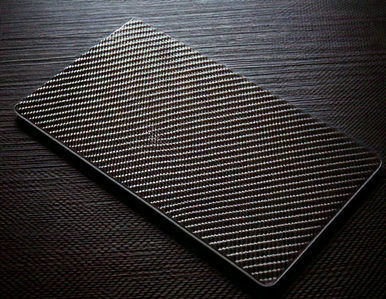
The choice of materials for the substrates is extremely important to improve the performance and long-term operation of satellites.
In recent years, CFRP (carbon fiber reinforced plastic) has been attracting attention as a material for such products.
CFRP is a lightweight, rigid, and durable material with excellent thermal stability and radiation resistance, making it suitable for use in space environments.
This article details the advantages of using CFRP for substrates, processing methods, and how to select a reliable supplier.
Receive technical proposals at TaigaTable of Contents
What is a substrate for satellites?
Substrates for satellites are critical components that support the structure and function of the satellite.
They function mainly as substrates for electronic devices and communication equipment, and must be able to withstand the harsh environment of space.
And in recent years, CFRP (carbon fiber reinforced plastic) has been attracting attention as a material that satisfies the high durability, light weight, and thermal stability required for substrates.
CFRP is a composite material that incorporates carbon fiber into resin as a reinforcing material, and is lightweight, tough, and corrosion resistant.
It demonstrates excellent performance stability even under severe conditions such as the vacuum conditions unique to space, rapid temperature changes, and radiation, and is capable of protecting satellite functions over the long term.
In large satellites, a sandwich panel structure combining CFRP and an aluminum honeycomb core has been adopted and is being used as a support substrate for solar panels, thus expanding the range of its utilization.
The use of CFRP as the material for the substraight, which is the heart of the satellite, will improve the overall performance and service life of the satellite.
Why CFRP is a suitable material for substrates
CFRP has excellent physical properties and is an indispensable material for improving the performance and long-term operation of satellites.
Here, we will explain in detail why CFRP is the best material for substrates, in terms of light weight and high strength.
Lightweight and durable
CFRP is extremely lightweight compared to metal materials, yet highly durable.
This characteristic allows for long-term operation of satellites while significantly reducing launch costs.
Since it is also resistant to corrosion, it has the advantage of being less susceptible to deterioration under the harsh environment of outer space.
In addition, the properties of resin materials provide better vibration damping than metal, which mitigates the stresses caused by vibration during launch and thermal cycling in space.
Furthermore, CFRP is characterized by higher fatigue strength than metallic materials.
In space, thermal expansion and contraction are repeated due to orbital temperature changes, but CFRP can maintain stable performance over a long period of time in these environments.
High rigidity
The rigidity of CFRP outperforms other materials in ensuring the shape stability of the substraight.
This rigidity ensures the precise placement and accurate operation of electronic and communications equipment and maximizes the functionality of the satellite.
CFRP is also suitable for mounting precision equipment because of its inherently low dimensional change due to temperature variation.
In addition, its high X-ray transparency facilitates nondestructive testing and operational verification, contributing to more efficient quality control and failure diagnosis.
What is required for CFRP machining of substrains
CFRP machining of substrains requires advanced technology and precision.
The main requirements are as follows
- High-precision dimensional control
- Ensure surface quality
- Thermal management considerations
- Balance between light weight and strength
Because substrates are the mounting base for electronic devices, they may require micron-level accuracy and require strict dimensional accuracy and processing technology.
Smooth and uniform surfaces are required for the formation of electronic circuits and mounting of components, and it is essential to control surface roughness and prevent microscopic scratches and defects.
Furthermore, in order to cope with temperature changes in space, processing that takes into account thermal conductivity and thermal expansion coefficient is required, and special processing techniques are used to improve the lamination configuration and thermal conductivity.
In order to achieve both strength and light weight, design of optimum fiber orientation and advanced molding techniques such as sandwich structures are also required.
Specific molding techniques include advanced technologies such as autoclave molding and RTM molding.
In addition, it is necessary to select a processing method suitable for the characteristics of CFRP, such as laser processing or ultrasonic processing.
Points to consider when selecting a contractor for CFRP processing of substraight
When requesting CFRP fabrication of a substraight, it is important to select the appropriate contractor.
Here are some details on how to choose a vendor.
Whether the company has experience in aerospace equipment processing
Processing aerospace equipment requires special skills and experience.
When selecting a vendor, please check their experience in CFRP processing in the aerospace field.
Specifically, check for experience in manufacturing parts for satellites and space equipment, as well as quality control certification (JIS Q 9100) for the aerospace industry.
A supplier with a proven track record in the aerospace field is likely to have a better understanding of the unique requirements of the space environment (e.g., degassing characteristics in a vacuum environment, radiation resistance, etc.).
For example, a track record of doing business with space agencies and major satellite manufacturers is an indicator of the vendor's technical capabilities and reliability.
Do you have a track record in satellite-related fields such as substrates?
For a more reliable supplier, it is advisable to choose one that has experience in the manufacture of substrates and other satellite-related components.
Our experience with satellites means that we understand and are capable of handling the unique requirements of the space environment (thermal cycles, vacuum environment, etc.).
It is also a good idea to check the vendor's past projects and past experience in cooperation with space agencies.
In particular, suppliers with experience in manufacturing substrates are likely to be familiar with related technologies such as electronics packaging and thermal design, which can be a significant advantage in optimizing the overall design and manufacturing process.
In addition, experience in solving problems and examples of improvements from past projects will also provide valuable know-how that can be applied to high-quality substrate production.
Is the quality control system sufficient?
If you are looking for high quality products, it is important to check the quality control system of the supplier in detail.
Specifically, check the following points
- Status of implementation of quality management system (e.g., ISO 9001)
- Availability of non-destructive testing equipment and qualifications of testing technicians
- Status of clean rooms and other manufacturing environments
- Introduction of traceability system
A supplier with a strict quality control system can be expected to produce and supply high-quality substrates.
Especially for products used in space applications, it is essential to ensure traceability throughout the entire process, from material procurement to manufacturing, inspection, and shipping, as any defects can cause significant damage.
Furthermore, since even the smallest contamination by foreign matter is unacceptable, the presence of clean room manufacturing and strict quality control processes are important criteria in the selection of a vendor.
Also check for a continuous improvement cycle and whether the vendor is flexible enough to respond to technological advances and new requirements.
Summary
By using CFRP for the substrates, lightweight, highly rigid, and durable satellite components can be manufactured.
However, CFRP processing requires advanced technology, so when selecting a supplier, be sure to thoroughly check its track record in the aerospace field and quality control system.
By utilizing the latest material and processing technologies, we can manufacture substrates with higher performance and reliability.
We expect to continue to develop new substrates that take full advantage of the characteristics of CFRP and improve manufacturing technology.
If you are considering manufacturing substrates utilizing CFRP, please contact us.Taiga."Please make use of the following
Taiga is a free service that allows you to consult with experienced contractors.
We can efficiently proceed with the development of difficult or new parts, small-lot production, prototyping, and mass production while keeping costs low.
Receive technical proposals at Taiga