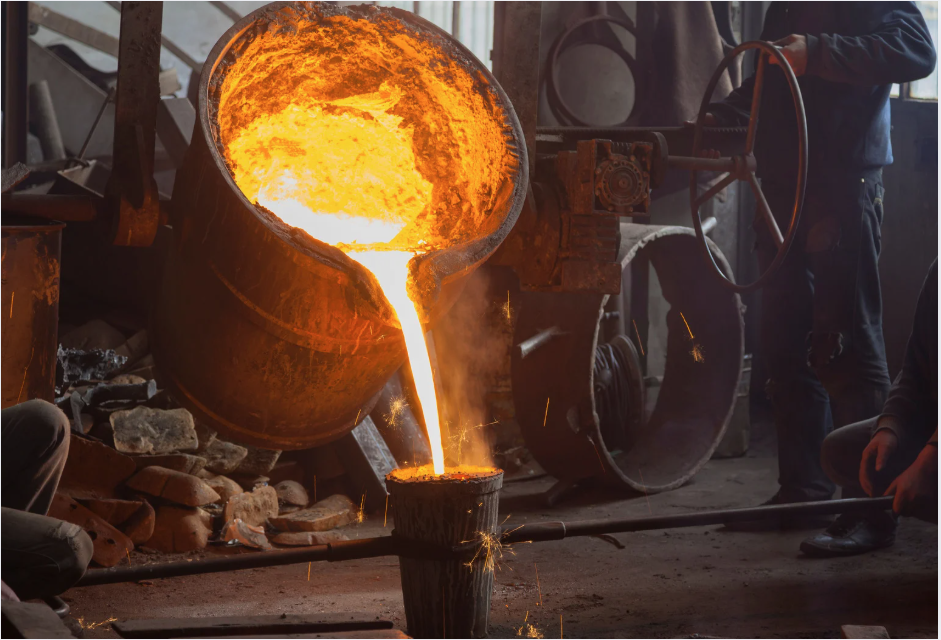
This article explains the advantages and disadvantages of sand casting, plaster mold casting, and metal mold casting, as well as cost quotes, delivery times, and key points for selecting a supplier.
In addition, we will also present information you need to understand when considering small-lot production, from ways to reduce initial costs to comparisons with 3D printing.
Receive technical proposals at TaigaTable of Contents
What are the advantages of requesting casting in small lots?
A major benefit of small-lot production is increased efficiency in product development and market competitiveness.
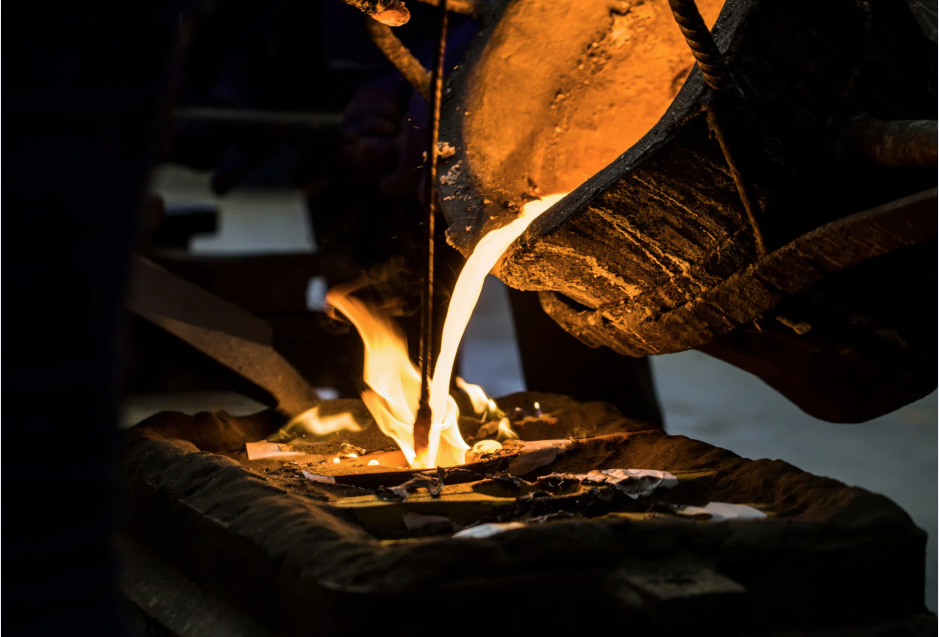
Small-lot production allows us to respond quickly to defects discovered during the manufacturing process, minimizing wasted parts production and costs compared to mass production.
Another advantage is that products can be adjusted based on market response, making it easier to adapt to modern consumer needs.
It is also suitable for high-mix production, enabling variation development to meet the demands of various users.
In recent years, as times change, manufacturers have become more cost-conscious, and the demand for small-lot production in product development is increasing.
Main casting method suitable for small lot production
There are three main casting methods suitable for small lot production
Sand casting
Sand casting is a method of pouring molten metal into molds made of hardened sand, and is characterized by low mold-making costs and suitability for small-lot production.
It is also suitable for casting high-melting-point metals such as iron, and can produce complex shapes and hollow structures, making it suitable for manufacturing large products.
Another advantage is that the modeling speed is fast and can be produced in a short period of time.
On the other hand, dimensional accuracy is relatively low, and the unit price tends to be high due to the need to remake the mold each time.
There is a disadvantage of rough surfaces, but surface quality has improved in recent years with the use of artificial silica sand and the evolution of curing methods using resin.
Plaster mold casting (lost cut casting)
Plaster mold casting is a method of making a mold by making a prototype with wax and covering the prototype with plaster around it.
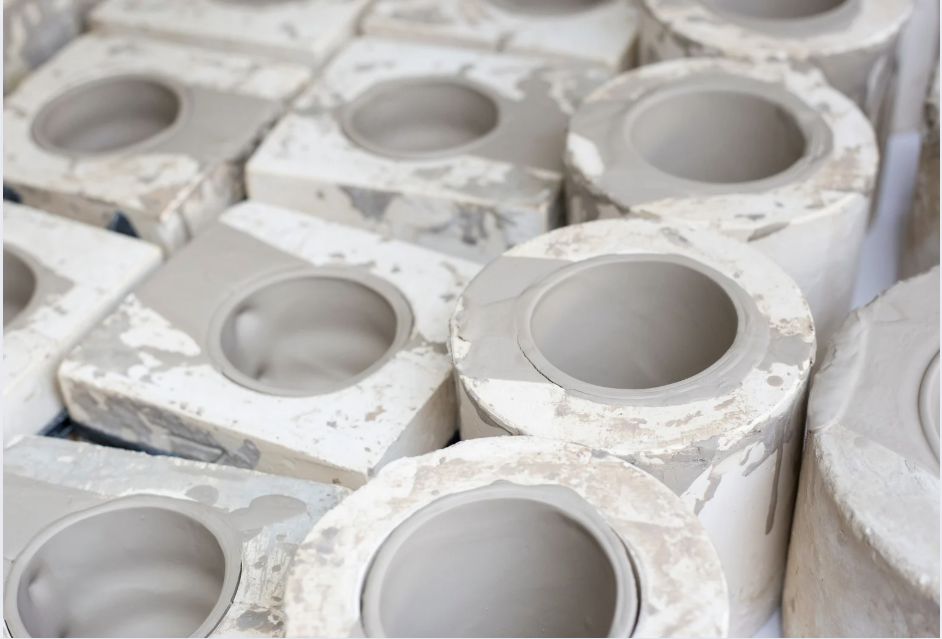
The advantage is that initial costs can be reduced because molds are not required. It is also suitable for manufacturing complex shapes and precision parts.
With a smooth finish and precision equivalent to die casting, it is often used for die casting prototypes and small lot production.
However, costs tend to be higher than sand casting.
Die Casting
Mold casting is a method of molding by pressing molten metal into a metal mold.
Since the molds can be used repeatedly, they are suitable for mass production, allowing for a smooth transition from prototype to mass production.
Another advantage is that the cooling rate is fast, which improves the mechanical properties of the castings.
It also has excellent dimensional accuracy and surface quality, making it suitable for small-lot production of precision parts and products where appearance quality is important.
However, the initial cost of mold fabrication is high, so costs may be higher for small-lot production.
How costs and prices are determined for small lot casting
The cost of small lot casting is determined primarily by the following factors
- Casting method
- Product Shape and Size
- Materials to be used
- Post-casting machining and finishing
- Number of lots
- Delivery Time
In general, sand casting tends to be relatively inexpensive, while plaster and mold casting tend to be more expensive.
Also, the cost will naturally be higher for products with complex shapes and expensive materials such as titanium and stainless steel.
On the other hand, as the number of lots increases, the unit cost tends to decrease because fixed costs are spread over a larger number of lots.
As for cost quotations, production of 40 lots of engine parts costs about 37,000 yen/piece for sand casting and 36,000 yen/piece for plaster casting.
When requesting small-lot casting, request quotes from multiple vendors and compare costs.
How to reduce the cost of small lot casting
To reduce the cost of small lot casting, the following methods are available
Use a simplified mold
Molds are necessary tools for mass production of products in plastic molding and casting, but the initial cost is high.
Therefore, the use of simplified molds enables cost-saving manufacturing and processing for small-lot production and prototyping.
Simplified molds made of aluminum or with simplified structures are not only less expensive than main molds, but can also be delivered in a shorter period of time.
However, it has limitations in durability and product shape, and can only be used for production of about 2,000 shots.
Use aluminum die-cast wooden molds
Aluminum die-casting wooden molds are a method of manufacturing aluminum die-cast products using molds made from processed wood, and are attractive in that they can be manufactured with short delivery times and at low cost.
High-precision wooden molds can achieve dimensional accuracy and smooth cast surfaces similar to die casting.
The range of production is wide from prototyping to small lot production, and can be substituted for stamping and forging.
What is the turnaround time for small lot casting?
Delivery time for small-lot casting varies depending on the product dimensions, shape, casting method, and busyness of the supplier.
The standard turnaround time is about one month, but this may be extended depending on the complexity of the shape and the presence of surface treatment, and it is necessary to consider that it may take several weeks to several months.
Points to consider when selecting a vendor for small lot casting
When selecting a vendor for small-lot casting, keep the following points in mind.
Number of lots handled
The minimum number of lots that can be handled varies from vendor to vendor.
In general, most vendors will be able to handle sand and plaster mold castings from less than 10 pieces, die castings from 30 pieces, and mold castings from about 50 pieces.
Selecting a vendor that is flexible enough to accommodate future increases in production will also lead to long-term requests.
Supported materials and supported processing methods
The range of materials and processing methods that a foundry can handle greatly affects the potential for product development.
As a basic rule, check for compatibility with major aluminum alloys (AC2A, AC4B, ADC12, etc.) and magnesium alloys, but also check for compatibility with special materials.
It is also important to be able to offer complex processing methods such as post-casting machining and surface treatment.
For example, selecting a supplier with the technical capabilities to handle parts with complex geometries and products requiring thin-wall molding will enhance the quality and functionality of the product.
Past Performance
A vendor's past processing and manufacturing performance is essential to determine its technical capabilities and reliability.
Check for experience in manufacturing similar products and parts to the product or part you are requesting, as well as hollow casting and thin-wall molding.
If possible, we recommend that you ask to be presented with an actual sample to confirm the quality of the finished product directly.
Time to delivery
Accuracy and the ability to shorten delivery times are important in managing product development schedules.
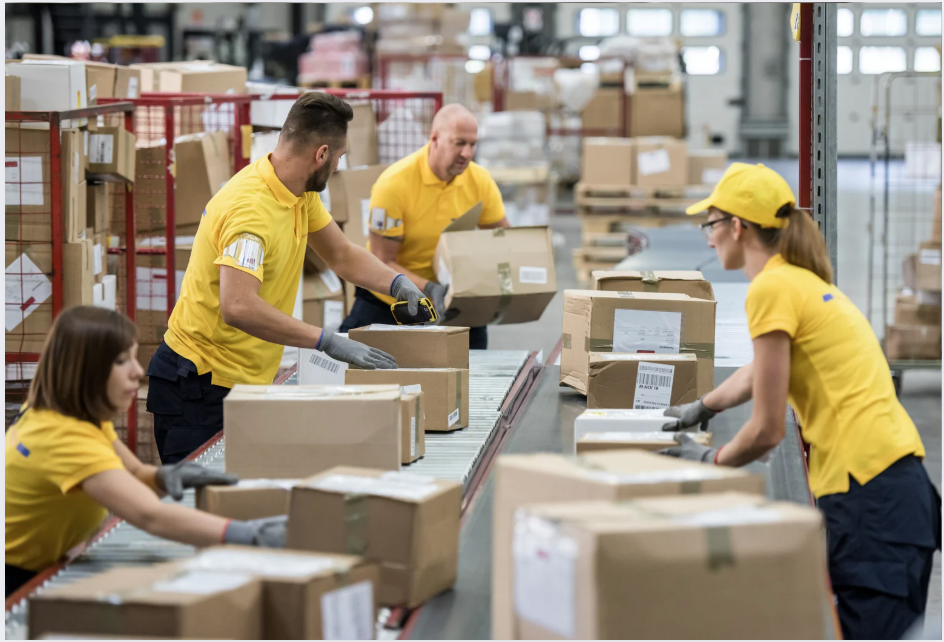
Check for the availability of a digital linkage system that allows 3D CAD data to be directly reflected in the casting process, as well as the implementation of a process visualization and progress management system.
In addition, a track record of emergency response and shortened turnaround time will make the request more reliable.
Selecting a vendor that can reliably meet your company's delivery requirements will lead to smooth product development.
In some cases, 3D printing is recommended for small-lot production.
3D printing is also recommended for prototypes of complex shapes and parts for design verification.
Since 3D printing does not require molds, it can be produced in a shorter time and at a lower cost than casting.
In particular, 3D printing may be advantageous under the following conditions
- Very small lot production (1-10 pieces)
- Complex shapes that are difficult to produce by casting
- When rapid prototyping is required
- When material strength is not so demanding
Small lot production by 3D printing offers the following advantages
- Low prototyping costs
- High degree of freedom in design, easy to change specifications
- Complex shapes and hollow structures can be formed in one piece
- Improvement study with 3D data improves quality in a short period of time
However, the disadvantages are that it is less strong than cast products and the surface quality may be inferior.
Carefully consider the product's required specifications and production volume, and compare the advantages and disadvantages of casting and 3D printing to select the best production method.
Summary
Small lot casting is an effective means of cost and time efficiency in high-mix, low-volume production and prototype making.
However, it is important to make comparisons because a 3D printer may be more suitable for some cases, such as when very small-lot production or quick delivery is required.
Please refer to the casting methods and vendor selection points described in this article to find the best option for your company's needs.
If you are considering casting parts in small lots, please contact us.Taiga."Taiga is a free service that allows you to consult with experienced contractors.
We can efficiently proceed with the development of difficult or new parts, small-lot production, prototyping, and mass production while keeping costs low.
Receive technical proposals at Taiga