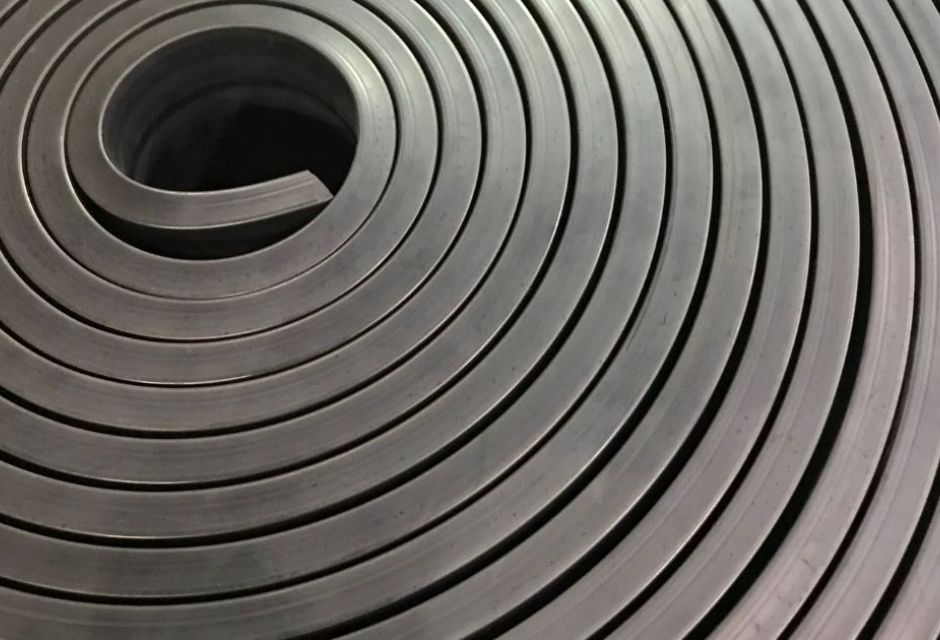
ゴムの射出成形は、複雑な形状の部品などの大量生産に向いており、電子機器から自動車部品、産業用部品まで幅広い産業で活用されています。
しかし、これからゴム素材を用いた製品や部品の製造を考えている方の中には「ゴム素材の特徴は?」「そもそも射出成形って何?」と、疑問をお持ちの方も多いでしょう。
そこで本記事では、ゴムの射出成形のメリット・デメリット、具体的な製造工程、さらには成形不良とその対策まで、製品開発担当者の皆様に役立つ情報を詳しく解説します。
射出成形以外のゴム成形方法との比較も行い、最適な製造方法の選択をサポートしますので、ぜひ参考にしてください。
Taigaで技術提案を受ける目次
ゴムの射出成形とは?
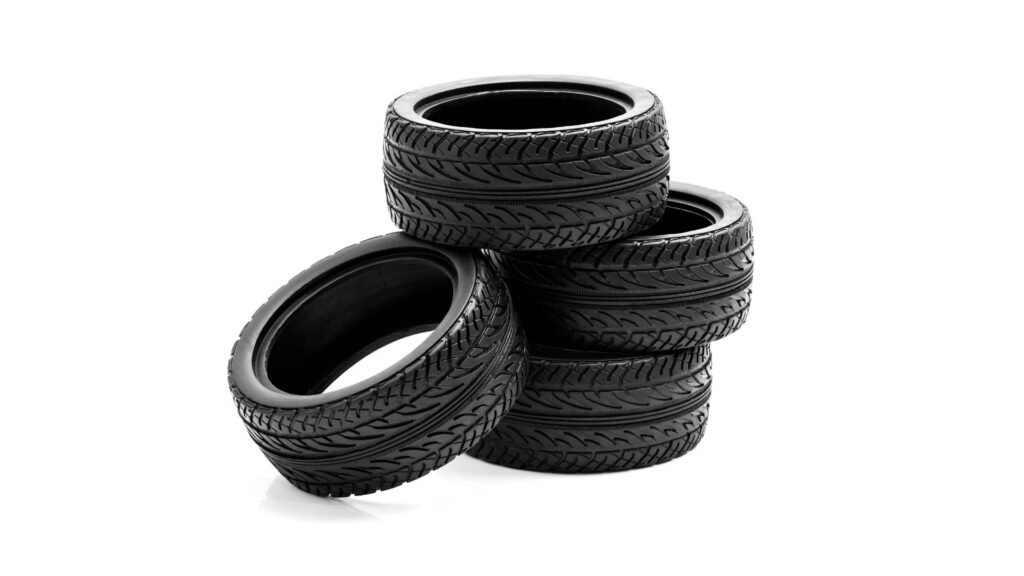
ゴムの射出成形とは、加熱・溶融させたゴム材料を高圧で金型に注入し、成形する製造方法です。
金型が必要な分、初期投資は高めですが、自動化により無人生産が可能なため長期的には経済的な製造方法といえます。
また、複雑な形状の部品や大量生産に適しており、OA機器部品、パッキング、医療機器など、幅広い産業で活用されているのも特徴です。
ゴム材料の選択肢は、シリコーンゴムやニトリルゴムなど、流動性の高いものに限定されますが、多くのゴム材料で射出成形が可能です。
高品質な製品を効率的に生産できる射出成形は、現代のものづくりに欠かせない技術として注目を集めています。
インサート成形と射出成形の違い
インサート成形と射出成形は、製造工程と用途が異なる成形技術です。
射出成形は、プラスチック樹脂を高温で溶かし、金型に圧入して固める方法で、大量生産に適しています。一方でインサート成形は、金属や異素材の部品を金型内に配置し、その周囲に樹脂を射出して成形する技術です。
インサート成形のメリットとしては、異素材を一体化することで後工程の手間を省き、コストダウンにつながる点が挙げられます。
後工程で接着するよりも強度や耐久性が向上するため、ゴムと金属の接着性が求められる自動車部品など、耐久性が重要な用途で特に有用です。
ゴムの成形方法に射出成形を選ぶメリット
ゴムの射出成形には、以下のようなメリットがあります。
- 精度が高い
- 複雑な形状の成形が可能
- 後加工がほぼ不要
- 硬化時間が短い
- 製品あたりの単価を抑えられる
流動性の高いゴムを加圧射出することで、金型全体に材料が均一に行き渡り、精密かつ高精度な形状を成形できます。
また、微細な穴や複雑な曲面の成形などにも対応しているため設計自由度が高く、複雑な部品製造が可能です。
成形時に付きやすいパーティングラインやゲート跡も少なく、完成品に近い形で仕上がるため、後加工もほとんど必要ないでしょう。
さらに、温度と圧力を精密に管理する最新技術によって、成形にかかる時間を短縮できるのもうれしいポイントです。
ゴムの成形に射出成形を用いるデメリット
一方で、ゴムの射出成形には以下のようなデメリットも存在します。
- 初期費用が高額
- 小ロットや少量生産に不向き
- 使用可能な材料が限定される
- 金型のメンテナンスコストが高い
射出成形では、金型製作や射出成形機を用意するのに多くの費用がかかります。
初期費用が高額となるので、小ロット生産は適していません。
また、使用できる材料はシリコーンゴムやニトリルゴム、ポリウレタンなど流動性の高いゴムに限定されるため、材料の選択肢は少なめです。
金型の定期的なメンテナンスも必要なので、ランニングコストも含めた検討が必要でしょう。
ゴムの射出成形の流れ
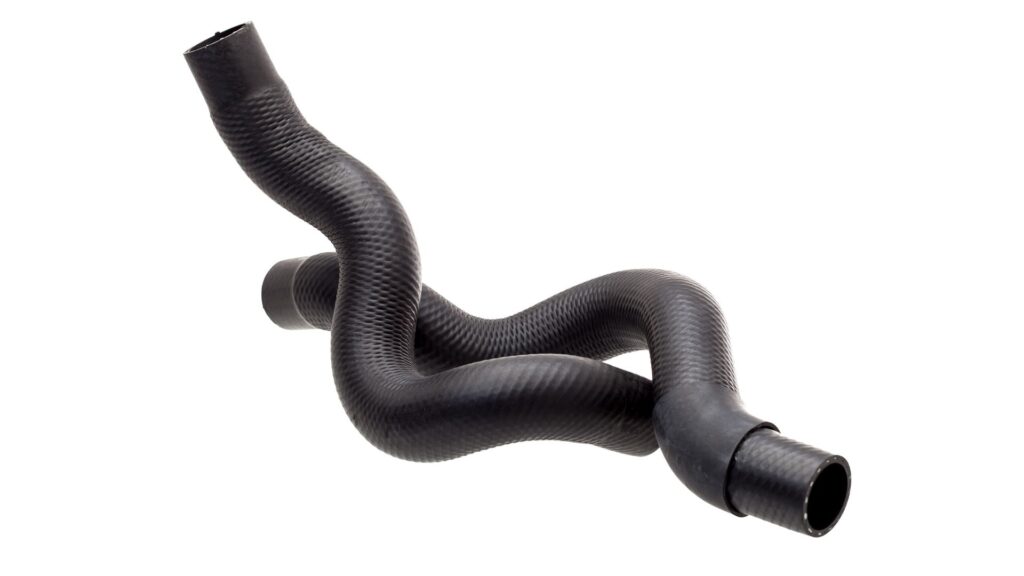
ゴムの射出成形は、複数の工程を経て製品を生み出す精密な製造プロセスです。
以下では、ゴムの射出成形の手順について簡単に見ていきましょう。
練り合わせ作業
ゴム素材は、そのままの状態では成形に使用できないため、架橋剤や充填剤を加えて練り、弾性を持たせる必要があります。
まず「素練り」で分子構造を柔らかくし、次に「混錬」で加硫剤や顔料を加え、錬ニーダー機やロール機で成形材料を作ります。
混錬工程では温度や時間を厳密に管理しながら、材料の均一性を保つことが大切です。
ここでの配合バランスや混合状態が、ゴムの強度や硬さなど最終製品の性能を大きく左右します。
裁断・型締め
ロール機で練られたゴム材料をシート状に整え、製品に合わせて適切なサイズに裁断します。
次に、裁断した材料を射出成形機にセットし、金型を閉じる型締め工程に進みます。
型締めとは、金型にゴムを充填する際の圧力で金型が開かないように強い圧力をかける作業です。
適切な圧力設定により寸法精度が高まり、ゴムの漏れも防げます。
射出成形
型締めが完了したら、加熱・溶融したゴム材料を金型内に射出します。
射出速度・圧力・温度を精密に制御し、金型のキャビティ全体が均一になるように充填するのが重要です。
なお、この際に成形条件の設定が正確でないと、ヒケやショートショット、ウェルドラインなどの不良を招く原因となります。そのため、成形時の射出設定には高度な技術が求められるでしょう。
射出後はゴムを加硫(硬化)させ、圧力と温度を保持して所定の形状と強度を確保します。
仕上げ
成形が完了したら、慎重に金型を開いて製品を取り出します。
品質に影響するため、型開きの速度や角度は綿密な設計・調整が必要です。
取り出した製品には、バリ(余分なゴム)やゲート跡が残っている場合があるため、これらを除去する仕上げ作業を行います。
必要に応じて寸法検査や外観検査も実施し、製品の洗浄や梱包を行って出荷準備を整えます。
ゴム成形でよくある成形不良
ゴムの射出成形では、さまざまな成形不良が発生する可能性があります。
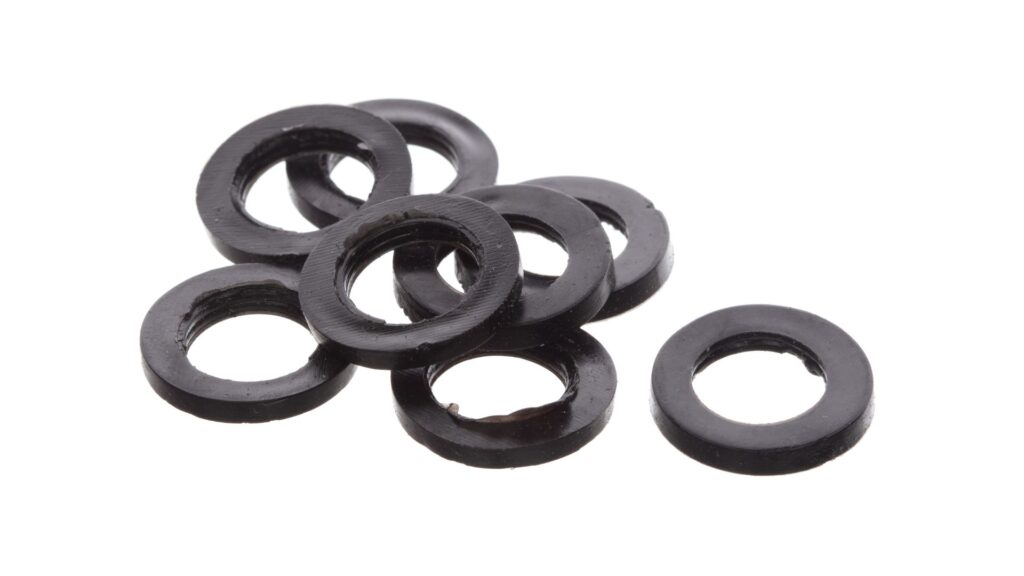
代表的な成形不良は、以下の通りです。
- ショートショット(充填不足)
- バリ(はみ出し)
- ウェルドライン(合流線)
- ヒケ(バックラインディング)
- エア(バブル)
- 発泡
- 欠け
- 変形
- 異物混入
これらの不良は製品の強度低下、外観不良、精度低下などの問題を引き起こします。
成形不良を防ぐためには、成形条件の最適化や金型設計の見直し、材料の選択、作業環境の改善などが必要となります。
射出成形以外のゴム成形方法
射出成形以外のゴム成形方法には、主に圧縮成形、圧入成形、押出成形、機械加工があります。
それぞれのメリットとデメリットは以下の通りです。
成形方法 | メリット | デメリット |
圧縮成形 | ・金型費が安価・設備が簡単・使用材料が最小限 | ・バリが多く出る・分厚い製品は寸法精度が低い |
圧入成形 | ・寸法精度が高い・複雑形状の成形が可能・金属インサートに適する | ・金型構造が複雑で高価・スクラップ量が多い |
押出成形 | ・長尺品の連続生産が可能・効率的な生産が可能 | ・断面形状が一定に限られる・複雑形状の成形が難しい |
機械加工 | ・金型製作が不要・小ロット生産に対応・複雑形状の成形が可能 | ・製品あたりの単価が高い・一部の形状には高度な技術が必要 |
圧縮成形は比較的安価で簡単ですが、精度に課題があります。
また、圧入成形は精度が高く複雑形状に適していますが、コストが高くなるのが難点です。
押出成形は長尺品の生産に適していますが、形状の自由度が限られます。
このように、それぞれの成形方法にはメリット・デメリットがあります。
それぞれの特性を踏まえたうえで、製品の形状、生産量、要求される精度などに応じて、最適な成形方法を選定することが大切です。
まとめ
ゴムの射出成形は、高精度で複雑な形状の部品を大量生産できる効率的な製造方法です。
初期投資は高いものの、生産性と品質の面で優れた特性を持ちます。
ただし、材料の制約や成形不良のリスクもあるため、製品の要件や生産規模に応じて、他の成形方法との比較検討が必要です。
なお、ゴム素材の射出成形は多くのケースで加工業者に依頼することになるでしょう。
業者ごとに成形可能な素材や製造実績は異なるので、ゴム素材に対応していることはもちろん、製造したい製品や部品の成形実績があるかをよく確認してください。
適切な成形方法の選択と、専門業者との連携により、高品質なゴム製品の開発・製造が可能となります。
射出成形を活用した部品製造を検討している方は、ぜひ「Taiga(タイガ)」をご活用ください。Taigaは、無料で経験豊富な業者に相談できるサービスです。
難易度の高い部品や新規部品の開発、少量生産、試作から量産まで、コストを抑えつつ効率的に進めることが可能です。
Taigaで技術提案を受ける