped products. Here, we have summarized the work process of can manufacturing from order receipt to delivery. Let's take a quick look at the overall picture of can manufacturing.
Meeting and design
The first step is a meeting with the customer. The first step is to interview the customer about the can product they are looking for and propose a specific design. The cycle of design proposals and feedback is repeated to determine the final product that meets the customer's needs.
At this stage, it is important to discuss product specifications, delivery dates, and costs to clarify the direction of the project.
Drawing
Once the design is finalized, drawings are prepared. Drawings not only serve as explanatory materials for customers, but are also important documents that are indispensable for coordination between design and processing. When creating drawings, we take into consideration the differences in material characteristics and their impact on production efficiency, and provide estimates that meet the customer's requirements. Making accurate and detailed drawings prevents errors in subsequent processes and increases productivity.
Cutting and fusing
Once the drawings are completed and a contract is signed with the customer, the manufacturing process begins. First, materials such as metal sheets and shaped steel are procured and cut into the required shapes by cutting or fusing. Relatively thin metal sheets can be cut by laser cutting or punching.
On the other hand, when thicker materials are used, it is necessary to select a cutting method that melts the metal while cutting, such as gas cutting or arc cutting.
Drilling and bending
The cut-out metal material undergoes drilling (punching) and bending processes. The purpose of the drilling process is to pre-drill holes in the plate material for bolts and other parts to pass through when assembling parts.
Bending, on the other hand, is the process of bending a metal sheet into the shape of a can. Various methods, such as die bending and roll bending, are selected according to the shape of the final product, the type of material, and the thickness of the sheet.
weld
In the can manufacturing process, welding is one of the most important processes. For example, simply bending a metal sheet into a cylindrical shape does not make a perfect cylinder. Welding must melt the metal and cool it to join it.
There are various welding processes, such as arc welding, argon welding, and tig (TIG) welding, and the appropriate method is selected according to the product material and application.
Surface Treatment
Because the products manufactured in the can manufacturing process are often required to have long-term durability and a beautiful appearance, surface treatment is applied according to customer requirements. For example, plating is performed to improve corrosion resistance, and polishing and painting are performed to achieve a beautiful finish. This is an important process to add value to the product.
Assembly
The processed parts are finally assembled into finished products. During assembly, bolts and other parts are used to secure the parts in place at the points prepared by the drilling process. Manual assembly is the mainstay of can manufacturing, but work efficiency can be improved by utilizing hand tools and other machines.
inspection
Assembled products are inspected prior to shipment. Inspection verifies that the product meets the requirements set forth in the contract with the customer. Inspection items include dimensional accuracy, visual quality, and functionality. Only products that pass all inspection items are delivered to the customer.
Important points in can manufacturing process
Since can manufacturing requires advanced technology, the wider the range of products your company can handle, the more diverse your customer base you may be able to attract. This is especially useful when manufacturing parts that require strength and durability.
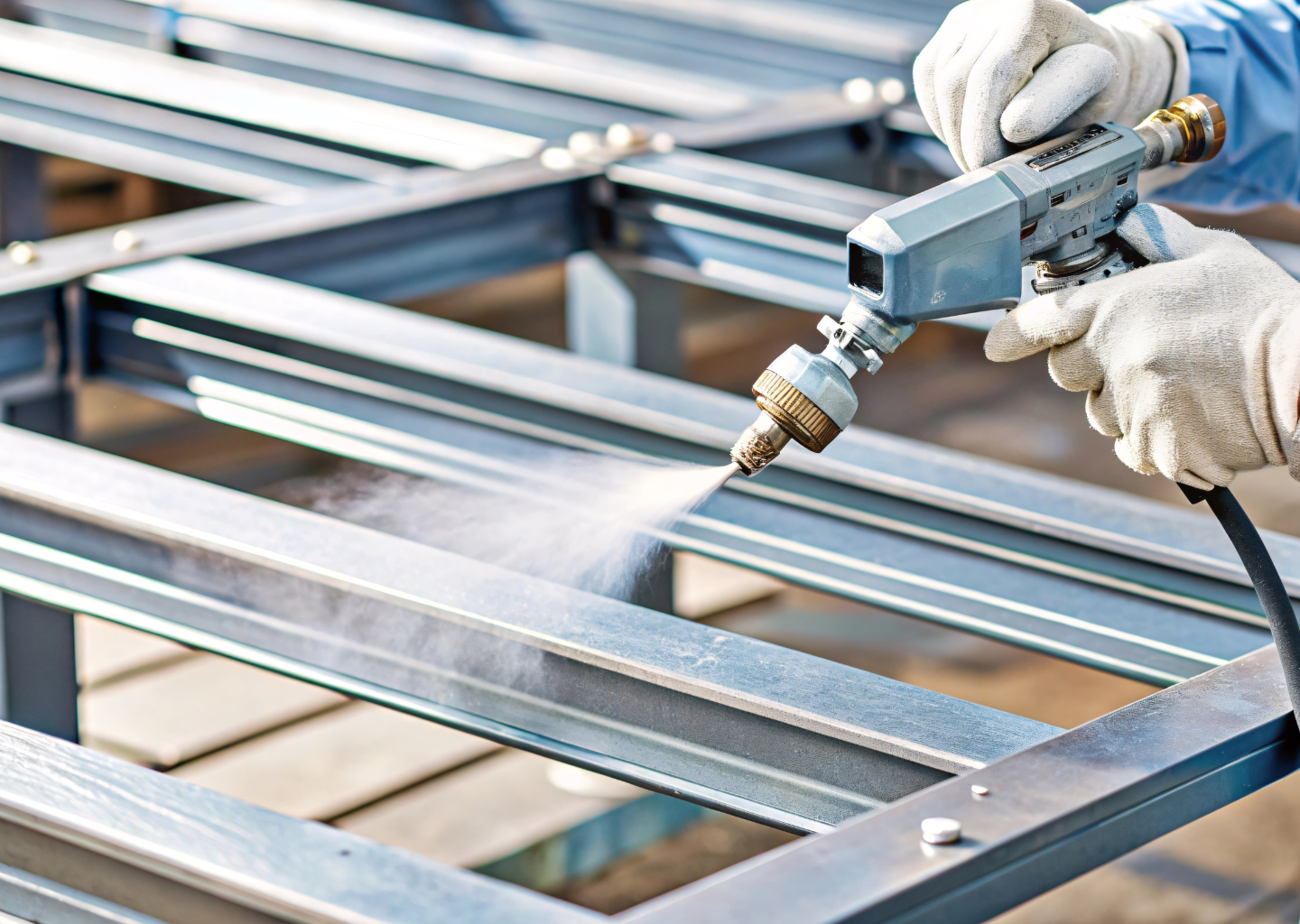
Advantages of Make-to-Order
In the can manufacturing process, each product is often made to order and can be customized to meet the specific needs of the customer. The make-to-order model reduces the risk of holding unnecessary inventory and allows the company to produce only what is needed when it is needed.
Utilization of the latest technology
Manual labor is common in the can manufacturing process, but recently robots and digital technology have been introduced. This has enabled automation of welding and processing, resulting in more efficient production. Furthermore, the introduction of production management systems and customer management systems can improve overall operational efficiency and reduce costs.
Production Flow Optimization
In the can manufacturing process, products are completed through many processes. Therefore, smooth coordination between each process is important. Improving the production flow can be expected to increase work efficiency and production speed. In particular, strengthening communication among personnel in charge of each process will lead to smooth production.
Summary
Can manufacturing is a metalworking technology used primarily in the production of large structures and tanks required in industry. The can manufacturing process begins with design, followed by a lengthy process of cutting, machining, welding, surface treatment, and assembly to produce the can product.
In order to effectively carry out can manufacturing, it is essential to have advanced technical capabilities and an efficient production process. Furthermore, by adopting a business model based on build-to-order production, it is necessary to establish a system that enables prompt provision of optimal products that meet customer needs. This will enable us to eliminate waste and achieve higher customer satisfaction.
We invite you to start your parts manufacturing with "Taiga" - Taiga is a highly secure and state-of-the-art technology that allows us to manufacture parts according to your needs. Please feel free to contact us first. Let's create new value for your parts together!
For more information about Taiga, click here.