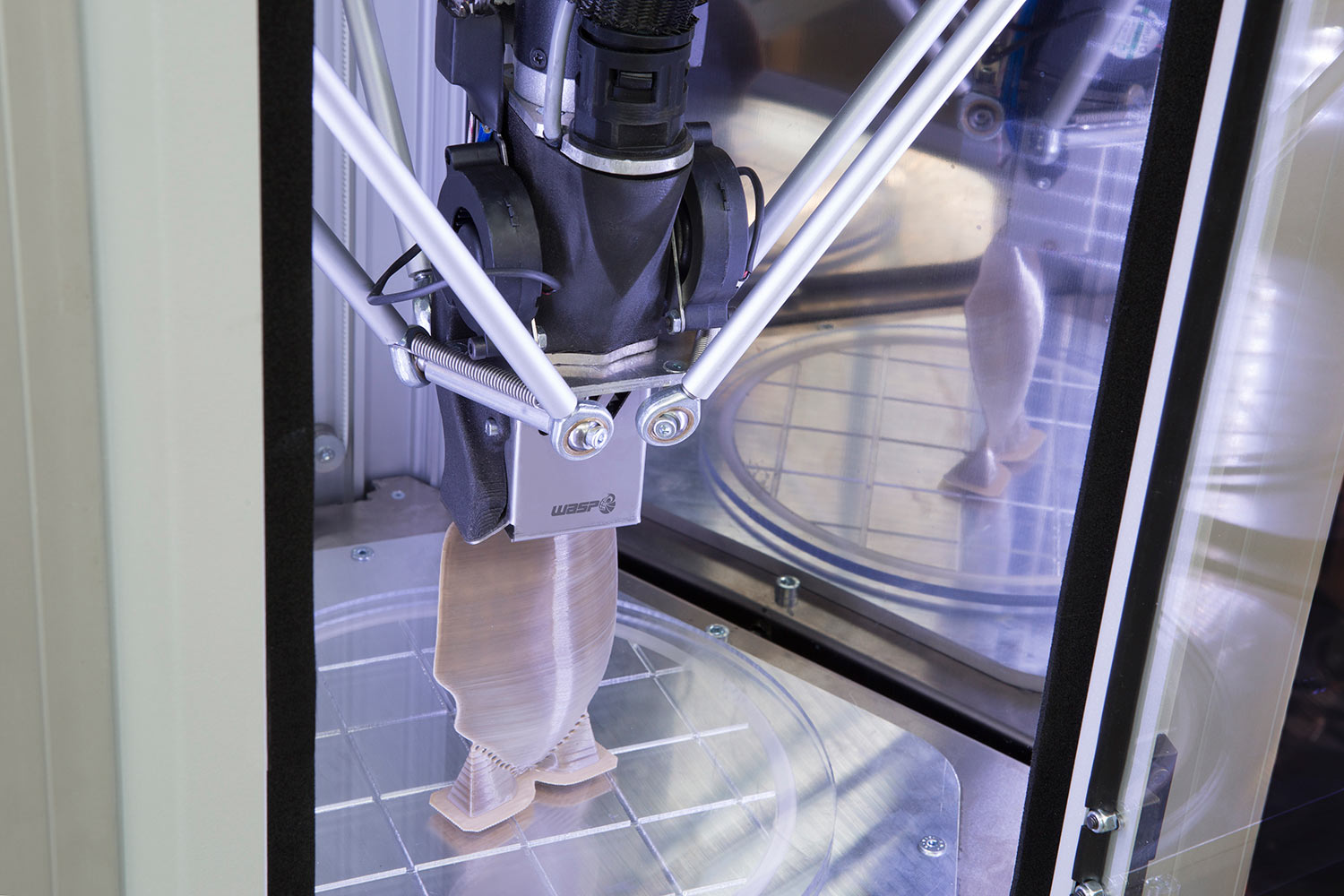
In the development of medical devices, PEEK (polyetheretherketone) is attracting attention as a material with high mechanical strength and biocompatibility.
This article provides a detailed explanation of the processing method, production flow, and even the key points for selecting a vendor for medical device prototyping using PEEK.
We hope you will find this information useful for those in charge of development and design at medical device manufacturers, as well as for engineers who are working on prototypes for implants and surgical instruments.
Receive technical proposals at TaigaTable of Contents
Why PEEK is chosen for medical device development?
The reason why PEEK (polyetheretherketone) is used in many situations in the medical device field is because of its excellent properties.
The main properties of PEEK are as follows
- Heat resistance: Continuous use temperature is about 260°C, melting point is very high at 334°C
- Mechanical strength: Excellent tensile strength and impact resistance even in high temperature environments
- Flame retardant: Very little smoke or toxic gases are generated during combustion
- Chemical resistance: Excellent resistance to many acids, alkalis, and organic solvents
- Hydrolysis resistance: Highly resistant to corrosion and other effects even under high temperature steam
- Electrical insulation: Stable electrical properties
- Biocompatibility: Non-toxic and inert in the body
- X-ray transparency: Easy to confirm implant location
- Food Safety: Meets Japanese Food Sanitation Law, U.S. FDA, and other standards
- Lightweight: Lighter than metal and easier to handle
These properties make it suitable for medical device manufacturing, and it is used in a wide range of applications such as bone fixation devices and implants.
PEEK is also available in the following types
type | feature |
Standard Grade | This is the basic grade known as "PEEK. It has an excellent balance of heat resistance, mechanical strength, and chemical resistance, and can withstand continuous operating temperatures of around 250°C. It has good machinability and can be cut to a high degree of accuracy. |
Sliding grade | Approximately 10% of carbon fiber, graphite, and tetrafluoroethylene (PTFE) are added to the basic grade to improve sliding and wear resistance. It has a low coefficient of friction and excellent wear resistance for unlubricated sliding in high-temperature environments. |
Reinforced Grade | This grade has improved mechanical strength by adding glass or carbon fibers. Compared to the basic grade, the strength, rigidity, and elasticity are greatly improved, and the heat deformation temperature is very high. Cutting workability is reduced by the addition of fibers. |
Conductive grade | This grade is made conductive by adding carbon fiber, and is used in environments where static electricity and dust are undesirable. Mechanical strength and wear resistance are also improved, but cutting workability is reduced. |
Antistatic grade | This grade has antistatic properties with a surface resistivity of 10^6 to 10^9Ω. It is suitable for applications where the generation of static electricity must be suppressed. |
Medical Grade | This grade has particularly enhanced biocompatibility. It has excellent chemical and radiation resistance, can be sterilized by pressurized steam at high temperatures, and is used for implants and medical devices. |
By using the appropriate grade for each application, optimal performance can be expected by taking advantage of the characteristics of each grade.
Processing method for PEEK used in medical device prototyping
Various processing methods exist for prototyping PEEK products for medical devices.
Since each has its own characteristics, it is important to select the best method for the application and purpose.
Machining
Cutting is the most common and effective processing method for PEEK products for medical devices.
Machine tools such as lathes and machining centers are used to cut, shave, and drill holes in plate materials to form products and parts.
The strength of the cutting process is its ability to achieve a high degree of accuracy of ±0.01 to 0.05 mm.
For example, it can reproduce details that are difficult to reproduce by injection molding, such as implant parts with complex shapes and medical connectors with fine grooves.
Although it is suitable for small-volume production and prototyping, it should be noted that cost issues arise during mass production, such as wear and tear on specialized tools and longer machining times.
Injection Molding
Injection molding is a processing method in which PEEK resin in pellet form is melted at high temperature, injected into a mold, and allowed to cool and solidify to form a product.
High reproducibility and efficient production are possible, and it is suitable when uniform quality and mass production in a short time are required.
On the other hand, it is not suitable for small-lot production because of the initial investment required to fabricate the mold.
In addition, surface accuracy is inferior to that of machining, making it difficult to form complex shapes.
Extrusion molding
Extrusion is a processing method suitable for manufacturing long products and hollow structures.
Molten PEEK is continuously extruded from a die (mouthpiece) to form a product with a constant cross-sectional shape.
Taking advantage of the excellent mechanical strength, chemical resistance, and abrasion resistance of PEEK resin, we can manufacture a variety of pipes and rods from small to large diameters and from thin to thick walls.
It is particularly suitable for the production of tubular parts and wire coating materials.
One disadvantage is that extrusion molding is difficult to handle complex shapes.
3D printing
3D printing is a modeling technology that has been gaining attention in recent years and is characterized by its high degree of customization and flexibility.
In particular, it is utilized in the medical field to produce implants of different shapes and sizes for each patient.
Also, designs such as porous or hollow structures, which are difficult to realize with conventional processing technology, are possible.
However, there is still room for improvement in terms of production speed and cost efficiency during mass production compared to other processing methods.
Flow of creating a medical device prototype using PEEK
Prototyping of PEEK products for medical devices generally proceeds as follows
- inquiry
- Meeting & Estimate
- design
- Selection of processing method
- prototype
- examination
- delivery of goods
First, a vendor is selected, product requirements and budget are discussed, and a formal request is made after the quotation is confirmed.
Then, once product specifications and processing methods are determined, prototype fabrication begins.
After completion of the prototype, we repeatedly evaluate its performance and identify areas for improvement to optimize the design.
Thereafter, in preparation for the transition to a full-scale mass production system, it is necessary to repeat the cycle of evaluation and improvement to raise the degree of perfection of the product.
Medical devices are subject to strict safety and functionality requirements, so even in the prototype stage, processes specific to medical devices may be included, such as sterilization and biocompatibility testing.
Examples of medical-related prototypes using PEEK
PEEK is used in many medical applications.

Typical medical devices using PEEK are as follows
- Bone Fixation Devices
- Temporary abutment tooth
- Implant Treatment Devices
- Catheter Shaft
- Reagent Line Tubing
- Spinal Rod
- Trauma Treatment Plates
PEEK is used in parts that require high strength and X-ray permeability, such as spinal rods and implant treatment devices.
Lightweight yet safe, it can be applied to a variety of medical devices.
How to choose a contractor for prototyping medical devices using PEEK
When requesting PEEK products for medical devices, it is important to confirm the following points
Confirmation of results in the medical device field
When choosing a vendor for PEEK processing or prototyping, you should check how well the vendor has performed in the medical field in the past.
In particular, suppliers with a successful track record in areas that require high precision and safety, such as implants and surgical instruments, are highly reliable.
Is a quality control system in place?
The medical field requires a strict quality control system.
Be sure to thoroughly check the quality control system provided by the vendor, such as compliance with ISO 13485 standards and sterilization readiness.
Summary
PEEK is gaining attention as an important material in the medical device industry.
Its excellent heat resistance, biocompatibility, and x-ray permeability allow for a wide range of uses, from implants to surgical instruments.
If you are considering prototyping and processing medical devices using PEEK, choose a supplier with high technical capabilities and appropriate quality control.
If you are considering manufacturing PEEK components, please contact us!Taiga."Taiga is a free service that allows you to consult with experienced contractors.
We can efficiently proceed with the development of difficult or new parts, small-lot production, prototyping, and mass production while keeping costs low.
Receive technical proposals at Taiga