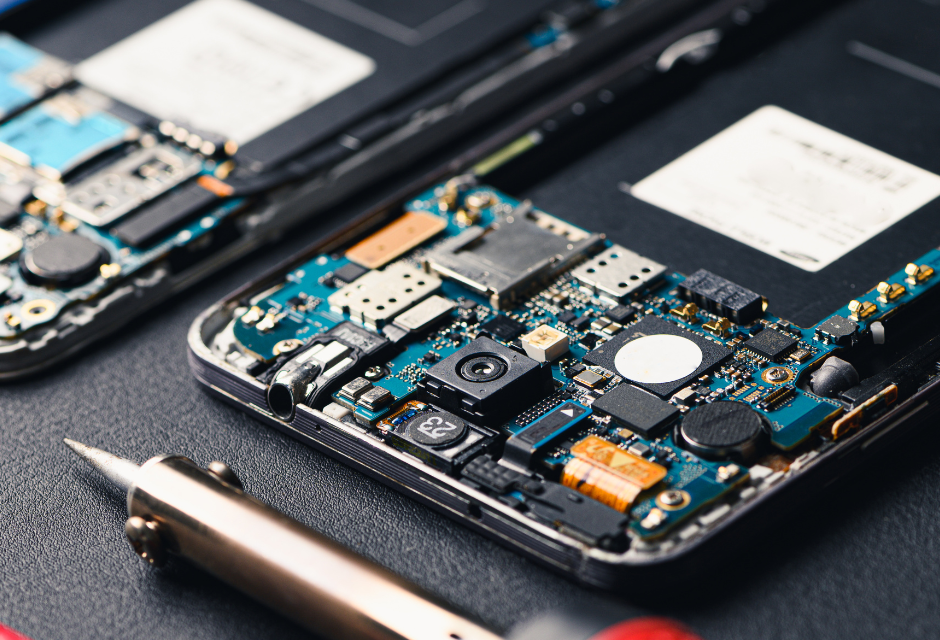
In recent years, "flexible printed circuit boards (FPCs)" have been attracting attention in the field of electronic device development; FPCs are flexible and bendable substrates, ideal for products that require miniaturization and weight reduction.
In this issue, we will explain the features, applications, and manufacturing process of FPCs in an easy-to-understand manner. By reading to the end, you should be able to see how it can be used in your own products.
For more information about Taiga, click here.Table of Contents
What is a flexible printed circuit board (FPC)?
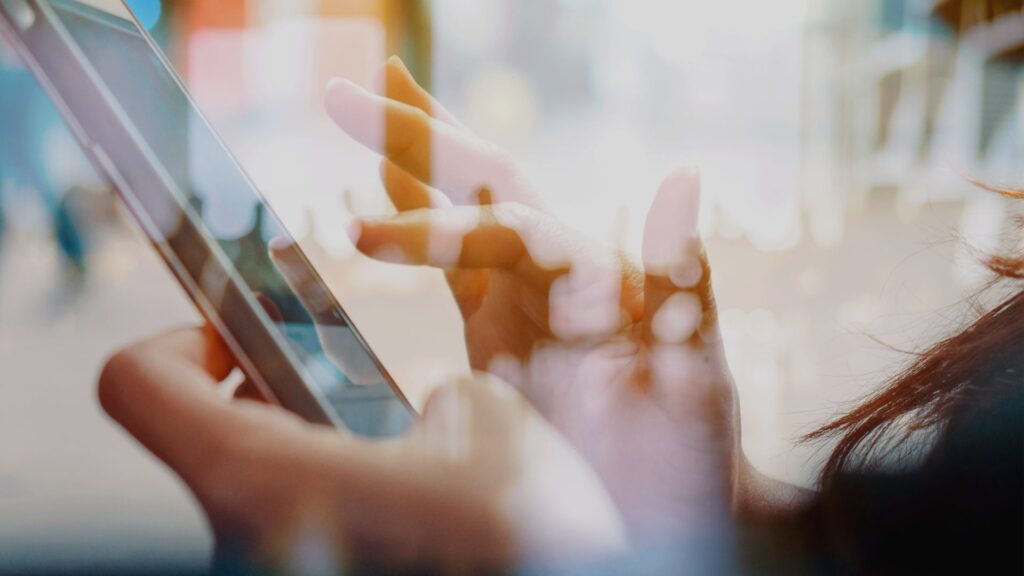
Flexible printed circuit board" or "flexible printed circuit board" is the Japanese translation of the English term "Flexible Printed Circuit. It is also called FPC for short. Flexible" means "flexible," and as the name implies, the greatest feature of FPCs is their flexibility to be bent or folded freely.
By using a thin insulating material as a base material, FPCs are not only flexible but also compact and lightweight. Due to these characteristics, FPCs are widely used in devices such as smartphones and tablet terminals, where space-saving is required.
First, let us explain some basic information about FPC.
FPC Material
CCL (Copper Clad Laminate) is the main material used for FPCs, which consists of a base film as an insulator and a conductor foil.
The base film is made of materials such as polyimide (PI), which has excellent heat resistance and flexibility, and liquid crystal polymer (LCP), which has a low dielectric constant. This base film is sandwiched between copper foil and heated and pressurized to form the CCL.
There are two main types of CCL: 2-layer and 3-layer. 2-layer CCL has a structure in which the copper foil is directly fused to the base film, while 3-layer CCL has a structure in which the base film and copper foil are bonded together using adhesives.
FPC Manufacturing Process
This section describes the general process of completing an FPC.
circuit formation
First, a copper-clad laminate (CCL), which serves as the substrate for the FPC, is fabricated. Then, the drilling process, called through-hole processing, is performed.
Dry film resist is laminated to form a circuit pattern through the processes of exposure and development. The circuit is completed by chemically dissolving (etching) the copper foil in areas not covered by the resist, leaving only the necessary portions.
coverlay treatment
To protect the formed circuits, a cover film is bonded over the entire board. This process creates an insulating layer that prevents external influences.
Surface Treatment
Copper easily oxidizes in the air, making it difficult to solder or mount components without modification. Therefore, a surface treatment is applied as an anti-corrosion treatment. In most cases, nickel or gold plating is applied.
external processing
The board is punched out precisely according to the blueprints and finished by attaching reinforcement boards and mounting components as necessary.
Electrical and visual inspections are conducted, and if there are no problems, the product is packed and shipped.
Main applications of FPCs
FPCs are used as components in electronic devices.
- smart phone
- digital camera
- PC
- display
- HDD (Hard Disk Drive)
- car navigation system
- keyboard
- calculator (electronic)
FPCs are an ideal choice, especially for smartphones, where wiring must fit efficiently in a limited space.
Difference between FPC and FFC
Simply put, an FPC is a substrate and an FFC is a cable. FPCs are thin and lightweight, and can be bent freely. Not only can the wiring pattern be freely designed, but also components such as resistors and chips can be mounted.
On the other hand, FFC (Flexible Flat Cable) is a cable with copper foil sandwiched between insulating films, and like FPC, it is not possible to mount components on it. However, because of its low manufacturing cost and short production time, FFC is often chosen for situations where simple wiring is sufficient.
Features of FPC
Rigid substrates have been widely used as electronic circuit boards.
Rigid substrates are hard substrates made of glass or paper impregnated with epoxy resin. They have the advantage of being easy to directly fix components and facilitate mounting, but they often limit the degree of design freedom.
FPC is the solution to these issues. Here are some of the unique features of FPC.
Compact and lightweight
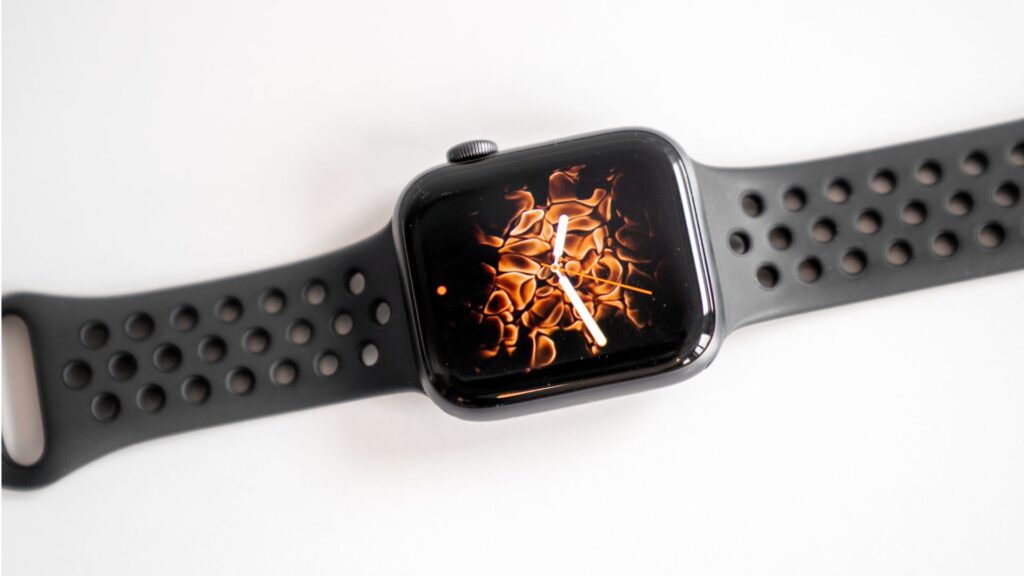
FPCs are thinner and lighter than rigid substrates because circuits are formed on a film-like substrate.
This characteristic allows for easy integration into devices where space is limited. Its light weight also makes it suitable for products that are supposed to be portable.
For example, the thinness and lightness of FPCs are a major advantage in smartphones and wearable devices.
Can be folded and incorporated
Rigid boards cannot be bent because of their rigid insulation and can only be placed flat.
On the other hand, since FPCs can be freely bent, they can be used for three-dimensional wiring and wiring in moving parts. For example, in the hinge part of a folding smartphone, wiring needs to move when the screen is opened or closed, but this is not a problem with FPC.
It can be said that the flexibility of FPCs greatly expands the design freedom of electronic devices and encourages more innovative product development.
Heat Tolerant
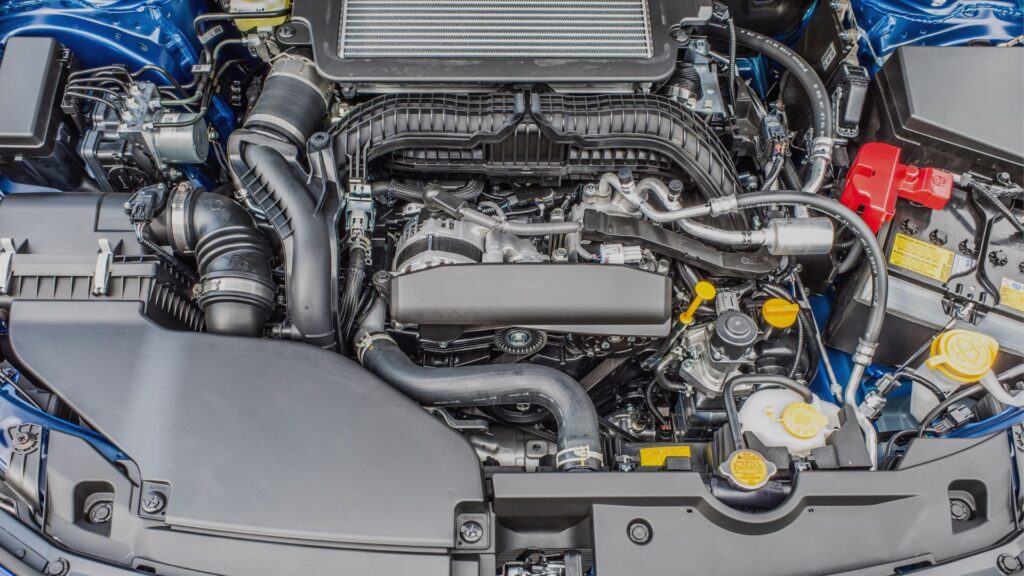
Rigid substrates are made of paper or glass cloth as a base material, combined with phenolic or epoxy resins. They are susceptible to heat and moisture and have durability issues.
On the other hand, FPCs have excellent heat resistance and can be used stably for a long period of time in high-temperature environments exceeding 100°C.
Therefore, it performs well in environments where it generates heat, such as in the engine compartment of an automobile or in factory equipment. They are also increasingly used in a variety of applications because of their stable operation even in places where temperature changes are severe.
Reduced assembly costs
The manufacturing process for electronic products involves a variety of labor-intensive tasks, such as mounting circuit boards, wiring work, and case assembly.
In the case of rigid boards, the board and wiring are separate, so connections using connectors and cables are required. This increases labor and equipment costs and makes it difficult to keep manufacturing costs (assembly costs) low. Another disadvantage is that defects such as misplaced parts and unstable operation can easily occur.
On the other hand, the use of connectors and cables can be greatly reduced in FPCs because the board and wiring are integrated. Fewer components will simplify assembly operations and reduce manufacturing costs. In addition, the overall production efficiency will be improved because the defect rate will also be reduced.
FPC Structure
FPC structures can be divided into the following four types
- Single-sided structure
- Double-sided structure
- Multilayer FPC Structure
- Flex rigid structure
Here are the features of each.
Single-sided structure
A "single-sided FPC" is an FPC in which the circuit (conductor pattern) is arranged on only one side.
Its simple structure makes it possible to take full advantage of the "soft," "light," and "thin" characteristics of FPCs. It is mainly used when you want to incorporate it into a small space in electronic devices.
However, since circuits are placed on only one side, the space available for placing components is limited, and the degree of freedom in wiring is low. Therefore, if complex circuits or multiple functions are required, it is better to consider other structures.
Double-sided structure
Double-sided structure (double-sided FPC)" is an FPC with circuits on both sides.
Since the front and back sides are available, there is no need to divide the FPC into two pieces. Wiring density is increased, components can be mounted on both sides, and space can be used even more effectively.
However, it should be noted that the movable durability is weakened compared to a single-sided structure.
Multilayer FPC Structure
The "multilayer FPC structure" is an FPC that combines single-sided and double-sided FPCs and laminates (multilayers) the circuits. It is especially used in products that require high functionality and high reliability, such as communication equipment, medical equipment, and aerospace.
Since the board and cable are integrated into one unit, connectors can be omitted and the product can be efficiently integrated into a small space. In addition, since everything is made of the same material and structure, it has excellent heat resistance and can be used in harsh environments.
However, the cost is higher than single-sided or double-sided because the man-hours required for manufacturing are more than double those required for single-sided or double-sided. Another disadvantage is that the circuit pattern on the inner layer cannot be visually confirmed, making it difficult to correct.
Flex rigid structure
The "Flex Rigid Structure" integrates the FPC and rigid substrate, providing the flexibility of the FPC and the strength of the rigid substrate at the same time, allowing for even greater design flexibility.
Another major advantage is that the FPC and rigid board are integrated, eliminating the need for connectors and cables that were previously required. Not only does this reduce the number of components and simplify the assembly process, it also prevents noise generation at the connection points.
Summary
Flexible substrates (FPCs) are based on thin insulating materials and have the flexibility to be bent and folded freely. As a result, FPCs can be placed in tight spaces that are difficult to accommodate with rigid substrates without any problems, enabling miniaturization and weight reduction.
However, there are several structures of FPCs, and selecting the best type for your product requires specialized knowledge. Since a wrong choice may affect product performance and manufacturing processes, we recommend that you consult with a trusted expert or manufacturer as early as possible.
At Taiga, experienced engineers are available for free consultation. By utilizing chat, all members involved in the project can also share design and manufacturing status and feedback in real time. We encourage you to take advantage of "Taiga" for successful product development.
For more information about Taiga, click here.