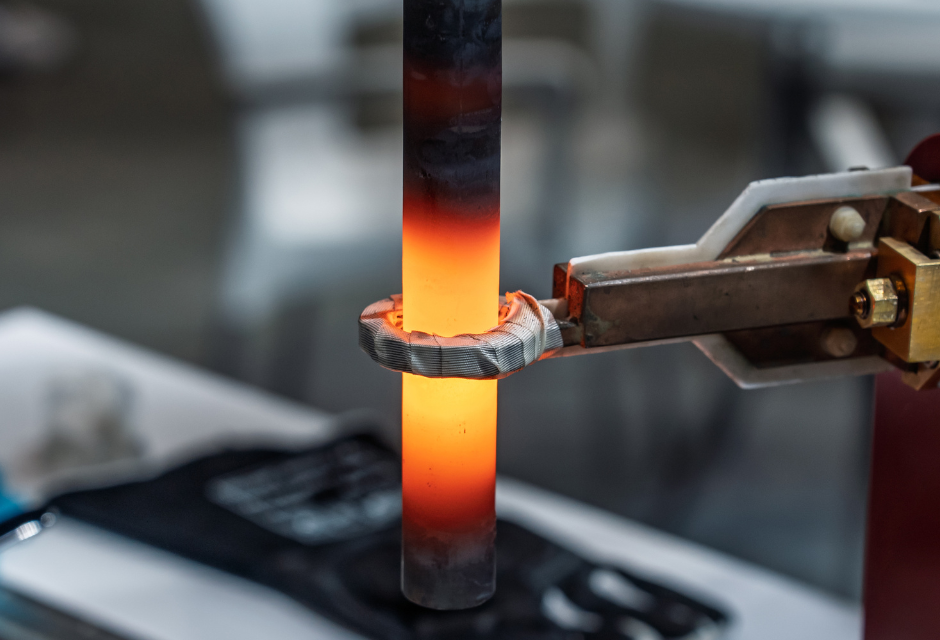
If you want to improve the durability and performance of parts, "high-frequency quenching" is recommended among a number of processing methods. It is characterized by its ability to enhance wear and fatigue resistance by rapidly heating and cooling the surface.
This article provides an easy-to-understand explanation of the characteristics of high-frequency quenching processing, how it differs from other processing methods, and even specific types. Please read to the end in order to determine the optimal manufacturing method.
For more information about Taiga, click here.Table of Contents
What is high-frequency quenching process?
High-frequency quenching" is one of the technologies to harden metal surfaces.
High-frequency induction currents are used to rapidly heat the steel surface, followed by rapid cooling. This process hardens the surface and greatly improves wear and fatigue resistance. In addition, the interior of the steel retains its original properties.
In addition, because heating and cooling are quick and can be automated, it is widely used in a variety of industries.
Mechanism of high-frequency quenching process
High-frequency quenching process can harden the surface of metals, but how exactly does it work? The following is a rough explanation of the process.
- A coil is placed around the part to be hardened and a high-frequency induction current is applied.
- Magnetic forces are generated in the coil and "eddy currents" are generated in the component.
- Eddy currents concentrate on the surface (epidermal effect) and are rapidly heated by resistive heat.
- Immediately cooled rapidly with water (cooling liquid)
- As it tends to become hard and brittle in this state, it is finally "tempered" at a low temperature of 150 to 200℃.
Examples suitable for high-frequency quenching process
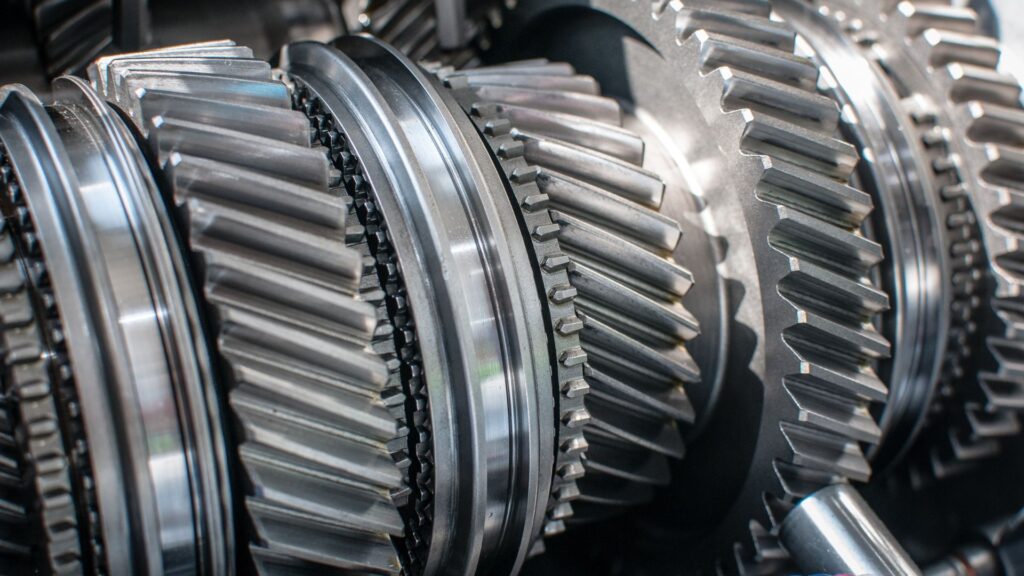
High-frequency quenching process is widely used for parts of automobiles, machine tools, and construction and civil engineering machines. It is especially suitable for parts such as "gears" and "shafts" that require wear resistance.
For example, gears used inside automobile engines must withstand high loads over long periods of time, so it is essential to improve their strength through induction hardening.
Materials suitable for induction hardening
Materials commonly treated by induction hardening include carbon steel, alloy steel, and stainless steel.
- Carbon steel (S45C, S50C, S55C)
- Alloy steel (SCM435, SCM440, SNCM439)
- Bearing steel (SUJ2)
- Stainless steel (SUS420J2, SUS440C)
- Carbon tool steel (SK3)
- Alloy tool steel (SKS3, SKD11)
Note that high-frequency quenching is not suitable for steel materials that are not magnetized because it uses the principle of induction heating to heat the metal.
It is necessary to determine the appropriate material and processing method, taking into consideration the characteristics and properties of the part. We recommend consulting with a specialist first.
Differences between high-frequency quenching and other processing methods
The following explains the differences between high-frequency quenching and other processing methods. Since each of them has different areas of expertise, use them according to your application and purpose.
Difference between high-frequency quenching and flame hardening
Many people may imagine that "quenching" involves heating metal by blowing flames with a burner. This method is called "flame hardening.
Since no special coils or jigs are required, there are no expensive initial costs. In addition, adjustments can be made by skilled technicians to accommodate parts with complex shapes.
However, the challenge is that it is very difficult to adjust the temperature, and quality is highly dependent on the experience and skills of the technicians.
On the other hand, high-frequency quenching can be PC-controlled. The major advantage is that the temperature and heating range can be set in detail, making it easy to maintain stable quality. Especially in mass production, high-frequency quenching is suitable because of the need to maintain uniform quality.
Difference between induction hardening and laser hardening
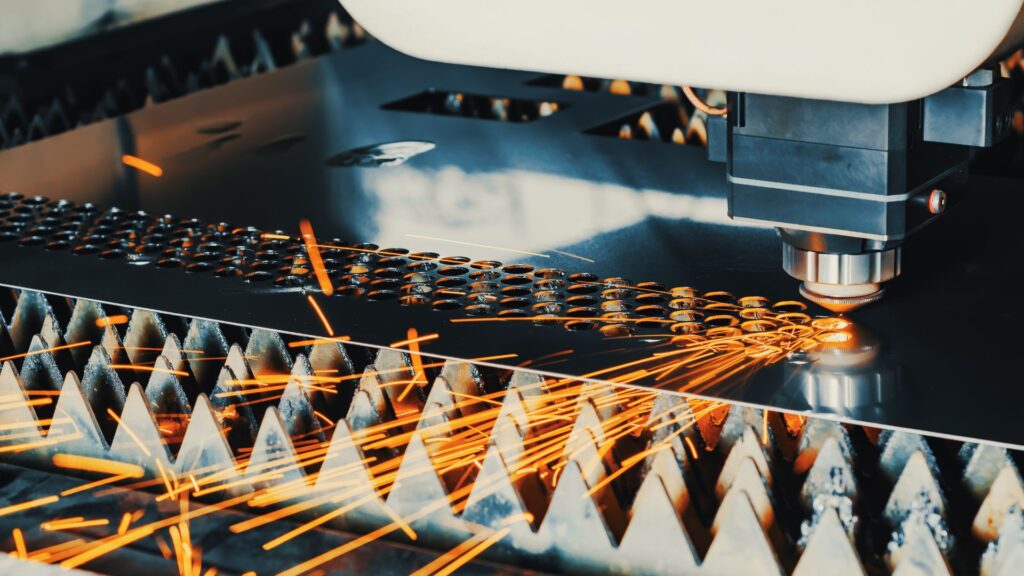
Laser quenching" is a technology that heats only a specific part by irradiating a laser beam, and is good at pinpoint precision heating. It is capable of heat treatment even in areas as far back as the light can reach, and since unnecessary heat does not affect the surrounding area, distortion of the part can be minimized.
However, the width of the laser beam is limited and is not suitable for processing more than 100 mm wide.
High-frequency quenching uses electromagnetic induction to heat the workpiece, which enables uniform hardening over a wide area. By using both laser hardening and high-frequency hardening according to the area to be processed and the shape of the part, efficient and high quality hardening can be achieved.
Difference between quenching and tempering
Both "quenching" and "tempering" are heat treatment techniques to adjust the properties of metals, and are usually performed as a set.
Quenching is a process that hardens the surface by rapidly heating followed by rapid cooling. It improves wear resistance, but because the internal structure is unstable, cracking and deformation may occur if the material is processed as it is.
Tempering is a process in which metal hardened by quenching is heated again to moderately soften its hardness and increase its tenacity. Tempering is performed at lower temperatures than quenching, and the properties change depending on the temperature.
For example, gears and shafts, which require flexibility, are tempered at high temperatures between 400°C and 650°C to give them tenacity. On the other hand, tools that require hardness are tempered at a low temperature of approximately 200°C to stabilize the inside and prevent cracking and age-related deterioration.
This combination of quenching and tempering allows metal parts to be preserved for a long period of time.
Features of high-frequency quenching process
The following is a summary of the advantages of the high-frequency quenching process.
- Hardness increases in a short time
- Less decarburization and oxidation
- Location and depth can be fine-tuned.
- High toughness is maintained.
- High production efficiency
Let's take a closer look.
Hardness increases in a short time
High-frequency quenching is a technology that rapidly heats and cools metal surfaces to increase their hardness. It also improves wear and fatigue resistance, making it ideal for parts that will be used for long periods of time.
For example, high-frequency quenching is often used for automotive parts and gears for industrial machinery because they require high durability. Please consider this when manufacturing parts that operate under high loads for long periods of time.
Less decarburization and oxidation
If heat treatment is not performed properly, problems such as "decarburization" and "grain boundary oxidation" may occur.
Decarburization is a phenomenon in which oxygen in the air combines with carbon on the steel surface during heating, resulting in the loss of carbon. The layer with less carbon than specified (decarburized layer) does not become sufficiently hard and the durability of the part is reduced.
Intergranular oxidation is a phenomenon in which the metal surface is exposed to oxygen, water vapor, and carbon dioxide (oxidizing atmosphere) during heat treatment, causing the grain boundaries to oxidize. This can cause abnormal wear and tear.
In the high-frequency quenching process, rapid heating and cooling take place in a short period of time, minimizing the risk of decarburization and oxidation, and minimizing heat-induced deformation.
Especially for parts that require precision, the surface quality directly affects the performance of the product, so the characteristics of the high-frequency hardening process are extremely important.
Location and depth can be fine-tuned.
The strength of the high-frequency quenching process is that the location and depth of heating can be finely adjusted. As long as coils can be manufactured, it is possible to heat a wide range of parts and complex shapes all at once.
For example, high-frequency quenching can be used for precision work such as hardening only specific teeth on gears.
High toughness is maintained.
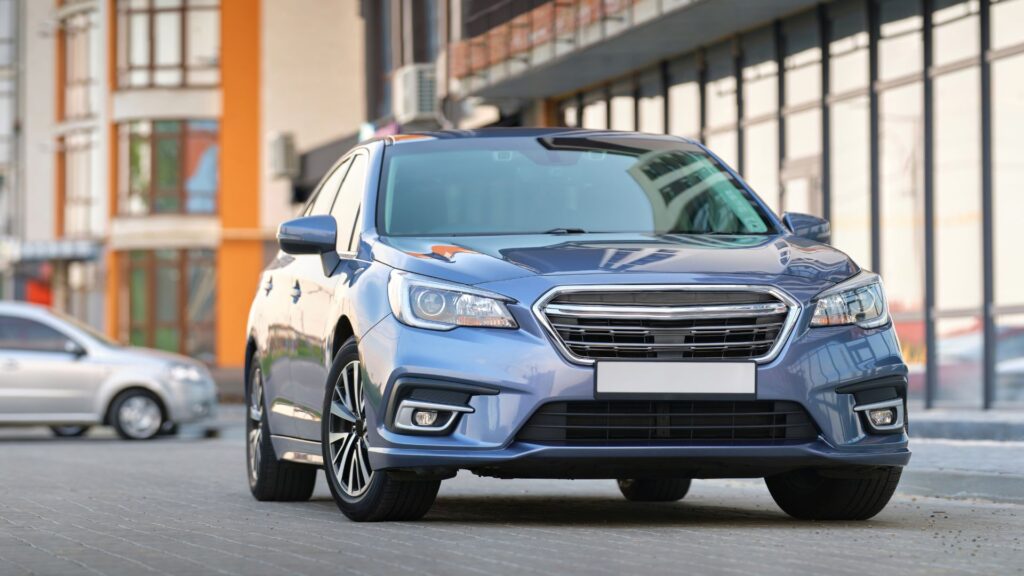
Toughness is a technical term that describes the degree to which a material is able to withstand pressure and impact. Parts with high toughness are less likely to fracture or crack, which is important for ensuring the safety of automobiles, machinery, etc.
High-frequency quenching is a processing method that hardens only the surface of the metal. It is possible to produce parts with high wear resistance on the surface and retained tenacity on the inside.
Because they can withstand harsh environments, they are often used in parts such as gears, rails, and cams in industrial machinery.
High production efficiency
In the high-frequency quenching process, temperature and speed are controlled by computer. It is characterized by ease of operation and difficulty in quality variation among technicians.
In addition, the heating speed is fast because it is electrically heated, leading to shorter production time. It is also possible to automate the entire process from transport of the workpiece to machining and finishing.
Because of its ability to combine quality and productivity, it is strongly recommended if you anticipate high volume processing of automotive parts and industrial machinery.
Types of high-frequency quenching process
In a word, "high-frequency quenching processing" is divided into several types. Since each has different characteristics, it is important to select the most suitable processing method according to the shape of the part and its application.
Here we explain the typical types of high-frequency quenching processes in an easy-to-understand manner.
Fixed one-shot quenching
The "one shot in place hardening" method heats the area to be hardened all at once while rotating the part. This method is widely used because it does not require large movements of the heating coil or the part itself, and the surface can be hardened uniformly.
individual tooth hardening
The "tooth-by-tooth hardening" method is mainly used for gears, in which the gear teeth are heated and hardened one by one. Fine adjustments can be made for each tooth, but in some cases, a new coil must be designed and manufactured.
Vertical transfer quenching
Vertical Transfer Quenching" is a heating method in which the coil and parts are heated while moving in the vertical direction. It is particularly suitable for round bars and cylindrical parts.
Horizontal transfer quenching
Horizontal Transfer Hardening" is a method in which hardening is performed while the coil and part are moved laterally. It is especially used for parts with flat surfaces or when a wide area needs to be hardened.
Summary
In this issue, we have explained in detail the basics of "high-frequency quenching processing," its features, differences from other processing methods, and even specific types of processing.
Induction hardening process hardens the surface of parts in a short time and improves wear and fatigue resistance. Stable quality control and high production efficiency by PC control are also major advantages.
Understanding the characteristics of each processing method and choosing the best method for the application and purpose can further improve the quality and performance of parts.
If you are not sure which process is suitable for your product, please contact Taiga. Our experienced engineers will propose a design and processing method.
The ability to share feedback in real time via chat makes the manufacturing and development process run more smoothly.
There is no charge for this service, so please register for an account and take advantage of it.
For more information about Taiga, click here.